PEEKだけじゃない!PESの性能とコストで差がつく次世代部品開発
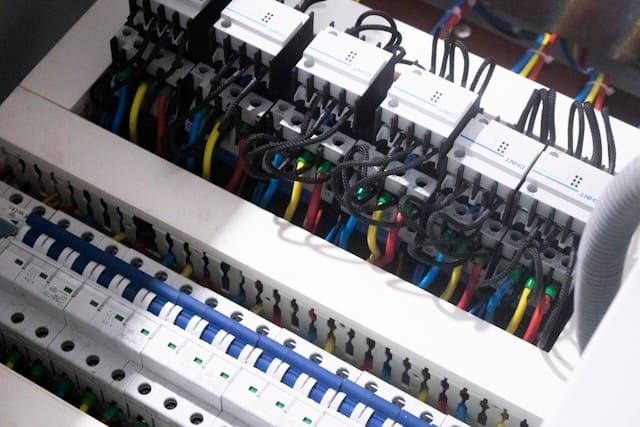
高性能樹脂の一つであるPES(ポリエーテルサルフォン)は、その優れた特性から各種産業分野で注目されています。例えばPEEKやPEIと並び、PESはスーパーエンプラに位置付けられる高機能材料です。これらは従来の汎用樹脂では対応できない過酷な環境下でも使用可能であり、PESはその中でも高い性能と比較的良好なコストバランスを兼ね備えている点で注目されています。電子電気、機械、医療、産業機器など、幅広い分野の製品設計者にとって、PESは金属や他の樹脂を置き換える有力な素材候補となり得ます。近年では、製品の軽量化・高性能化に伴い金属部品を高性能樹脂に置き換えるニーズが高まっており、PESのようなスーパーエンプラの重要性はますます増しています。
射出成形メーカーから見たPESの魅力
射出成形によって複雑な形状部品を製造できるPESは、高機能樹脂として次のような魅力を備えています。
優れた耐熱性
PESはUL規格での連続使用温度が約180℃に達する高耐熱性樹脂です。未強化樹脂としてはフッ素樹脂(PTFE)に次ぐ水準であり、高温環境下でも性能を維持できます。例えば通常のプラスチックでは変形してしまうような150℃を超える条件下でも、PESなら形状と機能を保つことが可能です。そのため、機械や電子機器の高温部品にも安心して適用できます。
高い機械的強度と寸法安定性
PESは常温から高温に至る広い温度範囲で剛性・強度をしっかり保つことができ、クリープ(長期間荷重による変形)もしにくい樹脂です。また非結晶樹脂であるため成形収縮が小さく、複雑形状でも寸法精度高く成形できます。その結果、精密部品に要求される寸法安定性に優れ、長期にわたり安定した機械的性質を発揮します。
耐薬品・耐加水分解性
分子中にスルホン基を持つPESは化学的にも安定で、各種薬品や油剤への耐性があります。例えば、自動車の油圧作動油や医療用の消毒薬などに長時間さらされる環境でも、PESは物性の劣化が少なく、安心して使用できます。特に高温下の水や蒸気による劣化(加水分解)に強く、繰り返しのオートクレーブ(高圧蒸気滅菌)にも耐えられるため、医療機器部品などで長期間使用できます。
難燃性・電気絶縁
PESは自己消火性を持ち(UL94 V-0相当)、難燃剤無添加でも高い難燃性を示します。しかもベース樹脂自体がハロゲン成分を含まないため、燃焼時の有害ガス発生が少なく安全性に優れます。また電気絶縁性にも優れるため、高電圧がかかる電子電気部品でも安心して使用でき、安全基準のクリアに貢献します。
良好なコストパフォーマンス
