【徹底解説】PC(ポリカーボネート)の特性と用途(後編):設計・成形の勘所
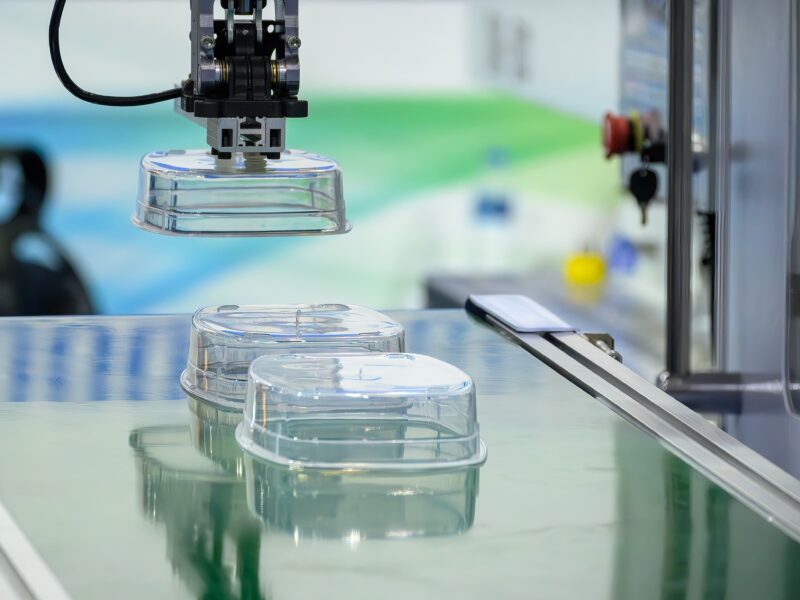
前編では、PC(ポリカーボネート)が持つ「高い透明性」、「卓越した耐衝撃性」、「良好な耐熱性と寸法安定性」、「難燃性」、「耐薬品性の限界」といった基本的な特性について詳しく解説しました。これらの特性は、PCを数多くの製品で採用する上での大きな魅力となっています。
本コラム後編では、前編で明らかにしたPCの優れた特性を、実際の製品開発においてどのように活かしていくかという、より実践的な側面に焦点を当てます。具体的には、PCがどのような代表的な用途で使用され、その際に設計上どのようなポイントが重要となるのかを解説します。さらに、高品質なPC製品を安定して得るために不可欠な、成形プロセスにおける注意点についても詳しく掘り下げていきます。前編で得たPCの基礎知識を土台に、そのポテンシャルを最大限に引き出すための「勘所」を掴んでいきましょう。
代表的な用途と設計時のポイント
PCの優れた特性は、多岐にわたる分野で活用されています。ここでは代表的な用途と、それぞれの設計時に考慮すべきポイントを解説します。
照明カバー、レンズ、ディスプレイ保護部品など光学部品
PCは、その高い透明性と良好な耐熱性、耐衝撃性から、様々な光学部品に採用されています。LED照明のカバーやレンズ、自動車のヘッドランプレンズやインナーレンズ、コピー機やスキャナーの読取り窓、液晶ディスプレイや有機ELディスプレイの表面保護パネル、導光板、カメラレンズの一部など。
要求特性
– 高透明性・低ヘイズ:光の損失を最小限に抑え、クリアな視界や配光性能を確保する。
– 光学的均一性:屈折率のムラや内部歪みが少ないこと。特にレンズ用途では重要。
– 耐候性:屋外使用や照明器具などでは、紫外線による黄変や物性低下を防ぐ必要がある。
– 耐熱性:光源からの熱や、夏場の車内など高温環境下での変形を防ぐ。
設計時のポイント:
– 光学グレードの選定:異物管理が徹底され、黄変しにくい配合が施された光学グレードや、UVカット性能を付与したグレードを選定します。
– ヘイズ対策:材料選定だけでなく、金型表面の仕上げ(鏡面仕上げ)が重要です。また、成形条件(射出速度、保圧、金型温度)の最適化により、フローマークやシルバーストリーク、内部応力による複屈折を低減します。
– ゲート設計:光学的に重要な部分にウェルドラインやジェッティングが発生しないよう、ゲート位置、種類、サイズを慎重に検討します。レンズなどの厚肉品では、ヒケやボイドを防ぐための適切なゲート設計と保圧設定が不可欠です。
– リブ・肉厚設計:急激な肉厚変化はヒケや内部応力の原因となるため、滑らかな肉厚変化を心がけます。光学部品では、リブが影として映り込まないような配置も考慮します。
– アンチグレア・ハードコート処理:ディスプレイ保護部品では、反射防止(アンチグレア)や表面硬度向上(ハードコート)のための二次加工も一般的です。これらのコーティング材との密着性も考慮が必要です。
筐体、透明カバー、機構部品
PCの優れた耐衝撃性と適度な剛性は、様々な機械部品や筐体に適しています。電動工具のハウジング、家電製品の筐体や操作パネル、OA機器の内部機構部品やカバー、スマートフォンの筐体、ヘルメットや保護シールドの帽体、スーツケースなど。
要求特性
– 高耐衝撃性:落下衝撃や外部からの衝撃に対する耐久性。
– 剛性・強度:構造部材としての強度、荷重に対する変形の少なさ。
