EU新エコデザイン規則(ESPR)徹底解説 ─ DPPの親法規、製造業へのインパクトと対応戦略
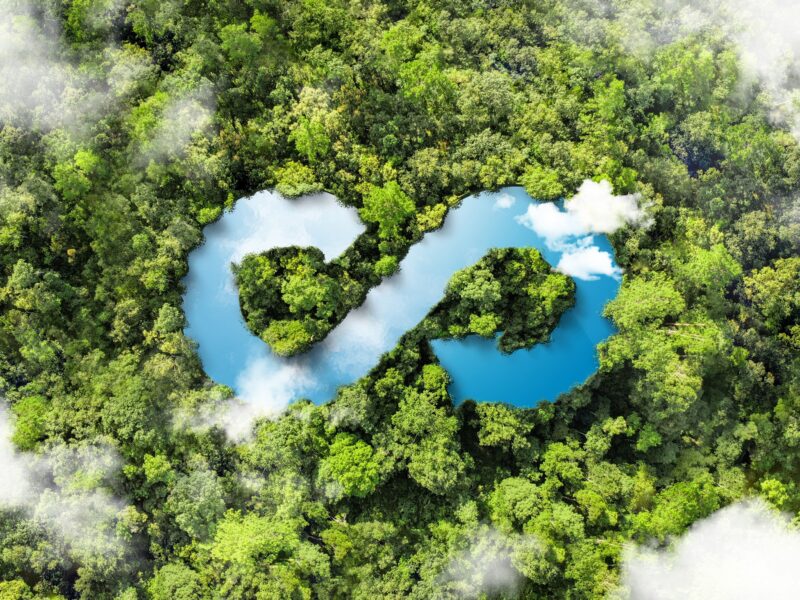
地球規模での環境問題が深刻化し、持続可能な社会への移行が国際的な共通目標となる中、欧州連合(EU)が打ち出す環境政策は、世界の産業構造に大きな変革を迫っています。その中核をなす取り組みの一つが、2022年に公表され、現在最終調整が進む「エコデザイン規則(ESPR: Ecodesign for Sustainable Products Regulation)」です。このESPRは、EU市場で販売される製品の環境性能基準を大幅に引き上げ、製品のライフサイクル全体を通じた持続可能性を追求するものであり、日本の製造業にとっても対岸の火事ではありません。
先に解説したDPP(デジタルプロダクトパスポート)は、このESPRが求める製品情報を収集・伝達するための重要なツールとして位置づけられています。本コラムでは、ESPRが具体的に何を目指し、従来の規制とどう異なり、DPPとどのように連携するのかを深掘りします。そして、この新たな規制の波が日本の製造業、特にグローバルサプライチェーンに組み込まれる多くの企業にどのようなインパクトを与え、いかにして備えるべきか、その方向性を探ります。
ESPRとは何か? ─ 製品のライフサイクル全体を捉える新基準
ESPR、正式には「持続可能な製品のためのエコデザイン要件を設定するための規則案」は、EUの包括的な環境政策である「欧州グリーンディール」および「サーキュラーエコノミー行動計画」の実現に向けた最重要施策の一つとして位置づけられています。その根本的な目的は、EU市場に出回る製品の環境負荷を、製品の設計段階から廃棄・リサイクルに至るまでのライフサイクル全体で低減し、持続可能な製品をEU市場における「標準」とすることにあります。
ESPRは、これまで主にエネルギー関連製品(家電、照明器具など)を対象としてきた「エコデザイン指令(ErP指令: Energy-related Products Directive 2009/125/EC)」を大幅に拡張・刷新するものです。従来のErP指令との主な違いは以下の2点に集約されます。
第一に、対象製品の大幅な拡大です。ErP指令がエネルギー消費効率に焦点を当てていたのに対し、ESPRは原則として食品、飼料、医薬品、動物用医薬品を除くほぼ全ての物理的な製品を対象範囲に含めることを目指しています。これにより、繊維製品、家具、建設資材、鉄鋼、アルミニウム、セメント、化学物質、ICT製品、電子機器など、極めて広範な産業分野が影響を受けることになります。
第二に、要求事項の深化・多様化です。エネルギー効率の向上は引き続き重要な要素ですが、ESPRではそれに加えて、製品の耐久性、信頼性、修理可能性、アップグレード可能性、再利用可能性、リサイクル性(リサイクル材含有率目標や解体の容易さを含む)、製品のカーボンフットプリント、特定の懸念物質の使用制限や追跡など、より多角的かつ具体的な持続可能性要件が導入されます。
ESPRは、製品が環境に与える影響の約80%が設計段階で決定されるという認識に基づき、製品開発の上流工程から環境配慮を義務付けることで、資源消費の抑制、廃棄物の削減、そして循環型経済への移行を強力に推進しようとしています。この「ライフサイクル思考」こそが、ESPRを理解する上で最も重要なキーワードと言えるでしょう。
ESPRが製品に求める新たな要求事項
ESPRが製品に求める新たな要求事項は多岐にわたり、従来の製品安全や品質基準とは次元の異なる、包括的な「持続可能性」の確保を目指しています。以下に主要なエコデザイン要件を挙げます。
① 耐久性・信頼性: 製品が意図した期間、適切に機能し続けること。早期の故障や陳腐化を防ぐ設計が求められます。
② 修理可能性: 製品が故障した場合に、容易かつ経済的に修理できること。これには、修理マニュアルや診断ツールへのアクセス、スペアパーツの適正価格での提供義務(最低保証期間の設定など)が含まれます。