PESは、PEEKと比べて材料コストが低めで、量産成形によるコストメリットも得やすい素材です。さらに、PESは歴史が長く複数のメーカーから供給されているため入手性にも優れます。高性能と経済性を両立できることから、設計段階で採用しやすい点も魅力と言えます。このようにPESは、射出成形によって得られる高精度な形状と相まって、過酷な条件下で求められる性能を発揮できる点が大きな魅力です。射出成形メーカーとしても、これらの利点を持つPESを活用することで、金属代替や高機能部品の実現に貢献できると考えています。
PESの化学的背景と特性
分子構造と基本情報
ポリエーテルスルホン(PES)は、その名称が示す通り、分子主鎖にエーテル結合とスルホン基(–SO₂–)を交互に有する芳香族系の高機能ポリマーです。具体的には、パラ位で結合したベンゼン環同士をエーテル基とスルホン基でつないだ直鎖状構造を持ち、分子全体として高い剛性と耐熱性を発揮します。PESは非結晶(非晶性)樹脂に分類されるため明確な融点を持ちませんが、ガラス転移温度(Tg)は約225℃と非常に高く、非晶性スーパーエンプラの中でもトップクラスの耐熱性を有します。1970年代に商業化されて以降、その高温特性と成形安定性から多くの産業分野で活用されてきました。
優れた耐熱性と寸法安定性
PESは高いTgに加え、熱変形温度(HDT)も200℃を超えるため、過酷な高温環境下でも機械的強度や形状を維持できます。さらに、非結晶樹脂であることから成形収縮が少なく、寸法変化も各方向で均一です。これは精密成形部品において非常に有利であり、電子部品のハウジングや自動車エンジン周りの構造部品など、高精度が要求される用途に適しています。
耐薬品性と加水分解耐性
PESは多くの油類、アルカリ、アルコール、洗浄剤に対して高い耐薬品性を示します。また、エステル結合を含まない構造であるため加水分解に強く、熱水や蒸気環境にも耐性を持ちます。これにより、オートクレーブ滅菌が必要な医療機器部品や、熱水が流れる配管系部品などでも高い信頼性を発揮します。寸法安定性も吸水率の低さに支えられており、長期使用でも物性劣化が起こりにくい点が特長です。このように、PESの分子構造に由来する優れた耐熱性・寸法安定性・耐薬品性は、極めて過酷な条件で使用される機器部品において重要な性能要素となります。次節では、こうした高性能素材を扱ううえでの射出成形上の課題と、それに対する当社の取り組みについてご紹介します。
PES成形における技術課題と当社のソリューション
高温成形に対応する設備と温度管理技術
PESの成形には非常に高い温度が求められます。樹脂の溶融温度は330〜380℃に達し、一般的な成形機では対応できない場合があります。当社では、PES専用に高温対応の射出成形機を導入しており、バレル全体の温度を細かく制御可能です。樹脂の熱劣化を防ぐため、シリンダー温度は最適化されたプロファイル(例:後端340℃ → 前端360℃)で制御され、スクリューの形状も滞留を最小限に抑える設計としています。これにより、安定した溶融状態での成形が可能となり、品質のばらつきを防ぎます。
高精度な金型温度制御と寸法安定性の確保
