直鎖型PPS、架橋型PPSの違い~成形加工性と材料選定のポイント~
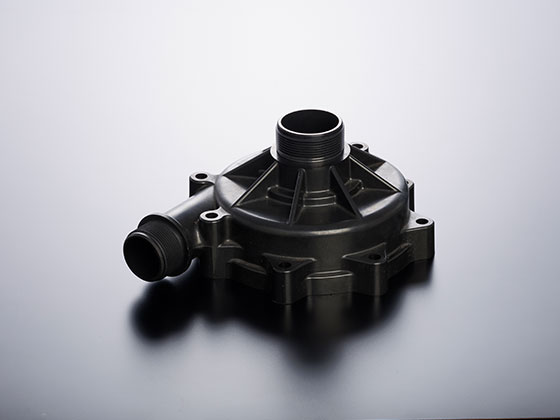
前編「基本特性と材料選択の基礎知識」では、PPS(ポリフェニレンサルファイド)の主要な2タイプ、直鎖型と架橋型について、その分子構造の違いに起因する基本的な物性(流動性、機械的特性、熱的特性、結晶化挙動など)の差を比較解説しました。直鎖型は靭性に優れ、架橋型は流動性や高温クリープ性に特徴があることをご理解いただけたかと思います。
しかし、設計者の皆様が材料を選定する際には、その材料が持つ基本的な特性だけでなく、「実際にどのように成形されるのか?」「製造プロセスで問題は起きないか?」といった「成形加工性」に関する視点も非常に重要です。材料の特性差は、推奨される成形条件、発生しやすい不良の種類やその対策、さらには金型設計に至るまで、射出成形のあらゆる側面に影響を及ぼします。
本コラム(後編)では、前編で明らかになった直鎖型・架橋型PPSの特性差が、実際の「射出成形」プロセスにどのように直結するのか、具体的な影響と対策に焦点を当てて解説を進めます。成形条件の最適化、不良低減のためのヒント、金型設計・メンテナンス上の注意点、そして最終的な材料選定における実践的な考え方について、設計と製造の橋渡しとなるような情報提供を目指します。
射出成形プロセスにおける留意点:タイプ別比較
PPSを安定して高品質に成形するためには、その特性に合わせたプロセス管理が不可欠です。ここでは、成形前の準備から、具体的な成形条件、そして発生しやすい不良とその対策について、直鎖型と架橋型の違いを意識しながら見ていきましょう。
成形前の準備
予備乾燥: PPSは他のエンプラと比較して吸湿性が低い材料ですが、成形温度が300℃を超える高温であるため、わずかな水分でも加水分解による物性低下や、成形品表面にシルバーストリーク(銀条)と呼ばれる外観不良を引き起こす可能性があります。そのため、成形前には十分な予備乾燥が推奨されます。
推奨条件例: 一般的に130~150℃で3~4時間程度の熱風乾燥または除湿乾燥が行われます。
タイプによる差: 直鎖型、架橋型で乾燥条件に大きな差はありませんが、必ず使用するグレードの推奨条件をメーカー資料で確認してください。乾燥不足は確実に不良に繋がります。
成形条件の最適化
適切な成形条件の設定は、PPSの性能を最大限に引き出し、不良を抑制するための鍵となります。
シリンダー温度設定
PPSの成形温度は高く、一般的に300~340℃の範囲で設定されます。
流動性の違いを考慮: 前編で述べた通り、架橋型は比較的流動性が良く、直鎖型は粘度が高い傾向があります。そのため、架橋型ではやや低め(例:300~320℃)、直鎖型ではやや高め(例:310~340℃)の温度設定が基本となる場合があります。ただし、これはあくまで傾向であり、グレードや成形品の形状によって最適温度は異なります。
滞留時間と熱分解リスク: 高温での成形となるため、シリンダー内での滞留時間が長くなりすぎると、PPSが熱分解を起こし、物性低下やガス発生、金型汚れの原因となります。特に上限に近い温度設定の場合は注意が必要です。成形機のシリンダー容量とショットサイズのバランス(ショットサイズがシリンダー容量の20~80%程度になるように)も考慮しましょう。
金型温度設定
