金属部品と樹脂(エンプラ)部品は何が違う? ─ 素材特性の基本を押さえる
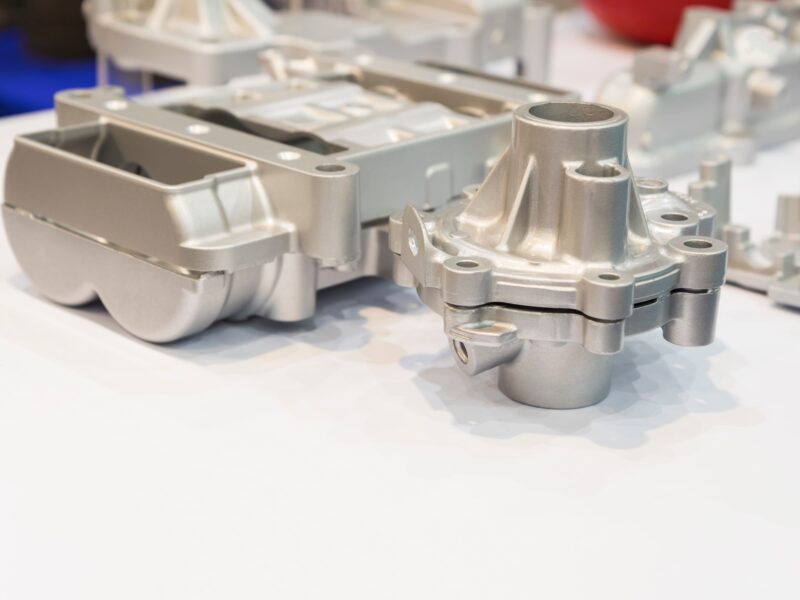
その置き換え、本当に大丈夫?「樹脂≠軽い金属」
軽量化やコストダウン、あるいは錆びない特性を求めて、これまで金属で作られていた部品を樹脂、特に強度や耐熱性に優れたエンジニアリングプラスチック(エンプラ)に置き換える動きが活発です。しかし、ここで一つ大きな注意点があります。それは、「金属部品と同じ形状で作れば、樹脂でも同じ性能が出せるわけではない」ということです。
多くの方が樹脂に対して持つイメージは「軽い」ことかもしれません。確かに樹脂は金属より圧倒的に軽量ですが、単に「樹脂=軽い金属」と考えてしまうのは危険です。両者は成り立ちからして全く異なる素材であり、強度、硬さ、熱に対する挙動、水分や薬品への耐性など、多くの基本的な特性が大きく異なります。そのため、金属の設計図をそのまま流用して樹脂部品を作ると、「思ったより簡単に曲がってしまった」「熱で変形して使えなくなった」「湿気で寸法が変わってしまった」といった問題が起こりがちです。
金属代替を成功させるためには、まず金属と樹脂の基本的な「違い」を正しく理解し、設計の前提そのものを変える必要があります。本コラムでは、金属部品から樹脂部品への置き換えを考える上で、最低限押さえておくべき基本的な素材特性の違い(比重、剛性、耐熱性、吸水性、耐候性・耐薬品性、加工性)を整理し、それが設計にどう影響するのかを分かりやすく解説します。
比重(密度)の違い──軽いが、それだけではない
まず最も分かりやすい違いが重さ(比重、密度)です。
金属
鉄(鋼):約 7.9 g/cm³
アルミニウム:約 2.7 g/cm³
亜鉛合金(ダイカスト用):約 6.7 g/cm³
マグネシウム合金:約 1.8 g/cm³
樹脂(エンプラ)
多くの場合、1.0 〜 1.6 g/cm³ の範囲に収まります。ガラス繊維(GF)などで強化した場合でも、2.0 g/cm³ を超えることは稀です。例えば、同じ体積であれば、樹脂は鉄の約1/5〜1/8、アルミニウムの約1/2程度の重さしかありません。この「軽さ」は、製品の軽量化による燃費向上(自動車)、持ち運びやすさ(携帯機器)、作業者の負担軽減(組立工程)など、多くのメリットをもたらします。これが金属代替の大きな動機の一つです。
【設計への影響】
単純に置き換えるだけで大幅な軽量化が実現できます。しかし、後述するように樹脂は金属より柔らかいため、同じ形状では強度や剛性が不足する可能性があります。軽量化のメリットを享受しつつ、必要な性能を確保するためには、形状の工夫(肉厚を増やす、リブを立てるなど)が必要になることが多く、結果的に体積が増えることも考慮しなければなりません。
部品単体の軽量化だけでなく、製品全体の重量バランスがどう変化するかも重要です。特定の部品だけを軽くすることで、重心位置が変わり、意図しない挙動(振動しやすくなる、倒れやすくなるなど)を示す可能性もあります。質量は振動のしやすさ(固有振動数)にも影響します。軽い部品に置き換えることで、共振周波数が変化し、これまで問題なかった振動が発生する可能性も考慮が必要です。「軽い」ことは大きな魅力ですが、それに伴う強度・剛性の低下や、他の特性への影響も踏まえて設計を進める必要があります。
