射出成形におけるヒケの原因と対策
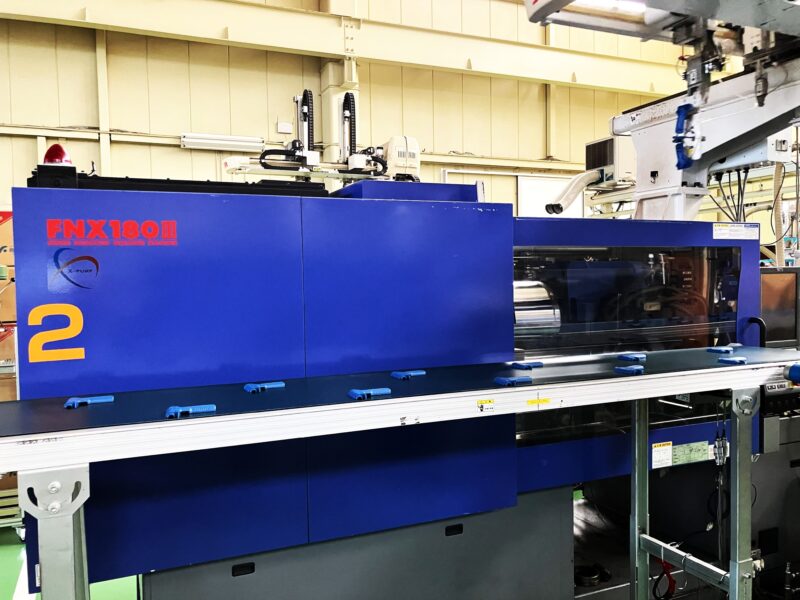
射出成形におけるヒケとは、成形品の表面に生じる凹みや歪みを指します。特に、肉厚の部分やリブ、ボスの周辺で発生しやすく、外観品質の低下を招くだけでなく、製品の機能性や組み立て精度にも影響を与える可能性があります。
ヒケが発生する主な原因は、樹脂の冷却収縮によるものです。射出成形では、溶融した樹脂が金型内に充填された後、冷却・固化することで形状が形成されます。この過程で、樹脂は冷却とともに収縮しますが、特定の箇所で収縮量が不均一になると、表面の凹みとして現れます。
リブとは、例えば空の箱をイメージしてください。その内側に斜めに切ってある薄板のようなものです。
樹脂成形において何も工夫なくこれを形作った場合、冷却による収縮の効果で壁面は内側に引っ張られたように倒れこむ形状(凹み)になります。収縮率の高い材料においてはより顕著です。これでは要求寸法が出せず組み立てもままなりません。
リブはこれらの効果を軽減、抑止し、さらに製品強度を向上させる効果もあるために設けられます。しかし、リブを設置した周辺部分は肉厚不均衡になりやすいです。
ボスとは面上に隆起した凸形状の突起です。機械の構造を支えたり、ネジ穴やピンで部品を結合させたりする役割の他、相手部品との位置決めなど、このボスにリブをつけ、倒れを防止する場合もあります。設計上、このボスのある位置は比較的、肉厚になりやすいです。
射出成形におけるヒケの特徴として、以下の点が挙げられます。
・表面の凹み
肉厚部分やリブの周辺で発生しやすく、見た目が損なわれます。
・光の反射の違い
ヒケがある部分は周囲と比べて光の反射が異なり、品質不良として目立ちます。
・寸法変化を伴う場合がある
製品の内部応力が原因で、長期間使用すると変形が進行することもあります。
ヒケは、ボイド(空隙・気泡)やフローマーク(フローマーク)と混同されることがありますが、発生した不良を正確に分類することが重要です。ボイドは成形品内部に生じる気泡であり、フローマークは樹脂の流動不良による表面の模様です。ヒケは、成形品の表面に発生する凹みである点が大きく異なります。
ヒケが発生すると、外観不良だけでなく、製品の機械的強度の低下や、部品の組み立て精度に影響を与えることがあります。そのため、特に高品質が求められる工業製品では、ヒケの発生を抑えるための対策が必要不可欠です。
