医療・食品分野に最適 PPSUの特性と射出成形技術を徹底解説
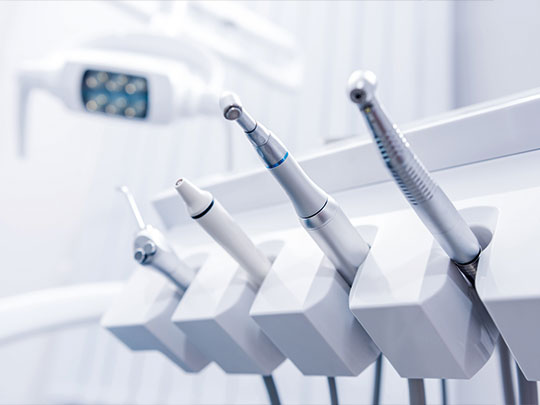
当社は、長年にわたり精密射出成形を手掛ける専門メーカーとして、様々な高機能プラスチックの可能性を追求してまいりました。今回は、スーパーエンプラの一角を占めるPPSUに焦点を当て、その卓越した特性と、当社が培ってきた射出成形技術について詳しく解説します。PPSUは、他のスーパーエンプラと比較しても、特に優れた耐衝撃性、耐薬品性、そして繰り返しの蒸気滅菌にも耐えうる抜群の耐加水分解性を誇ります。これらの特性から、医療機器、食品機械、航空宇宙、配管部品など、高い信頼性と安全性が要求される分野で金属代替材料としての地位を確立しつつあります。製品の軽量化、高性能化、長寿命化といった現代のニーズに応える上で、PPSUの重要性はますます高まっています。
射出成形メーカーから見たPPSUの魅力
私たち府中プラがPPSUの成形を手掛ける中で実感する、他の高機能樹脂と比較した場合のPPSUの際立った魅力をいくつかご紹介します。
卓越した耐衝撃性と靭性
PPSUの最も特筆すべき特性の一つが、スーパーエンプラの中でもトップクラスの耐衝撃性です。特に、切り欠き(ノッチ)部からの破壊に対する抵抗力が高く、落としたりぶつけたりしても割れにくい「靭性(ねばり強さ)」に優れています。これは、例えばポリカーボネート(PC)を凌駕するレベルであり、医療機器のハウジングや航空機の内装部品など、不意の衝撃を受ける可能性がある用途において、部品の破損リスクを大幅に低減し、安全性向上に貢献します。金属からの代替を検討する際、軽量化と同時に高いレベルの耐久性・安全性を確保できる点は大きな魅力です。
優れた耐熱性と高温特性
PPSUは非晶性樹脂でありながら、約220℃という非常に高いガラス転移温度(Tg)を有します。これにより、連続使用温度は約180℃に達し、高温環境下でも優れた機械的強度や剛性を維持します。熱変形温度(HDT)も高く、荷重がかかった状態での高温耐久性にも優れています。この耐熱性は、例えばPES(ポリエーテルサルフォン)やPEI(ポリエーテルイミド)と同等レベルであり、高温殺菌や高負荷運転が行われる医療機器や産業機器部品への適用を可能にします。
抜群の耐薬品性と耐加水分解性
PPSUは、幅広い化学薬品に対して優れた耐性を示します。酸、アルカリ、アルコール類、油脂、さらには医療現場で用いられる各種の消毒剤や洗浄剤に対しても安定しており、劣化しにくいのが特徴です。特に強調すべきは、繰り返しの蒸気滅菌(オートクレーブ、通常121℃~134℃)に対する極めて高い耐性です。他の多くの透明樹脂が高温高湿環境下で加水分解を起こし物性が低下するのに対し、PPSUは数千回の滅菌サイクル後も強度や透明性を維持できるとされています。この特性は、再利用が前提となる手術器具のトレイやハンドル、滅菌ケースといった医療用途において、他の材料では代替困難な圧倒的な優位性をもたらします。
高い寸法安定性と精密成形性
