迫るPFAS規制:射出成形部品への影響と代替戦略(後編)
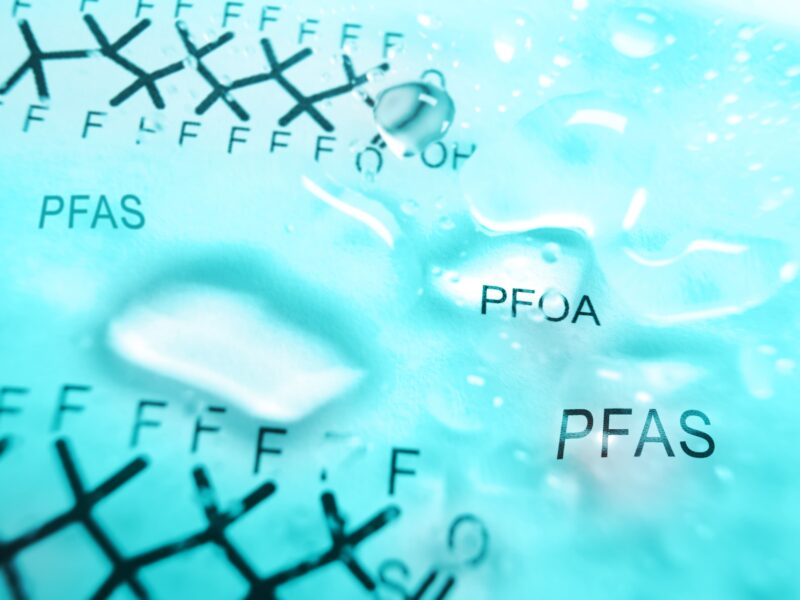
本コラムは、PFAS(有機フッ素化合物)規制が射出成形部品の設計・材料選定に与える影響と、その対応策について解説しています。前編では、PFASの基本的な概要、射出成形における役割、そして世界と日本における規制の最新動向、さらに規制強化がもたらす具体的な課題(材料選択肢の制限、設計変更の必要性、コスト増、技術的ハードル)について述べました。後編では、これらの課題を踏まえ、具体的なPFAS代替技術や材料の選択肢、代替材料を選定・導入する上でのチェックポイント、そして最後に私たちからのメッセージをお伝えします。
PFAS代替技術の最前線 ~ 設計担当者のための材料選択ガイド ~
PFAS規制という大きな課題に対し、どのような代替材料や技術が検討されているのでしょうか。ここでは、設計担当者の皆様が代替材料を選定する上での考え方と具体的な材料の選択肢について解説します。
代替検討の基本戦略
PFASからの代替を検討する際には、まず、「本当にその部品にPFASレベルの高性能が必要なのか?」を問い直すことが重要です。これまでの設計を踏襲しているだけで、現状の要求仕様に対してオーバースペックになっている可能性はないでしょうか。要求性能を必要最低限まで見直し、再定義することで、より安価で入手しやすい非PFAS材料が選択肢に入る可能性があります。また、これまで単一のPFAS材料で複数の機能(例:耐薬品性と摺動性)を賄っていた場合、その機能を分離して考えるというアプローチも有効です。例えば、摺動性は表面コーティングで付与し、母材には耐薬品性に優れた別の非PFAS材料を選ぶ、といった具合です。これにより、最適な材料の組み合わせが見つかるかもしれません。
スーパーエンプラによる代替
PFAS(特にフッ素樹脂)の代替として、まず検討されるのが、PEEKやPPSといった高性能なエンプラやスーパーエンプラです。これらは、非PFASでありながら高い性能を持っています。
PEEK
材料特性:連続使用温度が260℃クラスと極めて高い耐熱性を持ちます。濃硫酸などの一部の強酸を除き、広範な薬品に対して優れた耐性を示します。高い機械的強度、耐摩耗性、耐加水分解性(高温水中でも物性が劣化しにくい)、低アウトガス性(真空環境下でのガス放出が少ない)なども特徴です。
代替用途例:高い耐熱性、耐薬品性、純度が求められる半導体やFPDの製造装置部品(ウェハーキャリア、洗浄槽部品、リングなど)。軽量化と高信頼性が求められる航空宇宙分野の部品(参考)。生体適合性を持つグレードもあり、医療機器(手術器具、インプラント関連)にも使用されます。耐摩耗性や耐熱性が要求される産業機械の部品(ギア、軸受、シールリング)など、幅広い分野でPFAやPTFEの代替候補となります。
主要グレード:未強化の標準グレードのほか、摺動性を向上させたグレード(炭素繊維、グラファイト、あるいは非PFAS系の固体潤滑剤などを配合)、ガラス繊維などで機械強度を高めた強化グレード、静電気対策用の導電性グレードなど、用途に応じた多様なグレードがあります。(摺動グレードの中にはPTFE配合品も存在するため、PFASフリーを確認する際は注意が必要です)。
代替のポイント:PFA/FEP/PTFEの代替として非常に有力ですが、一般的に材料コストが高い点が課題です。また、摺動性に関しては、PTFEの自己潤滑性には及ばない場合が多いため、摺動グレードの適切な選定や相手材との組み合わせ検討が重要です。射出成形には高温(シリンダー温度350~400℃、金型温度150~200℃)が必要であり、高度な成形技術が求められます。
PPS
