「製品の身分証明書」DPPとは何か?設計者が今知るべき背景と今後の対応
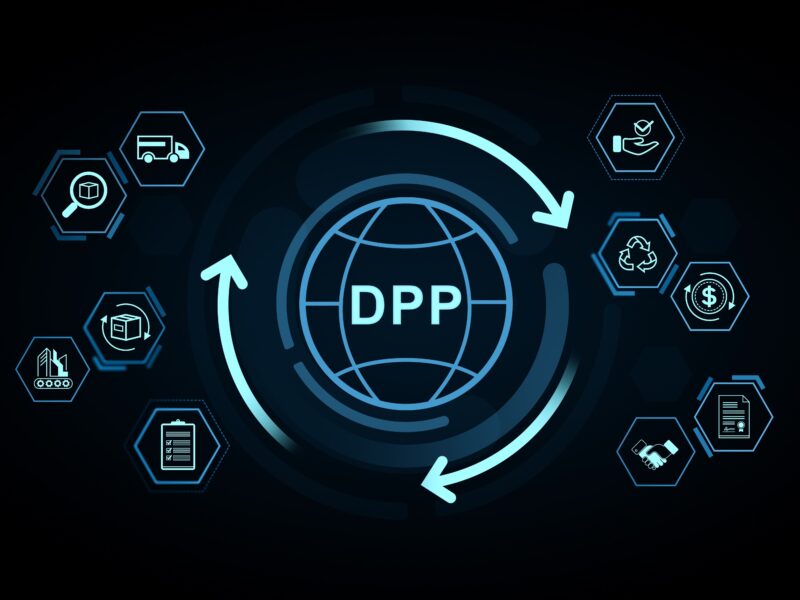
製造業において、製品のライフサイクル全体にわたる「見える化」は、DX推進の波とともに加速しています。特に、地球環境への配慮と持続可能な社会の実現を目指すサーキュラーエコノミー政策が世界的に進展する中で、製品に関する情報の透明性確保は喫緊の課題です。この大きな流れの中で登場したのが、「デジタルプロダクトパスポート(DPP)」です。これは、いわば「製品の身分証明書」とも呼べるもので、製品がどこで生まれ、どのような素材で構成され、どのように修理・リサイクルできるのかといった情報を、デジタルで追跡可能にする仕組みです。
このDPPは、最終製品メーカーだけでなく、その製品を構成する部品や材料の設計・選定に携わる設計者にとっても、決して無関係ではありません。むしろ、製品の初期段階である設計こそが、DPPに記載される情報の質や製品の持続可能性を大きく左右するのです。本コラムでは、DPPの概要から、設計者がDPPとどのように関わり、どのような課題に直面し、そして今後どのように対応していくべきか、その方向性について解説します。
DPPとは何か? ─ 製品の持続可能性情報を集約するデジタルな仕組み
DPPは「Digital Product Passport」の略称で、製品の持続可能性に関する情報を電子的に記録し、サプライチェーン全体で共有・追跡可能にするための仕組みです。その主な目的は、製品の透明性を高め、修理やリサイクルの促進、さらには資源効率の向上を通じてサーキュラーエコノミー(循環経済)への移行を加速することにあります。具体的には、製品に付随する「デジタルな情報ラベル」として、以下のような多岐にわたる情報が紐づけられることが想定されています。設計者としては、これらの情報が自らの設計判断や情報管理とどう結びつくのかを理解することが重要です。
① 材料構成: 使用されている素材の種類、リサイクル材の含有率、特定の化学物質(例:REACH規則の高懸念物質SVHC)の有無や濃度など。設計段階での材料選定が直接的に関わります。
② 製造情報: 製造プロセスにおけるエネルギー消費量、CO2排出量、使用水の量など。設計段階での材料選択や部品点数の削減が、これらの環境負荷に影響を与える可能性があります。
③ 修理性・耐久性: 修理の可否、修理マニュアルや診断ツールへのアクセス、スペアパーツの入手可能性や価格、製品の期待寿命など。製品の構造設計、部品のモジュール化、標準化などが鍵となります。
④ リサイクル性・解体性: 解体の容易さ、リサイクル可能な材料の特定、リサイクル方法、リサイクル工程で回収可能な材料情報、有害物質の分離方法など。材料の種類の統一、異材接合の回避、分解しやすい締結方法の採用といった設計配慮が求められます。
⑤ サプライチェーン情報: 主要な部品の供給元、製造拠点など、製品のトレーサビリティに関する情報。
⑥ その他: 製品の取扱説明書、安全に関する情報、認証情報など。
このDPP導入の動きは、特にEU(欧州連合)が主導しており、2022年に提案された「エコデザイン規則(ESPR: Ecodesign for Sustainable Products Regulation)」において、その法的枠組みが示されました。ESPRは、従来のエネルギー効率中心のエコデザイン指令を大幅に拡張し、製品の耐久性、修理可能性、リサイクル可能性、リサイクル材含有率、カーボンフットプリントなど、より広範な持続可能性要件をほぼ全ての物理的製品に課すものです。DPPは、これらのESPRが求める情報を収集・伝達するための重要なツールとして位置づけられています。
DPPの導入は製品カテゴリごとに段階的に進められる計画で、最初の対象として電池が挙げられており、続いて繊維製品、電子機器、建設資材、プラスチック、化学物質などが有力視されています。具体的な導入スケジュールや詳細な情報要件は、各製品カテゴリの特性に応じて、今後「委任規則」という形で定められていくことになります。
DPPと設計者が関係するポイント ─ 設計段階からの情報創出と持続可能性の織り込み
DPPの導入は、最終製品メーカーだけでなく、製品の企画・設計段階から深く関わる設計者に大きな影響を及ぼします。なぜなら、DPPに記載される情報の多くは、設計段階での意思決定や情報管理にその源流があるからです。
