成形不良を防ぐゲート設計の基本と実践:ウェルド・反り・ヒケを抑える最適解とは?
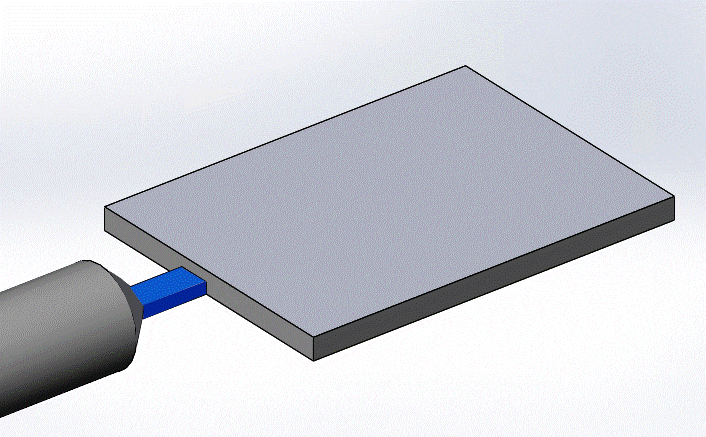
射出成形は、複雑な形状を持つプラスチック部品を効率的に大量生産するための基幹技術です。このプロセスにおいて、最終製品の品質を決定づける重要な要素が「金型」であり、その中でも特に精密な設計が求められるのが「ゲート」です。ゲートとは、溶融した樹脂が金型内の製品形状を形作る空間(キャビティ)へと流れ込む「入口」を指します。このゲートの設計、すなわちゲートの位置、形状、サイズ、数は、製品の外観、強度、寸法精度といった基本的な品質だけでなく、生産性やコストにも直接的な影響を及ぼします。適切なゲート設計は高品質な製品への道筋であり、不適切な設計は多くの成形不良の温床となります。
本記事では、射出成形部品の設計に携わる方を対象に、この重要な「ゲート」について、その基本的な役割から代表的な種類、品質への影響、そして最適なゲートを選定するための考え方まで、設計者が把握しておくべき基礎知識を体系的に解説します。本稿がゲート設計への理解を深め、より良い製品開発に貢献できれば幸いです。
ゲートの基本的な役割と機能
ゲートは単なる樹脂の通り道ではなく、高品質な成形品を実現するために複数の重要な役割を果たしています。
溶融樹脂の通路制御
ゲートはランナーからキャビティへの最終関門であり、通常ランナーより断面積を小さくすることで、キャビティへの樹脂の流入速度や圧力を調整します。また、ゲート通過時のせん断発熱は樹脂の流動性に影響を与えますが、過度なせん断は樹脂劣化の原因となるため注意が必要です。
充填パターンのコントロール
ゲートの位置、数、形状は、キャビティ内での樹脂の流れ方(充填パターン)を決定づけます。これにより、外観不良や強度低下の原因となるウェルドライン(樹脂の合流痕)やフローマーク(流れ模様)の発生位置を制御することが可能になります。
圧の効果的な伝達
成形後の樹脂収縮によるヒケ(凹み)や寸法変化を防ぐ「保圧工程」において、ゲートは圧力をキャビティへ伝える通路となります。ゲートが早期に固化(ゲートシール)すると保圧不足になるため、適切なゲートシールタイムを考慮したサイズ設計が、特に厚肉品や結晶性樹脂では重要です。
キャビティからの逆流防止
保圧完了後、ゲート部が先に固化することで「逆止弁」として機能し、キャビティ内の樹脂がランナー側へ逆流するのを防ぎます。これにより、製品重量や寸法の安定化に寄与します。
成形品とランナーの分離点
成形後、製品本体と不要なランナー部を切り離す際の「分離点」となります。ゲートの形状やサイズは、ゲートカット作業の容易さやゲート跡の品質(大きさ、綺麗さ)に影響します。
