PPS射出成形における「ガス対策」完全ガイド ~設計から成形、金型メンテナンスまで~
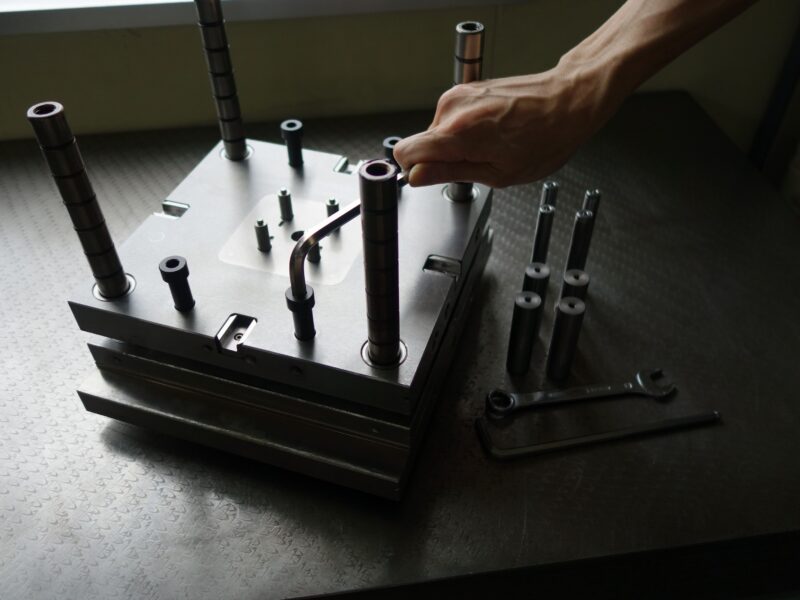
PPS(ポリフェニレンサルファイド)は、その卓越した耐熱性、耐薬品性、機械強度、寸法安定性から、ポンプ部品、配管機器、電気電子部品など、過酷な環境下で使用される高機能部品に不可欠なスーパーエンジニアリングプラスチックとして広く採用されています。しかし、その優れた性能の裏側で、射出成形の現場では「ガス」に起因するトラブルに頭を悩ませることが少なくありません。ガス焼けによる製品の外観不良や強度低下、金型表面に付着・蓄積する「ヤニ」や「モールドデポジット」と呼ばれる金型汚れによる寸法不良や離型不良、そしてそれに伴う頻繁な金型メンテナンスによる生産性の低下…。PPS成形におけるガス問題は、製品の品質、コスト、そして生産性すべてに深刻な影響を及ぼす、避けては通れない課題と言えます。
本コラムでは、このPPS成形におけるガス問題に焦点を当て、なぜガスが問題となるのか、その原因から具体的な影響、そして克服するための対策を「製品設計」、「成形条件」、「金型設計」、「金型メンテナンス」という製品ライフサイクルの各段階に沿って、体系的かつ網羅的に解説します。ガス対策を制するものがPPS成形を制する――長年にわたるPPSの成形加工を通じて培った当社のノウハウを公開いたします。
なぜPPS成形ではガスが問題になるのか?