PESは寸法安定性に優れた材料ですが、それを最大限引き出すには金型温度のコントロールが極めて重要です。金型温度は140~180℃と高く、一般樹脂とは異なる加熱システムが必要です。当社では、成形収縮を最小限に抑え、高精度な部品の量産を実現しています。収縮率や補正値に関しては、自社で蓄積したデータベースを活用し、型設計段階から反映させています。
乾燥管理と外観品質の維持
PESは吸湿性があり、成形前の乾燥が不十分だと気泡や銀筋などの外観不良の原因になります。当社では、ペレットを160~180℃で最低5時間以上乾燥させる体制を取っています。これにより、外観の透明感や強度が求められる部品でも安定した品質を提供することができます。見た目の品質と寸法の安定性を両立させるには、こうした乾燥管理の徹底が不可欠です。
高粘度樹脂への対応と成形安定性
PESの溶融状態は高粘度であり、金型への充填性に課題があります。当社では、大容量・高圧力に対応した成形機を導入し、必要に応じて150〜180MPaの射出圧を確保しています。また、ゲート径やランナー構造を工夫し、空気の逃げ道を確保することで、ヒケやウェルドラインの発生を抑制。射出速度と保圧切り替えのタイミングも最適化しており、成形品内部に応力が残らないように制御しています。冷却時間も必要最小限に抑えることで、サイクルタイムの短縮とコスト低減にも貢献しています。以上のように、PESの成形には高温管理、精密な金型設計、徹底した乾燥管理、高粘度対応といった複数の技術要素が求められます。当社ではこれらすべてに対して実践的なノウハウを蓄積しており、PESの成形における高度な要求に対応できる体制を構築しています。難易度の高い材料であっても、私たちは「量産品質の安定化」と「高機能部品の実現」を両立させることをお約束します。
産業界におけるPESの採用事例
電子・電気分野
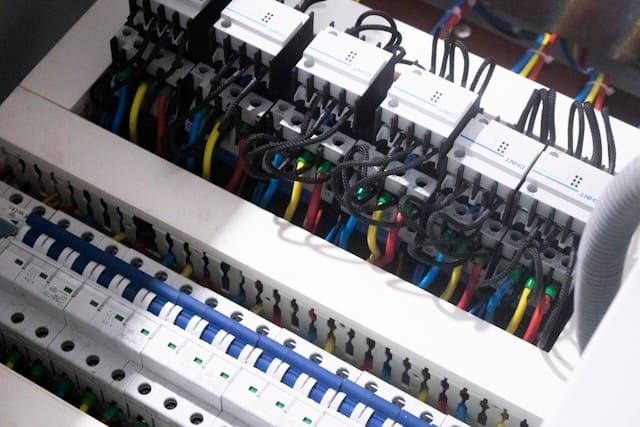
コネクタ、スイッチ部品、コイルボビン、ヒューズボックスカバーなど、高温や高電圧環境で使用される絶縁部品にPES製が用いられています。耐熱・難燃性に優れることから、動作時に発熱する電子機器内部でも信頼性の高い材料として活躍しています。また、ヘアドライヤーや照明機器の高温部品にも使用されるなど、身近な製品にも応用されています。
自動車分野
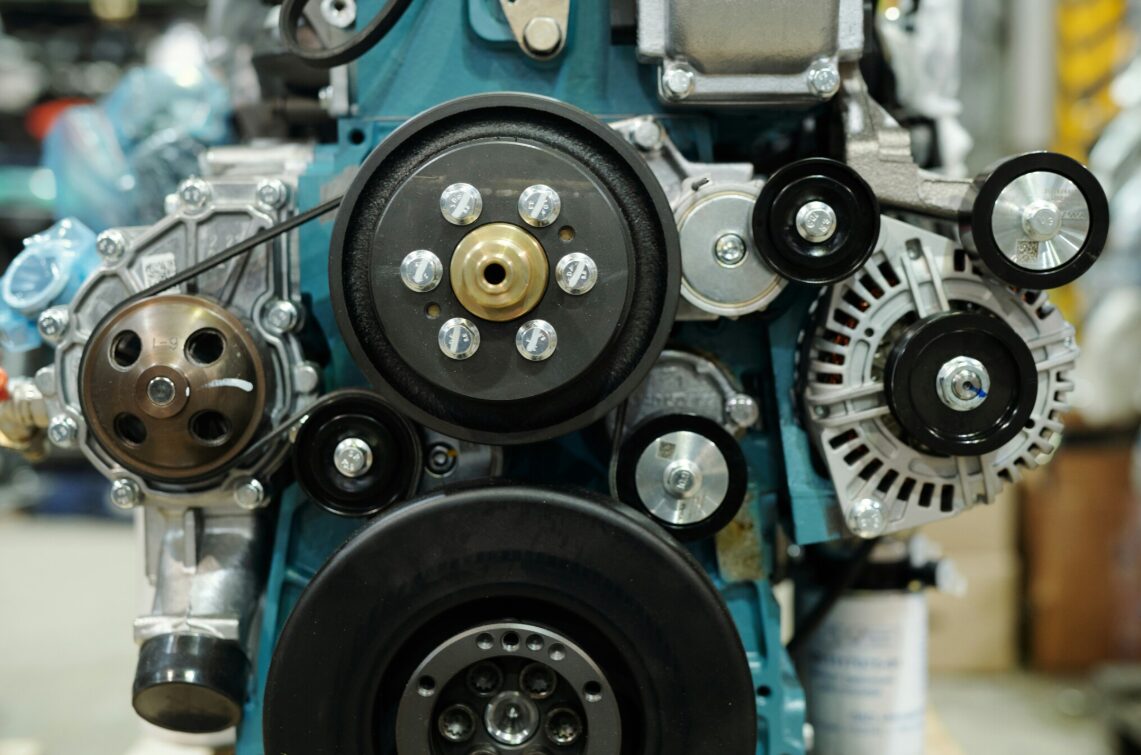
エンジン周辺部品(インシュレータやポンプハウジングなど)やランプのリフレクター(反射板)にPESが使われています。金属代替による軽量化と耐熱性の両立が求められる場面で効果を発揮し、耐油性・耐ガソリン性を活かして燃料系統部品にも適用されています。さらには、自動変速機内部の樹脂製ギアといった高負荷部品への採用例もあります。
産業機器・機械部品分野
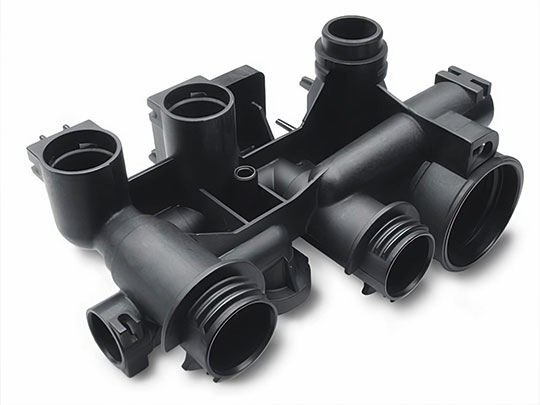