– 寸法安定性:温度や湿度変化に対する寸法変化の少なさ、精密な嵌合(かんごう)精度。
– 難燃性:電気製品の筐体などでは、UL規格などの難燃性が要求される。
設計時のポイント
– ガラス繊維強化PCの活用:より高い剛性、強度、耐クリープ性が求められる場合は、ガラス繊維を配合した強化グレードを検討します。ただし、透明性は失われ、異方性(成形方向による物性の違い)やソリが発生しやすくなるため注意が必要です。
– 二次加工との相性:塗装、印刷、接着、溶着、メッキなどの二次加工を行う場合、PCとの相性を確認します。特に溶剤系の塗料や接着剤はケミカルクラックを引き起こすリスクがあるため、PC対応品を選定するか、応力のかかりにくい設計、プライマー処理などを検討します。超音波溶着やレーザー溶着は比較的相性が良い接合方法です。
– 応力集中の緩和:衝撃を受ける可能性のある部品では、コーナー部にRを設ける、リブの根元にRを付けるなど、応力集中を避ける設計が重要です。
– 嵌合設計:圧入やスナップフィット設計では、PCのクリープ特性(長時間荷重がかかると変形が進む現象)や応力緩和を考慮し、適切な締め代や勘合力を設定します。
– ネジ止め設計:タッピンネジを使用する場合は、下穴径やネジの種類を適切に選定し、過度な締め付けトルクを避けます。インサートナットの使用も有効です。
安全ゴーグル、フェイスシールド等の医療、安全部品
PCの透明性、耐衝撃性、そして一部グレードでは生体適合性や滅菌耐性を持つことから、医療分野や安全保護具にも広く用いられています。安全ゴーグル、フェイスシールド、ヘルメットのバイザー、医療機器のハウジングや透明カバー、血液透析器(ダイアライザー)のハウジング、注射器のシリンジ(一部)、実験用器具など。
要求特性
– 高耐衝撃性・飛散防止性:作業者の目や顔を飛来物から保護する。
– 透明性:クリアな視界の確保。
– 耐薬品性:消毒液(アルコール、次亜塩素酸ナトリウムなど)への耐性。
– 滅菌耐性:ガンマ線滅菌、エチレンオキサイドガス(EOG)滅菌、オートクレーブ滅菌(一部グレード)などへの対応。
– 生体適合性:体液や組織と接触する用途では、ISO10993などに適合する医療用グレードが必要。
設計時のポイント:
– 薬品暴露・応力クラックへの注意:消毒作業などでアルコールやその他の薬品に頻繁に接触する場合、ケミカルクラックのリスクが高まります。残留応力を低減する成形条件の選定やアニール処理、あるいは耐薬品性に優れたコーティングを施すなどの対策を検討します。特に、応力が集中しやすい箇所(曲げ部、固定部など)は注意が必要です。
– 滅菌方法の選定と材料適合性:採用する滅菌方法によって、PCの物性(特に透明性や衝撃強度)が影響を受ける場合があります。ガンマ線滅菌は黄変を引き起こしやすく、オートクレーブ滅菌(高温高圧蒸気)は加水分解による強度低下のリスクがあります。滅菌耐性のある専用グレードを選定するか、影響の少ない滅菌方法を選択します。
– 快適性・装着性(保護具の場合):ゴーグルやフェイスシールドでは、軽量性、顔へのフィット感、曇り防止(防曇コーティング)なども重要な設計要素となります。
– バリ・エッジ処理:医療用途や皮膚に接触する部品では、バリやシャープエッジが残らないよう、金型設計や仕上げ処理に注意が必要です。
成形上の注意点
PCは優れた材料ですが、その特性を最大限に活かすためには、成形プロセスにおけるいくつかの重要な点に注意を払う必要があります。特に吸湿管理と温度管理は、品質を左右する最重要ポイントです。