PPS成形で問題となる「ガス」は、主に以下の4つの発生源から生じると考えられています。
樹脂自体からの発生ガス
PPSは非常に熱安定性の高い樹脂ですが、300℃を超える高温の溶融状態に長時間晒されたり、スクリュー回転による過度のせん断を受けたりすると、ポリマー鎖が微量ながら分解し、硫黄化合物(H2S、SO2など)を含むガスを発生させる可能性があります。特に、シリンダー内での滞留時間が長い場合や、高温設定での成形時に顕著になる傾向があります。
添加剤からの発生ガス
ガラス繊維強化グレードの場合、繊維表面の処理剤(シランカップリング剤など)や、その他グレードに含まれる滑剤、安定剤などの添加剤が高温で分解・揮発し、ガス発生の一因となることがあります。
キャビティ内の空気
射出成形では、金型が閉じた状態でもキャビティ内には空気が存在します。射出時に溶融樹脂が流入してくると、この空気が圧縮され、逃げ場を失ってたまりやすくなります。
材料中の水分・揮発分
PPSは吸湿性が低いとはいえ、ゼロではありません。予備乾燥が不十分だと、残存した水分が高温で水蒸気となり、ガスが発生します。また、ペレット自体に含まれる低分子量の未反応モノマーやオリゴマーなども揮発することがあります。
これらのガスが成形プロセス中に適切に排出されないと、「ガス焼け」や「金型汚れ」といった問題を引き起こします。
ガス焼け
キャビティ内の空気や発生ガスが、充填される樹脂によって行き場を失い、急激に圧縮(断熱圧縮)されることで数百度もの高温になります。この高温によって樹脂自体が燃焼・炭化し、製品表面に黒~褐色の焦げ跡として現れるのがガス焼けです。主に、ガスが最後に溜まる充填末端や、ガスベントが不十分な箇所で発生します。
金型汚れ(ヤニ、モールドデポジット)
発生したガスや樹脂の分解生成物が、高温の金型表面(キャビティ、コア、ベント部、パーティング面など)に付着し、徐々に蓄積していく現象です。初期は薄い膜状ですが、進行すると硬い炭化物や硫化物などの層となり、除去が困難になります。
ガス問題が引き起こすトラブル(影響の具体例)
ガス問題は、単なる外観不良にとどまらず、様々なトラブルを引き起こします。
成形品品質の低下
外観不良:ガス焼けは最も代表的な外観不良です。金型汚れが原因で、製品表面の光沢ムラや転写不良(シボ模様などが綺麗に出ない)も発生します。
強度低下:ガス焼け部分は材質が劣化・脆化しており、製品強度を著しく低下させます。また、ウェルドライン(樹脂の合流部)にガスが巻き込まれると、その部分の結合が不十分になり、強度が低下します。
寸法不良:金型汚れがキャビティ表面に蓄積すると、製品の寸法が徐々に変化してしまいます。また、ガスが充填を阻害し、ショートショット(充填不足)となることもあります。
生産性・コストの悪化
不良率増大:上記のような品質不良品の発生は、選別工数の増加と廃棄ロスに繋がります。
成形不安定化: ショートショットや離型不良(金型汚れによる)が頻発すると、安定した連続生産が困難になります。
メンテナンス工数増大:金型汚れを除去するための頻繁な金型清掃が必要となり、成形機の稼働率を著しく低下させます。無理に汚れを除去しようとして金型を傷つけるリスクもあります。
生産性の制限:ガス焼けを恐れて射出速度を上げられないなど、本来達成できるはずの短いサイクルタイムを実現できず、生産効率が低下します。
このように、ガス問題はPPS成形における品質・コスト・納期(QCD)すべてに悪影響を与えるため、根本的な対策が不可欠です。
設計段階でできるガス対策(発生抑制と排出促進)