ボイラーや温水ポンプの部品、工業用バルブや配管など、熱水や薬品に晒される機器でPES製部品が用いられています。高温下でも物性が安定し、腐食や劣化が起こりにくいため、装置の信頼性向上に寄与しています。また、食品製造設備での高温洗浄工程に耐えるプラスチック部品として採用される例もあります。
医療分野
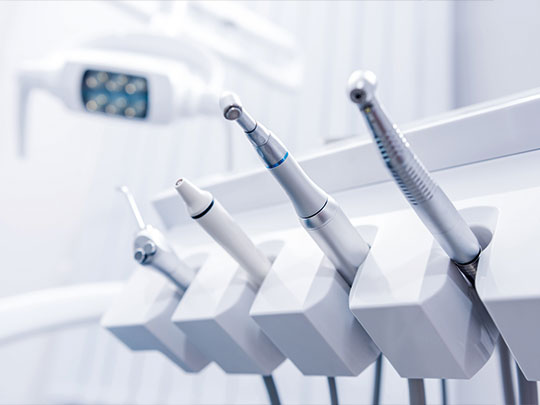
手術器具のハンドルや流体接続部品、分析機器のカセット類などでPESが採用されています。高圧蒸気滅菌(オートクレーブ)による繰り返し消毒にも耐え、長期間の使用でも機械的強度を維持できるため、医療現場で安心して使用できる材料です。また、人工透析装置のフィルターハウジングなど体液に触れる部品にも用いられており、生体適合性と耐久性を両立しています。
航空・宇宙分野
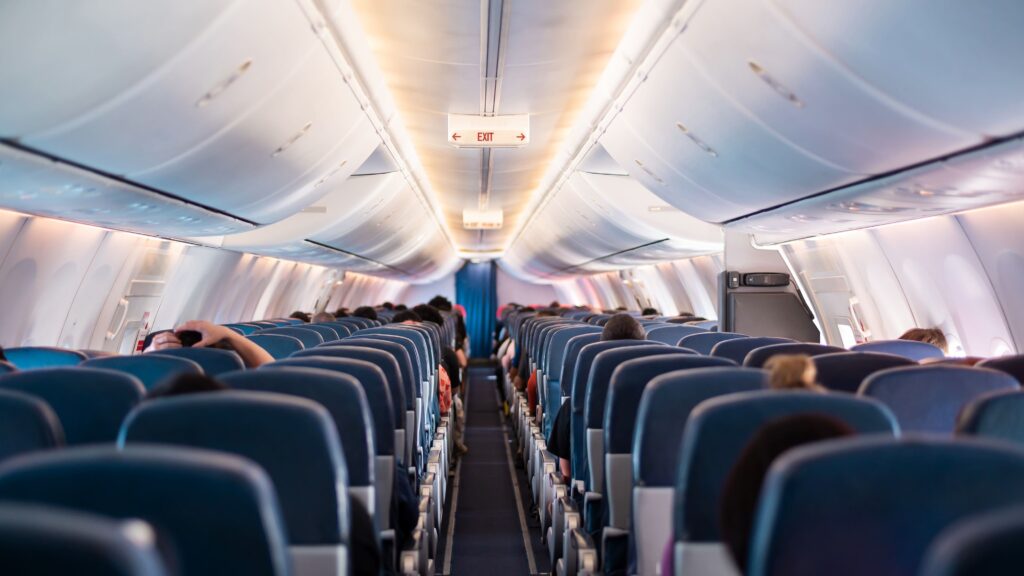
機内の熱風ダクトや窓枠など、耐熱性と難燃性が要求される航空機客室や鉄道車両の内装部品(熱風ダクト、窓枠など)にもPESが利用されています。軽量で自己消火性を持つため、安全性と性能の両立が可能な材料として注目されています。こうした幅広い採用が進む背景には、PESが金属部品に比べ重量や加工コストを大幅に削減しつつ、高い性能と信頼性を確保できる点があります。例えば、金属製部品をPES樹脂に置き換えることで重量を半分以下に削減し、防錆処理が不要になるためメンテナンス工数を削減できた例もあります。さらに、従来の汎用樹脂では満たせない厳しい安全基準(難燃性・耐久性など)をクリアできる素材としてPESが貢献していることも要因でしょう。このようにPESは特定の業界に偏ることなく、さまざまな用途で活躍しています。設計者にとって、要求特性に応じてPESを選択肢に入れることで、製品の信頼性や付加価値を高めることができるでしょう。
当社のPES成形における強み
製品・金型デザインに関するノウハウ
PESは非晶性樹脂でありながらも非常に高い耐熱性と機械的強度を兼ね備えており、設計自由度が高い一方で、成形時の内部応力や部品設計上の微細な肉厚変化が物性や寸法安定性に与える影響が大きい素材です。当社では、過去のPES製品設計・成形実績をもとに、抜き勾配やリブ配置、ゲート位置、肉厚の均一化など、PES特有の特性を踏まえた最適な製品・金型設計を提案しています。とくに寸法精度が求められる小型精密部品や薄肉部品において、設計初期段階からのフィードバックにより、初回トライから仕様を満たす高い品質での立ち上げを可能にしています。
最適な成形条件の設定
PESは射出成形時の溶融温度が330〜380℃と非常に高く、また非晶性であるため、急冷や過度のせん断が寸法変動や内部応力の原因となる場合があります。当社では、加熱プロファイルの細かな温度設定に加え、保圧・冷却時間、型温コントロールを組み合わせたPESに最適化された成形条件を確立しています。とくに金型温度は140〜180℃と高めに設定し、内部応力を最小限に抑える成形を行っています。これにより、反りや歪みの少ない安定した製品供給を実現しています。