乾燥条件
PCは吸湿性が比較的低い(飽和吸水率0.35%程度)とされていますが、それでも成形前に十分な予備乾燥が不可欠です。ペレットが水分を吸収したまま高温のシリンダー内で溶融されると、加水分解という化学反応が起こります。加水分解はPCの分子鎖を切断し、分子量を低下させます。その結果、特に衝撃強度が大幅に悪化し、PC本来の靭性が失われ脆くなります。シルバーストリーク(銀条)と呼ばれる放射状の筋模様が発生し、外観を損ねます。
また、溶融樹脂の粘度低下により鼻たれや発泡が発生します。これらを防ぐため、一般的な乾燥条件は、120~130℃の熱風乾燥機で4時間以上とされています。ペレットの水分率を0.02%以下にすることが推奨されます。大型のホッパーローダーを使用する場合は、中心部まで十分に乾燥が進むように、より長時間の乾燥や、除湿乾燥機の使用が望ましいです。乾燥が不十分な場合、透明部品ではシルバーストリークが顕著に現れるため、成形初期のトライで確認できます。一度加水分解を起こした材料は元に戻らないため、乾燥管理はPC成形の基本中の基本と言えます。
金型温度と成形温度
適切な温度管理は、PC成形品の品質に大きく影響します。金型温度は、一般的に80~120℃の範囲で設定されます。金型温度が高いほど、溶融樹脂の流動性が向上し、金型キャビティへの充填がスムーズになります。これにより、薄肉製品や複雑形状品でもショートショット(充填不足)を防ぎやすくなります。また、高い金型温度は金型表面の転写性を向上させ、光沢のある美しい表面を得やすくなります。特に光学部品では重要です。さらに、成形品が金型内でゆっくり冷却されるため、残留応力が低減され、反りやクラックのリスクを抑える効果があります。ただし、金型温度が高すぎると冷却時間が長くなり、成形サイクルが伸びて生産性が低下します。また、製品の離型時に変形しやすくなることもあります。
成形温度(シリンダー温度)は、一般的に270~320℃の範囲で設定されます。グレードや成形機の種類、製品の肉厚や形状によって最適な温度は異なります。温度が低すぎると溶融粘度が高くなり、充填不足やフローマーク、ウェルドラインの強度低下を引き起こします。温度が高すぎると樹脂の熱分解が始まり、黄変、黒点、ガス焼け、強度低下の原因となります。特にシリンダー内での滞留時間が長い場合は注意が必要です。ノズル温度は、糸引きや鼻タレを防ぐためにシリンダー設定温度よりやや低めに設定することがあります。
金型温度と成形温度は相互に関連しており、製品の要求品質、使用するPCグレード、成形サイクルなどを考慮して最適化する必要があります。
離型性
PCは、溶融時の金型への付着性がやや高く、離型性はあまり良くありません。特に透明グレードや高光沢が求められる製品では、離型剤を成形品に直接塗布したり、金型に頻繁にスプレーしたりすることが外観や後加工(塗装、接着など)の観点から困難な場合があります。
そのため、金型設計段階での配慮が重要になります。十分な抜き勾配(通常1°以上、深物では2~3°以上)を設けることが基本です。鏡面仕上げにしすぎると真空吸着しやすくなる場合があります。適切な表面粗度や、微細なシボ加工を検討することもあります(透明性が求められない場合)。製品が均等に、かつ変形しないように突き出せるよう、エジェクタピンの数、位置、面積を適切に設計します。アンダーカット処理が必要な場合は、スライドコアや傾斜ピンの設計も重要です。金型鋼材の選定や、窒化処理、PVDコーティングなどの表面処理によって離型性を向上させることができます。離型時にエアを吹き付けて離型を助けることもあります。
