エンプラの線膨張係数が設計に与える影響:寸法変化と対策の基礎知識
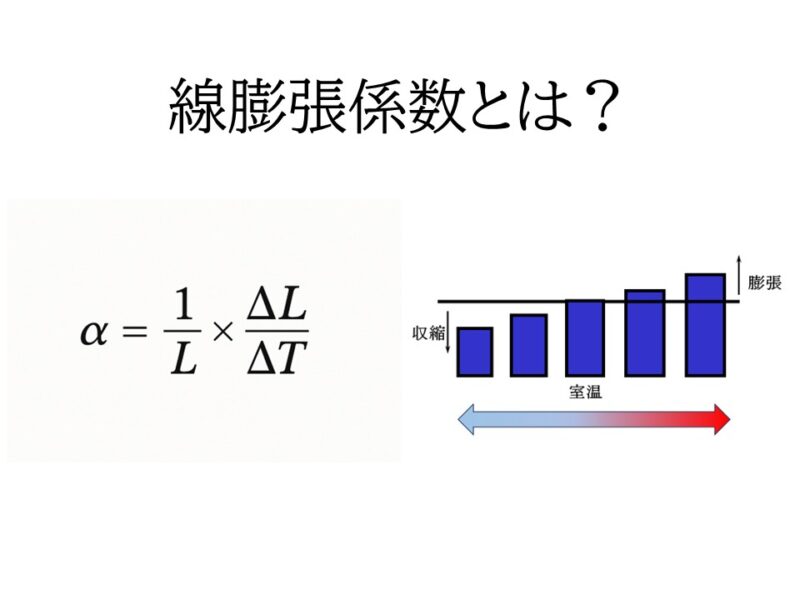
エンプラは、軽量かつ高機能な材料として金属代替の役割を担い、今日の製品開発に不可欠な存在です。しかし、その優れた特性の裏で、設計者が見落としがちな重要な特性があります。それが「熱による寸法変化」、すなわち「線膨張」です。
エンプラの線膨張係数(CTE; Coefficient of Thermal Expansion)は金属に比べて格段に大きく、この特性を無視した設計は、部品の嵌合不良や動作不良、最悪の場合は製品の破損といった深刻な品質問題を引き起こす原因となります。本コラムでは、エンプラを扱う上で必ず知っておくべき線膨張係数の基礎知識と、それが製品設計に与える具体的な影響、そして信頼性を確保するための対策について、要点を絞って分かりやすく解説します。
線膨張係数とは何か
製品設計において温度変化を考慮する上で、基本となる物理量が「線膨張係数」です。まずはこの言葉の定義と、特に樹脂材料を扱う上での注意点を確認しましょう。
定義と単位
線膨張係数とは、温度が1℃上昇するごとに、材料の長さが元の長さに対してどれくらいの割合で変化するかを示す指標です。単位は「×10⁻⁵/℃」や「ppm/℃」などで表され、この数値が大きいほど、温度による寸法変化が大きい材料であることを意味します。
例えば、長さ1mの棒材が温度1℃の上昇で70μm(0.07mm)伸びる場合、その材料の線膨張係数は7.0×10⁻⁵/℃となります。精密な部品設計において、このわずかな変化が無視できない影響を及ぼすことがあります。
なお、熱による膨張には体積全体が変化する「体積膨張」もありますが、部品同士の位置関係やクリアランスが重要となる機械設計では、特定の方向の長さ変化を示す「線膨張」が主に用いられます。本稿でも線膨張係数を中心に話を進めます。
樹脂成形品特有の「異方性」
金属材料の多くは、どの方向にも物性がほぼ均一な「等方性」を示します。一方で、射出成形などで製造される樹脂製品は、方向によって物性が異なる「異方性」を持つという大きな特徴があります。
これは、溶融した樹脂が金型内を流れる際に、樹脂を構成する高分子や配合されたガラス繊維などが流れの方向に沿って並ぶ「配向」が生じるためです。この配向により、線膨張係数にも方向性が生まれます。
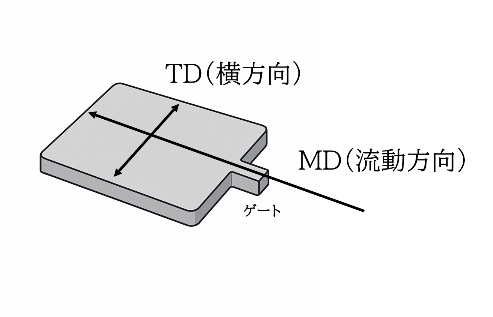
流れ方向(MD):分子や繊維が整列しているため、熱で膨張しにくく、線膨張係数は小さくなります。
流れに直角な方向(TD):配向が弱いため、熱で膨張しやすく、線膨張係数は大きくなります。
近年の研究では、射出成形品の線膨張係数異方性が、繊維配向や分子配向の度合いに強く依存することが明らかになっています。特に短繊維強化樹脂では、面内配向が進むことで線膨張係数が等方的に近づく傾向が観察されています。
このように、一つの部品内でも測定する方向によって線膨張係数が異なるという点は、樹脂設計における非常に重要なポイントです。この異方性が、後述する製品の「反り」や「歪み」の主な原因となります。
測定方法の概要
線膨張係数は、TMA(熱機械分析装置)などを用いて精密に測定されます。代表的な国際規格としてISO 11359やASTM D696があり、これらの規格に準拠した試験で得られたデータが、材料選定や設計の基礎情報となります。
エンプラと金属の線膨張係数の比較
エンプラを金属の代替として使用する際、両者の線膨張係数の差を具体的に把握しておくことが不可欠です。この差がいかに大きいか、代表的な材料の数値で比較してみましょう。
