ホットランナーとは何か? 射出成形の基本構造とコスト・品質に関わる基礎知識
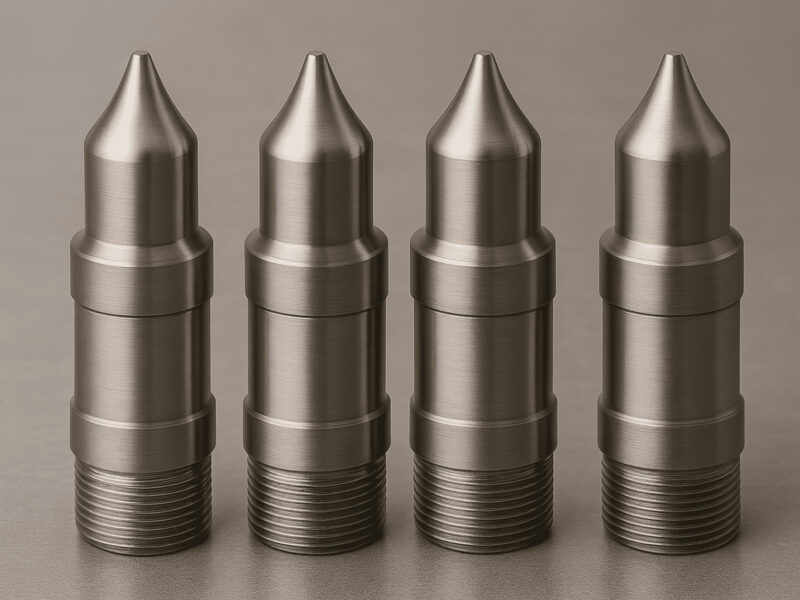
射出成形において、製品品質や生産性を左右する重要な要素のひとつが「金型設計」です。中でも、ランナー(樹脂の流路)部分の設計は、材料ロスやサイクルタイム、品質安定性に直結します。本コラムでは、近年多くの量産現場で採用されている「ホットランナー」について、その仕組みや構造を基礎からわかりやすく解説します。府中プラが長年培ってきた経験をもとに、その核心に迫ります。
ホットランナーとは? 金型のランナーを加熱する仕組み
射出成形金型には、成形機から製品部(キャビティ)まで溶融樹脂を導く「ランナー」という流路が不可欠です。このランナーの方式によって、生産性やコストは大きく変動します。ここでは、主流となりつつあるホットランナーの基本的な仕組みを、従来のコールドランナーと比較しながら解説します。
コールドランナーとの違い
従来のコールドランナーは、金型全体で冷却されるため、キャビティ内の製品と同時にランナー部の樹脂も固まります。成形後、製品と固まったランナーが一体で取り出されるため、ランナーを切り離す後工程と、廃棄または再利用される材料ロスが必ず発生します。
一方、ホットランナーは、ランナー部分にヒーターを内蔵し、常に加熱することで内部の樹脂を溶融状態に保つシステムです。樹脂は固まることなく直接キャビティに供給され、製品だけが成形されます。これにより、コールドランナーで課題だった材料ロスとランナーカット工程を原理的にゼロにすることができます。
【コールドランナーとホットランナーの比較】
項目 | コールドランナー | ホットランナー |
ランナーの状態 | 冷却され、製品と共に固まる | 加熱され、常に溶融状態を保つ |
材料ロス | ランナー部分がロスになる | 原理的に発生しない |
後工程 | 製品とランナーの切り離しが必要 | 不要 |
金型構造 | シンプル | 複雑(加熱・制御機構が必要) |
初期コスト | 安価 | 高価 |
ホットランナーの基本構造
ホットランナーシステムは、以下の主要な部品で構成され、精密な温度管理によって機能します。
マニホールド:成形機から供給された樹脂を分岐させ、各ノズルへ均等に分配する加熱ブロック。金型内部で樹脂流路のハブ(集線装置)の役割を果たします。
ノズル:マニホールドから送られた樹脂を、最終的にキャビティへ射出する筒状の部品。先端のゲートから製品が形作られます。
ヒーター・温度センサー:マニホールドとノズルを設定温度に加熱し、その温度を正確に測定・監視するための心臓部です。
制御装置:各センサーからの情報に基づき、ヒーターへの電力をコントロールする司令塔。システム全体の温度を精密に管理します。
ゲート方式の種類
ノズル先端(ゲート)の方式にはいくつか種類があり、製品の要求品質やコストに応じて選択されます。
ピンゲート(オープンゲート):構造がシンプルで安価。ただし、ゲートからの糸引き等が発生しやすい場合があります。
ダイレクトゲート:大きなゲート口を確保でき、大型品や高粘度樹脂に適します。ゲート跡が大きく残るのが特徴です。
バルブゲート:ピンの開閉でゲートを物理的に制御する高機能な方式。ゲート跡が美麗で高品質な成形が可能ですが、最も高価です。
ホットランナーの基本的な仕組みと成形サイクル
ホットランナーが実際の成形プロセスでどのように機能し、生産性に貢献するのかを解説します。
樹脂供給と保温のメカニズム