まず、材料選定と化学物質管理の重要性が格段に高まります。 DPPでは、使用されている材料の種類、リサイクル材の含有率、そして特定の有害化学物質(例えばREACH規則で規制されるSVHCや、RoHS指令で制限される物質)の含有状況などを詳細かつ正確に開示することが求められます。これは、設計者が材料を選定する際に、単に機能やコストだけでなく、環境負荷、リサイクル性、含有化学物質のリスクといった情報をサプライヤーから入手し、評価・管理しておく必要があることを意味します。例えば、リサイクル材を積極的に採用した設計や、有害化学物質を意図的に排除した設計は、DPPを通じてその価値が「見える化」されることになります。
次に、製品の修理可能性、耐久性、リサイクル性を考慮した設計(エコデザイン)が一層強く求められます。 DPPには、修理マニュアルへのアクセス方法やスペアパーツの入手可能性、製品の解体手順やリサイクル可能な材料の情報などが含まれるため、設計段階からこれらの要素を織り込むことが不可欠です。
① 修理しやすい設計: モジュール構造の採用、標準的な工具で分解・交換可能な部品の使用、故障診断の容易化など。
② 耐久性の高い設計: 長期間の使用に耐える材料の選定、堅牢な構造設計、アップグレード可能な設計など。
③ リサイクルしやすい設計: 単一素材の使用、異材の分離容易性、リサイクル時に問題となるラベルや接着剤の回避、プラスチック部品への材質表示など。
これらの設計配慮は、製品のライフサイクル全体での環境負荷低減に貢献し、DPPを通じてその取り組みが評価されることになります。
さらに、設計プロセスにおける情報管理とトレーサビリティの確保が重要になります。 設計者が選定した部品や材料に関する情報は、サプライヤーから正確な形で入手し、製品構成情報(BOM)と紐づけて管理する必要があります。また、設計変更があった場合には、その変更がDPPに記載される情報にどのような影響を与えるのかを把握し、関連情報を更新するプロセスも必要となります。
「DPPに登録される製品情報」は誰が管理するのか? 最終的には製品を市場に出す最終製品メーカーがDPPの情報を集約し、その正確性に責任を持つことになります。しかし、その元となるデータの多くは、部品サプライヤーや材料メーカーから提供される必要があり、そしてどのような部品や材料を使い、どのような製品構造にするかを決定する設計者こそが、DPPに記載されるべき情報の「創出者」であり「初期管理者」であると言えます。 設計部門と調達部門、品質保証部門、さらにはサプライヤーとの緊密な連携なくして、正確で信頼性の高いDPPは成り立ちません。
設計者として具体的にDPPを意識して取り組むべき情報管理や設計配慮の例としては、以下のようなものが考えられます。
① 使用材料・部品の詳細情報の記録: 材料グレード、メーカー名、リサイクル材含有率の証明、含有化学物質の安全性データシート(SDS)や分析データ、各種認証情報などを収集・管理する。
② リサイクル適性情報の考慮: 材料の種類(例:PP、ABS、PETなど)を明確にし、リサイクルプロセスを阻害する可能性のある着色剤、添加剤、異材コンタミのリスクを評価する。
③ 修理・解体容易性の設計への反映: 製品の分解手順書(案)の作成、標準部品やモジュール部品の積極的採用、特殊工具を必要としない締結方法の検討など。
④ 設計変更時の影響評価: 部品や材料の変更が、製品の持続可能性情報(特に化学物質情報、リサイクル性など)に与える影響を評価し、関連情報を更新する。
これらの情報を設計段階から意識し、効率的かつ正確に管理・活用できるかが、今後の設計者の競争力、ひいては企業の競争力を左右する重要なポイントとなるでしょう。
日本企業の対応状況とDPP導入に向けた設計現場の課題
DPPへの対応は、特に欧州市場と直接取引のある大手企業や、グローバルなサプライチェーンに深く関わる自動車産業や電機・電子産業などを中心に進みつつあります。これらの企業では、EUの規制動向をいち早く察知し、社内体制の整備やサプライヤーへの情報提供要求を開始しています。しかし、多くの日本企業、特にサプライチェーンの下流に位置する企業や、リソースの限られる中小企業にとっては、DPPはまだ遠い話と感じられたり、何から手をつければよいか戸惑ったりしているのが実情かもしれません。設計現場がDPPに対応していく上で直面する可能性のある課題としては、以下のようなものが挙げられます。