ヒケの発生原因
ヒケの発生原因は、大きく分けて成形条件、金型設計、製品設計、材料特性の4つの要因に分類されます。それぞれの要因について詳しく解説します。
成形条件に起因する要因
金型温度の不適切さ
溶融樹脂粘度の低下
シリンダー温度を上げると溶融樹脂の粘度が低下します。低粘度状態では金型内での樹脂流動が速くなり、冷却開始後の凝固層形成が遅延によるヒケが促進されます。
射出速度と圧力の不足
適切な射出速度と圧力が確保されていないと、樹脂が均一に充填されず、特定の部位に収縮が集中します。
保圧時間の不足
保圧時間が短いと、冷却中の樹脂の収縮を補償できず、結果としてヒケが生じます。
金型設計に起因する要因
ゲート設計の不備
ゲートの位置やサイズが適切でないと、樹脂の流れが偏り、肉厚部分にヒケが生じやすくなります。
冷却系統の不均一性
金型内の冷却が均一でないと、一部のエリアで収縮が大きくなり、ヒケの原因となります。
製品設計に起因する要因
肉厚の不均一性
肉厚の異なる部分(偏肉)があると、冷却速度の差によって収縮が不均一になり、ヒケが発生します。
リブやボスの設計不良
リブやボスは材料によっても収縮率が変わってくるため、それらの肉厚と外観上の板厚(母材)が同じ厚みということはなく、一般的にリブは40~70%ボスは40~60%です。この振り幅は材料の収縮率と外観性のバランスを図っていくことになります。
材料特性に起因する要因
樹脂の収縮率
樹脂の種類によって収縮率が異なり、高収縮率の材料はヒケが発生しやすくなります。
樹脂の流動性
流動性の低い材料は金型内での充填が不十分となり、ヒケの原因となります。
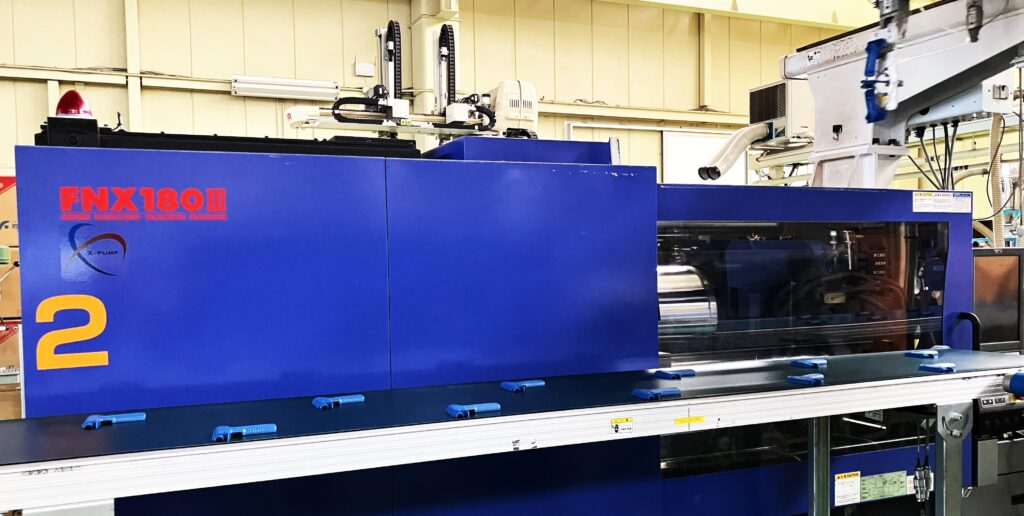
ヒケの発生を防止する対策
ヒケを防止するためには、成形条件の最適化、金型設計の改善、製品設計の工夫、材料選定を総合的に判断し対応します。
成形条件の最適化のみで改善されることもありますが、材料変更で収縮率の差が大きいものだと設計、金型の修正が必要になるような複合的な場合もあります。
成形条件の最適化
溶融樹脂粘度の上昇
シリンダー温度を下げると溶融樹脂の粘度が上昇します。高粘度状態では金型内での樹脂流動が遅くなり、冷却開始後の凝固層形成が早まります。これにより成形品表面が急速に固化し、内部への樹脂補充が可能な時間を確保できるため、体積収縮によるヒケが抑制されます。
