耐熱・耐薬品性が求められる「配管継手部品」の樹脂化
Before
本事例の「配管継手部品」は従来、この部品は金属で製造されており、高温や薬品に晒される厳しい使用環境でも耐久性と性能を発揮していました。
しかし、金属製品特有の錆の発生や重量の問題が課題とされており、耐久性向上と軽量化を目的とした樹脂化の検討が求められていました。
また、加工工程が複雑で、製造コストの削減も課題となっていました。
After
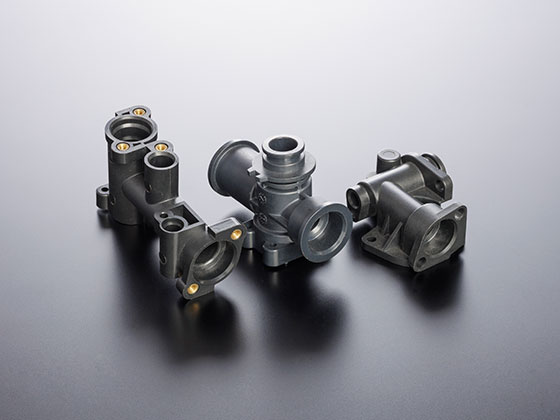
配管継手部品の素材を金属から高耐熱性・高強度、さらに優れた耐薬品性を持つPPA アモデルに変更する提案を行い、樹脂化を実現しました。この素材は、成形難易度が高いMXD6レニーを上回る技術的知見を必要としますが、当社は豊富な成形実績と高度な技術力により、安定した量産化を達成しました。
樹脂化により、錆の発生を防止し、耐久性の向上と軽量化を同時に実現しました。また、金属製時代には複雑だった加工工程を削減し、製造コストの大幅な削減にも成功しています。
さらに、多方スライドを活用した複雑形状の金型設計を製作し、バリの発生を最小限に抑えることで、外観品質に対する厳しい要求にも対応しました。
最後に、真鍮製のビットを熱カシメすることで、接合部の耐久性を確保し、信頼性の高い製品を提供しています。
Point
1.金属から樹脂への転換:金属製品をPPA アモデルに樹脂化することで、錆の防止、軽量化、耐薬品性の向上を実現。
2.高度な成形技術で高品質を確保:アモデル特有の成形難易度に対応するため、当社の蓄積された技術と多方スライドを活用した金型設計により、外観品質と量産性を両立。
3.耐久性への対応:成形後に真鍮製ビットの熱カシメ工程を導入し、接合部の強度を高め、過酷な使用環境下でも信頼性の高い性能を発揮。