非晶性樹脂であるPPSUは、成形収縮率が比較的小さく、かつ等方性(方向による差が少ない)であるため、精密な寸法精度が要求される部品の成形に適しています。また、吸水率が非常に低いため、湿度の変化による寸法変動も最小限に抑えられます。これにより、複雑な形状を持つコネクタ部品や、嵌合精度が求められる機構部品などにおいても、長期にわたる安定した性能を発揮します。
透明性と着色性
PPSUのナチュラルグレードは、固有の淡い琥珀色をしていますが、高い透明性を持っています。これにより、内部の流体の流れや部品の状態を目視で確認する必要がある用途(例:医療用コネクタ、フィルターハウジング)への適用が可能です。また、顔料の添加による着色も容易であり、製品の識別やデザイン性の向上にも対応できます。
PPSUの化学的背景と特性
分子構造と基本情報
PPSUは、その名の通り、分子の主骨格にフェニレン基(ベンゼン環)、スルホン基(-SO₂-)、そしてエーテル結合(-O-)を組み合わせて構成される芳香族系のポリマーです。具体的には、ビフェニル構造をスルホン基とエーテル結合で連結したような構造を持ち、これにより分子鎖全体として高い剛性と化学的安定性を獲得しています。
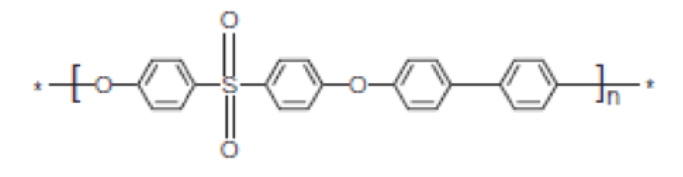
PPSUは、熱可塑性樹脂の中でも非晶性に分類されます。これは、分子鎖が規則正しく並んだ結晶構造を持たず、ランダムに絡み合った状態であることを意味します。この非晶性構造が、PPSUの透明性や良好な寸法安定性(低い成形収縮と等方性)に寄与しています。明確な融点は持ちませんが、分子鎖の運動が活発になり始める温度であるガラス転移温度(Tg)が約220℃と非常に高いことが、その優れた耐熱性の根幹となっています。
耐衝撃性のメカニズム
PPSUが他のサルフォン系樹脂(PSU、PES)と比較して特に高い耐衝撃性を示す理由は、分子構造中の比較的柔軟なエーテル結合の存在と、分子鎖自体の絡み合いやすさにあると考えられています。外部からの衝撃エネルギーを分子鎖の運動によって効果的に吸収・分散させることで、亀裂の発生や進展を抑制し、高い靭性を発揮します。特に、応力が集中しやすいノッチ部での破壊に対する抵抗力が高いのが特徴です。
耐薬品性と耐加水分解性の根拠
分子骨格を構成する芳香族環、スルホン基、エーテル結合はいずれも化学的に非常に安定な結合であり、多くの薬品に対して高い抵抗力を示します。特に、加水分解(水分子による化学結合の切断)を引き起こしやすいエステル結合やアミド結合を分子内に含まないため、高温の水や蒸気に対する耐性が極めて優れています。これが、繰り返しの蒸気滅菌に耐えうる理由です。
寸法安定性と吸水特性
非晶性構造であることに加え、PPSUは分子構造的に極性が比較的小さいため、吸水率が非常に低い(飽和吸水率でも0.5%程度)という特徴があります。水分による寸法変化や物性低下が極めて少ないため、湿度の変化が大きい環境下や水中での使用においても、安定した寸法精度と性能を維持することができます。
PPSU成形における技術課題と府中プラのソリューション
高温成形への対応