材料特性:連続使用温度が200~240℃クラスと高い耐熱性を持ちます。200℃以下の環境では、ほとんどの有機溶剤や薬品に対して優れた耐性を示します。寸法安定性が非常に高く、吸水性も極めて低いため、精密な部品に適しています。また、難燃剤を添加しなくても高い難燃性(UL94 V-0相当)を示すことも大きな特徴です。溶融時の流動性が高く、薄肉複雑形状の成形も比較的容易です。
代替用途例:高い耐熱性、寸法安定性、難燃性が求められる電気電子部品(コネクタ、スイッチ、ボビン、センサーハウジングなど)。耐薬品性と耐熱性が要求される住設機器や産業機械の部品(ポンプケーシング、バルブ、インペラーなど)。PFA、FEP、ETFEなどの代替として、コストと性能のバランスが求められる場合に有力な選択肢となります。
主要グレード:ガラス繊維で強化されたグレードが標準的ですが、より高い強度や靭性を持つグレード、成形時のバリ発生を抑制した低バリグレード、摺動性を付与したグレードなどがあります。
代替のポイント:PEEKと比較すると安価で、射出成形性も良好です。しかし、PEEKに比べると耐熱性や靭性(衝撃強度)、一部の薬品(特に高温の酸化性薬品)に対する耐性は劣る場合があります。用途の要求レベルに応じて使い分けることが重要です。
PEI
材料特性:連続使用温度が170℃クラスの非晶性スーパーエンプラです。琥珀色で透明性があり、高い強度と剛性、優れた寸法安定性を持ちます。幅広い温度域で安定した電気特性(高い絶縁破壊強度、低い誘電損失)を示し、耐加水分解性にも優れるため、スチーム滅菌などにも耐えられます。耐放射線性も良好です。
代替用途例:高い寸法精度と耐熱性が求められる電気電子部品(高密度コネクタ、ICソケット、基板部品など)。繰り返し滅菌が必要な医療機器(手術器具トレイ、コネクタなど)。食品加工機械の部品。
代替のポイント:透明性が必要な場合や、高温環境下での優れた電気特性が要求される場合に、PFAや他の耐熱樹脂の代替として検討されます。
LCP(液晶ポリマー)
極めて低い誘電率・誘電正接を持ち、高周波特性に優れるため、5G/6G通信関連のコネクタやアンテナ部品などで、フッ素樹脂の代替として注目されています。流動性が非常に高く、薄肉精密成形に適しますが、異方性(流れ方向と垂直方向で物性が異なる)が大きい点に注意が必要です。
汎用エンプラ・その他材料による代替
要求性能によっては、より汎用的なエンプラや他の材料も代替候補となりえます。
変性PPE、PA、PBT
難燃性が要求される電気電子部品などに広く使われています。従来、難燃剤としてハロゲン系(臭素系など)が使われることがありましたが、環境規制の流れから非ハロゲン化が進んでいます。PFAS規制とは直接関係ありませんが、難燃剤の種類によっては、PFASを含まないリン系、窒素系、金属水酸化物系などが採用されています。ただし、難燃剤の種類によって物性(機械強度、耐熱性、吸湿性など)や成形性が変化するため、注意が必要です。
UHMWPE(超高分子量ポリエチレン)
非常に高い耐摩耗性と自己潤滑性を持ち、PTFEの代替として摺動部品などに使われることがあります。比較的安価ですが、耐熱性や耐クリープ性(荷重下での変形しにくさ)はPTFEに劣ります。また、溶融粘度が高いため、射出成形が可能なグレードは限定的です。
シリコーン
ゴム弾性を持ち、耐熱性、耐寒性、耐候性に優れるため、シール材やガスケットとしてフッ素ゴム(FKM、これもPFASの一種)やPTFEの代替となる場合があります。射出成形可能なグレード(LSR:液状シリコーンゴム)もありますが、耐薬品性(特に溶剤)や機械的強度はフッ素樹脂に劣る場合があります。
フッ素系加工助剤(PPA)の代替
