「噴霧器のノズル」の樹脂化
Before
本事例の「噴霧器のノズル」は、噴出穴の芯ずれ精度が重要な部品です。従来、金属製ノズルを使用していましたが、ノズル底部と上部を貫通させるための穴加工には多くの時間とコストがかかっていました。
また、内部に斜めの貫通穴を持つ特殊な形状が特徴で、複数サイズの製品を製造する際にも個別の加工が必要でした。
After
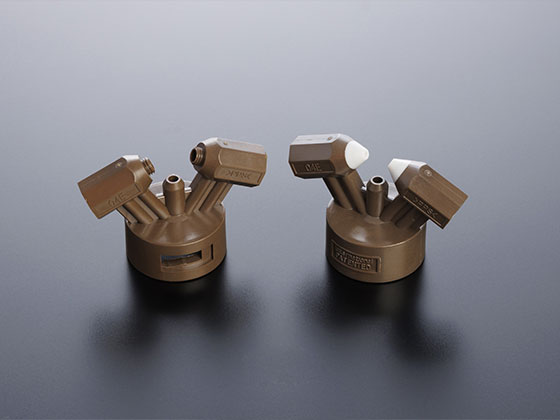
噴霧器のノズルを金属から樹脂へ変換することで、製造コストと組立工程のタクトタイムの大幅な短縮を実現しました。
内部に斜めの貫通穴を含む複雑な形状を1回の成形で対応してます。これにより、後工程で必要だった穴あけ加工を完全に省略しました。
また、同形状で異なるサイズの製品についても、金型の駒交換による柔軟な対応を可能にし、効率的な生産を実現しています。
Point
1.製造コスト削減:金属加工に比べ、樹脂成形によって穴あけ工程を排除し、大幅なコストダウンを達成。
2.品質向上:斜めの貫通穴を含む複雑形状を1回の成形で実現し、精度と品質を両立。
3.サイズ展開の柔軟性:金型の駒交換により、複数サイズの製品を効率よく製造可能に。