PPSUを溶融させるためには、樹脂温度として350~390℃という非常に高い温度が必要です。これは一般的な汎用樹脂やエンプラの成形温度を大幅に上回ります。当社では、PPSUをはじめとするスーパーエンプラの成形に対応可能な高温仕様の射出成形機を導入しています。シリンダーやノズルのヒーター容量、断熱性能、耐熱材料などを最適化し、設定温度を精密に制御できる体制を整えています。また、高温下で樹脂が長時間滞留すると熱劣化(焼け、分解、物性低下)を引き起こすため、スクリュー形状の最適化や滞留時間の管理を徹底し、常に新鮮で均質な溶融樹脂を供給できるよう努めています。
金型温度の厳密な管理
高品質なPPSU成形品を得るためには、金型温度を140~180℃という高温で、かつ均一に維持することが極めて重要です。金型温度が低いと、樹脂が急冷されて内部に応力が過剰に残留し、寸法精度が悪化したり、後工程や使用中にクラックが発生したりする原因となります。当社では、キャビティ表面温度を均一に保つための温調回路の最適配置、断熱構造の採用などにより、成形品の内部応力を最小限に抑え、高い寸法安定性と信頼性を実現します。過去のデータに基づき、製品形状や肉厚に応じた最適な金型温度プロファイルを設定します。
徹底した乾燥管理
PPSUは他のサルフォン系樹脂と同様に吸湿性は低い部類ですが、高温で成形されるため、ペレット(材料の粒)に含まれるわずかな水分でも、成形時に加水分解を引き起こしたり、製品表面にシルバー(銀条痕)や気泡といった外観不良を発生させたりする原因となります。
当社では、PPSUの成形前には150℃前後で4~6時間以上の予備乾燥を徹底しています。高性能な除湿乾燥機を使用し、材料の含水率をメーカー推奨値(通常0.02%以下)まで確実に低下させます。乾燥後の材料管理(吸湿防止)にも細心の注意を払い、常に最適な状態で成形に臨める体制を構築しています。
高粘度溶融樹脂への対応
PPSUの溶融粘度は比較的高く、特に複雑な形状や薄肉部分への充填には高い射出圧力が必要となる場合があります。充填不足(ショートショット)やヒケ、ウェルドラインの発生を防ぐためには、適切な対策が必要です。当社は、高射出圧力を発生可能な成形機を保有しており、PPSUの高粘度に対応できます。さらに、金型設計段階でゲートやランナーの形状・サイズを最適化し、圧力損失を低減するとともにスムーズな充填を促します。ガスベントの適切な配置により、キャビティ内の空気やガスの排出を助け、充填不良を防ぎます。また、射出速度や保圧のプロファイルを精密に制御することで、ヒケやウェルドラインを目立たなくし、内部応力を低減します。
残留応力とクラック対策
非晶性樹脂であるPPSUは、成形時の冷却ムラや不適切な保圧などにより内部に応力が残留しやすく、これが後工程での切削加工時や、特定の薬品との接触(ソルベントクラック)、あるいは長期使用におけるクラックの原因となることがあります。前述した金型温度の厳密な管理や保圧条件の最適化により、成形段階での残留応力低減に努めます。さらに、製品形状において応力が集中しやすい鋭角なコーナー部を避け、Rを設けるなどの形状提案を設計段階から行います。特に高い耐薬品性や寸法安定性が要求される場合には、成形後に製品を特定の温度で加熱・徐冷するアニール処理を行うことで、残留応力を効果的に除去するノウハウも有しています。
