入れ子設計で差がつく射出成形:量産コストと品質を左右する金型の基本構造とは
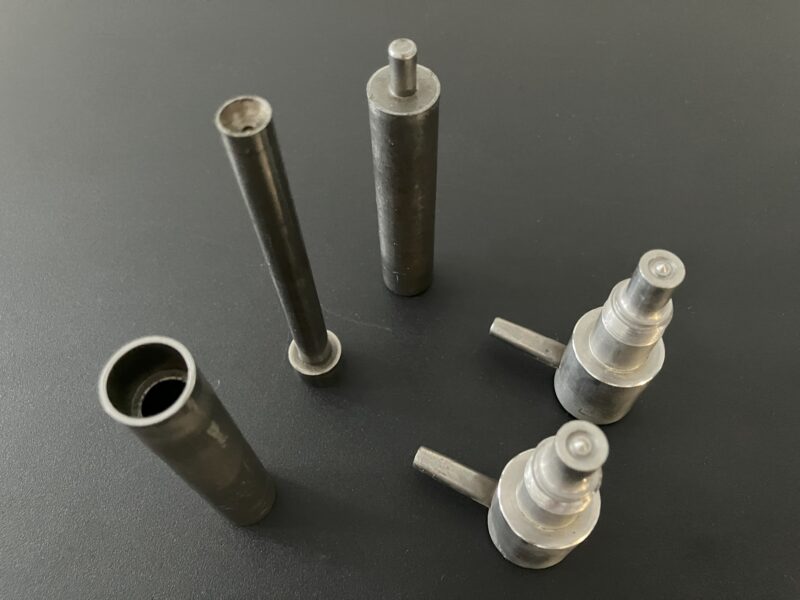
射出成形において、製品品質やコスト競争力は、製品設計だけでなく「金型設計」の巧拙に大きく左右されます。中でも、金型の一部を別部品化する「入れ子」の設計は、製品形状の自由度、メンテナンス性、さらには金型の耐久性やランニングコストに直結する重要な要素です。この「見えにくい部分」をどう最適化するかが、量産の成否を分けます。
本コラムでは、入れ子の基本的な役割から設計の考え方、コストや品質に与える影響までを実務的な視点で解説します。また、当社が実践するイエプコ処理による入れ子メンテナンスの効果についても触れ、トータルな金型最適化の重要性をお伝えします。
入れ子とは ― 金型設計に欠かせない構造要素
金型設計を語る上で、まず理解しておくべき基本構造が「入れ子」です。これは単なる部品ではなく、金型の性能を最大限に引き出すための戦略的な要素です。
入れ子の基本構造と役割
入れ子とは、金型のコア(製品の内側を形作る部分)やキャビティ(製品の外側を形作る部分)の特定箇所を、別部品として製作し、はめ込む構造のことです。本体となる金型(母型)に、機能的な部品を「入れて」使うことから「入れ子」と呼ばれます。
この構造がもたらす主な役割は、大きく分けて2つあります。
一つ目は、「複雑形状の実現」です。
金型は巨大な金属の塊から切削加工によって作られますが、一体構造のままでは加工工具が届かない深い溝や側面の穴、アンダーカット形状などを彫り込むことは困難です。そこで、形状が複雑な部分を別パーツ(入れ子)として製作し、後から母型に組み込むことで、一体加工では不可能な形状でも精密に再現できます。また、成形時に発生するガスを効率的に抜くための「ガスベント」を入れ子の合わせ目に設けるなど、成形品質を向上させる目的でも活用されます。
二つ目は、「メンテナンス性の向上」です。
射出成形は、高温高圧の樹脂を繰り返し金型に流し込む過酷なプロセスです。特に、樹脂が最初に当たるゲート部や、製品を突き出すエジェクタピンの周辺、摺動するスライドコアなどは、数万、数十万ショットというサイクルの中で必ず摩耗や疲労が蓄積します。もし金型が一体構造であれば、一部分の摩耗や破損でも金型全体の大規模な修理が必要となり、莫大なコストと長い生産停止期間が発生します。
しかし、あらかじめ摩耗しやすい部分や破損リスクの高い部分を入れ子化しておけば、問題発生時にその部品だけを交換するだけで済みます。これにより、修理コストを大幅に抑制し、ダウンタイムを最小限に抑え、金型全体の寿命を飛躍的に延ばすことができるのです。
入れ子が使われる代表的な製品・用途例
入れ子の効果は、様々な製品や用途で発揮されています。以下に代表的な例を挙げます。
ネジ穴・細穴・複雑な凹形状
コネクタのハウジングや精密機器の筐体などに見られる、側面のネジ穴や微細な穴は、入れ子構造の典型的な活用例です。入れ子を用いることで、これらの加工困難な形状を精密かつ安定して成形できます。
意匠面の細かなロゴ・文字
製品表面のブランドロゴや文字なども、多くは入れ子によって作られています。意匠はモデルチェンジで変わることが多いため、ロゴ部分を入れ子にしておけば、入れ子だけを交換するだけで迅速にバリエーション展開が可能です。
高耐久性・高精度が求められる摺動部品や機構部品
ギアやカムなど、他の部品と接触しながら動く摺動部品では、耐摩耗性が品質を左右します。こうした部品の金型では、摺動部や摩耗が激しい箇所に、母材よりも硬度や潤滑性に優れた特殊な鋼材を入れ子として使用します。これにより、必要な部分だけを高性能化し、製品の耐久性と寸法安定性を長期間維持できます。