PPSの性能を引き出す上で、金型温度は非常に重要なパラメータです。一般的に130~150℃という高い温度が推奨されます。
結晶化の促進: 高い金型温度は、冷却過程でPPS分子が規則正しく配列する時間を与え、結晶化を十分に進行させます。これにより、本来の耐熱性、機械強度、耐薬品性、寸法安定性が発揮されます。
表面外観の向上: 金型表面への転写性が向上し、滑らかで光沢のある表面が得られやすくなります。
内部応力の低減: ゆっくり冷却されることで、成形品内部に残る応力が緩和され、ソリやクラックのリスクが低減します。
タイプによる影響: 直鎖型は架橋型に比べて結晶化速度が速い傾向がありますが、どちらのタイプであっても、性能を十分に引き出すためには130℃以上の金型温度が強く推奨されます。金型温度が低いと(例:100℃以下)、結晶化が不十分となり、期待される性能が得られないばかりか、寸法安定性も悪化する可能性があります。金型温度の均一なコントロールも、ソリ防止のために重要です。
射出圧力・速度
流動性の違いに応じた設定: 架橋型の高流動グレードでは、充填は容易ですが、バリの発生を防ぐために、必要以上に高い圧力や速度は避ける方が良い場合があります。一方、直鎖型の高粘度グレードでは、充填不足(ショートショット)を防ぐために、比較的高めの射出圧力や速度が必要になることがあります。
せん断発熱: 射出速度を上げると、樹脂内部での摩擦(せん断)による発熱が大きくなります。PPSは熱安定性が高いとはいえ、過度のせん断発熱は熱分解のリスクを高めるため注意が必要です。
多段制御の活用: 充填過程で射出速度を変化させる多段制御は、ガスベント(空気抜き)を効果的に行ったり、ジェッティング(蛇行痕)を防いだりするのに有効です。
保圧条件(圧力・時間)
成形収縮によるヒケや寸法変動を抑制するために重要です。
収縮率の補償: PPSは結晶化に伴う収縮が比較的大きい樹脂です。特に結晶化度の高い直鎖型は、架橋型よりも収縮率が大きくなる傾向があるため、それを補うための適切な保圧設定(圧力と時間)がより重要になります。
ゲートシール時間: 保圧は、キャビティへの入り口であるゲートが固化(ゲートシール)するまで有効です。ゲートが早く固化しすぎると、十分な保圧がかからずヒケの原因となります。ゲートサイズや金型温度も保圧効果に影響します。
過剰な保圧のリスク: 保圧が高すぎたり長すぎたりすると、内部応力の増大、ソリ、バリ、離型不良の原因となるため、バランスが重要です。
背圧・スクリュー回転数
背圧: 適度な背圧(例:5~15MPa程度)は、溶融樹脂の密度を高めて計量を安定させ、樹脂中の揮発分(ガス)をベント(スクリュー後方へ逃がす)する効果があります。ただし、背圧を高くしすぎると、せん断発熱が増加し、計量時間も長くなるため注意が必要です。
スクリュー回転数: 回転数を上げすぎると、これも過度のせん断発熱を招く可能性があります。樹脂が十分に溶融・混練され、かつ計量時間が適切になる範囲で設定します。
成形収縮と寸法精度
収縮率の傾向
PPSは結晶性樹脂のため、非晶性樹脂に比べて成形収縮率は大きくなります。特に、結晶化度が高くなりやすい直鎖型は、架橋型よりも収縮率が小さくなる傾向があります(例:GF強化グレードで、流れ方向(MD)の収縮率が直鎖型0.2-0.5%、架橋型0.3-0.7%程度など。グレードにより異なります)。また、ガラス繊維などのフィラーは配向(特定の方向に並ぶ)するため、流れ方向とその直角方向(TD)で収縮率が異なる「異方性」を示します。
