迫るPFAS規制:射出成形部品への影響と代替戦略(前編)
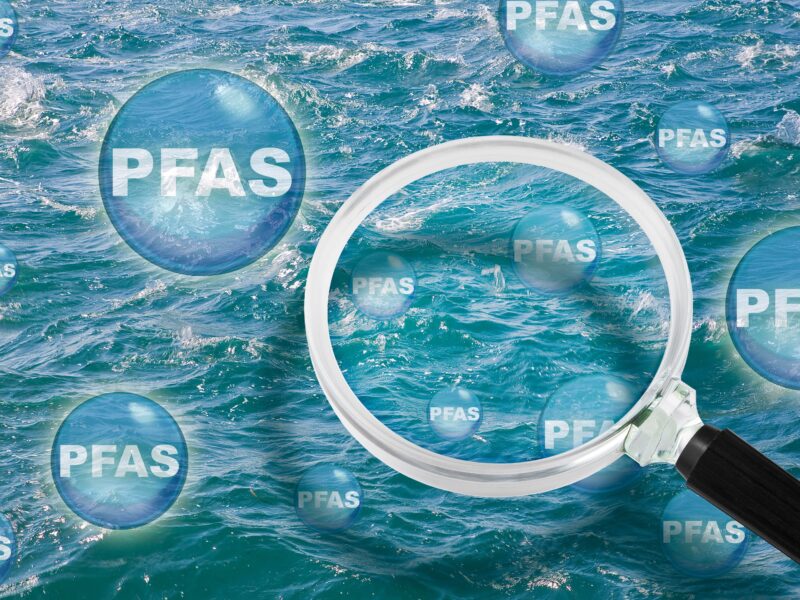
近年、「PFAS(ピーファス)」という言葉を耳にする機会が増えています。PFASは、パーフルオロアルキル化合物及びポリフルオロアルキル化合物の総称であり、そのユニークな特性から多くの工業製品に利用されてきました。しかし、その環境中での残留性や人の健康への影響が懸念され、世界的に規制を強化する動きが急速に進んでいます。
私たち射出成形業界においても、PFASはフッ素樹脂をはじめとする高機能材料や、成形プロセスを助ける添加剤として重要な役割を果たしてきました。そのため、PFAS規制の強化は、製品設計や材料選定、サプライチェーン管理、そしてコスト構造に至るまで、広範囲にわたる影響を及ぼす可能性があり、設計担当者の皆様にとっては避けて通れない課題となっています。
本コラムでは、射出成形部品の設計に携わる皆様を対象に、PFAS規制の最新動向、それがもたらす具体的な影響、そして有望な代替材料や技術に関する情報を網羅的に解説します。PFAS規制という大きな変化の波を乗り越え、持続可能な製品開発を進めるための一助となれば幸いです。前編では、まずPFASの基本的な概要と射出成形における役割、そして世界と日本における規制の最新動向、さらに規制強化が設計や材料選定に与える直接的な影響について解説します。
PFASの化学的定義と特異な物性
まず、規制の対象となっているPFASとはどのような物質なのか、基本的な知識と射出成形分野での使われ方を確認しましょう。PFASは、分子内に極めて安定した「炭素-フッ素結合(C-F結合)」を複数持つ有機化合物の総称です。このC-F結合は非常に強力であるため、PFASは熱や化学薬品に対して優れた安定性を示します。また、フッ素原子の特性により、低摩擦性(滑りやすさ)、撥水・撥油性(水や油をはじく)、高い電気絶縁性といった多様な機能を発揮します。これらのユニークな物性の組み合わせが、PFASを多くの産業分野で「なくてはならない」材料たらしめてきた理由です。
射出成形分野で主に利用されるPFAS
射出成形分野では、PFASは主に以下の形で利用されています。
フッ素樹脂(フルオロポリマー)
PTFE(ポリテトラフルオロエチレン)
「テフロン®」という商標で広く知られています。極めて優れた低摩擦性、耐薬品性、耐熱性を持ちますが、溶融しないため一般的な射出成形は困難です。主に圧縮成形などで部品化され、摺動部品、シール材、パッキンなどに使われます。他のフッ素樹脂と比較する上で重要な材料です。
PFA(パーフルオロアルコキシアルカン)/ FEP(フッ化エチレンプロピレン)
PTFEに近い優れた特性を持ちながら、溶融するため射出成形が可能です。高い純度や耐薬品性、耐熱性が要求される半導体製造装置の部品(継手、バルブ、ポンプ部品)、薬液用チューブ、耐食性が求められる化学プラント部品、医療機器部品などに広く利用されています。
ETFE(エチレン-テトラフルオロエチレン共重合体)
PTFEやPFA/FEPより機械的強度や耐候性に優れます。射出成形も可能ですが、電線被覆やフィルム用途が主で、射出成形部品としての利用は限定的です。比較対象として特性を理解しておくことは有益です。
PVDF(ポリフッ化ビニリデン)
フッ素樹脂の中では機械的強度が高く、耐候性にも優れます。また、圧電性という特異な性質も持ちます。ポンプ、バルブ、配管部品、センサーハウジング、医療機器部品などに射出成形品として利用されます。リチウムイオン電池のバインダーとしての用途も知られています。
フッ素系加工助剤(PPA – Polymer Processing Aids)
主にPE(ポリエチレン)やPP(ポリプロピレン)などのポリオレフィンを射出成形する際に、ごく少量(数百~千ppm程度)添加されるフッ素系のポリマーです。成形時に金型表面に薄い層を形成し、メルトフラクチャー(溶融樹脂表面の荒れ)を防止したり、樹脂の流動性を向上させたり、金型の汚れを低減したりする効果があります。製品性能に直接寄与するわけではありませんが、安定した生産に貢献しています。これらのPPAもPFAS規制の対象となる可能性があり、非含有グレードへの関心が高まっています。
その他の含有可能性
上記以外にも、特定の機能を持たせるための添加剤や、成形プロセスで使用される離型剤、あるいは材料合成時の副生成物として、製品中に微量のPFASが含まれる可能性もゼロではありません。サプライチェーン全体での情報管理が重要になる所以です。
