射出成形部品設計者必見!材料着色のMOQ上昇に立ち向かう、マスターバッチ活用のススメ
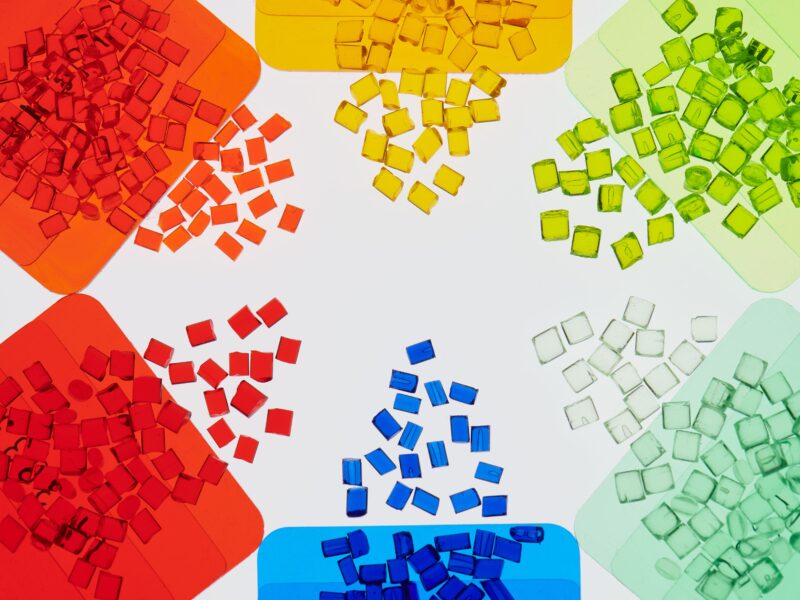
射出成形部品の設計において、「色」は製品の顔であり、ブランドイメージを左右し、時には機能性をも担う重要な要素です。しかし近年、材料メーカーの着色ペレットに対するMOQ(最小発注数量)が引き上げられる傾向にあり、特に小ロット生産や多色展開を必要とする製品の設計者にとって、頭の痛い問題となっています。本コラムでは、こうした状況下でますますその重要性を増している「マスターバッチ」に着目し、射出成形部品の設計者が知っておくべき基礎知識から、MOQ上昇という課題にどう対応できるのか、そして選定・活用における実践的なポイントまで詳しく解説します。
マスターバッチとは何か?:設計者が知るべき基本の「キ」
まず、マスターバッチの基本についておさらいしましょう。
定義:高濃度の機能性粒子を閉じ込めたペレット
マスターバッチとは、高濃度の顔料(色の素)や各種添加剤(機能を与える成分)を、熱可塑性樹脂(キャリア樹脂)中に均一に分散させたペレット状の着色剤・機能性付与剤のことです。イメージとしては、「色の素や機能の素がギュッと濃縮された粒」と考えてください。
これを、着色されていないナチュラル(無着色)の樹脂ペレットと一定の割合で混合し、そのまま射出成形機に投入することで、成形と同時に製品に着色したり、特定の機能を付与したりすることができます。
主な用途:着色だけじゃない、広がる可能性
マスターバッチの最も一般的な用途は、プラスチック製品の着色です。しかし、その用途は着色に留まりません。
⓵カラーマスターバッチ: 赤、青、黄といった基本色から、メタリック、パール、蛍光色など、多彩な色表現を可能にします。
② 機能性マスターバッチ:
– 難燃マスターバッチ: 製品に燃えにくさを付与します(家電製品、OA機器、建材など)。
– 帯電防止マスターバッチ: 静電気の発生を抑え、ホコリの付着防止や電子部品の保護に貢献します(電子部品トレイ、包装材など)。
– 紫外線吸収(UVカット)マスターバッチ: 紫外線による製品の劣化(変色、強度低下)を防ぎます(屋外使用製品、農業用フィルムなど)。
– 抗菌・防カビマスターバッチ: 細菌やカビの繁殖を抑制します(医療機器、食品容器、日用品など)。
– その他: 滑剤(成形性向上)、酸化防止剤(樹脂の熱劣化防止)、発泡剤、レーザーマーキング用など、様々な機能を持つマスターバッチが存在します。
設計者としては、単に「色を付ける」だけでなく、「どのような機能を付与したいか」という視点からもマスターバッチの活用を検討できることを覚えておきましょう。
マスターバッチの構成要素:品質を左右する3つの柱
マスターバッチの品質や性能は、主に以下の3つの要素によって決まります。設計者が材料選定する上で、これらの構成要素への理解は不可欠です。
顔料または染料:色の心臓部
製品に色を与える主要成分です。大きく分けて有機顔料、無機顔料、そして染料があります。
⓵ 有機顔料
鮮やかな色相が多く、着色力に優れる。透明性が高いものもある。
一般的に無機顔料に比べ耐熱性、耐候性、隠蔽力(下地を隠す力)が劣る傾向がある。
例:アゾ系顔料(黄、橙、赤)、フタロシアニン系顔料(青、緑)など。
② 無機顔料
耐熱性、耐候性、隠蔽力に優れる。比較的安価なものが多い。
有機顔料に比べ色相の鮮やかさや着色力で劣る場合がある。重金属を含むものもあるため、用途によっては注意が必要(例:RoHS指令など)。
例:酸化チタン(白)、カーボンブラック(黒)、酸化鉄(赤、黄、茶)など。
③ 染料
樹脂に溶解して透明な着色をする。鮮やかな色相が得られる。
耐熱性、耐候性、耐移行性(他の素材に色が移る現象)が顔料に比べて劣る場合が多い。
例:溶剤染料、分散染料など。
設計者は、製品に求められる色調だけでなく、使用環境(屋内/屋外、温度条件など)、耐薬品性、コスト、各種規制(食品衛生法、RoHS指令など)を考慮して、適切な顔料/染料が使用されたマスターバッチを選定する必要があります。