ポリオレフィンなどの射出成形時に使用されるPPAについては、PFAS規制を見越して、非フッ素系の加工助剤(シリコーン系、特殊アクリル系など)の開発が進められています。また、PPAを使用しなくても良好な成形性を実現できるようなコンパウンド技術(樹脂改質、添加剤配合)や、金型表面処理技術、成形条件の最適化なども代替アプローチとして検討されています。
最難関 ~ PTFEの「超低摩擦性」代替への挑戦 ~
PFAS代替において、技術的に最もハードルが高いとされるのが、PTFEが持つ極めて低い摩擦係数(自己潤滑性)を、非PFAS材料で実現することです。完全な代替は難しい場合も多いですが、以下のようなアプローチが考えられます。
摺動グレードPEEK/PPS
前述の通り、炭素繊維、グラファイト、二硫化モリブデンといった非PFAS系の固体潤滑剤を配合することで、摩擦・摩耗特性を改善したグレードが開発されています。しかし、PTFEのレベルには達しないケースも多く、相手材との組み合わせや使用環境(温度、速度、面圧など)による性能変化も考慮する必要があります。
自己潤滑性を持つ特殊ポリマー
ポリアミドやポリオレフィンの中にも、分子構造レベルで自己潤滑性を付与した特殊な射出成形グレードが存在します。これらは特定の用途でPTFE代替として実績がある場合もありますが、耐熱性や耐薬品性はPTFEに劣ることが多いです。
表面改質技術(二次加工)
射出成形した部品の表面に、低摩擦なコーティング(例:DLC(ダイヤモンドライクカーボン)コーティング、非フッ素系の潤滑コーティングなど)を施す方法です。母材の特性と表面の摺動性を両立できますが、コーティングの密着性や耐久性、コストが課題となります。プラズマ処理などで表面の性質を改質する方法もあります。
設計的アプローチ
材料だけで解決しようとせず、設計面での工夫も重要です。摺動する相手材の材質や表面粗さを見直す、潤滑油やグリースを併用する(ただし、使用環境によっては不可)、非接触シール構造を採用するなど、部品やシステム全体での最適化を図ります。
具体的な業界・用途別 代替検討事例
代替材料の検討は、具体的な用途や要求性能によって大きく異なります。例えば、以下のような検討事例が考えられます。
事例1 – 半導体製造装置のOリング/シール
PFAの高い純度と耐薬品性が求められるが、より高温への対応やアウトガス低減のため、高純度PEEKやPPSへの代替が検討されるケース。
事例2 – 産業機械の摺動ブッシュ/ワッシャー
従来PTFE充填POMやPAが使われていた箇所で、より高い耐熱性や耐荷重性が求められる場合に、PEEKやPPSの摺動グレードへの代替が検討されるケース。
事例3 – 食品・医療機器のシール/ガスケット
PTFEの化学的安定性や低溶出性が求められるが、コストや弾力性の観点から、特殊シリコーンや(射出成形可能な)UHMWPEグレードへの代替が検討されるケース。
事例4 – 化学プラント等のポンプ/バルブ部品
PVDFやPFAの耐薬品性が必須であったが、特定の薬液に対してはPEEKやPPSでも対応可能であり、コストや機械強度面から代替が検討されるケース。
代替材料の選定・導入を成功させるためのチェックポイント
PFAS代替材料の選定と導入は、慎重に進める必要があります。ここでは、設計担当者の皆様が留意すべきチェックポイントを挙げます。
要求性能の再評価と優先順位付け
前述の通り、まずはその部品に本当に必要な性能は何かを改めて明確にします。「絶対に譲れない要件(Must)」と「できれば満たしたい要件(Want)」を切り分け、優先順位をつけます。これにより、代替材料の選択肢を絞り込みやすくなります。
長期信頼性評価の重要性