世界と日本のPFAS規制 最前線 ~設計担当者が把握すべきポイント~
PFASに対する規制は、なぜこれほど急速に進んでいるのでしょうか。その背景と、設計担当者が特に注意すべき規制の最新動向を見ていきましょう。
規制強化の背景
PFASの中でも特にPFOA(ペルフルオロオクタン酸)やPFOS(ペルフルオロオクタンスルホン酸)は、環境中で分解されにくく、生物の体内に蓄積しやすい性質(難分解性・高蓄積性)が問題視されてきました。これらが広範囲の環境(水、土壌)や生物、さらには人の血液からも検出され、健康への影響(発がん性、免疫毒性、発達への影響など)が懸念されるようになったことが、規制強化の大きな背景です。当初はPFOA/PFOSが主な対象でしたが、類似の構造を持つ多数のPFASについても同様の懸念があるとして、より広範なPFASを規制しようという動きが国際的に広がっています。
国際的な枠組み
残留性有機汚染物質に関するストックホルム条約(POPs条約)は、国際的な化学物質規制の重要な枠組みです。この条約では、PFOS(2009年)、PFOA(2019年)、そしてPFHxS(ペルフルオロヘキサンスルホン酸、2022年)とその関連物質が、製造・使用・輸出入を原則禁止または厳しく制限する対象として追加されました。今後、さらに多くのPFASが規制対象として検討される可能性があります。
EU REACH規則「Universal PFAS Restriction Proposal」
現在、射出成形業界を含む多くの産業界が最も注目しているのが、EUの化学物質規制であるREACH規則の下で進められているPFASの包括的な制限提案です。2023年1月に欧州化学品庁(ECHA)から公表されたこの提案は、「Universal PFAS Restriction Proposal」と呼ばれ、約1万種類ともいわれる広範なPFASを対象としています。提案の骨子は、特定の適用除外を除き、PFAS自体の製造、上市(市場への投入)、そして「使用」を原則禁止するという、非常に厳しいものです。現在、この提案はECHAの科学委員会(リスク評価委員会RAC、社会経済分析委員会SEAC)による評価が進められており、多数の意見が提出されています。最終的な規制内容は、これらの評価や意見を踏まえ、欧州委員会での審議を経て決定されますが、早ければ2025年頃から段階的に施行される可能性が指摘されています。
設計担当者にとって特に重要なのは、「使用」が禁止対象に含まれる点です。これは、PFASを含む部品をEU域内で製造することだけでなく、EU域外で製造されたPFAS含有部品を輸入してEU域内の製品に組み込むことも制限される可能性があることを意味します。サプライヤーがEU域外であっても、EU市場向けの製品に関わる場合は対応が必須となります。
一方で、社会的に必須であり代替が困難な特定の用途(半導体製造プロセス、特定の医療機器、安全保障関連など)については、適用除外(Derogation)が申請・議論されています。フッ素ポリマーそのものの扱いについても議論が続いていますが、仮に除外が認められたとしても、その多くは期限付き(例えば5年や12年)となる可能性が高く、恒久的な解決策とはなりません。
また、製品中のPFAS含有に関する情報伝達義務も強化される見込みです。サプライチェーンの上流から下流まで、製品にどのPFASがどれだけ含まれているか(あるいは含まれていないか)を正確に把握し、伝達する仕組みの構築が急務となります。閾値(規制対象となる含有濃度)の設定についても議論が行われています。
米国(連邦・州)の動向
米国でもPFAS規制は強化の方向にあります。連邦レベルでは、環境保護庁(EPA)が飲料水中のPFAS濃度基準の設定や、有害物質排出目録(TRI)へのPFAS追加、スーパーファンド法(CERCLA)に基づく有害物質指定などを進めています。また、州レベルでの動きも活発で、特にメイン州やカリフォルニア州などでは、特定の製品カテゴリー(食品包装、繊維製品など)におけるPFASの意図的な添加を禁止する法律が既に施行・計画されており、今後、対象製品が拡大する可能性もあります。
日本(化審法・関連法規)の状況