適切なゲート設計を怠ると、外観不良、寸法不良、強度不足、成形不良(ショートショット、バリなど)、生産性の低下、コスト増など、様々な問題が発生するリスクがあります。
ゲート設計の基本パラメータ
最適なゲート設計のためには、主に以下の4つのパラメータを製品要求や成形条件に合わせて総合的に検討する必要があります。
ゲート位置
製品のどこにゲートを設けるかは最重要項目です。以下の点を考慮します。
均一充填:樹脂がスムーズに流れ、キャビティ全体に行き渡る位置(通常、厚肉部や中央部付近)。
ウェルドライン制御:外観や強度に影響の少ない箇所へウェルドラインを誘導できる位置。
ガスベント:空気が効率的に排出されるよう、最終充填箇所を考慮した位置。
ゲート跡:外観や機能に影響せず、許容できる位置(裏面、側面など)。
応力集中回避:製品使用時に負荷がかかる箇所や、クラック懸念箇所への直接配置は避ける。
離型性:成形品をスムーズに取り出せる位置。
ゲート数
製品サイズ、形状、要求品質に応じて1点または複数(多点)のゲートを設けます。
多点化の理由:大型・複雑形状での流動距離短縮、充填時間短縮(サイクル向上)、ウェルドライン制御、反り抑制。
注意点:金型構造の複雑化・コスト増、充填バランス調整の難化、ウェルドライン増加の可能性。必要最小限の数にとどめるのが基本。
ゲートサイズ(断面積)
ゲートの幅、厚み(または直径)を指します。決定には多くのトレードオフが存在します。
樹脂流動性:低流動性・高粘度・フィラー入り樹脂ほど大きなサイズが必要。
保圧効果 vs ゲートシール:十分な保圧にはある程度の大きさが必要だが、サイクル短縮には早期シール(小さいサイズ)が有利。
充填速度 vs 圧力損失:高速充填には大きい方が有利だが、圧力損失は増える。
ゲートカット性 vs ゲート跡:カットしやすく跡を小さくするには小さい方が有利。
せん断発熱 vs 樹脂劣化:小さすぎると過度のせん断発熱で樹脂が劣化するリスク。
これらのバランスを考慮し、製品要求を満たす最適なサイズを見つけることが重要です。
ゲート形状
ゲートの断面形状(円形、矩形など)も、樹脂の流れ、応力集中、ゲートカット性、ゲート跡に影響します。詳細は後述のゲート種類で解説します。
これらのパラメータの最適化には、CAE(Computer Aided Engineering)による流動解析が極めて有効です。試作前に充填挙動、ウェルドライン位置、ヒケ・反り傾向などを予測・可視化し、設計段階で問題点を修正することで、開発期間短縮、コスト削減、品質向上に大きく貢献します。
代表的なゲートの種類と特徴