代表的な金属の線膨張係数(目安)
- ステンレス鋼(SUS304): 約1.7 ×10⁻⁵/℃
- 炭素鋼(S45C): 約1.2 ×10⁻⁵/℃
- アルミニウム(A5052): 約2.3 ×10⁻⁵/℃
代表的なエンプラ(非強化)の線膨張係数(目安)
- PC(ポリカーボネート): 約6.5~7.0 ×10⁻⁵/℃
- PBT(ポリブチレンテレフタレート): 約7.0~9.0 ×10⁻⁵/℃
- PPS(ポリフェニレンサルファイド): 約3.0~6.0 ×10⁻⁵/℃
- PEEK(ポリエーテルエーテルケトン): 約4.5~5.5 ×10⁻⁵/℃
両者を比較すると、一般的なエンプラの線膨張係数は、アルミニウムの約3倍、ステンレス鋼の4~5倍にも達することがわかります。これは、同じ温度変化に対して、エンプラ部品が金属部品の何倍も大きく寸法変化することを意味し、両者を組み合わせる際には特に注意が必要です。
スーパーエンプラ(PEEK、PPS等)は、非強化でも比較的低い線膨張係数を示し、寸法安定性に優れることが学術的にも報告されています。
ガラス繊維(GF)強化による低減効果
この大きな線膨張係数を改善する有効な手段が、ガラス繊維(GF)などを配合した強化グレードの使用です。ガラス繊維自体の線膨張係数は極めて小さいため、樹脂に混ぜ込むことで成形品全体の線膨張係数を大幅に下げることができます。
例えば、PBT樹脂の場合、ガラス繊維を30%強化したグレード(PBT GF30)の線膨張係数は約2.0~3.0×10⁻⁵/℃となり、非強化品の1/3以下にまで低減します。この値はアルミニウムに近く、金属との寸法変化の差を小さくできるため、寸法安定性が求められる用途で非常に有効です。ただし、繊維を配合することで前述の「異方性」はより顕著になるため、設計上の配慮は一層重要になります。
線膨張係数が製品設計に与える影響
理論的な数値の差が、実際の製品にどのような問題を引き起こすのか。ここでは、設計現場で直面する具体的な影響を解説します。
寸法精度への影響:干渉、ガタつき、動作不良
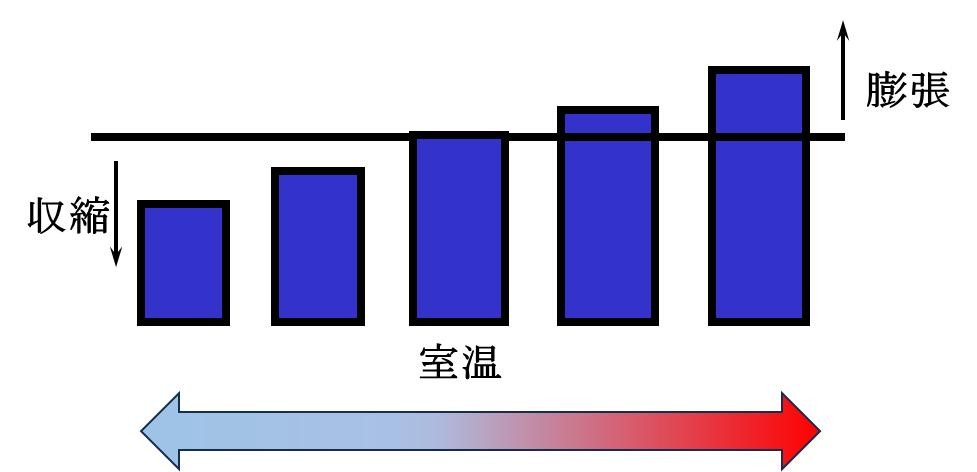
製品が使用される環境温度は常に変化します。特に、内部に発熱源を持つ電子機器や、過酷な温度変化に晒される部品などでは、熱による寸法変化が製品機能に直接影響します。
高温環境下では、部品が想定以上に膨張し、隣接する部品との隙間(クリアランス)を埋めて「干渉」を起こします。これにより、部品同士が強く押し合って破損したり、摺動部が動かなくなったりする動作不良の原因となります。一方、低温環境下では、部品が収縮することで、圧入で固定していた部品に「ガタつき」が生じたり、必要な嵌合力が失われたりします。製品が機能する全温度域で性能を維持するためには、この熱による寸法変化を定量的に見込んだ公差設計が不可欠です。
異材接合部での応力発生と破損リスク
金属部品とエンプラ部品をボルトやインサート成形などで接合する「異材接合」は非常に多い設計手法ですが、線膨張係数の差が大きな問題を引き起こすことがあります。温度が変化すると、エンプラは金属よりも大きく膨張・収縮しようとしますが、金属によって動きが拘束されるため、接合界面に強い「熱応力」が発生します。
この熱応力が繰り返し加わることで、以下のような不具合が生じます。
- 接合部に微小なクラックが発生し、製品寿命を縮める。
- インサートナットの周囲に隙間が生じ、保持力が低下する。
- 接着や溶着で接合した部分が剥がれてしまう。
- 部品全体が応力を逃がそうとして反ってしまう。