産業界におけるPPSUの採用事例
医療機器分野
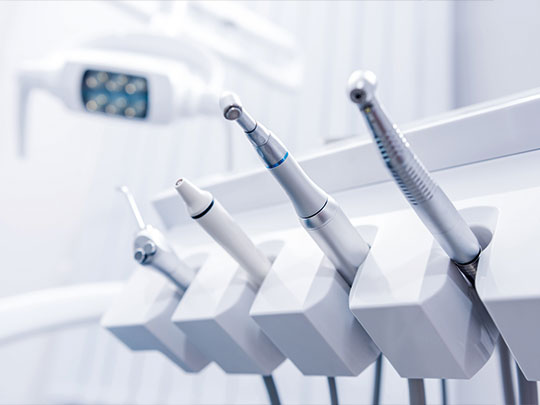
PPSUの特性(耐薬品性、耐衝撃性、透明性、生体適合性、特に繰り返しの蒸気滅菌耐性)は、医療分野のニーズと非常に良く合致しており、最も重要な用途の一つとなっています。
滅菌が必要な器具: 手術器具のハンドルやグリップ、内視鏡の部品、各種カニューレ、滅菌用トレイやコンテナなど。軽量で持ちやすく、繰り返し使用に耐えるため、金属や他の樹脂からの代替が進んでいます。
耐衝撃性が求められる部品: 輸液ポンプのハウジング、各種モニター機器の筐体やコネクタ部分など、落下や衝撃のリスクがある箇所
体液接触・流路部品: 人工透析装置のダイアライザー部品、血液分析装置のキュベットや流路ブロック、輸液ラインのコネクタなど(生体適合性グレード使用)。透明性を活かして内部の確認が可能です。
航空宇宙分野
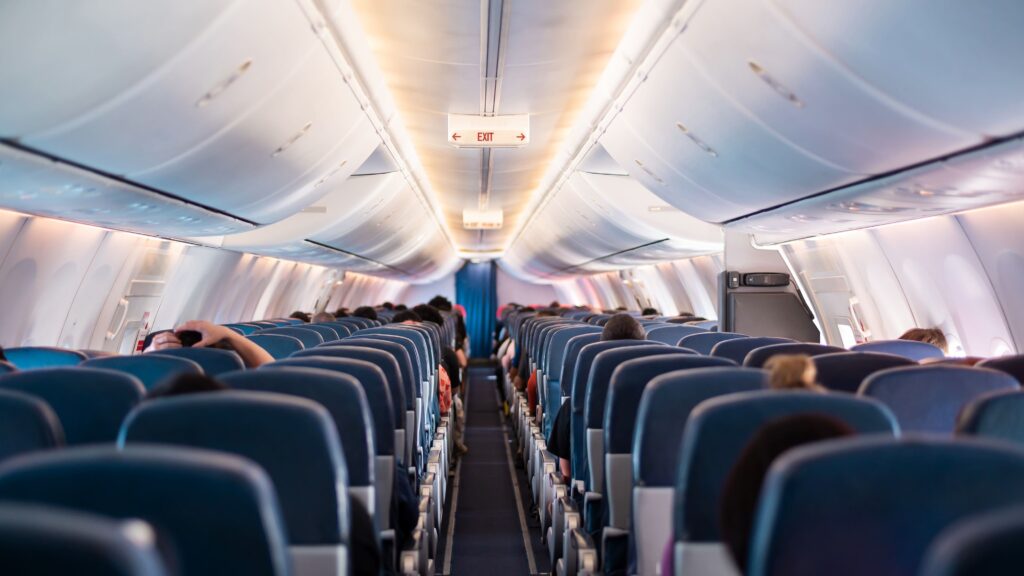
軽量性、難燃性、耐薬品性(航空燃料、作動油、洗浄剤など)、そして高温環境下での耐久性が求められる航空機の内装部品などに採用されています。
内装部品: 機内食サービス用のカートや食器類、座席周りのアームレストやテーブル部品、照明カバー、空調ダクトなど。金属や他の樹脂と比較して軽量化に貢献します。
食品機械・配管部品
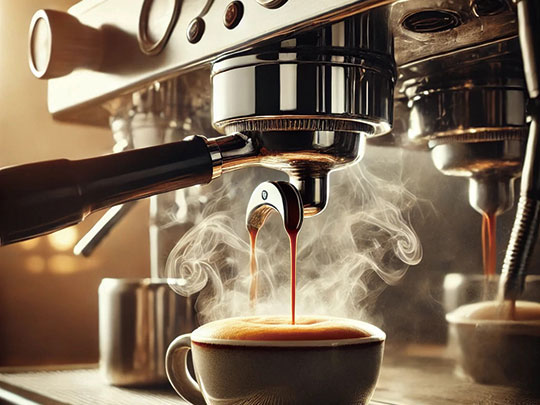
高温の液体や蒸気に接触し、かつ頻繁な洗浄や殺菌が必要とされる用途で活躍しています。
食品加工機器: 高温での調理や殺菌工程に用いられる機器の部品、充填ノズル、搬送部品など。耐薬品性と耐加水分解性が洗浄・殺菌プロセスでの耐久性を保証します。
飲料ディスペンサー: 高温水や蒸気が通るバルブ、コネクタ、フィルターハウジングなど。風味への影響が少ない点も評価されています。
温水・蒸気配管: 工業用や業務用の給湯システム、蒸気ラインの継手、バルブ、メーター部品など。
府中プラのPPSU成形における強み
製品・金型設計に関するノウハウ
PPSUの成形を成功させるためには、材料特性を考慮した製品設計と金型設計が鍵となります。当社では、PPSUの優れた耐衝撃性を活かしつつ、応力割れのリスクを低減するための形状提案(適切なR付け、肉厚の均一化など)を設計初期段階から行います。また、高い寸法精度を実現するために、PPSUの成形収縮特性に基づいた精密な金型設計(適切な収縮率の適用、高精度な温調回路設計、最適なゲート位置・種類の選定)を行います。長年の経験に基づき、PPSU特有の課題を未然に防ぐ設計ノウハウを提供します。
最適な成形条件の設定と安定化
PPSUの成形には、高温・高圧といった厳しい条件と、それを精密に制御する技術が求められます。当社は、高温仕様の成形機と精密な金型温度調節システムを駆使し、PPSUに最適化された成形条件(樹脂温度、金型温度、射出速度、保圧、冷却時間など)を確立しています。これにより、樹脂の熱劣化を最小限に抑え、内部応力を低減し、反りや寸法ばらつきの少ない高品質な製品を安定して量産することが可能です。