ゲートには多様な種類があり、それぞれにメリット・デメリットが存在します。製品特性に合わせて最適なものを選択することが重要です。
ダイレクトゲート (Direct Gate)
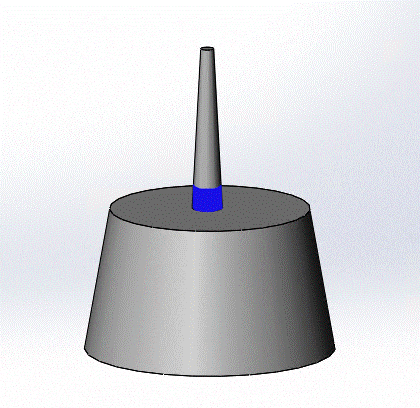
概要:スプルーが直接製品中央部等に接続。最もシンプルな構造(非制限ゲート)。
利点:圧損小、保圧効果大。厚肉品、大型品向き。金型安価。
欠点:ゲート跡大(円錐状)。手動カット必須。応力集中しやすい。
用途バケツ、容器等、ゲート跡が問題にならない製品。
サイドゲート (Side Gate / Edge Gate)
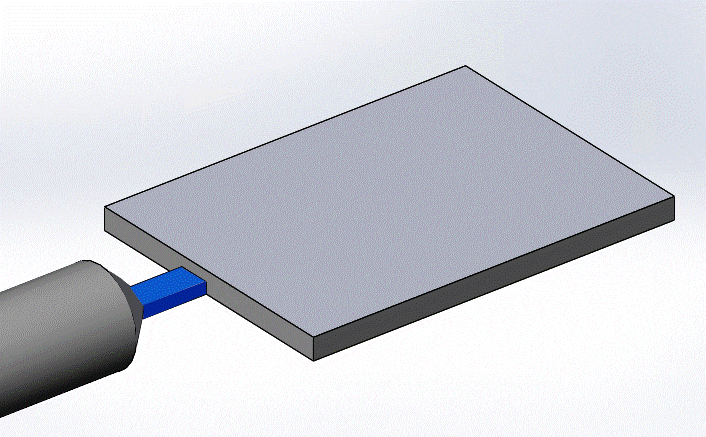
概要:製品側面(パーティングライン上)に設ける最も一般的なゲート(制限ゲート)。
利点:シンプル、安価。多点化容易。汎用性が高い。
欠点:手動カット必須。ゲート跡が側面に残る。ジェッティング懸念。
用途:あらゆる汎用部品(ゲート跡許容時)。
オーバーラップゲート (Overlap Gate)
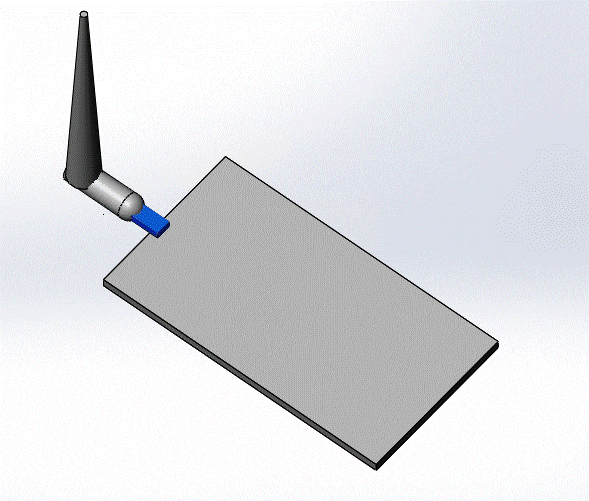
概要:サイドゲートが製品表面/裏面に回り込む形状。
利点:薄板製品の反りやフローマーク抑制に効果的。
欠点:ゲート跡が表面/裏面に残る。手動カット必須。
用途:反りを抑えたい薄板部品、カバー類。
ファンゲート (Fan Gate)
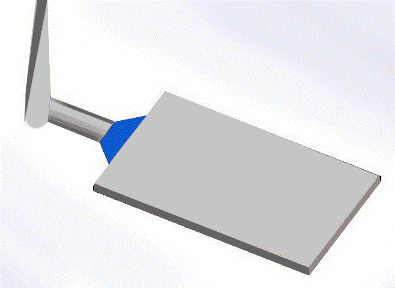
概要:サイドゲート幅を扇状に広げた形状。
利点:均一充填で反り・フローマーク抑制。幅広薄肉品、光学部品向き。
欠点:カット手間大、ゲート跡広い。材料ロス増。
用途:幅広薄肉品、透明部品、レンズ。
フィルムゲート (Film Gate / Flash Gate)
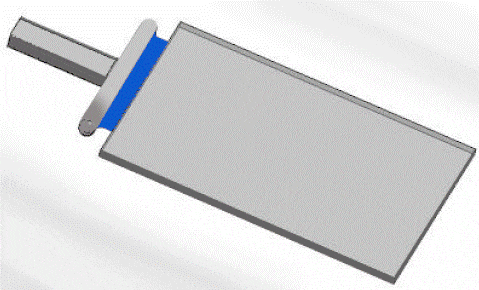
概要:製品の一辺全体に薄い膜状のゲートを設ける。
利点:究極の均一充填で反り・応力最小化。高精度・高外観品に最適。
欠点:カット極めて困難。材料ロス著大。高精度金型要。
用途:導光板、精密シート等。
タブゲート (Tab Gate)
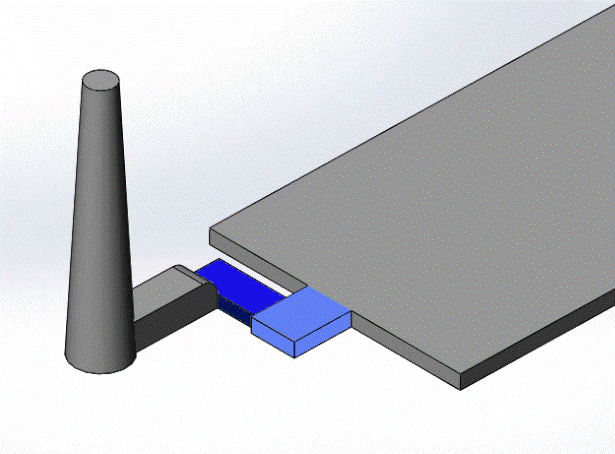
概要:ランナーと製品間に緩衝部(タブ)を設け、そこからゲート接続。
利点:ジェッティング抑制、応力緩和に有効。透明部品向き。
欠点:カット2箇所必要。材料ロス増。
用途:透明カバー、応力割れ懸念部品。
ピンポイントゲート (Pinpoint Gate)
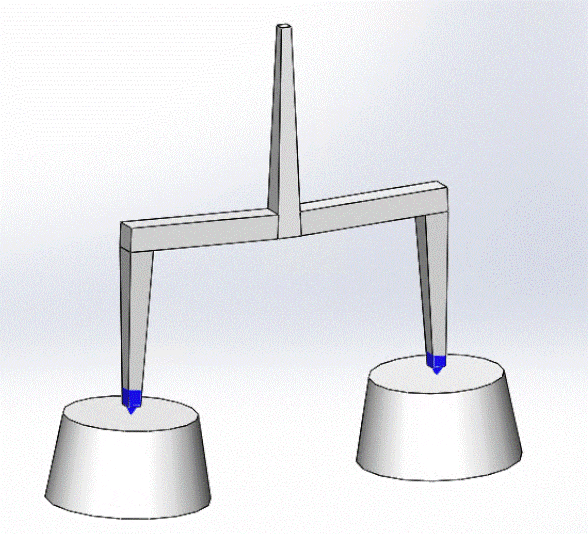