入れ子設計が量産コストに与える影響
入れ子設計は、技術的な選択肢であるだけでなく、製品のライフサイクル全体を見据えた「コスト戦略」そのものです。初期投資とランニングコストのバランスをどう取るかが、企業の利益を大きく左右します。
金型製作費と入れ子コストの考え方
一般的に、入れ子構造を採用すると、金型の初期費用は高くなる傾向にあります。母型とは別に部品を製作し、それらを精密に嵌め合わせるための追加工数が発生するためです。
しかし、重要なのは「メンテナンスや修理にかかる費用とのトレードオフ」で考えることです。
例えば、1,000万円の一体構造の金型と、入れ子化によって1,100万円になった金型があるとします。量産中に摩耗による不具合が発生した場合、前者は金型全体の大規模な修理が必要となり、数百万円の修理費と数週間の生産停止を招くかもしれません。一方、後者は数万円の予備入れ子に交換するだけで、数時間のうちに生産を再開できる可能性があります。
少量生産であればシンプルな一体構造が合理的かもしれませんが、数十万ショット以上の大量生産を計画している場合、入れ子化による初期投資は、将来の損失を防ぐための「保険」として、極めて有効な投資となるのです。
入れ子交換が容易な設計の重要性
入れ子化のメリットを最大限に享受するためには、「交換が容易であること」が絶対条件です。トラブル発生時に、金型を成形機から降ろし、完全に分解しなければ入れ子が交換できないようでは、ダウンタイムの短縮効果は半減してしまいます。
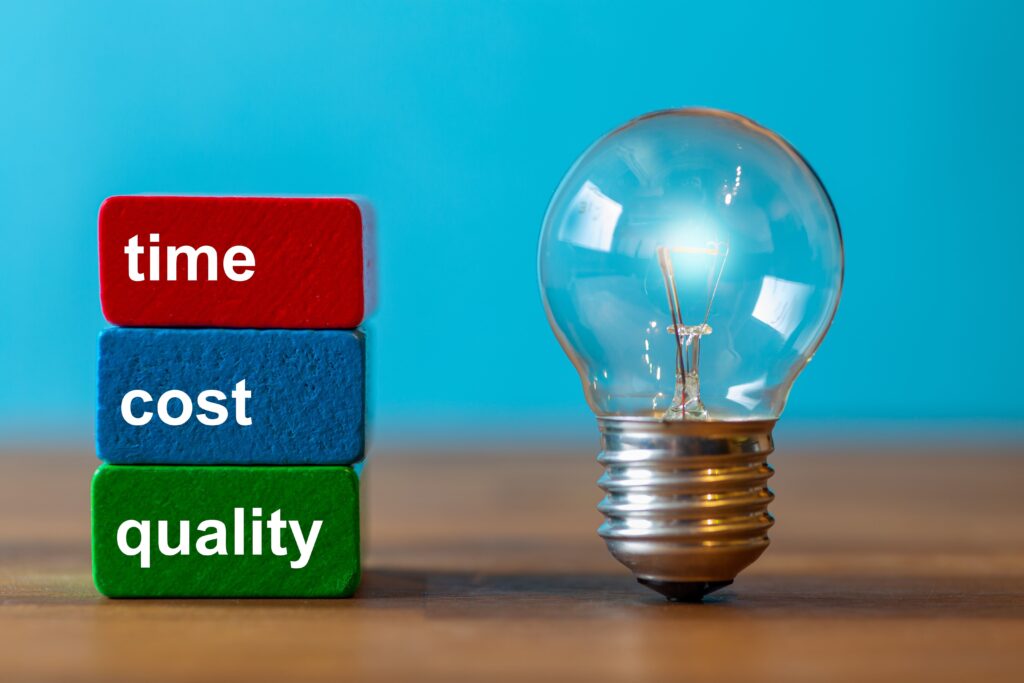
理想的なのは、金型を成形機に搭載したまま、あるいは最小限の分解で、迅速に入れ子を交換できる設計です。これにより、トラブル発生から生産再開までの時間を劇的に短縮できます。特に、24時間稼働の量産ラインや多品種生産の現場において、このダウンタイムの差は企業のコスト競争力に直接的な影響を与えます。摩耗が予測されるゲートブッシュや、折損しやすい細いコアピンなどを、金型の外部から簡単にアクセスできる構造にする配慮が求められます。
長期的な視点でのコスト最適化
金型は消耗品ですが、入れ子設計を戦略的に活用することで、その寿命を最大限に延ばすことが可能です。金型全体の寿命は、最も弱い部分の寿命によって決まります。入れ子化とは、いわば「金型のウィークポイントを交換可能な部品に置き換える」行為です。
摩耗しやすい部分、破損しやすい部分を計画的に入れ子化し、定期的に交換していくことで、金型本体である母型は健全な状態を保ち続けることができます。これにより、一つの金型で生産できる製品の総数(トータルショット数)を大幅に増やし、結果として製品一個あたりの金型償却費を低減できます。
製品の生産数量やライフサイクルを予測し、「どの部分を、どのタイミングで交換できるように入れ子化しておくか」という戦略を立てること。これこそが、長期的な視点でのコスト最適化なのです。
入れ子設計と製品品質の関係
入れ子はコストだけでなく、製品の寸法精度や外観品質、成形の安定性といった「品質」にも深く関わっています。適切な入れ子設計は、高品質な製品を安定して生み出すための土台となります。
寸法精度・外観品質に与える影響
入れ子は別部品を組み合わせる構造であるため、その「合わせ目の精度」が品質を大きく左右します。入れ子と母型との間にわずかでも隙間があれば、そこに樹脂が流れ込んで「バリ」が発生し、外観や組み立て性を損ないます。また、合わせ面の精度が低いと、成形圧力で入れ子が動き、製品の寸法がばらつく原因にもなります。