キャリア樹脂(担体):顔料を運び、製品と馴染む媒体
顔料や添加剤を保持し、成形時にベースとなる樹脂(ナチュラル材)と均一に混ざり合うための媒体となる樹脂です。キャリア樹脂の選定は、マスターバッチの品質と最終製品の物性に極めて重要な影響を与えます。原則として、最終製品に使用する樹脂(ベース樹脂)と同一、または非常に相溶性(混ざりやすさ)の良い樹脂が選ばれます。例えば、PP(ポリプロピレン)製品にはPPベースのキャリア、PE(ポリエチレン)製品にはPEベースのキャリアといった具合です。相性の悪いキャリア樹脂を使用すると、以下のような問題が発生する可能性があります。
– 分散不良: 顔料が均一に分散せず、色ムラ、スジ、ブツなどの外観不良。
– 物性低下: 製品の強度、靭性、耐衝撃性、耐熱性などが著しく低下。
– 成形不良: シルバーストリーク、ガス焼け、離型不良など。
特に設計者としては、マスターバッチのデータシートでキャリア樹脂の種類を確認し、使用するベース樹脂との適合性を必ず確認する必要があります。
分散剤・各種添加剤:縁の下の力持ち
顔料をキャリア樹脂中に均一かつ安定的に分散させるため、またマスターバッチ自体や最終製品に特定の機能を付与するために、様々な添加剤が使用されます。
⓵ 分散剤: 顔料粒子の表面に作用し、凝集(粒子同士が集まって塊になること)を防ぎ、濡れ性を向上させ、キャリア樹脂中への均一な分散を助けます。顔料の種類や濃度に応じて最適な分散剤が選ばれます。
② その他の添加剤:
– 滑剤: マスターバッチ製造時の加工性向上、成形時の流動性向上、離型性向上。
– 酸化防止剤: マスターバッチや最終製品の熱による酸化劣化を防止。
– 紫外線安定剤: 光による劣化を防止(キャリア樹脂や顔料の保護)。
これらの添加剤は、少量で大きな効果を発揮しますが、種類や量を誤ると最終製品の物性に悪影響を与える可能性もあるため、マスターバッチメーカーのノウハウが活かされる部分です。
なぜ今、マスターバッチ活用が重要なのか?:MOQ上昇時代を乗り切る設計者の選択肢
冒頭で触れた通り、近年、着色コンパウンドのMOQが上昇傾向にあります。この背景と、それに対してマスターバッチがいかに有効な解決策となり得るのかを掘り下げていきましょう。
材料メーカーのMOQ上昇、その背景にあるもの
材料メーカーがMOQを引き上げる背景には、いくつかの複合的な要因があります。
⓵ 原料価格の変動と高騰: 原油価格やナフサ価格の不安定化、特定の顔料や添加剤の需給逼迫による価格高騰は、少量生産の採算性を悪化させています。
② 生産効率の追求: メーカーとしては、一度の生産ロットが大きい方が生産計画を立てやすく、段取り替えの回数も減り、コスト効率が向上します。少量多品種の着色コンパウンド生産は、この効率化と逆行します。
③ 環境規制強化の影響: 特定の顔料や添加剤が環境規制(REACH規則など)や安全性への懸念から使用制限されたり、代替品が高価であったりすることで、少量生産のコストを押し上げています。
④ サプライチェーンの不安定化: 地政学的リスクやパンデミックなどにより、原料調達が不安定になり、少量多品種への対応余力が低下している側面もあります。
⑤ 人手不足と合理化: 製造業全体の人手不足や、メーカー内の合理化推進も、少量対応が難しい状況を生んでいます。
これらの要因が絡み合い、結果として着色コンパウンドのMOQが上昇し、設計者や購買担当者を悩ませているのです。
MOQ上昇が設計者にもたらす厳しい現実
着色コンパウンドのMOQ上昇は、射出成形部品の設計者にとって以下のような具体的な課題をもたらします。
⓵ 小ロット生産部品の調達難: ニッチな市場向けの製品や、ライフサイクルの短い製品、補給部品など、少量しか生産しない部品の着色材料を確保するのが難しくなります。
② 試作・開発段階でのハードル上昇: 新製品開発時、複数の色で試作して比較検討したい場合でも、色ごとにMOQを満たす量の材料を購入する必要があり、コストと時間の負担が増大します。色変更の柔軟性も失われます。