剛性(ヤング率)の違い──同じ荷重でも変形が大きい
次に重要な違いが硬さ(剛性、ヤング率)です。これは、材料がどれだけ変形しにくいかを示す指標です。
金属
鋼(鉄):約 200 GPa
アルミニウム:約 70 GPa
樹脂(エンプラ)
非強化グレード:一般的に 2 〜 4 GPa 程度
ガラス繊維(GF)強化グレード:強化しても 10 〜 20 GPa 程度
数値の桁が全く違うことにお気づきでしょうか。一般的なエンプラは、アルミニウムの1/20〜1/30、鉄の1/50〜1/100程度の剛性しかありません。 ガラス繊維で強化しても、アルミニウムの半分にも満たない場合がほとんどです。これは、「樹脂は金属に比べて非常に柔らかい」ということを意味します。
【設計への影響】
金属と同じ感覚で設計すると、荷重がかかった際に大きくたわんでしまいます。樹脂部品の設計では、「ある程度の変形は起こるもの」として、それを許容できるか、あるいは変形を抑えるための工夫が必要かを判断しなければなりません。必要な剛性を確保するためには、単純に肉厚を増やすか、効果的な位置にリブ(補強の骨)を設けるといった、樹脂特有の設計アプローチが不可欠になります。また。長い形状の部品(梁やシャフトなど)では、自身の重さだけでもたわみやすくなります。金属と同じ細さでは、垂れ下がってしまったり、振動しやすくなったりするため、断面形状の工夫(I字断面、パイプ形状など)も重要です。
「軽い」けれど「柔らかい」。このトレードオフを理解し、形状で剛性を補う発想が樹脂設計の基本となります。
耐熱性──熱で形が変わる、柔らかくなる樹脂
物質がどれくらいの温度まで耐えられるかを示す耐熱性も、金属と樹脂では大きく異なります。
金属
鉄やアルミニウムは、融点(溶け始める温度)がそれぞれ約1500℃、約660℃と非常に高く、一般的な使用環境(数百度程度)であれば、熱による強度低下や変形は比較的小さいと言えます。
樹脂(エンプラ)
樹脂の種類によって様々ですが、連続して使用できる温度の上限は、汎用エンプラ(POM, PA6, PBTなど)で概ね80℃〜150℃程度、スーパーエンプラと呼ばれる高性能なものでも200℃〜260℃程度が一般的です。樹脂の耐熱性を評価する指標として、荷重たわみ温度(HDT)やガラス転移温度(Tg)があります。HDTは、一定の荷重をかけた状態で温度を上げていったときに、規定のたわみ量に達する温度を示します。Tgは、樹脂が硬いガラス状態から柔らかいゴム状態に変化し始める温度で、この温度を超えると急激に剛性が低下します。
【設計への影響】
部品が使用される環境の最高温度を確認し、それに対して十分な耐熱性を持つ樹脂を選定することが大前提です。特に熱源を有する機器、照明器具周辺など、高温になる箇所での使用には注意が必要です。使用温度上限に近い温度で荷重がかかると、変形(クリープ現象)が起こりやすくなったり、強度が低下したりします。余裕を持った材料選定と、高温での物性値を考慮した設計が必要です。樹脂は金属よりも熱で膨張・収縮しやすい(線膨張係数が大きい)傾向があります。温度変化によって部品の寸法が変わり、他の部品との嵌合がきつくなったり、隙間が大きくなったりする可能性を考慮する必要があります。金属の感覚で「このくらいの温度なら大丈夫だろう」と安易に判断せず、使用温度と樹脂の耐熱グレードをしっかり確認することが重要です。