金型設計への反映
精密な寸法精度が要求される部品では、使用するPPSグレードの収縮率(MD/TD)を正確に見込み、金型キャビティの寸法を設計する必要があります。特にタイプやグレードを変更する際は、収縮率の違いを考慮した金型修正が必要になる場合があります。
成形条件の影響
金型温度が高いほど結晶化が進み収縮率は大きくなる傾向があります。一方、保圧を高く、長くするほど収縮は抑制されます。安定した寸法を得るためには、これらの成形条件を厳密に管理することが重要です。
発生しやすい成形不良とその対策
PPS成形では、その特性に起因する特有の不良に注意が必要です。
バリ
特に架橋型の高流動グレードで発生しやすい傾向があります。
対策:
– 型締力が十分か確認する(成形機の能力、設定値)。
– 射出圧力、保圧、射出速度を必要最低限に調整する。
– 金型温度が高すぎないか確認する。
– 金型のパーティング面(合わせ面)の精度を確認し、清掃や修正を行う。
– パーティングラインの設計を見直す(バリが出ても問題ない箇所にするなど)。
ガス焼け・金型汚れ(ヤニ)
PPSは成形時に、微量ながら硫黄化合物を含む腐食性のガスを発生させることが知られています。また、キャビティ内の空気が断熱圧縮されることでもガス焼けが発生します。これらのガスや分解生成物が金型表面に付着し、蓄積すると「金型汚れ(ヤニ、モールドデポジット)」となり、ガス抜け不良、外観不良、寸法不良、離型不良などを引き起こします。特に架橋型の方がガス発生量が多いと言われることもあります。
対策:
– ガスベントの最適化と定期清掃: 最も重要な対策です。パーティング面、エジェクターピン周辺、入れ子の隙間などに十分な深さと幅のガスベントを設け、定期的に清掃して詰まりを防ぎます。ベントが詰まるとガス焼けやショートショットが多発します。
– 成形条件の調整: 射出速度(特に充填終盤)を下げる、シリンダー温度や背圧を必要以上に上げない、滞留時間を短くするなどの調整が有効な場合があります。
– 金型材質・表面処理: 耐腐食性に優れた金型材料を選定したり、適切な表面処理(例:窒化処理、クロムメッキ、TiNコーティングなど)を施したりすることが、金型汚れの付着防止とメンテナンス性向上に繋がります。
ヒケ・ボイド
肉厚部、リブやボスの付け根など、冷却が遅く収縮が大きい箇所で発生しやすくなります。
対策:
– 保圧圧力や保圧時間を最適化する(上げる、長くする)。
– ゲートサイズを大きくし、ゲートシール時間を遅らせる。
– 製品の肉厚を可能な限り薄く、均一にする設計変更。
– ガスアシスト成形などを検討する。
ウェルド強度低下
樹脂の流れが合流する部分(ウェルドライン)は、分子の絡み合いが不十分になりやすく、強度が低下します。特に衝撃特性などでは、靭性に優れる直鎖型の方がウェルド強度は有利な傾向があります。
対策:
– シリンダー温度、金型温度、射出速度を上げて、合流部での樹脂の溶着を促進する。
– ウェルド部にガスが溜まらないように、適切な位置にガスベントを設ける。
– ゲートの位置や数を変更し、ウェルドラインが発生する位置を目立たない場所や応力のかからない場所に移動させる設計変更。
離型性
高い金型温度(130℃以上)で成形するため、固化していてもまだ柔らかい状態で突き出すことになります。突き出し時の変形や傷に注意が必要です。
対策:
– 十分な抜き勾配を設ける。