ガス対策は、成形現場だけでなく、製品設計の段階から始まっています。設計段階での配慮が、後の工程でのトラブルを未然に防ぐことに繋がります。
ガス溜まりを意識した形状設計
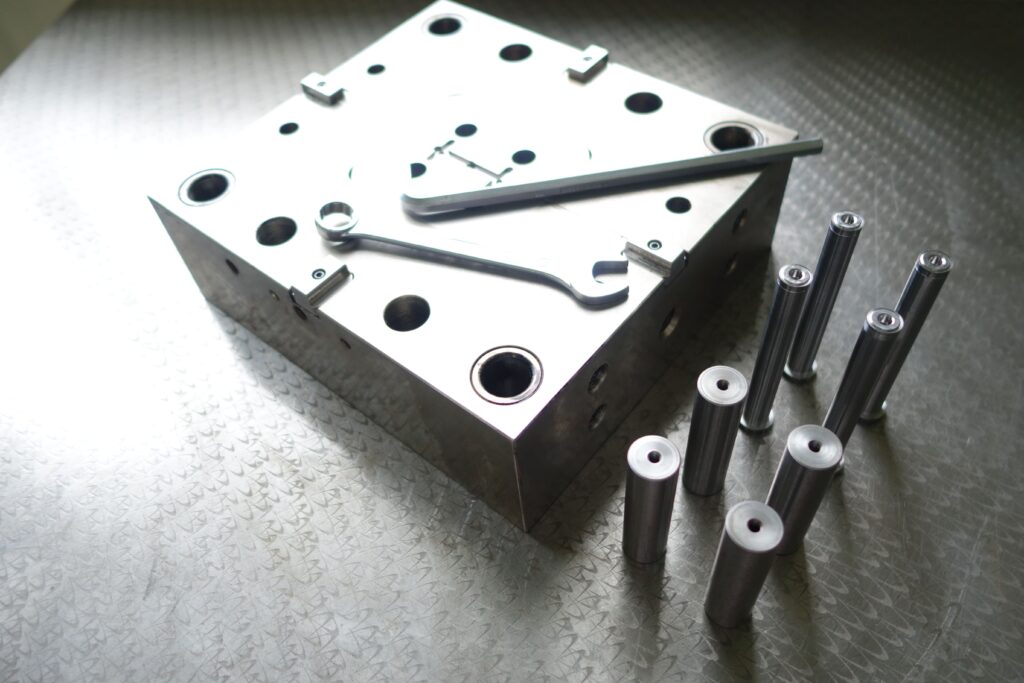
製品形状を設計する際には、溶融樹脂がどのように流れ、どこで空気やガスが最後に閉じ込められそうかを意識することが重要です。極端な厚肉部や袋小路のような形状は、ガス溜まりとなりやすいため、可能であれば避けるか、その箇所に効果的なガスベントを設置することを前提とした設計を心がけます。
肉厚を可能な限り均一にすることも、スムーズな充填を促し、空気の巻き込みを低減する上で有効です。
充填バランスとゲート設計
CAE流動解析などを活用して充填パターンを予測し、ガスが充填末端や意図したベント箇所へスムーズに押し出されるように、ゲートの位置や数を最適化します。複数のゲートを設ける場合は、同時に充填が完了するようにバランスを取ることも、ガス閉じ込めを防ぐポイントです。
ガスベント設置スペースの考慮
金型構造上、ガスベントを設置しやすい設計を意識します。例えば、パーティングライン(金型の合わせ面)をガスが抜けやすい位置に設定する、突き出しピンをガスが溜まりやすい箇所に効果的に配置する(ピンのクリアランスもベントとして利用できる)、といった配慮です。
成形条件によるガス対策(発生抑制と排出促進)
適切な成形条件の設定は、ガスの発生を抑制し、発生したガスをスムーズに排出させるための重要な手段です。
ガスの発生を抑制する条件
樹脂温度・滞留時間:必要以上に高い樹脂温度や、シリンダー内での長い滞留時間は、樹脂の熱分解によるガス発生を促進します。メーカー推奨温度範囲内のできるだけ低い温度で、かつ適切なサイズの成形機を選定し、滞留時間を管理することが基本です。
背圧・スクリュー回転数:過度のせん断発熱はガス発生の原因となります。背圧はガス抜き効果も期待できますが、上げすぎは禁物です。必要最低限(例:5~15MPa程度)に設定し、スクリュー回転数も上げすぎないように注意します。
予備乾燥の徹底:水分由来のガス(水蒸気)は、シルバーストリークだけでなくガス焼けの原因にもなります。推奨条件(例:130~150℃で3~4時間)での確実な乾燥が不可欠です。
ガスをスムーズに排出させる条件
射出速度の制御(特に充填終盤): これが最も効果的なテクニックの一つです。キャビティ内のガスは、樹脂が充填されるに従ってベントに向かって押し出されます。充填終盤で射出速度を遅くすることで、ガスがベントから排出されるための時間的猶予を与え、断熱圧縮によるガス焼けを効果的に抑制できます。多くの成形機には、射出工程中の速度を段階的に変える「多段速度制御」機能が搭載されていますので、これを活用します。ただし、速度を落としすぎると他の問題(ヒケ、ウェルド強度低下など)を引き起こす可能性もあるため、バランスの見極めが重要です。
型締力:適正な型締力を設定します。高すぎるとパーティング面のベントが潰れて機能しなくなる可能性があります。
金型設計・製作におけるガス対策(排出経路の確保)
ガス対策の要諦は、「発生したガスをいかに効率よく金型外へ排出するか」にあります。そのための鍵を握るのが金型設計、特にガスベントの設計です。
ガスベントの最適設計
設置場所:パーティングライン(PL)全周を基本とし、特に充填末端となりやすい箇所には十分なベントを設けます。CAE解析や試作成形で充填末端を正確に把握することが重要です。その他、エジェクターピン(ピンと穴のクリアランス、ピン側面へのDカット加工等)、入れ子やスライドコアの合わせ部なども重要なベント経路となります。ランナー末端のガス抜きも忘れずに。