アニール処理のノウハウ
特に高い耐薬品性や寸法安定性が要求される製品、あるいは残留応力によるクラックが懸念される製品に対しては、成形後のアニール処理が有効です。当社では、製品形状や使用環境に応じて最適なアニール条件(温度、時間、冷却方法)を設定し、残留応力の除去や物性のさらなる向上を図るノウハウを有しています。処理効果の検証も適切に行い、信頼性を担保します。
厳格な品質保証体制
PPSUが多く採用される医療機器や航空宇宙分野では、極めて高い信頼性が要求されます。当社では、これらの要求に応えるため、厳格な品質保証体制を構築しています。画像測定器を用いた精密な寸法検査はもちろん、外観基準に基づいた目視検査にも対応可能です。材料の受け入れから成形、検査、出荷に至るまでの各工程で品質データを記録・管理し、完全なトレーサビリティを確保しています。
PPSUと射出成形技術の将来展望
需要の拡大
医療分野では、高齢化の進展や低侵襲治療の普及により、高性能で安全な医療機器への要求が高まり続けており、繰り返しの滅菌に耐えるPPSUの需要はさらに拡大するでしょう。食品分野においても、安全基準の厳格化や製造プロセスの高度化に伴い、耐熱・耐薬品性に優れたPPSUの採用が増えると予想されます。また、航空機のさらなる軽量化ニーズも追い風となります。
材料技術の進化
材料メーカーによるPPSU樹脂自体の改良も進んでいます。例えば、摺動性を向上させたグレード、導電性を付与したグレード、さらに耐熱性や耐薬品性を高めた新しいポリマーアロイなどが開発される可能性があります。これにより、PPSUの適用範囲はさらに広がっていくでしょう。
成形技術の高度化
射出成形技術自体も進化を続けています。CAEシミュレーション技術の精度向上により、より複雑な形状や薄肉製品の成形可能性予測が容易になります。また、精密な金型加工技術や成形プロセスをリアルタイムで監視・制御するスマートファクトリー化の進展により、PPSUのような加工難易度の高い成形材料でも、安定した品質と生産性を両立できる時代が来るのはそれほど先の話ではないかもしれません。
サステナビリティへの貢献
PPSUは耐久性に優れ長寿命であるため、製品ライフサイクル全体での環境負荷低減に貢献します。また、今後はリサイクル技術の開発や、植物由来原料を用いたバイオベースポリマーへの関心も高まる可能性があります。
まとめ
PPSUは、スーパーエンプラの中でも、特に卓越した耐衝撃性、広範な耐薬品性、そして繰り返しの蒸気滅菌にも耐える抜群の耐加水分解性を併せ持つ、非常にユニークで高性能な材料です。これらの特性は、医療機器、食品機械、航空宇宙部品など、安全性と信頼性が最優先される過酷な環境下で、他の材料では代替困難な価値を提供します。当社は、PPSUの特性を熟知し、最適な成形条件の設定、金型設計、アニール処理など、高品質な成形品を提供するための技術とノウハウを蓄積しています。材料選定から量産までのトータルソリューションを提供し、お客様の製品の高機能化と製造効率向上に貢献します。高性能部品の開発や金属代替をご検討の際は、ぜひ当社にご相談ください。