成形機で溶かされた樹脂は、金型に内蔵されたマニホールドに送られます。ヒーターで常時加熱されているマニホールドは、樹脂を溶融状態のまま分岐させ、各ホットランナーノズルへと分配します。同じく加熱されたノズルを通り、樹脂は最終的にキャビティへと充填されます。つまり、ホットランナーは金型内に常に温度が保たれた樹脂の流路を設けるようなものです。これにより、樹脂は熱や圧力を失うことなく、効率的にキャビティへ供給されます。
成形サイクルにおけるホットランナーの役割
ホットランナーは成形サイクルの各工程で、特に以下の点で優位性を発揮します。
射出・保圧工程:ランナーでの圧力損失が少ないため、射出・保圧がキャビティ末端まで効率的に伝わります。これにより、ヒケやソリが抑制され、製品の寸法安定性が向上します。
冷却工程:最大のメリットは冷却時間の短縮です。コールドランナーでは肉厚なランナーも冷却する必要がありましたが、ホットランナーでは製品部のみの冷却で済みます。この差が、成形サイクルタイムの大幅な短縮(製品によっては20~30%)に直結します。
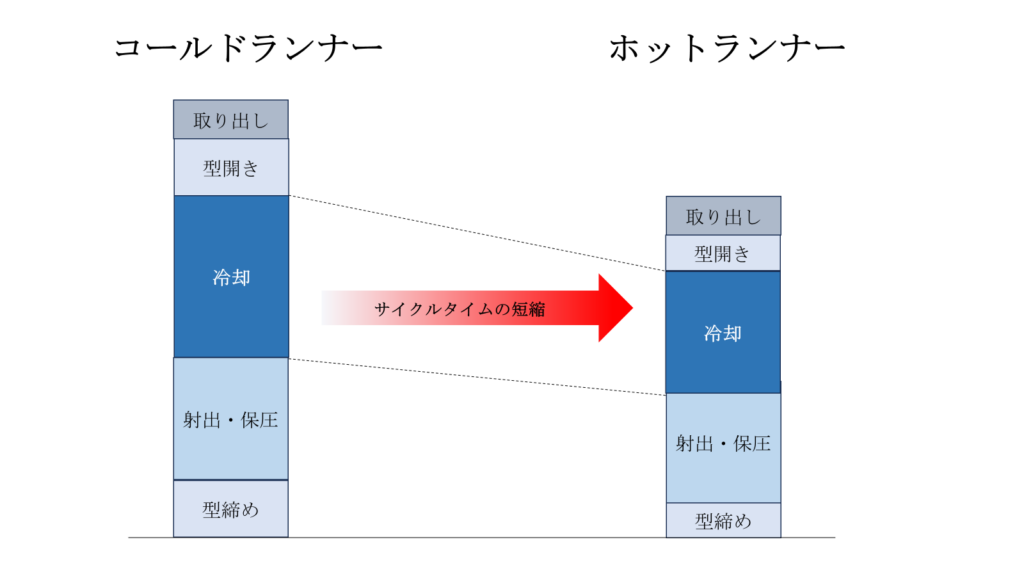
離型(型開き・製品取出し)工程:製品だけが取り出されるため、ランナー処理が不要となり、ロボットによる取り出しも容易になります。これにより、成形工程全体の自動化・省人化に大きく貢献します。
ホットランナー採用の前に知っておくべき注意点
ホットランナーは非常に有効な技術ですが、導入にはデメリットやリスクの理解が不可欠です。
金型コストと構造の複雑化
最大のハードルは、高価なシステム一式を組み込むことによる初期金型コストの増加です。コールドランナー金型に比べ、コストは大幅に上昇します。
また、加熱部と冷却部を共存させる断熱構造や、各部品の熱膨張を考慮した精密な設計・製作ノウハウが不可欠となり、金型構造は複雑化します。
材料適性の確認
ホットランナーは樹脂を高温で長時間保持するため、熱に弱い樹脂では注意が必要です。熱分解によるガスや炭化物の発生は、製品の強度低下や外観不良といった品質不良に直結します。そのため、使用樹脂がホットランナーに適しているか、事前の確認が不可欠です。
メンテナンス性とトラブルリスク
複雑な構造は、相応のトラブルリスクとメンテナンスを伴います。特に以下のトラブルには注意が必要です。
加熱不良:ヒーター断線等で樹脂が固化し、成形が停止する。
ノズル詰まり:異物や炭化物がゲートを塞ぎ、充填不良を起こす。
樹脂漏れ:最も深刻なトラブル。接合部から樹脂が漏れ出し、金型を損傷させる。修理には多大な時間とコストを要します。
これらのリスクを防ぐため、日常点検や定期メンテナンスといった、コールドランナー以上の手厚い保守管理が安定稼働の鍵となります。
まとめ
ホットランナーは、ランナーを加熱することで材料ロスをゼロにし、成形サイクルの短縮を実現する、射出成形における非常に強力な手段です。その導入は、生産効率の向上とトータルコストの削減に大きく貢献します。
しかし、その効果を最大限に発揮するためには、コールドランナーとの違いや、マニホールド、ノズルといった基本構造、そして保温の仕組みを正しく理解することが不可欠です。同時に、初期コストの高さや、材料適性、メンテナンスの重要性といった注意点も十分に考慮し、製品仕様や生産量に応じた適切な判断が求められます。
府中プラでは、お客様の製品に最適なランナー方式をご提案いたします。次回のコラムでは、今回触れた内容をさらに掘り下げ、ホットランナーがもたらす具体的なメリットや、採用を判断する上での設計・コスト面でのポイントについて、より詳しく解説します。