③ アップグレード可能性: 製品の機能や性能を、ソフトウェアの更新や部品交換によって後から向上させられる設計。これにより製品寿命の延長が期待されます。
④ リサイクル性: 製品の寿命が尽きた後、効率的にリサイクルできること。具体的には、解体・分別しやすい設計、使用材料の識別表示、リサイクル材の利用目標設定、再生材含有率の開示などが挙げられます。
⑤ エネルギー効率・資源効率: 製品の製造時および使用時におけるエネルギー消費量、水消費量、原材料使用量を最小限に抑えること。
⑥ カーボンフットプリント: 製品のライフサイクル全体(原材料調達から製造、輸送、使用、廃棄・リサイクルまで)で排出される温室効果ガスの総量を算定し、開示することが求められる可能性があります。
⑦ 有害化学物質の追跡と制限: 製品に含まれる特定の懸念物質(例:REACH規則で規制される高懸念物質(SVHC)など)の使用を禁止または制限し、その含有情報を追跡・開示すること。これにより、安全なリサイクルや人の健康・環境保護が促進されます。
⑧ 売れ残り製品の廃棄禁止: 特に衣料品や履物、電気・電子機器などの売れ残り製品の廃棄を原則禁止し、再利用やリサイクルを促す措置も検討されています。
これらの多岐にわたるエコデザイン要件に関する情報を、消費者、事業者、そして規制当局が容易にアクセスできるようにするための手段として導入されるのが、DPP(デジタルプロダクトパスポート)です。ESPRは、このDPPの導入に関する法的根拠を提供するものであり、製品にQRコードやRFIDタグなどを付し、そこからオンラインで製品の持続可能性情報にアクセスできる仕組みを想定しています。DPPには、材料組成、リサイクル方法、修理マニュアル、カーボンフットプリントといった情報が記録され、サプライチェーンの透明性向上とサーキュラーエコノミーの実現に不可欠な役割を担います。
ESPRに基づく具体的なエコデザイン要件やDPPの詳細は、製品カテゴリごとに「委任規則」や「実施規則」といった下位法令で順次定められていく予定です。優先的に対象となる製品群としては、前述の繊維製品、家具、鉄鋼、アルミニウム、セメント、化学物質、タイヤ、ICT製品、電子機器などが挙げられていますが、これらはEU委員会が今後行う影響評価や協議を経て決定されます。最初の委任規則は2024年以降に採択される見込みであり、企業はこれらの動向を注視し続ける必要があります。
ESPRが日本の製造業、特にサプライチェーンに与える影響
ESPRの導入は、EU市場でビジネスを展開する日本企業にとって、避けては通れない大きな変革を意味します。その影響は、最終製品メーカーだけでなく、部品や素材を供給するサプライチェーン全体に及びます。
まず、直接的な影響を受けるのは、EU市場に製品を輸出している最終製品メーカーです。これらの企業は、ESPRが定める新たなエコデザイン要件を製品設計に織り込み、DPPを通じて関連情報を提供しなければなりません。対応が遅れれば、EU市場へのアクセスが制限されるリスクが生じます。しかし、より広範かつ深刻なのは、間接的な影響、すなわちサプライチェーン全体への波及です。EU向け製品に使用される部品や素材を供給する国内のTier1、Tier2サプライヤー、さらにはその先の原材料メーカーに至るまで、ESPRが求める情報開示の連鎖に組み込まれることになります。例えば、最終製品メーカーが自社製品のDPPを作成するためには、各部品の材料組成、リサイクル性、含有化学物質、製造時の環境負荷といった詳細な情報を、部品サプライヤーから入手する必要があります。これは、成形メーカーであれば使用樹脂のグレード、リサイクル材比率、着色剤情報、エネルギー消費量などを、材料メーカーであれば化学組成や環境フットプリントデータなどを提供する責任が生じることを意味します。