特に温度変化の激しい環境では、この熱応力が製品の長期信頼性を損なう致命的な要因となり得ます。
成形品の異方性による「反り」と「歪み」
樹脂成形品が持つ線膨張係数の異方性(MDとTDの差)は、製品の「反り」や「歪み」の直接的な原因です。高温の金型から取り出されて冷却される過程で、線膨張係数の大きいTD方向は、MD方向よりも大きく収縮しようとします。この収縮率の差が、平らであるべき部品を反らせてしまうのです。
この現象は製品使用中の温度変化でも同様に起こり、常温では問題なかった部品が高温環境で反ってしまうこともあります。この反りは、部品の組み付け性を悪化させたり、外観品質を損なったりする原因となります。
対策と材料選定の考え方
線膨張に起因する問題を未然に防ぐには、材料選定から設計、成形までの一貫した視点での対策が求められます。
線膨張係数の小さい材料を選ぶ
最も基本的な対策は、用途に適した低線膨張材料を選ぶことです。PEEKやPPSといったスーパーエンプラは、非強化グレードでも比較的線膨張係数が低く、高い寸法安定性が期待できます。前述の通り、ガラス繊維などを配合した強化グレードは、線膨張係数を金属に近いレベルまで低減できる非常に有効な選択肢です。
繊維配向を考慮した金型・製品設計
特にGF強化グレードを用いる場合、反りの原因となる繊維配向をコントロールすることが重要です。樹脂の入り口であるゲートの位置や数を工夫することで、製品内の樹脂の流れ方、すなわち繊維の配向を制御し、反りを抑制します。また、製品の肉厚をできるだけ均一にすることも、均一な冷却収縮を促し、反りを低減するための基本原則です。
熱変形を許容する組立設計
材料や成形だけでは吸収しきれない寸法変化は、組立構造の工夫で対応します。熱による変形を力で抑え込むのではなく、うまく「逃がす」設計思想が鍵となります。ネジ止め箇所を長穴にするなど、部品が熱膨張した際にスライドできる「遊び」を設けることで、部材間に発生する熱応力を効果的に逃がします。また、使用温度範囲から寸法変化量を計算し、高温で干渉せず、低温でガタつかない、最適な隙間を設計に盛り込み、適切にクリアランスを設計します。
シミュレーションの活用
CAEによるシミュレーションは、試作前に問題を発見し、対策を講じるための強力なツールです。熱変形解析は、製品が特定の温度に置かれた際の変形量や応力分布を予測し、設計の妥当性を検証します。流動解析は、成形時の樹脂の流れや繊維配向を予測し、反りの発生を未然に防ぐためのゲート位置や成形条件の最適化に役立ちます。
材料カタログに記載されている線膨張係数は、あくまで標準的な条件下での参考値です。実際の製品の線膨張係数は、形状や成形条件によって変化するため、特に高精度が求められる場合は、実測値やシミュレーションに基づいた慎重な設計が不可欠です。
まとめ
エンプラの線膨張係数は、金属代替や高精度な製品設計を進める上で決して見過ごすことのできない重要な特性です。金属に比べて数倍大きいこの値を念頭に置かなければ、意図しない寸法変化が製品の品質と信頼性を根底から揺るがしかねません。
この課題を乗り越えるためには、材料の特性を正しく理解し、材料選定の段階から、熱変形を許容する設計、繊維配向をコントロールする成形技術まで、開発プロセス全体で一貫した配慮を行うことが不可欠です。
府中プラでは、長年の樹脂成形に関する知見を活かし、線膨張係数を含む各種特性評価から、シミュレーションを駆使した設計支援まで、お客様の課題解決をトータルでサポートいたします。エンプラの寸法安定性や熱に関する設計でお困りの際は、ぜひお気軽にご相談ください。お客様の製品開発に最適なソリューションをご提案いたします。