成形条件が割れ(クラック)を呼ぶ? 残留応力・ウェルドライン・冷却不良が引き金になる理由
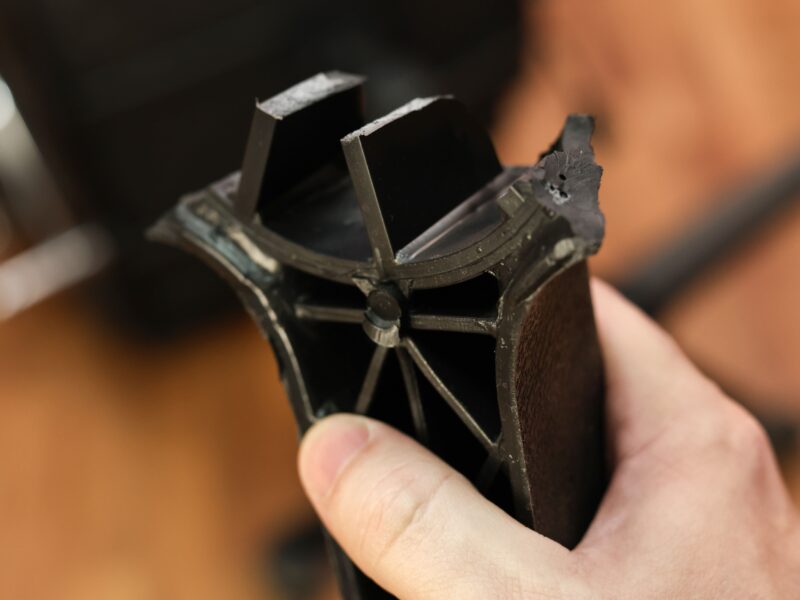
「完璧な材料を選び、応力集中を避けた形状設計も行った。それなのに、なぜか製品が割れてしまう…」
設計現場でこのような壁に突き当たった経験はないでしょうか。その原因は、目に見えない「成形プロセス」に潜んでいるかもしれません。射出成形は、溶融した樹脂を金型に流し込み、冷やし固めるという、一見シンプルなプロセスです。しかしその裏側では、圧力、温度、速度といった様々なパラメータが複雑に絡み合い、最終製品の品質、特に「割れにくさ(靭性)」に絶大な影響を与えています。
どんなに優れた設計図も、それを忠実に再現する成形技術が伴わなければ意味がありません。今回のコラムでは、設計者が見落としがちな「成形条件」に起因するクラックに焦点を当てます。特に、破壊の三大引き金となる「残留応力」、「ウェルドライン」、「冷却不良」が、なぜ、どのようにして製品を脆くするのか、そのメカニズムを解説します。当社では、長年の経験を通じてこうした成形条件設定のノウハウを深く蓄積しており、材料と設計のポテンシャルを最大限に引き出す量産体制を構築しています。成形現場で何が起きているのかを理解することは、より良い設計へのフィードバックとなり、トラブルを未然に防ぐ力となります。
目に見えない破壊の元凶「残留応力」の正体
残留応力とは、外部から力がかかっていないにもかかわらず、成形品内部に残り続ける応力のことです。これは成形品にとって「内部的な負荷」であり、この値が高いほど、外部からのわずかな力で破壊に至りやすくなります。残留応力は、主に以下の2つのメカニズムで発生します。
分子配向による応力
溶融樹脂が金型の細いゲートや薄肉部を高速で通過する際、糸状のポリマー分子は流れの方向に引き伸ばされ、整列します。これを「分子配向」と呼びます。この配向した状態のまま樹脂が冷え固まると、分子は元のランダムな状態に戻ろうとする力を内部に溜め込みます。これが分子配向による残留応力です。特にゲート周辺は強い配向が起こりやすく、残留応力が集中する傾向があります。
不均一な冷却による応力
成形品は、金型に接触している表面から冷え固まっていきます。一方、肉厚な部分の内部は、ゆっくりと冷えていきます。プラスチックは冷却時に収縮するため、先に固まった表面層と、後から収縮しようとする内部層との間で「引っ張り合い」が生じます。これにより、製品表面には圧縮応力が、内部には引張応力が残留します。特に、クラックの起点となりやすいのは内部の引張応力です。
これらの残留応力は、製品の強度を初期状態から低下させている「見えない負債」のようなものです。外部からの荷重が加わると、この負債に上乗せされる形で応力が作用するため、本来の材料強度を発揮する前に破壊に至ってしまうのです。
成形条件が「残留応力」を生み出すメカニズム
では、具体的にどのような成形条件が残留応力を増大させてしまうのでしょうか。特に重要な「保圧」と「冷却」のバランスに注目してみましょう。
NG条件①:過剰な保圧と低すぎる樹脂温度