吸水性──水分による寸法変化と物性低下に注意
金属にはない、樹脂特有の性質として吸水性があります。
金属
基本的に水を吸うことはありません(錆びることはありますが)。
樹脂(エンプラ)
樹脂の種類によっては、空気中の水分を吸収したり、水に浸漬することで材料内部に水分を取り込んだりします。特にPA(ポリアミド、ナイロン)は吸水性が高く、飽和吸水率は数%に達することがあります。一方、POM(ポリアセタール)やPC(ポリカーボネート)などは比較的吸水率が低い材料です。
水分を吸収すると、樹脂には次のような変化が起こります。水分を含むことで体積が増加し、部品の寸法が大きくなります。一般的に、吸水すると引張強度や曲げ強度、剛性が低下します。また、絶縁性が低下する場合があります。部品設計においては、こうした吸水による物性の変化を予め想定しておくことが重要です。
【設計への影響】
浴室や厨房設備、屋外で使用される部品など、湿度が高い環境や水に触れる環境では、吸水による寸法変化を考慮した設計(クリアランス設定など)が必要です。精密な寸法精度が求められる部品には、吸水性の低い樹脂を選ぶか、吸水率を考慮した公差設定が求められます。
部品の強度計算を行う際には、乾燥状態だけでなく、想定される吸水状態での物性値を考慮する必要があります。特にPA(ポリアミド、ナイロン)系の材料を使用する場合は注意が必要です。使用環境の湿度条件や求められる寸法安定性に応じて、適切な吸水特性を持つ樹脂材料を選定することが重要です。材料メーカーのデータシートで飽和吸水率や吸水時の寸法変化率、物性変化を確認しましょう。吸水性は、金属設計ではほとんど考慮しない要素ですが、樹脂、特にPA系のエンプラを使う際には必ずチェックすべき重要な特性です。
耐候性・耐薬品性──樹脂の得意・不得意を知る
屋外での使用や、特定の化学薬品に触れる環境では、耐候性(紫外線、雨風への耐性)や耐薬品性が問題になります。
金属
鉄は錆びやすいですが、ステンレス鋼やアルミニウム、亜鉛メッキ鋼板などは比較的高い耐候性・耐食性を持ちます。酸やアルカリに対しては、金属の種類によって耐性が異なります。
樹脂(エンプラ)
防錆性に優れる点は大きなメリットです。水や湿気による錆の心配がありません。しかし、紫外線に対しては、劣化しやすい(変色、強度低下、表面のひび割れなど)樹脂が多いです。屋外で使用する場合は、耐候性グレードの材料を選んだり、塗装や表面コーティングを施したりする必要があります。耐薬品性は、樹脂の種類と薬品の種類(酸、アルカリ、有機溶剤、油など)の組み合わせによって大きく異なります。ある薬品には強くても、別の薬品には弱いというケースが普通です。
【設計への影響】
部品がどのような環境(屋外/屋内、紫外線暴露の有無、接触する可能性のある薬品の種類・濃度・温度など)で使用されるかを正確に把握することが、適切な材料選定の第一歩です。材料メーカーは、各種薬品に対する耐性データや、耐候性試験の結果を提供しています。これらを参考に、使用環境に適した材料を選定します。当社は材料メーカー各社と緊密な関係を有しています。ご不明な場合は当社までお気軽にお問い合わせください。