この動きは、製品開発・設計思想の根本的な転換を促します。従来の「作って売る(リニアエコノミー)」モデルから、「長く使ってもらう」「修理して使い続ける」「使用後は資源として循環させる(サーキュラーエコノミー)」モデルへのシフトが不可欠となります。設計段階から、耐久性、修理のしやすさ、解体の容易さ、リサイクルに適した材料選定などを考慮することが標準となり、初期の製造コストだけでなく、製品のライフサイクル全体でのコストや環境負荷を最適化する視点が求められます。
これに対応するためには、情報収集・管理体制の構築が急務となります。製品の材料構成データ、各製造プロセスにおけるエネルギー消費量や排出量、サプライヤーから提供される化学物質情報、LCA(ライフサイクルアセスメント)評価に必要なデータなどを、正確かつ効率的に収集・管理し、必要に応じてDPPなどの形で開示できるシステムやプロセスを整備しなければなりません。サプライチェーン内でのデータ連携とトレーサビリティの確保は、その成否を分ける鍵となるでしょう。
特に、日本企業、とりわけリソースに限りのある中小企業が直面する可能性のある課題は少なくありません。LCA評価手法といった技術ノウハウ、IT投資、専門人材の確保、海外規制への対応遅れによる競争力の低下といったことです。これらの課題を認識し、早期に対策を講じることが、今後の事業継続と成長のために不可欠です。
ESPR時代に向けた製造業の対応戦略と準備
ESPRは大きな変化をもたらしますが、持続可能性を競争力に変える好機です。製造業が取り組むべき対応戦略と準備は次の通りです。
設計思想の転換とR&D投資
– モジュール化設計: 交換・修理・アップグレードを容易にし、製品寿命を延長する。
– 分解・修理しやすい構造: メンテナンス性を高める。
– サステナブル素材の採用: リサイクル材等を利用し、環境性能を高める。
– 設計へのLCA導入: 開発初期から環境負荷を評価・改善する。
情報基盤整備とDX推進
– PLM等活用: 製品情報を一元管理し、トレーサビリティを確保する。
– DPP対応データプロセス: DPP向け情報を収集・管理する体制を整備する。
– SC情報共有基盤: SC全体で効率的な情報共有を検討する。
サプライヤー連携と透明性向上
– SC全体での連携: ESPR要件を共有し、円滑な情報交換を行う。
– 持続可能性情報の開示: 部品・素材の情報をSC内で積極的に共有する。
社内体制構築と人材育成
– 規制動向の把握と共有: 最新情報を収集し、社内に周知する。
– 推進体制の構築: 担当部門の設置や部門横断チームを組成する。
– 専門人材育成・採用: 社員教育や外部活用で対応能力を高める。
ESPR対応は短期的なコスト増もあり得ますが、長期的には競争力強化、新ビジネスモデル創出、資源リスク低減、持続的成長への好機です。環境性能の高い製品は市場で差別化され、循環型設計は持続的成長の鍵となります。
まとめ
EUの新エコデザイン規則(ESPR)は、単なる一地域の環境規制を超え、グローバルな製造業のあり方を根本から変える可能性を秘めた、包括的かつ野心的な取り組みです。製品のライフサイクル全体を通じた持続可能性を追求し、エネルギー効率だけでなく、耐久性、修理性、リサイクル性など、より幅広い側面から製品の環境性能を評価・規制しようとしています。
日本の製造業にとって、ESPRへの対応は大きな挑戦であることは間違いありません。サプライチェーン全体での情報共有、製品設計思想の転換、新たな技術やシステムの導入など、取り組むべき課題は山積しています。しかし、これを乗り越えることは、単に規制をクリアするだけでなく、環境意識の高いグローバル市場で「選ばれる企業」となるための重要なステップです。
その情報伝達の鍵となるのがデジタルプロダクトパスポート(DPP)であり、ESPRとDPPは一体のものとして理解し、対策を講じる必要があります。ESPRの具体的な要求事項は、今後、製品カテゴリごとの委任規則によって詳細化されていきます。企業はこれらの最新動向を常に注視し、変化を先読みしながら、設計、調達、製造、販売、そしてリサイクルに至るまでのバリューチェーン全体で、戦略的かつ段階的に対応を進めていくことが求められます。ESPRの時代は、持続可能なものづくりを通じて新たな価値を創造し、国際競争力を高める好機と捉えるべきでしょう。