アニール処理のノウハウ
PESは非晶性でありながら、高温下での成形応力が製品性能に影響を与えることがあるため、必要に応じてアニール処理(熱時効処理)を行うことがあります。材料メーカーによれば、ガラス繊維強化グレードのウエルド部の強度は、150~180℃のアニール処理により15~20%向上します。当社では、製品形状や用途に応じて、アニール温度や時間を調整するノウハウを持っており、成形応力の除去や耐薬品性・寸法安定性のさらなる向上を図っています。医療機器向けや高温水下での使用が想定される部品については、特にアニール処理を慎重に行っています。
品質保証体制
PESはその用途特性から、高信頼性が求められる分野で使用されることが多く、当社では厳格な品質保証体制を敷いています。非晶性樹脂であるPESは一見すると寸法ばらつきが少ないように思われがちですが、内部応力やゲート位置によってわずかな変形が生じることがあります。当社では三次元測定機による寸法検査、表面観察、さらには吸水変形や加熱変形を想定した環境試験にも対応し、出荷前に高精度かつ高再現性の検査を行っています。さらに、成形条件や材料ロットのトレーサビリティ管理により、不測の事態にも迅速な対応が可能です。
PESと射出成形技術の将来展望
今後、さらなる高性能化や信頼性向上を目的として、PESを含むスーパーエンプラの需要は拡大していくと考えられます。例えば、自動車の電動化に伴い高温環境下で使用される樹脂部品のニーズが増し、パワーエレクトロニクス分野でも高耐熱材料への要求が高まるでしょう。PESはそうした新たな要求に応えうる素材として、今後さらに注目されるかもしれません。それに伴い、射出成形技術も高度化し、新しい加工手法や解析技術の発展によって、PESのような高機能樹脂でもより複雑で精密な成形が可能になるでしょう。また、材料メーカーによるPES樹脂自体の改良(さらなる耐熱性向上や靱性付与など)も期待され、新グレードの開発によって適用範囲は一層広がると考えられます。当社も最新技術を積極的に導入し、これからの市場ニーズに応える体制を強化していく所存です。
まとめ
PESは、耐熱性・強度・耐薬品性・難燃性といった優れた特性を兼ね備え、多岐にわたる分野の製品設計において魅力的な選択肢となる樹脂です。成形加工には高度な技術と設備が要求されますが、適切な対策を講じれば安定した品質の部品を得ることができます。実際に電子機器、自動車、医療機器など幅広い業界で採用が進んでおり、その有用性が実証されています。当社はPES成形に関する知見と経験を活かし、お客様の製品開発を全面的にサポートいたします。高性能材料の選択肢が広がる中、本コラムが、皆様の設計検討においてPESの可能性を見極める一助となれば幸いです。