① 情報収集・管理の負荷増大: DPPで求められる情報は多岐にわたり、かつ詳細です。特にサプライヤーからの化学物質情報やリサイクル材含有率証明などを正確に入手・管理するには、多大な工数とシステム対応が必要となる可能性があります。
② 設計プロセスの変更と新たな知識習得: 従来は機能やコストが優先されがちだった設計プロセスに、環境配慮や情報開示といった新たな視点を組み込む必要があります。LCA(ライフサイクルアセスメント)の知識、エコデザインの手法、関連法規制(REACH、RoHSなど)への深い理解などが求められます。
③ サプライヤーとの連携強化と情報共有の壁: DPPに必要な情報は自社だけでは完結せず、多数のサプライヤーからの協力が不可欠です。しかし、サプライヤー側の対応遅れや、企業秘密を理由とした情報開示の困難さ、情報フォーマットの不統一といった課題に直面する可能性があります。
④ データ標準化の動向とシステム対応: DPPで扱われるデータのフォーマットや連携方法は、現在国際的にも標準化が進められている段階です。どの標準に対応すべきかを見極め、社内の設計ツール(CAD、PLMなど)や情報管理システムを対応させていくには、投資と時間が必要です。
⑤ 部門横断的な連携体制の構築: DPP対応は設計部門だけでなく、調達、品質保証、製造、法務、ITなど、多くの部門が関わります。これらの部門間でのスムーズな情報共有と協力体制を構築することが不可欠ですが、組織の壁が障害となることもあり得ます。
これらの課題を解決するためには、個々の設計者の努力だけでなく、企業全体としての戦略的な取り組み、業界団体や関連省庁からの支援、そしてITツールやコンサルティングサービスの活用などが重要になります。
設計者としての現実的な備え ─ 今から始めるDPP時代への対応
DPPの本格導入までにはまだ時間があるとはいえ、設計者として今からできる備えは少なくありません。むしろ、早期に着手することで、将来的な混乱を避け、環境性能の高い製品開発を通じて競争優位性を築くことにも繋がります。
まず、「今から始められること」として、自らの設計プロセスと情報管理体制の見直しが挙げられます。
① 材料・部品選定基準のアップデート: 機能・コストに加え、環境負荷(リサイクル性、含有化学物質リスク、カーボンフットプリントなど)を材料・部品選定の重要な評価軸として組み込む。
② サプライヤーからの情報収集強化: サプライヤーに対して、DPPで求められる可能性のある情報(例:詳細な材料組成、リサイクル材含有率、SVHC非含有証明など)を積極的に要求し、入手した情報を体系的に管理する。
③ 設計情報のデジタル化と一元管理: 設計図面、BOM、材料仕様書、化学物質情報などを、PLMシステムなどを活用してデジタルで一元的に管理し、トレーサビリティを確保する。
④ エコデザイン手法の学習と実践: 修理しやすい設計、解体しやすい設計、リサイクルしやすい材料選定といったエコデザインの原則を学び、実際の製品設計に取り入れてみる。
DPPへの対応は、初期投資や体制構築の負担から「コスト増」と捉えられがちですが、視点を変えれば「製品価値向上と競争力の源泉」となり得ます。環境意識の高い顧客からの評価向上、新たなビジネスチャンスの獲得、さらには自社の設計プロセスの効率化や無駄の削減にも繋がる可能性があります。
まとめ
デジタルプロダクトパスポート(DPP)は、単にEUの新しい「環境規制」として捉えるべきではありません。むしろ、それは製品のライフサイクル全体における透明性を高め、持続可能な社会を実現するための「信頼される製品づくり」の要となる仕組みであり、製品の「身分証明書」にどのような情報を書き込むかを決定する上で、設計者は極めて重要な役割を担います。
この変化は、確かに設計者にとって新たな学習コストや情報管理の負荷をもたらす側面もあります。しかし、見方を変えれば、自らが設計した製品の優れた環境性能や安全性を客観的なデータで示し、顧客や社会からの信頼を獲得する絶好の機会でもあります。これからの時代は、正確なデータを持ち、それを設計に活かし、適切に開示・活用できる設計者、そして企業が選ばれます。
設計者も、サプライチェーンの一員として受け身で対応するのではなく、DPPの動きを先読みし、主体的な情報収集とエコデザインの実践を通じて、自らのスキルと製品の価値を高めていく積極的な姿勢が求められています。