「保圧」とは、金型に充填された樹脂が冷却収縮するのを補うため、追加で圧力をかける工程です。ヒケを防ぐために重要な工程ですが、この圧力が過剰になると、分子を無理やり金型に詰め込むことになり、極めて高い分子配向と残留応力を生み出します。
特に、樹脂温度が低い状態で高い保圧をかけると最悪です。粘度が高い状態で無理に流されるため、分子は強く引き伸ばされ、緩和する間もなく固化してしまいます。結果として、ゲート周辺は硬く、一見すると良品に見えますが、内部には「割れの時限爆弾」とも言える高い残留応力を抱え込んでいます。
どう見抜くか?
– ゲート付近にクラックが集中している。
– 偏光板(歪み検査器)で観察すると、ゲート周りに虹色の干渉縞が密に、そして強く現れる。
– 製品をアニール処理(加熱して応力を緩和させる処理)すると、ゲート付近が大きく変形する。
対策の方向性
保圧はヒケが出ない必要最低限に設定し、樹脂温度を適切に高めることで流動性を確保し、無理な圧力で分子を配向させないことが基本です。
NG条件②:金型温度の低すぎと冷却時間の短すぎ
生産サイクルを上げるために、金型温度を低く設定し、冷却時間を短縮するのはよくあるケースです。しかし、これは製品の表面だけを急激に冷やし、内部はまだ高温でドロドロという状態を生み出します。この極端な冷却ムラは、前述の「不均一な冷却による応力」を最大化させる原因となります。
表面だけが固まった製品は、金型から突き出された後も内部の冷却収縮が続きます。これにより、製品全体が反ったり、内部に大きな引張応力が残留したりします。また、金型表面の転写性も悪化し、微細な傷が付きやすく、これが破壊の起点となることもあります。
どう見抜くか?
– 製品全体の反りや変形が大きい。
– 特に厚肉部のヒケや内部ボイド(空洞)が目立つ。
– 切断して断面を見ると、表面と内部で光沢や質感が異なる(スキンコア構造が極端になっている)。
対策の方向性
適切な金型温度(材料メーカー推奨値)を維持し、製品内部まで十分に固化する冷却時間を確保することが重要です。これにより、製品全体の収縮が均一に近づき、残留応力は大幅に低減されます。
アキレス腱となる「ウェルドライン」の強度低下
ウェルドラインとは、金型内で複数の溶融樹脂の流れが合流する箇所にできる、細い線のことです。例えば、穴のある部品では、樹脂は穴を避けて流れ、その裏側で再び合流します。この合流部では、樹脂の先端部分が冷えかけていたり、分子の絡み合いが不十分だったりするため、物理的に一体化しておらず、構造的な弱点となります。
ウェルドラインの強度は、樹脂が合流する際の「温度」と「圧力」に大きく依存します。
NG条件③:樹脂温度・金型温度が低く、射出速度が遅い
樹脂温度や金型温度が低いと、樹脂は金型内を流れる間にどんどん冷えて粘度が高まります。さらに射出速度が遅いと、樹脂の先端が合流する頃にはすっかり冷え固まりかけてしまいます。これでは、異なる流れ同士が十分に溶け合って一体化することはできず、ただ接触しているだけの状態に近くなります。このようなウェルドラインは、わずかな力で簡単に剥離し、クラックの起点となります。
どう見抜くか?