③ コスト増大と価格転嫁の圧力: 必要量以上の材料を購入せざるを得ないため、材料コストが無駄に増加します。これが製品価格に転嫁されれば、市場競争力に影響します。
④ 在庫管理の負担増: 色ごとに大量の着色コンパウンドを在庫として抱える必要が生じ、保管スペースの確保や品質管理(長期保管による劣化リスク)の負担が増します。
⑤ 代替材料探索の必要性とリスク: 希望の色や仕様のコンパウンドが入手困難な場合、代替材料を探す必要が出てきますが、物性や成形性が同等とは限らず、再評価の手間やリスクが伴います。
マスターバッチが切り拓く、MOQ問題解決への道
このような厳しい状況下で、マスターバッチの活用は設計者にとって非常に有効な選択肢となります。
⓵ 圧倒的な小ロット対応力
マスターバッチの最大の利点は、ナチュラル材(無着色樹脂)と混合して使用するため、着色コンパウンドに比べて格段に小ロットでの着色が可能になる点です。ナチュラル材は汎用品として比較的入手しやすく、マスターバッチ自体もコンパウンドよりはMOQが小さいか、小分け対応してくれるサプライヤーも存在します。数キログラム単位での着色も現実的になり、試作や極小ロット生産への対応力が飛躍的に向上します。
② 在庫管理の劇的な効率化
従来、赤・青・黄と3色の部品を生産する場合、3種類の着色コンパウンドを在庫する必要がありました。しかしマスターバッチなら、1種類のナチュラル材と、赤・青・黄の3種類のマスターバッチを在庫すれば済みます。 これにより、在庫スペースの削減、在庫金額の圧縮、管理工数の削減が期待できます。さらに、急な色変更の要求にも、マスターバッチの変更だけで対応できるため、柔軟性が格段に高まります。
③ コスト削減の可能性
一般的に、着色コンパウンドは材料メーカーが調色・コンパウンド化する工程が入るため、ナチュラル材+マスターバッチの組み合わせよりも単価が高くなる傾向があります。MOQの問題で不必要な量のコンパウンドを購入するコストと比較すれば、トータルコストでマスターバッチの方が有利になるケースが多くあります。 また、輸送コストや保管コストの削減も期待できます。
④ 開発リードタイムの短縮:
試作品の色検討や顧客への色提案の際、マスターバッチなら比較的容易に色を変更し、少量の試作成形が可能です。これにより、開発サイクルを迅速化し、市場投入までの時間を短縮できます。
⑤ 環境負荷低減への貢献:
必要な時に必要な量だけを着色するため、着色済み材料のデッドストック(長期滞留在庫)や廃棄ロスを削減できます。 これは、サステナビリティが重視される現代において、企業価値を高める上でも重要な要素です。
このように、マスターバッチはMOQ上昇という課題を乗り越え、設計の自由度を高め、コスト効率を改善するための強力なツールとなり得るのです。
設計者がマスターバッチを選定・活用する際の重要ポイント
マスターバッチのメリットを最大限に引き出すためには、適切な選定と活用が不可欠です。設計者が特に注意すべきポイントを解説します。
最重要!樹脂との相溶性(キャリア樹脂の選定)
前述の通り、キャリア樹脂とベース樹脂(成形するナチュラル材)の相溶性は、製品の品質を左右する最も重要な要素です。
⓵ 確認事項
– マスターバッチのデータシートでキャリア樹脂の種類を必ず確認する。
– ベース樹脂と同一のキャリア樹脂が理想的。
– 異なる場合は、相溶性の高い組み合わせであるか(例: PEベースのMBをPPに使用するなど、限定的なケースもあるが注意が必要)。
– 不明な場合は、マスターバッチメーカーに必ず問い合わせる。
② 相性不良時のリスク
– 外観不良: 色ムラ、スジ(ストリーク)、ブツ(凝集物)、ウェルドラインの悪化、光沢ムラなど。
– 物性低下: 衝撃強度、引張強度、曲げ強度、耐熱性などの著しい低下。製品が脆くなる(脆化)。
– 成形不良: ガス焼け、ショートショット、シルバーストリーク、離型不良、スクリューへの付着など。