ベント寸法:深さ:PPSの場合、0.005mm~0.02mm程度が一般的です。この微小な隙間が、溶融樹脂の流出(バリ)は防ぎつつ、ガス分子のみを通過させるための肝となります。精密な加工精度が要求されます。
ランド長さ:金型が密着する部分(ベント溝の手前)の長さで、通常3~5mm程度。ここをガスが通過します。
ガス逃がし溝:ランドを越えたガスを金型外へスムーズに導くための溝。幅は広く(例:5mm以上)、深さも十分(例:0.5mm以上)に確保します。
ベントの種類:一般的な溝形状のほか、ガス抜けの効率を高めるために、特殊な形状(ジグザグ等)や、多孔質の焼結金属を用いた「ポーラスベント」なども有効な場合があります。
金型材質と表面処理
PPSから発生する可能性のある腐食性ガスや、GF強化グレードによる摩耗に耐えるため、金型のキャビティ・コア材質には耐腐食性・耐摩耗性の高い鋼材(例:ステンレス系、マトリックス系高速度鋼)を選定するか、適切な表面処理(窒化処理、各種PVD/CVDコーティングなど)を施すことが強く推奨されます。これにより、金型寿命の延長とメンテナンス性の向上が期待できます。表面処理は金型汚れの付着抑制にも効果があります。
金型メンテナンスによるガス対策(排出経路の維持)
どんなに優れたガスベントを設計・製作しても、成形を続けるうちに必ずガスや分解生成物によって汚れて詰まってしまいます。ガスベントの効果を持続させるためには、定期的かつ適切なメンテナンスが不可欠です。
定期メンテナンスの重要性
ガスベントの詰まりは、ガス焼け、ショートショット、寸法不良など、様々なトラブルの直接的な原因となります。計画的なメンテナンススケジュールを立て、実行することが安定生産の鍵です。
清掃頻度と方法
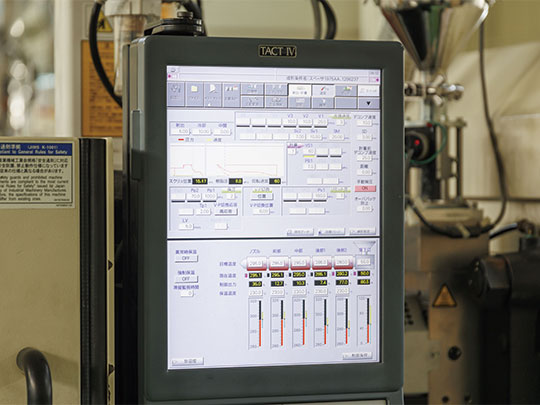
頻度: 一概には言えませんが、数千~数万ショットごと、あるいは製品品質に変化(ガス焼けの兆候、光沢の変化など)が見られたタイミングで実施するのが一般的です。汚れの度合いを観察しながら頻度を調整します。
方法: 最も確実なのは金型の分解清掃です。専用のクリーナーや溶剤、超音波洗浄機などを利用し、ベント溝やキャビティ表面の汚れを丁寧に除去します。化学的な洗浄と物理的な洗浄(柔らかいブラシやウエス)を組み合わせますが、ベントの精密なエッジ部を傷つけないよう細心の注意が必要です。研磨剤の使用は避けるべきです。生産中の応急処置としてドライアイス洗浄なども有効ですが、根本的な解決にはなりません。
ベント部の点検・補修
清掃時には、ベント部のエッジが摩耗したり潰れたりしていないかを確認し、必要であれば精密な補修や再加工を行います。
まとめ
PPS射出成形におけるガス問題は、やっかいな課題ではありますが、決して克服できないものではありません。その原因を正しく理解し、「製品設計」「成形条件」「金型設計」「金型メンテナンス」の各段階で、本稿で解説したような適切な対策を総合的に講じることが重要です。特に、ガスベントの適切な設計・設置と、それを維持するための定期的な金型メンテナンスは、PPS成形の成否を分けると言っても過言ではありません。これらの対策を徹底することで、ガスに起因する様々なトラブルを抑制し、PPSの持つ優れた性能を最大限に引き出した高品質な製品を、安定して生産することが可能になります。
当社では、PPS成形に関する豊富な経験とノウハウを蓄積しております。ガス対策をはじめ、PPS部品の設計や成形に関するお困りごとがございましたら、どうぞお気軽にご相談ください。お客様の製品開発を力強くサポートいたします。