概要:製品表面/裏面に設ける微小な点状ゲート。通常3プレート金型要。
利点:ゲート跡極小。自動カット可(金型内)。多点化容易、位置自由度高。
欠点:圧損大、充填性劣る。詰まりやすい。保圧効果低。金型高価。
用途:小型精密品、外観重視部品。
サブマリンゲート (Submarine Gate / Tunnel Gate)
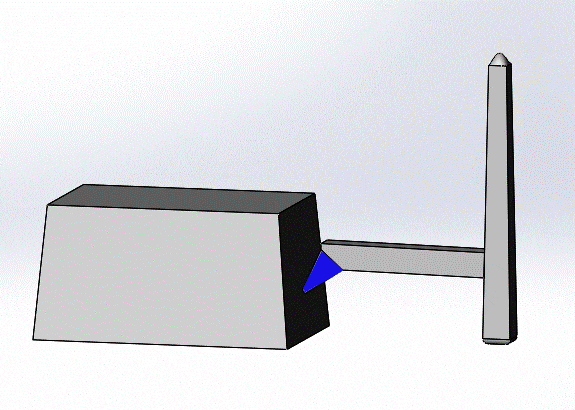
概要:金型内部から製品側面/裏面にトンネル状に設ける。自動カットゲートの代表。
利点:ゲートカット不要で自動化に最適。ゲート跡が目立たない。
欠点:圧損大。金型複雑・高価。カット不良や応力集中のリスク。
用途:大量生産品、自動化ライン部品、外観部品。
カーブドトンネルゲート (Curved Tunnel Gate / Banana Gate)
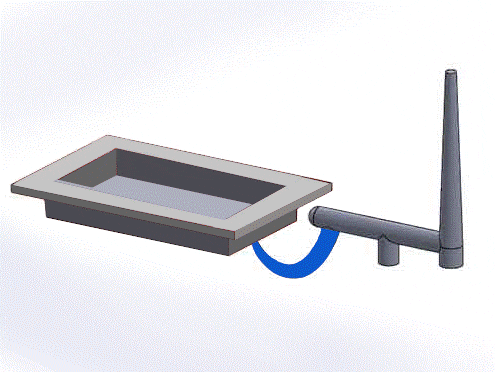
概要:サブマリンゲートのトンネル部が湾曲した形状。
利点:ゲート位置自由度極高。意匠面の裏側等に設定可能。自動カット。
欠点:圧損極大。金型超高価・複雑。リスクも高い。
用途:高意匠性が最優先される製品(スマホ筐体等)。
ホットランナーシステムのゲート
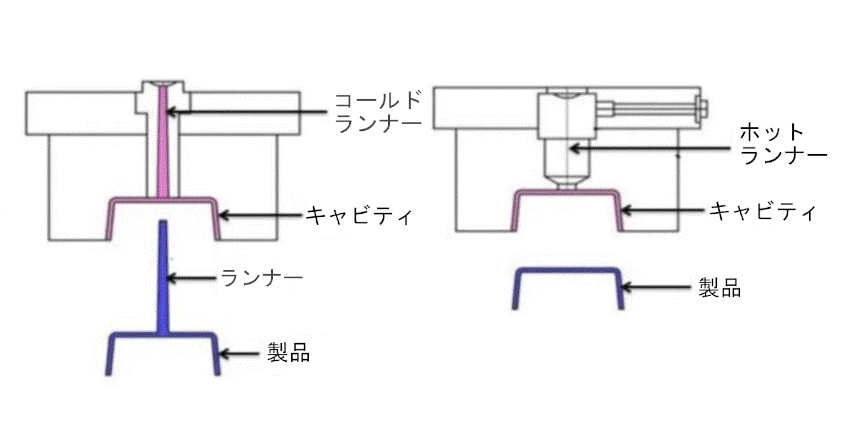
概要:ランナー部を加熱し樹脂を常に溶融状態に保つシステム。材料ロス無し、ハイサイクル化が可能。
利点: 材料費削減、サイクル短縮、圧損小、保圧効果高、ゲート位置自由度高。
欠点:初期投資(金型+システム費)が非常に高価。温度制御・メンテが複雑。
主なゲートタイプ
・バルブゲート:開閉ピンでゲートを精密制御。ゲート跡極小・高品質。最も高価だが最高品質。ウェルド制御やシーケンシャル充填も可能。
・オープンゲート:単純な開口部。構造は比較的シンプルだが、ゲート跡残りや糸引き懸念あり。
・適用:大量生産、大型品、ハイサイクル、高価な樹脂などに有効。
最適なゲートを選定するための考え方と実践フロー
多様なゲートから最適解を選ぶには、論理的なプロセスが必要です。
選定基準の明確化
製品に求められる品質(外観、寸法、強度)、コスト(金型、成形、材料、後加工)、生産性(サイクル、自動化)、製品特性(形状、材質)、生産数量を洗い出し、優先順位を明確にします。「必須条件」「重要条件」「推奨条件」のように重み付けすると判断しやすくなります。
ゲート選定の実践フロー(例)
1.情報収集・要件定義:図面、仕様、樹脂データを確認。
2.位置・数の初期検討:要求に基づき候補を検討。
3.候補ゲートタイプの洗い出し:選定基準(カット要否、ゲート跡、コスト等)から候補を絞る。