特に、複数の樹脂に対応できるとされる「ユニバーサルマスターバッチ」を使用する場合は注意が必要です。汎用性を高めるために、特定の樹脂との相溶性が最適化されていない場合があり、物性への影響が出や
すくなる傾向があります。使用前に必ず十分な評価を行ってください。
用途と要求性能に応じた顔料・添加剤の選定
製品が使用される環境や、求められる機能、法規制などを考慮して、最適な顔料や添加剤が使用されたマスターバッチを選定します。
⓵ 色に関する要求
– 色調・色差: ターゲット色との色差(ΔE)の許容範囲。
– 隠蔽性: 下地の色を隠す必要があるか(透明性を求めるか)。
– 耐候性・耐光性: 屋外使用か屋内使用か。紫外線や可視光による変色・退色の許容度。
– 耐熱性: 成形温度、製品使用時の最高温度に耐えられるか。顔料が熱分解しないか。
– 耐薬品性: 特定の薬品(洗剤、油、溶剤など)に接触する可能性があるか。
– 耐移行性(ブリード性): 顔料や染料が他の素材に色移りしないか。
② 機能性に関する要求
– 難燃グレード(UL94規格など)、帯電防止性能(表面抵抗値など)、抗菌効果のレベル。
– 機能の持続性(長期間効果が続くか)。
③ 法規制・安全性
– 食品衛生法(ポジティブリスト制度など): 食品に接触する用途か。
– RoHS指令、REACH規則(SVHC): 有害物質規制に対応しているか。
– 玩具安全基準(ST基準など): 玩具に使用するか。
– その他、業界特有の規制(医療機器、自動車部品など)。
これらの要求事項を明確にし、マスターバッチメーカーに伝えることで、適切な製品選定やカスタム対応の相談がスムーズに進みます。
適正な添加量と均一な混合:品質の鍵
マスターバッチは、通常、ベース樹脂に対して1~5%程度(製品により異なる)の比率で添加されます。この添加比率(希釈倍率)は非常に重要です。
⓵ 添加量
– 推奨添加量の遵守: マスターバッチメーカーが推奨する添加量を守ることが基本です。
– 過少添加: 色が薄い、色ムラ、期待した機能が得られない。
– 過剰添加: コスト増、物性低下(キャリア樹脂の比率が増えすぎるため)、成形不良(顔料の凝集、ガスの発生など)、色の飽和(濃くなりすぎる)。
② 均一混合
– マスターバッチとナチュラル材を均一に混合することが、色ムラや性能バラつきを防ぐために不可欠です。
③ 混合方法
– 手動混合: 少量の試作などで行われるが、混合ムラが出やすい。
– タンブラーミキサー、リボンブレンダー: ペレット同士を機械的に撹拌。比較的簡便で効果的。
– 計量混合機(ドライブレンダー): 成形機に直結し、設定した比率で自動的に計量・混合しながら供給。最も精度が高いが設備投資が必要。成形機のスクリューデザインや成形条件(背圧、スクリュー回転数など)も分散性に影響します。
まとめ:マスターバッチを味方につけ、設計の未来を切り拓く
材料着色のMOQ上昇という逆風は、射出成形部品の設計者にとって大きな課題です。しかし、本コラムで解説してきたように、マスターバッチは、この課題を乗り越え、むしろ設計の自由度、生産の柔軟性、コスト効率を高めるための強力な武器となり得ます。
重要なのは、マスターバッチの特性を正しく理解し、製品の要求仕様(色、機能、品質、コスト)と照らし合わせて、最適な製品を選定し、適切に活用することです。キャリア樹脂とベース樹脂の相性、顔料・添加剤の種類、添加量、混合方法、そして信頼できるサプライヤーとの連携。これらのポイントを押さえることで、マスターバッチのメリットを最大限に引き出すことができるでしょう。
今後、マスターバッチ技術はさらに進化し、より高機能なもの(例えば、自己修復機能、センサー機能を持つスマートマテリアルなど)、より環境に配慮したもの(バイオマスプラスチックキャリア、リサイクル材対応など)が登場してくることも期待されます。
射出成形部品の設計者の皆様には、ぜひこのマスターバッチという選択肢を積極的に検討し、設計段階からその活用を視野に入れることで、変化の激しい市場においても競争力のある製品開発を実現していただきたいと思います。本コラムが、その一助となれば幸いです。