金型温度の適正化
金型温度を適切に設定し、材料の流動性を確保することで均一な充填を実現します。金型温度が低すぎる場合、局所的な冷却不均一が発生しやすいため、成形部品の肉厚部分に合わせた温度管理が必要です。
射出速度と圧力の調整
適切な射出速度と圧力を設定し、均一な樹脂流動を確保します。高速充填しすぎると、ガス溜まりやウェルドラインの発生リスクがあるため、適切なバランスが重要です。
保圧時間と圧力の適正化
保圧時間を適切に延長し、収縮を補償します。保圧圧力を適正に設定し、型締め力と射出速度の調整によって均一な冷却を実現します。
金型設計の改善
ゲート位置とサイズの最適化
適切なゲート設計により、均一な充填を実現します。メインゲートとサブゲートの配置を工夫し、流動方向を最適化します。
冷却系統の均一化
金型内の冷却を均一にし、収縮差を抑制します。局所的な冷却の遅れを防ぐため、ウォーターチャンネルの設計を最適化します。
製品設計の工夫
肉厚の均一化
製品の肉厚を均一にすることで、冷却速度の差を減らし、ヒケの発生を防ぎます。
リブやボスの設計改善
リブやボスの肉厚を適切に調整し、収縮が集中しないようにします。
材料選定の工夫
収縮率の低い材料の選択
ヒケが発生しやすい高収縮率の材料を避け、低収縮率の材料やグレードを選ぶことでヒケを抑えることができます。
充填剤入り材料の選択
ガラス繊維は、プラスチック樹脂よりも収縮率が低いため、繊維が樹脂内部に均一に分散することで、全体の収縮を抑制します。特に肉厚部分での体積収縮が減少するため、ヒケ(表面のへこみ)が発生しにくくなります。但し、配向方向によっては改善されない場合もあります。
ヒケ対策表
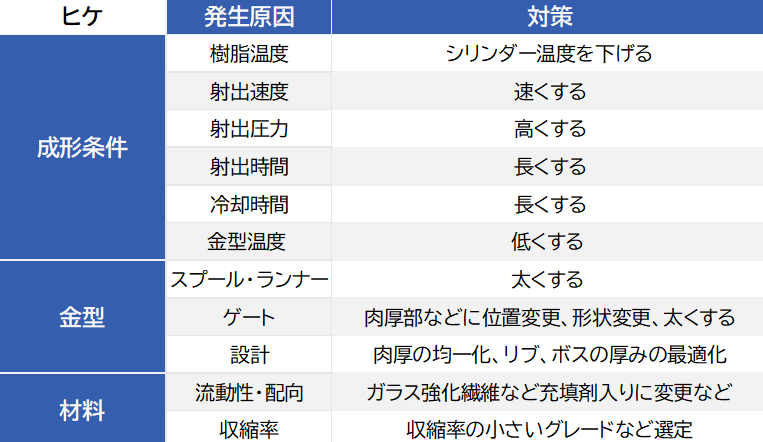
まとめ
射出成形におけるヒケは、成形品の品質に大きな影響を与える不良の一つです。ヒケの発生原因を正確に把握し、成形条件、金型設計、製品設計、材料特性の各要素に対する対策を講じることで、ヒケの発生を効果的に防止できます。当社では、長年の経験と高度な成形技術を活かし、高品質な成形品を提供します。
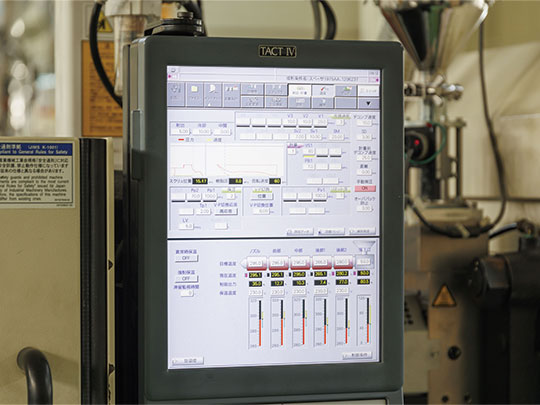