カタログスペックや短期的な試験結果だけでは、実際の使用環境における長期的な性能は分かりません。特に、熱、薬品、応力、摩耗などが複合的に作用する環境下での耐久性や、経年劣化については、実機に近い条件での長期評価が不可欠です。加速試験なども活用し、製品寿命全体を見据えた信頼性を確認します。
射出成形性の事前検証
選定した代替材料が、既存の金型や設備で問題なく成形できるか、事前に検証することが重要です。材料メーカーから提供される流動解析データなどを参考にしつつ、可能であれば試作成形を行い、最適な成形条件(温度、圧力、速度、保圧、冷却時間など)を見つけ出します。収縮率の違いによる寸法変化、ガス発生の有無と対策、金型温度制御の必要性なども確認します。
サプライヤーとの密な連携
材料メーカーやコンパウンドメーカーは、代替材料に関する最新の情報や技術データを持っています。積極的に情報交換を行い、技術的なサポートを得ることが成功の鍵です。また、PFAS非含有であることの証明や、将来にわたる安定供給体制についても、サプライヤーに確認しておく必要があります。
トータルコストでの比較検討
材料単価だけでなく、開発・評価にかかる費用、金型修正や設備投資の費用、成形サイクルや不良率の変化による製造コストへの影響、品質保証体制の構築コスト、さらには将来的な廃棄・リサイクルコストまで含めた「トータルコスト」で比較検討することが重要です。
複合的な視点での最適化
PFAS代替は、単に材料を置き換えるだけではうまくいかない場合もあります。材料の特性に合わせて、部品の設計(形状、肉厚、リブ構造など)や、射出成形プロセス全体(金型設計、成形条件、後処理など)を見直し、複合的な視点で最適化を図ることが求められます。
まとめ
PFAS規制の捉え方
PFASに対する規制強化は、もはや避けられない世界的な潮流であり、射出成形業界にとっても重要な転換点と言えます。短期的に見れば、設計変更やコスト増など、多くの課題をもたらすことは事実です。しかし、これは同時に、より安全で持続可能な製品開発へと舵を切り、新たな技術革新を促進する機会でもあります。
代替技術の現状
本コラムで見てきたように、PFAS代替技術や材料の開発は日々進歩しています。高性能エンプラやスーパーエンプラを中心に、様々な選択肢が登場しています。しかし、あらゆる用途に対応できる万能な代替材料は存在しません。それぞれの材料の長所・短所を正確に理解し、製品の要求性能やコスト、製造プロセスなどを総合的に考慮して、最適なものを選び抜くことが鍵となります。
当社の強みと提供価値
当社は、長年にわたり精密射出成形に携わり、汎用エンプラからスーパーエンプラに至るまで、多種多様な樹脂材料に関する深い知見と、高度な成形技術を培ってまいりました。この経験に基づき、PFASフリー材料を含む幅広い選択肢の中から、お客様の製品に求められる性能、コスト、そして量産時の成形性までをも満たす最適な材料をご提案できる知見が当社の強みです。
また、国内外の主要な材料メーカーとの強固なネットワークを活かし、最新の材料情報の提供や、時には入手が難しいとされる材料の調達に関しても、お客様をサポートいたします。
当社は単に成形を行うだけでなく、設計段階からの技術相談、代替材料を用いた試作成形による評価支援、そして量産化に向けた射出成形上の課題解決まで、お客様の製品開発プロセス全体をサポートするパートナーでありたいと考えています。
PFAS規制への対応は、多くの設計担当者の皆様にとって、複雑で困難な課題と言えます。代替材料の選定に迷われている、既存の設計からの変更点にお悩みである、あるいは新しい材料での射出成形性に不安があるなど、どのようなことでも結構です。ぜひお気軽に当社までご相談ください。お客様の状況を詳しくお伺いし、共に最適なソリューションを見つけ出すパートナーとして、全力でサポートさせていただきます。