ガラス繊維強化グレードの外観不良を諦めない!まだある 改善のアプローチ
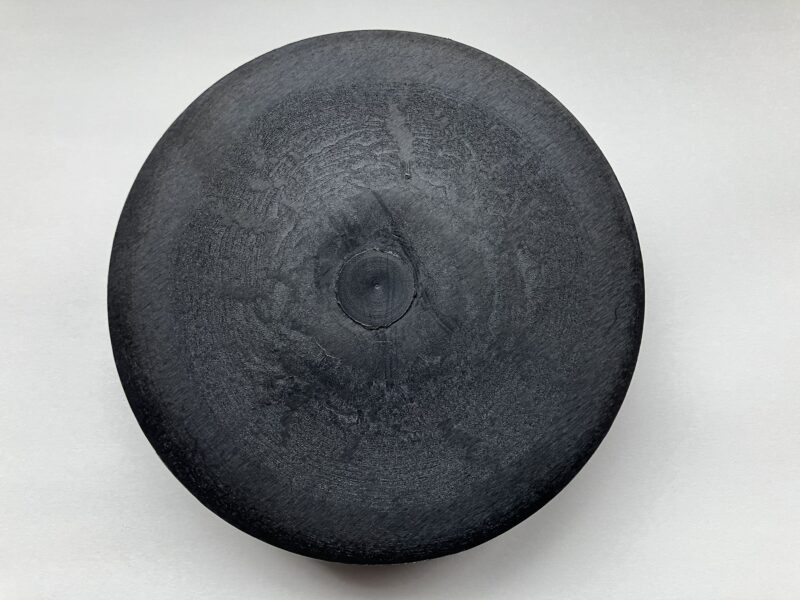
エンプラは産業機器、機械、家電など多様な分野で利用されており、その中でもガラス繊維強化グレードは、機械的強度や耐熱性、寸法安定性の向上を目的に幅広く採用されています。しかし、ガラス繊維強化グレードはその優れた機能性の反面、外観面での課題を抱えることが多く、特に意匠部品や外観品質が重視される用途では、ガラス繊維の露出やフローマーク、ウェルドラインなどの外観不良が問題となることが少なくありません。これらの外観不良は製品の付加価値を損なうだけでなく、歩留まりの低下や追加処理コストの増加といった生産現場の負担にも直結します。
本コラムでは、ガラス繊維強化グレードの外観不良の主な内容とその原因を整理し、現場で実践可能な外観改善のアプローチを紹介します。当社が蓄積してきたノウハウをもとに、成形条件の最適化や材料選定、さらには塗装などの後処理まで、幅広い観点から「まだある」改善策を提案し、各材料の特徴や短所も踏まえて実用的な知見をお届けします。外観性でお困りの際は、ぜひ当社までご相談ください。
外観不良の主な内容とその原因
ガラス繊維強化グレードを用いた成形品の外観不良には、いくつか代表的なパターンがあります。まず、最も多く見られるのが「ガラス繊維の露出・浮き」です。これは、成形品の表面にガラス繊維が現れ、白っぽくざらついた感触となる現象です。主な原因は、樹脂の流動性不足や成形条件の不適切さ、金型設計の問題などが挙げられます。特に流動末端やウェルド部、肉厚変化部で発生しやすく、樹脂が十分に繊維を包み込めない場合に顕著です。
次に、「フローマーク」や「ウェルドライン」も外観不良の代表例です。フローマークは樹脂の流れが不均一になることで表面に筋状の模様が現れる現象で、ウェルドラインは樹脂流が合流する部分で発生します。これらはガラス繊維の配向や樹脂の流動状態が大きく影響し、射出速度やゲート位置、金型温度などの成形条件が原因となることが多いです。
また、「色ムラ」や「光沢ムラ」も頻繁に見られる不良です。これは樹脂の温度ムラや混練不足、顔料分散の不良、さらにはガラス繊維の分散状態が影響します。特に薄肉部や複雑形状部では、樹脂の流動が不均一になりやすく、色や光沢のムラが目立ちやすくなります。
その他にも、「シルバー」「ブリスター」「焼け」「ボイド」「黒点」など、ガラス繊維強化グレード特有の外観不良があります。これらは原材料の品質や成形時の水分管理、金型のガス抜き、保管環境など、複数の要因が絡み合って発生します。外観不良の内容を正確に把握し、原因を多角的に分析することが、適切な対策の第一歩となります。
外観改善のアプローチ
ガラス繊維強化グレードの外観を改善するためには、単一の対策だけでなく、複数のアプローチを組み合わせて取り組むことが不可欠です。当社では、長年の経験と技術蓄積を活かし、4つの主要アプローチで外観改善に取り組んできました。ここでは、それぞれのアプローチについて解説します。外観性でお困りの際は、ぜひ当社のノウハウをご活用ください。
成形条件の最適化