標準グレードで耐性が不足する場合は、耐候性向上剤や紫外線吸収剤が添加されたグレードや、特定の薬品に強いグレードを検討します。あるいは、後加工で塗装やコーティングを行うことも選択肢となります。錆びないというメリットがある一方で、紫外線や薬品に対する弱点は樹脂ごとに異なります。「この樹脂なら大丈夫だろう」と決めつけず、必ず使用環境との適合性を確認しましょう。
加工性と設計自由度──樹脂は“一体化”が得意
部品を目的の形状に作り上げる加工性と、それによって実現できる形状の自由度も、金属と樹脂では大きく異なります。
金属
切削(削る)、板金プレス(曲げる・抜く)、鋳造(溶かして型に流す)、鍛造(叩いて成形する)、溶接(繋ぎ合わせる)など、様々な加工法がありますが、複雑な形状を作るためには複数の工程や部品の組み合わせが必要になることが多くあります。
樹脂(エンプラ)
射出成形という加工法が主流です。これは、溶かした樹脂を高圧で金型に射出し、冷却して固める方法で、非常に複雑な形状でも一度の工程(ワンショット)で大量に生産できるのが最大の特長です。
【設計への影響】
射出成形では、従来は複数の金属部品を組み合わせて作っていた機能を、一つの樹脂部品に一体化することが可能です。例えば、ブラケット、ボス(ネジ穴の土台)、リブ(補強)などをまとめて一つの部品として設計できます。これにより、部品点数、組立工数、管理コストを大幅に削減できます。金属加工では難しい滑らかな三次元曲面や、スナップフィット(はめ込み式の爪)のような樹脂特有の形状も比較的容易に実現でき、デザイン性や機能性の向上に繋がります。
非常に自由度が高い射出成形ですが、万能ではありません。金型から製品を取り出すための抜き勾配が必要だったり、アンダーカットと呼ばれる金型がそのままでは抜けない形状には特殊な金型構造(スライドコアなど)が必要になったりします。また、肉厚が不均一だとヒケや反りといった成形不良の原因になるため、適切な肉厚設計も重要です。射出成形による「一体化」と「複雑形状の実現」は、金属代替による大きなメリットですが、その恩恵を最大限に受けるためには、射出成形の原理や制約を理解した設計が求められます。
まとめ:違いを知ることから、最適な設計は始まる
ここまで、金属と樹脂の基本的な素材特性の違いを6つのポイントで見てきました。比重、剛性、耐熱性、吸水性、耐候性・耐薬品性、そして加工性。どれをとっても、両者には大きな違いがあることがお分かりいただけたかと思います。繰り返しますが、樹脂は単なる「軽い金属」ではありません。 見た目や寸法が同じ部品であっても、その「中身」=素材特性は全く異なり、設計で考慮すべき点も根本的に違います。金属部品の代替を検討する際には、まずこの「素材の性格の違い」をしっかりと認識することがスタートラインです。そして、それぞれの特性を踏まえ、「なぜ金属ではこの設計だったのか?」「樹脂の特性を活かすにはどう設計すべきか?」「樹脂の弱点をどう補うか?」という視点で、考え方を転換する必要があります。
今回のコラムで紹介した基本的な違いを理解した上で、さらに詳細な物性の違い(例えば、熱による変形のしやすさの違いである線膨張係数、時間とともに変形が進むクリープ現象、繰り返し荷重に対する弱さである疲労特性など)を知ることが、より安全で高性能な樹脂部品を設計するための次のステップとなります。金属代替は、単なる材料の置き換えではなく、設計そのものを見直すチャンスでもあります。まずは「違い」を正しく理解することから始めましょう。