– 突き出しピンの面積を大きく、数を多くし、突き出し圧力が局所的に集中しないように配置する。
– 必要に応じて離型剤を使用する(ただし、製品への付着や金型汚染に注意)。
– タイプによる顕著な差は報告されることが少ないですが、グレードによる違いはある可能性があります。
金型設計・メンテナンスに関する注意点
PPS成形を成功させるためには、金型にも特別な配慮が必要です。
ガス対策の徹底
前述の通り、PPS成形ではガス対策が極めて重要です。設計段階で十分なガスベントを効果的な位置に設けることが必須です。深さ(例:0.005~0.02mm程度)は樹脂が入り込まずガスだけが抜けるように精密に管理し、幅や長さは十分に確保します。また、成形中の定期的なベント清掃は、安定生産のために欠かせません。
金型材質の選定
PPSから発生するガスによる腐食と、特にGF強化グレードによる摩耗の両方に耐える必要があります。キャビティやコアには、耐腐食性と耐摩耗性を兼ね備えた鋼材(例:マトリックス系高速度鋼、ステンレス系鋼材、または適切な表面処理を施したプリハードン鋼など)の選定が推奨されます。
温度コントロール
130~150℃という高温域で、かつ均一な温度分布を実現するために、高精度な金型温度制御が必要です。温調媒体(通常は油)の流量や圧力を確保し、キャビティ表面近くに効率的な温調回路(水穴)を配置する設計が求められます。
ゲート・ランナー設計
圧力損失を最小限に抑え、せん断発熱をコントロールし、均一な充填を実現する設計が必要です。流動性の異なるタイプやグレードに合わせて、ゲートサイズやランナー径を最適化します。
後処理:アニールについて
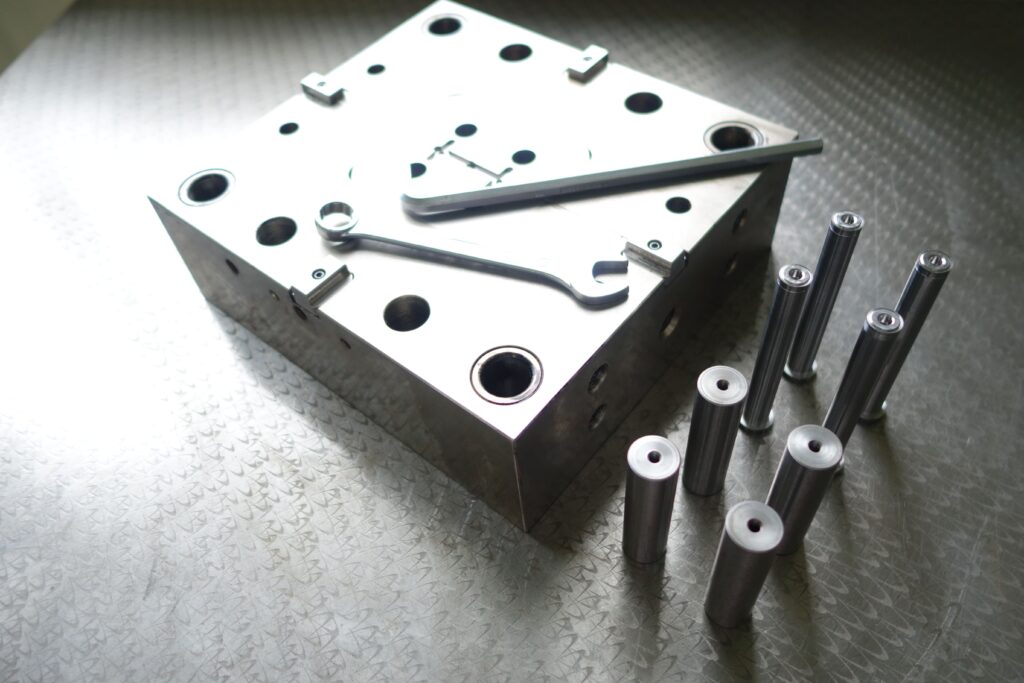
PPS成形品に対して、成形後に行われる熱処理を「アニール」と呼びます。アニールの目的は、第一に寸法安定性の向上です。 成形時に残った内部応力を緩和し、使用中の温度変化による寸法変化を抑制します。第二に結晶化度の向上です、 成形だけでは到達しきれなかった結晶化をさらに進行させ、耐熱性、剛性、耐薬品性をわずかに向上させることがあります。
特に精密な寸法精度が長期間要求される部品や、高温環境下で使用される部品に対して、アニール処理が有効な場合があります。一般的なアニール条件例は、 200℃前後で2~4時間程度加熱した後、ゆっくり冷却します。最適な条件は、部品形状や要求性能によって異なります。アニールによる寸法変化も考慮する必要があります。
一般的な用途例と材料グレード選定
これまでの特性と成形性の違いを踏まえ、どのような用途にどちらのタイプが適しているかの一般的な傾向を見てみましょう。
直鎖型PPSが適する一般的な用途
高い靭性(耐衝撃性、耐疲労性)、厳密な寸法精度、高い機械的強度が要求される用途が適します。
一般的な用途例
電気電子機器: 特に高い信頼性や挿抜耐久性が求められるコネクタ、精密スイッチ部品、センサーハウジング、リレー部品など。
精密機構部品: 高温下での精密な動作が要求されるギア、カム、レバーなど。
その他: 高強度・高靭性が求められる特殊なポンプ部品、フィルム、繊維、モノフィラメントなど。
適するグレード例
非強化高靭性グレード、GF強化(30~40%程度)高強度・高靭性グレード、摺動性改良グレードなど。
架橋型PPSが適する一般的な用途
優れた流動性(薄肉・複雑形状への充填性)、高温でのクリープ特性(寸法安定性)、コストパフォーマンスが要求される用途が適します。