最も基本的で効果的なアプローチが、成形条件の最適化です。樹脂温度や金型温度の設定は、ガラス繊維の表面露出やフローマークの発生に大きく影響します。樹脂温度が低すぎると流動性が悪化し、繊維が表面に現れやすくなりますが、高すぎると分解や焼けのリスクが高まります。金型温度も同様で、低すぎると表面が急冷されて繊維が浮きやすくなり、高すぎるとサイクルタイムが長くなるなどの課題が生じます。
射出速度や圧力の調整も重要です。射出速度が速すぎると樹脂の流動が乱れてフローマークやウェルドラインが目立ちやすくなりますが、遅すぎると充填不足や繊維の配向不良が生じます。保圧や冷却時間の管理も外観に直結する要素で、保圧不足はボイドやヒケ、繊維の浮きにつながりますし、冷却時間が短すぎると離型時に表面が損傷しやすくなります。
また、金型設計の見直しも有効です。ゲート位置やランナー設計、ベント位置などは樹脂の流れやガス抜けに影響し、外観性に大きな差を生みます。当社では、実験計画法や成形シミュレーションを駆使し、最適条件を効率的に導出するノウハウを蓄積しています。成形条件の最適化は、現場で最も取り組みやすく、かつ効果が高いアプローチですので、まずはご相談いただくことをおすすめします。
外観性に優れる樹脂材の採用
成形条件の最適化だけでは限界がある場合、材料自体の選定を見直すことも有効です。外観性に優れるエンプラとして、MXD6、半芳香族PA(ポリアミド)、非晶性PAなどが挙げられます。MXD6は高い機械強度と剛性、優れたガスバリア性、低吸水性を備えており、成形品の表面性状も良好です。ただし、結晶化速度が遅いため成形条件に注意が必要で、結晶化が不十分だと外観不良や物性低下が生じやすいという課題があります。また、標準グレードでは難燃性がやや低いため、用途によっては難燃剤の添加が必要となります。
半芳香族PAは高耐熱性と高剛性、耐薬品性、吸水による寸法変化の少なさが特徴です。外観性に優れるグレードも存在し、意匠部品への適用事例が増えていますが、成形温度が高く加工が難しい場合や、樹脂自体が高価である点、結晶化度が低いと物性や外観が十分に発揮できない点には注意が必要です。
非晶性PAは透明性や高い外観性、寸法安定性、塗装や接着性の良さが際立っています。成形ひずみが少なく、精密外観部品に適していますが、耐摩耗性や耐熱性は結晶性PAより劣り、高温下での強度低下や耐薬品性の劣化が見られます。
当社では、これらの材料特性を活かした最適な材料選定をサポートしています。部品の要求特性やコスト、加工性など、さまざまな観点からご提案が可能です。
高外観グレードの採用
近年では、ガラス繊維強化グレードの中でも「高外観グレード」と呼ばれる、外観性に特化した材料も登場しています。代表的なものとして、PPS(ポリフェニレンサルファイド)や半芳香族PAの高外観グレードが挙げられます。PPSは高耐熱性や耐薬品性、寸法安定性、難燃性、低吸水性といった優れた特性を持ち、過酷な環境下でも安定した性能を発揮しますが、衝撃強度や靭性がやや低く、特に低温では脆くなる傾向があります。また、塗装や着色が難しいという課題や、成形温度が高くコストも高めであることも考慮が必要です。
半芳香族PAの高外観グレードは、外観性・耐熱性・寸法安定性を高次元で両立しており、意匠部品への適用が進んでいます。一部グレードは塗装性や接着性にも優れていますが、価格が高めで、成形条件がシビアな場合もあるため、導入には十分な検討が必要です。