日本においても、化学物質の審査及び製造等の規制に関する法律(化審法)に基づき、2023年までにPFOS、PFOA、PFHxSとその塩、関連化合物が第一種特定化学物質に指定され、製造・輸入・使用が原則禁止となりました。EUの包括的な規制提案の動向などを注視しつつ、今後、国内でもさらなるPFAS規制が導入・強化される可能性は十分に考えられます。
規制動向の不確実性
このように、PFAS規制は世界各地で急速に、かつ複雑に進展しています。特にEUの包括的制限提案の最終的な内容や施行時期、適用除外の範囲などはまだ流動的な部分もあります。設計担当者の皆様には、常に最新の規制情報を入手し、自社製品への影響を評価し続けることが求められます。
設計・材料選定への直接的インパクト ~ PFAS規制がもたらす課題 ~
これらの規制強化は、射出成形部品の設計や材料選定に具体的にどのような影響をもたらすのでしょうか。主な課題を4つの側面に分けて整理します。
影響1 – 材料の選択肢制限とサプライチェーンリスク
最も直接的な影響は、これまで使用してきたPFAS含有材料の入手が困難になる、あるいは不可能になるリスクです。特に汎用的なフッ素樹脂グレードや、PFASを含む特定の添加剤を使用したコンパウンド(例えばPPA含有ポリオレフィンなど)は、供給停止や大幅な価格高騰に見舞われる可能性があります。サプライヤーに対して、使用している材料や部品にPFASが含まれていないか、含まれている場合はどの種類のPFASがどれだけ含まれているかを確認し、非含有証明書などを入手する必要性が高まります。しかし、サプライチェーンが複雑な場合、上流まで遡って正確な情報を得ることは容易ではありません。chemSHERPAの活用などが重要になりますが、情報の入手・管理には多大な労力がかかります。
影響2 – 既存製品の設計変更・再評価の必須化
現在PFASを使用している部品については、代替材料を用いた設計変更が避けられなくなる可能性があります。まずは、自社製品のどの部品、どの材料、どの添加剤にPFASが使われているかを正確に特定し、規制対象となるリスクを評価する必要があります。代替材料を選定した後は、その材料で従来の製品と同等の性能や機能が維持できるか、多角的な検証が必須です。機械的強度、耐熱性、耐薬品性、摺動特性、電気特性、寸法安定性、耐候性、そして長期的な信頼性(寿命)など、要求される特性は多岐にわたります。これらの評価には、多くの時間とコスト(試験費用、試作費用など)がかかります。さらに、使用材料を変更した場合、UL規格、FDA(米国食品医薬品局)認証、その他業界固有の規格や顧客要求仕様を満たすために、製品認証の再取得が必要になるケースも考えられます。
影響3 – コスト構造の変化
PFAS規制への対応は、様々なコスト増をもたらします。一般的に、PFAS代替となる高性能な材料は、従来のPFAS材料よりも高価であることが多くなっています。代替材料の調査・開発費用、性能評価・試験費用、場合によっては、収縮率の違いに対応するため金型修正や新規製作費用、射出成形条件の最適化など製造プロセス変更に伴う費用も発生します。
これらの直接的なコストに加え、規制対応が遅れた場合には、市場からの要求に応えられずにビジネスチャンスを失うリスク(機会損失)も考慮する必要があります。一方で、早期に対応し、PFASフリー製品を市場に投入できれば、それが新たな競争優位性につながる可能性もあります。短期的なコストだけでなく、中長期的な視点での費用対効果の判断が求められます。
影響4 – 技術的ハードルの克服
代替材料は、PFAS材料とは異なる物性や加工特性を持っています。例えば、溶融粘度、流動長、成形収縮率、ガス発生量、適切な金型温度などが異なるため、従来の射出成形条件や金型がそのまま使えない場合があります。安定した品質で量産するためには、成形技術の最適化や、場合によっては金型設計の見直しが必要になります。特に、PTFEが持つ極めて低い摩擦係数や、PFA/FEPが持つ広範な耐薬品性、特定のフッ素樹脂が持つ優れた高周波特性など、PFASならではの突出した性能が求められる用途では、同等の性能を持つ非PFAS材料を見つけることが技術的に非常に困難な場合があります。また、これまで実績のあるPFAS材料から新しい代替材料に変更することで、予期せぬ問題が発生する可能性も考慮する必要があります。例えば、異なる種類の材料を組み合わせることで、接触部分に電位差が生じて腐食(電蝕)が起きたり、熱膨張率の違いから応力集中が発生したりする可能性など、材料単体の評価だけでは見えてこない課題にも注意が必要です。