– ウェルドラインが、くっきりとシャープな線として目視できる。
– ウェルドライン部分を曲げると、ほとんど抵抗なくパキッと割れる。
– 破壊部品を観察すると、明らかにウェルドラインを起点にクラックが始まっている。
対策の方向性
ウェルドラインの強度を高めるには、「樹脂が合流する瞬間に、できるだけ高温・高圧であること」が鍵です。具体的には、樹脂温度や金型温度を適切に上げ、射出速度を速くすることで、樹脂の先端が冷える前に合流させ、互いに融着させる必要があります。また、設計段階でゲート位置を工夫し、ウェルドラインが製品の重要箇所や応力集中部に来ないようにすることも極めて重要です。
ゲート設計が招く破壊のリスク
ゲートは樹脂の入り口であり、成形品質を左右する非常に重要な要素です。ゲートの種類や位置が不適切だと、前述の残留応力やウェルドラインの問題を助長します。
NG条件④:ゲート位置の不適切さ
例えば、長方形の板の中心に1点ゲートを設けると、樹脂は放射状に広がり、両端で合流してウェルドラインが2本発生します。もしこの板が曲げ荷重を受ける場合、最も応力のかかる両端に最弱点であるウェルドラインが存在することになり、非常に割れやすくなります。
また、ゲートが製品の薄肉部に設けられていると、そこを通過する際に樹脂は強いせん断を受けて分子配向が強くなり、ゲート周辺に高い残留応力が集中します。
どう見抜くか?
– 破壊の起点が、常にウェルドラインやゲート付近である。
– CAEの流動解析結果を見ると、ウェルドラインの位置や圧力損失、分子配向の強さが予測できる。
対策の方向性
設計の初期段階で、製品にかかる荷重の方向や大きさを考慮し、「ウェルドラインが応力の低い場所にできる」「ゲートが応力集中部にこない」ようなゲート位置を検討することが不可欠です。これは設計者と成形技術者が協力して決めるべき最重要項目の一つです。
まとめ:設計と成形は車の両輪
これまで見てきたように、成形品が割れる原因は、設計図の中だけに存在するわけではありません。
– 過剰な保圧は、ゲート周辺に「残留応力」という爆弾を仕込む。
– 不適切な冷却は、製品全体に「ひずみ」をもたらし、脆化させる。
– 低い成形温度は、「ウェルドライン」をただの傷跡に変えてしまう。
これらの問題は、一見すると成形現場の課題のように思えます。しかし、その根本には、設計段階での配慮不足が隠れていることも少なくありません。例えば、極端な偏肉設計は、どんなに成形条件を工夫しても残留応力の発生を避けられません。また、ゲート位置の自由度を奪うような設計は、ウェルドライン対策を困難にします。
「割れない製品」を作るためには、設計と成形が車の両輪となって連携することが不可欠です。設計者は、自分の設計が成形プロセスでどのような現象を引き起こすかを想像し、成形しやすい形状を心がける必要があります。そして、もし成形起因と思われるトラブルに直面した際は、成形現場の担当者と協力し、今回解説したようなポイント(保圧、温度、ウェルドラインの状態など)を確認しながら原因を特定していく姿勢が求められます。
当社は、まさにこの「設計」と「成形」の両輪を高いレベルで回すことを得意としています。数々の材料と複雑な形状を扱ってきた経験から、残留応力やウェルド強度を最適化するための成形条件設定ノウハウを豊富に蓄積しています。お客様の設計思想を深く理解し、それを最高の品質で形にする。ぜひ、そのプロセスを安心してお任せください。 成形プロセスへの理解を深めることは、設計者自身のスキルアップに繋がり、より本質的な品質改善を実現するための強力な武器となるのです。