当社では、これら高外観グレードの特徴を活かした材料選定や成形条件の最適化に関して、多くの実績とノウハウを持っています。用途やご要望に応じて、最適なソリューションをご提案いたします。
塗装による外観改善
材料や成形条件だけでは外観不良を完全に解消できない場合、塗装などの後処理による改善も選択肢となります。塗装は、表面の色ムラや繊維露出を隠蔽できるだけでなく、多彩な色や質感を付与することで製品の付加価値を高める効果もあります。しかしながら、塗装工程の追加によるコスト増加や、塗装密着性・耐久性の確保といった新たな課題も生じます。特にPPSのように塗装が困難な材料も存在し、材料と塗料の相性や前処理方法、最終用途での耐久性などを十分に評価することが不可欠です。当社では、塗装を含む外観改善の総合的なご提案も行っておりますので、ご要望があればお気軽にご相談ください。
材料選定の考え方
ガラス繊維強化グレードの材料選定においては、部品ごとの要求特性を明確にし、各材料の特徴を踏まえて最適なものを選ぶことが重要です。まず、機械的強度や耐熱性、外観性、寸法安定性、耐薬品性、塗装・接着性、コストなど、部品に求められる性能を整理します。次に、それぞれの材料が持つ特徴や短所を比較し、最適な候補を絞り込みます。
たとえば、外観性と寸法安定性が特に重視される場合は、非晶性PAや高外観グレードの半芳香族PAが有力な選択肢となります。一方、耐熱性や耐薬品性が最優先される用途では、PPSや半芳香族PAが適しています。MXD6は、耐熱性、機械的強度、外観性のバランスが求められる場合に有効です。
材料選定の際には、成形条件や後処理の可否も重要な判断基準となります。サンプル評価や実機試作を通じて、実際の成形品での外観や物性を確認し、最適な材料を決定することが推奨されます。当社では、こうした材料選定や評価プロセスもトータルでサポートしています。
まとめ
ガラス繊維強化グレードは、機械的特性や耐熱性に優れる一方、外観性の課題がつきものです。ガラス繊維の露出やフローマーク、ウェルドライン、色ムラなどの外観不良は、製品の価値や生産効率に大きく影響します。こうした外観不良の改善には、成形条件の最適化、外観性に優れるエンプラや高外観グレードの選定、塗装などの後処理といった多様なアプローチが必要です。
しかし、最適な材料やグレードの選定は、部品の使用条件や環境、形状、金型構造、さらには生産現場の制約まで、多くの要素が関わるため、最適解を導き出すのは容易なことではありません。同じ材料でも、成形条件や金型設計、部品設計によって外観や物性は大きく変わります。こうした複雑な課題には、現場での経験や専門的なノウハウが不可欠です。
当社は、長年にわたりガラス繊維強化グレードの外観改善に取り組み、多くの現場で課題解決を実現してきました。材料に関しての深い知見と、成形現場のリアルな課題に基づく提案力を活かし、部品設計から材料・グレード選定、成形条件の最適化、金型設計のアドバイスまで、トータルでサポートいたします。外観性でお困りの際は、ぜひ当社のノウハウをご活用ください。お客様の現場に最適な解決策を、一緒に見つけてまいります。