4.比較・評価と絞り込: 候補の利点・欠点を要求と照らし合わせ、最適な方式に絞る(トレードオフ考慮)。
5.詳細設計とCAE検: ゲートサイズ等を設計し、CAE解析で充填性、ウェルド、反り等を検証・最適化。
6.最終決定と仕様化:解析結果、実績、専門家の意見を踏まえ、最終仕様を決定し図示。
設計者として留意すべき点
固定観念にとらわれず、常に製品要求に立ち返り、論理的な根拠を持ってゲートを選定することが重要です。品質・コスト・生産性のトレードオフを理解し、バランスの取れた判断が求められます。そして、設計初期段階から成形・金型の専門家と連携することが成功の鍵です。設計意図を正確に伝え、専門的なアドバイスを積極的に取り入れましょう。
ゲートカット処理
手動カットが必要なゲートでは、その処理品質も製品価値を左右します。
手動カットの方法と注意点
ニッパーやカッター等を使用。手軽ですが、作業者スキルによるばらつき、作業時間、安全管理が課題。製品損傷、バリ、白化、クラックを防ぐ配慮が必要です。設計段階でカットしやすい形状・サイズを考慮することが望ましいです。
自動カット(金型内カット)のメリットと留意点
サブマリンゲート等は自動カットにより効率化・コスト削減・品質安定化を実現。ただし、金型が複雑・高価になる点、カット不良リスク、金型メンテナンスの重要性に留意が必要です。
ゲート跡の仕上げ
外観部品では、ゲートカット後の跡処理(ヤスリがけ、研磨等)が必要な場合があります。これは追加コストとなるため、設計段階で跡が目立たない位置への配置や、仕上げが容易なゲート形状を検討することが重要です。
まとめ:最適なゲート設計が、高品質な射出成形品を生み出す
ゲートは、射出成形品の品質、コスト、生産性のすべてに影響を与える極めて重要な設計要素です。各ゲート方式の特性を深く理解し、製品の要求仕様、使用樹脂、金型構造、成形条件などを総合的に考慮して、明確な根拠に基づき最適な種類と仕様(位置、数、サイズ、形状)を選定・設計することが不可欠です。
本記事で解説した基礎知識が、皆様のゲート設計における判断の一助となり、より良い製品開発に繋がることを願っています。しかし、ゲート設計は経験とノウハウが求められる奥深い分野です。判断に迷う場合や、より高度な要求がある場合は、決して設計者だけで抱え込まず、射出成形および金型に関する豊富な経験と知識を持つ専門家にご相談ください。
ゲート設計に関するお悩み、より具体的な技術相談、試作から量産までのご依頼は、ぜひ私たち府中プラへお気軽にお問い合わせください。経験豊富な技術スタッフが、お客様の課題解決に向けて最適なソリューションをご提案させていただきます。