一般的な用途例
ポンプ・配管機器: インペラ、ケーシング、バルブコンポーネント、継手類など。(耐薬品性と高温耐水性を活かす)
電気電子機器: コイルボビン、各種ハウジング、ソケット、スイッチ筐体など。(耐熱性、難燃性、寸法安定性を活かす)
一般工業部品: 耐熱性・耐薬品性が求められる各種機構部品、ハウジングなど。
適するグレード例
GF強化(40%以上も多い)高流動・高剛性グレード、ガラス繊維/無機フィラー複合(低ソリ、高剛性)グレードなど。
グレード選定の考え方
上記はあくまで一般的な傾向です。直鎖型にも高流動グレードはありますし、架橋型でも靭性を改善したグレードが存在します。また、ガラス繊維の含有量や種類、炭素繊維強化、摺動剤添加など、各メーカーから非常に多様なグレードが提供されています。最終的な選定は、部品の要求仕様を明確にした上で、具体的な材料グレードのデータシートを比較検討し、必要であれば試作成形による評価を行うことが不可欠です。
材料選定の最終チェックポイントとまとめ
PPSのタイプとグレードを選定する際の最終的なチェックポイントをまとめます。
要求特性の優先順位付け
設計する部品にとって、最も重要な特性は何か? 靭性、流動性、剛性、耐熱性、クリープ特性、寸法精度、コスト… これらの優先順位を明確にすることが出発点です。
成形性とコストのバランス
最高の性能を持つ材料が、必ずしも最適とは限りません。既存の成形機や金型で安定して成形できるか? 不良率を低く抑えられるか? 材料コストとトータルコスト(成形加工費含む)のバランスはどうか? これらの現実的な側面も考慮が必要です。
グレードの多様性を認識する
「直鎖型」「架橋型」という大分類だけでなく、その中に存在する無数のグレードの特性を理解し、候補を絞り込む必要があります。フィラーの種類と含有量、各種添加剤(摺動改良、導電性付与など)の効果も考慮に入れましょう。
サプライヤー・成形メーカーとの連携
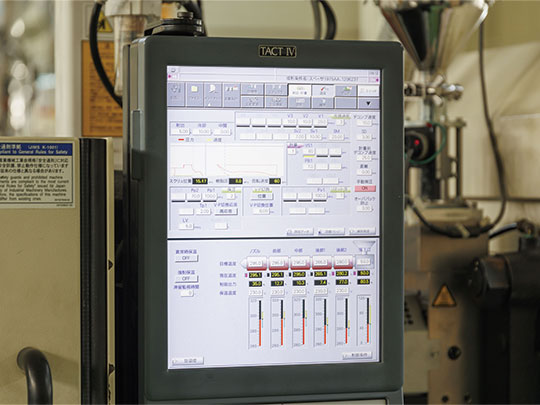
設計の初期段階から、材料メーカーや我々のような専門的な知識と経験を持つ成形メーカーに相談することが、最適な材料選定への近道です。「こんな部品を作りたいのだけど、どのPPSが良いだろうか?」「このグレードを使う上での注意点は?」といった具体的な相談を通じて、より的確な情報を得ることができます。試作成形による事前評価も有効な手段です。
まとめ
本コラム(後編)では、直鎖型・架橋型PPSの特性差が射出成形プロセスに与える具体的な影響と、材料選定における実践的なポイントを解説しました。成形条件の最適化、ガス対策の重要性、金型設計への配慮など、PPSを使いこなすためには多くのノウハウが必要となります。結論として、直鎖型PPSと架橋型PPSに絶対的な優劣はなく、それぞれに得意な領域があります。重要なのは、製品に求められる要求性能と、製造プロセス全体(成形性、コスト)を総合的に考慮し、最適なタイプ、そして最適なグレードを「適材適所」で選択することです。
当社では、PPSをはじめとする各種エンプラの射出成形において、長年の経験と実績を積み重ねてまいりました。材料選定に関するご相談から、試作、量産まで、お客様の製品開発をサポートさせていただきます。PPS部品の設計・成形に関してお困りのことがございましたら、どうぞお気軽にお問い合わせください。