代表的なトラブル
PC成形では、以下のようなトラブルが発生しがちです。原因と対策を理解しておくことが重要です。
– シルバーストリーク(銀条)
原因:ペレットの乾燥不足による水分、樹脂の熱分解による発生ガス、エアーベント不良による空気の巻き込み。
対策:十分な予備乾燥、成形温度の適正化(下げ方向)、シリンダー内滞留時間の短縮、金型のエアーベント設計の見直し、射出速度の調整。
– フィッシュアイ
原因:未溶融の樹脂ペレット、異種樹脂の混入、シリンダー内の炭化物。
対策:成形温度(特に後部)の確認・調整、スクリュー背圧の調整による混練性の向上、材料ホッパーやシリンダーの清掃、材料の適切な管理。
– ガス焼け・黒点(ヤケ)
原因:エアーベント不良による断熱圧縮、樹脂の過熱・滞留による熱分解。
対策:金型のエアーベントの設置・清掃、射出速度の低減、成形温度の適正化、シリンダー内滞留時間の短縮(型替え時のパージ徹底など)。
ヒケ・ボイド
原因:成形収縮に対する樹脂の補給不足。特に厚肉部で発生しやすい。
対策:保圧の最適化(高く、長く)、ゲート径の拡大、ゲート位置の変更、製品肉厚の均一化、金型温度の調整。
反り・変形
原因:成形品内の残留応力、不均一な冷却、金型設計(突き出しなど)。
対策:金型温度の均一化と適正化(高めに設定)、保圧・冷却時間の最適化、製品肉厚の均一化、アニール処理。
ウェルドラインの強度不足
原因:合流する樹脂温度の低下、空気の巻き込み。
対策:成形温度・金型温度の上昇、射出速度の調整、ゲート位置の変更、ガスベントの設置。
内部応力によるクラック
PCは応力に敏感で、特に残留応力が高い状態で特定の薬品に接触したり、衝撃が加わったりするとクラックが発生しやすいです。偏光板を使用して成形品内の残留応力を可視化し、応力集中箇所を特定できます。対策としては、金型温度を高めに設定する、保圧を適切にする、アニール処理(120℃程度で数時間)を行うなどが有効です。
まとめ
本コラムでは、前編・後編の2回にわたり、PCの基本特性から代表的な用途、そして設計および成形上の注意点について実務的な観点から解説してきました。
前編では、PCが持つ高い透明性、卓越した耐衝撃性、良好な耐熱性・寸法安定性、難燃性といった魅力的な特性と、その一方で注意すべき耐薬品性の限界などを確認しました。
後編では、これらの特性を活かした光学部品、機械部品、医療・安全部品といった具体的な用途例と、それぞれの設計における重要なポイントを提示しました。さらに、高品質なPC製品を実現するために不可欠な、成形前の乾燥処理、金型温度と成形温度の適切な設定、離型性の確保、そして代表的な成形トラブルとその対策について詳述しました。
PCは、汎用エンプラの中でも特にバランスに優れた高機能素材であり、その可能性は多岐にわたります。しかし、そのポテンシャルを最大限に引き出すためには、材料特性への深い理解に基づいた用途に応じたグレード選定と、設計段階からの緻密な配慮、そして成形条件の最適化が不可欠です。これらの要素が適切に組み合わさることで、PCは設計者の意図を忠実に反映した、信頼性の高い製品として具現化されます。
近年では、さらなる高機能化や環境対応型のPC開発も進んでおり、今後もPCは設計者にとって「第一候補」となり得る重要な材料であり続けるでしょう。本コラムが、PCという素材の理解を深め、より効果的に活用するための一助となれば幸いです。