さらに、製品の顔となる意匠面に入れ子を用いる場合、その材質や表面仕上げの選定が重要です。光沢が求められるなら鏡面仕上げ、マットな質感を出すならシボ加工やブラスト処理など、目的に応じた適切な仕上げを施すことで、製品の付加価値を高めることができます。
耐摩耗性と安定成形への寄与
量産が進むと金型は摩耗し、製品品質は劣化します。特に、GF(ガラス繊維)入り樹脂のように摩耗性の高い樹脂を使う場合、摩耗しやすいゲート周辺などを耐摩耗性に優れた高硬度の鋼材で製作した入れ子に置き換えることが極めて有効です。これにより、バリの発生や寸法変化といった品質劣化を未然に防ぎます。
また、POMやPAのように成形時に腐食性ガスを発生させる樹脂に対しては、耐腐食性に優れたステンレス系の鋼材を入れ子に採用するなどの対策が有効です。樹脂の特性に応じた適切な材質選定が、安定した成形を長期間維持する鍵となります。
弊社が実践するイエプコ処理の効果
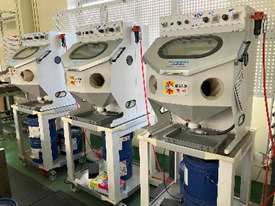
府中プラでは、入れ子の性能をさらに高めるため、「イエプコ処理」という特殊な表面処理技術を積極に活用しています。これは、微細なセラミック粒子などをメディアとして金型表面に高圧で噴射し、表面を改質する技術です。この処理により、主に以下の効果が得られます。
離型性の向上:表面が非常に滑らかかつ均一になり、成形品が金型からスムーズに抜けるようになります。これにより、製品の白化や変形を防ぎ、成形サイクルの短縮にも貢献します。
耐摩耗性の向上:表面の硬度が高まり、ガラス繊維入り樹脂などによる摩耗を効果的に抑制します。入れ子の摺動部に施せば、カジリや焼き付きも防げます。
汚れ付着の防止:緻密になった表面はガスヤケや樹脂のヤニが付着しにくくなり、金型清掃の頻度を削減できます。
当社では、特に微細形状や高い耐久性が求められる入れ子にイエプコ処理を施すことで、金型の長寿命化と製品品質の安定化を実現し、お客様のコスト削減に貢献しています。
入れ子設計の実務ポイントと注意点
入れ子設計は強力なツールですが、その効果を最大限に発揮させるためには、いくつかの実務的なポイントと注意点を押さえておく必要があります。
製品図面と金型設計の連動がカギ
最も重要なのは、「製品設計の段階から入れ子構造を前提として検討する」ことです。製品形状が固まってから金型設計を始めると、「入れ子にしたいが分割ラインが外観上許容できない」といった手戻りが発生しがちです。
理想は、製品設計の初期段階から金型メーカーと協議し、生産性やメンテナンス性を見越した上で製品形状を詰めていくことです。これにより、開発期間の短縮とトータルコストの最適化につながります。
金型メンテナンス性まで見据えた設計思考
優れた入れ子設計は、「将来の保守作業のしやすさ」まで見据えています。入れ子を固定するボルトは工具がアクセスしやすいか。交換時に他の部品を多数取り外す必要はないか。こうしたメンテナンス性への配慮は、量産現場での運用効率に直結します。
設計者は、自らがその金型をメンテナンスする立場になって考え、作業者の負担を軽減するような「思いやりのある設計」を心がける必要があります。
まとめ
入れ子設計は、射出成形の「見えにくい部分」ながら、製品品質とコスト競争力に直結する極めて重要な要素です。それは単なる部品分割ではなく、製品のライフサイクル全体を見通し、初期投資とランニングコスト、品質、メンテナンス性のバランスを最適化する「戦略的設計思考」そのものです。
さらに、当社が実践するイエプコ処理のような適切な表面処理を施すことで、金型の耐久性と成形安定性を一層高めることが可能です。製品仕様や生産条件を踏まえた合理的な入れ子設計と、表面処理を含めたトータルな金型最適化が、安定量産とコストメリットの両立につながります。