直鎖型PPS、架橋型PPSの違い~基本特性と材料選定の基礎知識~

近年、製品の高性能化、小型化、軽量化への要求が高まる中、従来の金属材料に代わる素材として、エンプラ、特にスーパーエンプラの活用がますます広がっています。その中でも、PPS(ポリフェニレンサルファイド)は、その卓越した性能バランスから注目を集めている代表的なスーパーエンプラの一つです。PPSは、200℃を超える高い耐熱性、非常に優れた耐薬品性と難燃性、高い機械的強度と剛性、そして成形後の寸法安定性など、多くの優れた特性を兼ね備えています。これらの特性により、PPSは、高温環境下や薬品に晒されるポンプや配管機器の部品(インペラ、ケーシング、バルブ、継手など)、高い信頼性が求められる電気電子機器の機構部品(コネクタ、スイッチ、センサー部品、リレー部品など)といった、従来は金属や他の樹脂では対応が難しかった領域で、その活躍の場を広げています。まさに、過酷な条件下で使用される部品設計において、強力な選択肢となり得る素材と言えるでしょう。
しかし、一口にPPSと言っても、実はその分子構造によって大きく「直鎖型(リニア型)」と「架橋型(クロスリンク型)」の2つのタイプに分類されることはご存知でしょうか。そして重要なのは、このタイプの違いが、PPSの基本的な物性や成形加工性に少なからず影響を与えるという点です。つまり、最終製品に求められる性能を最大限に引き出すためには、それぞれのタイプの特徴を正しく理解し、用途に合わせて最適なPPSを選択することが不可欠となります。
本コラム(前編)では、この直鎖型PPSと架橋型PPSに焦点を当て、まずはその根幹となる分子構造の違いから解説を始めます。そして、その構造の違いが、機械的特性、熱的特性、流動性、耐薬品性といった基本的な物性にどのような差をもたらすのかを、比較しながら詳しく見ていきます。設計の初期段階で材料への理解を深めることは、後々の手戻りを防ぎ、より良い製品開発へと繋がる第一歩です。では、早速、始めていきましょう。
PPSの分子構造:直鎖型と架橋型の違い
PPSの優れた特性の源泉は、その特有の分子構造にあります。まずは、基本的な化学構造を確認し、その上で直鎖型と架橋型の構造的な違いを見ていきましょう。
PPSの基本化学構造
PPSは、芳香族環であるベンゼン環(フェニレン基)と硫黄原子(スルフィド結合)が交互に直線状に結合した、[-C6H4-S-]n という繰り返し単位を持つポリマーです。この強固なベンゼン環と、比較的柔軟で熱安定性に優れたスルフィド結合の組み合わせが、PPSの高い耐熱性や剛性、そして優れた耐薬品性の基盤となっています。
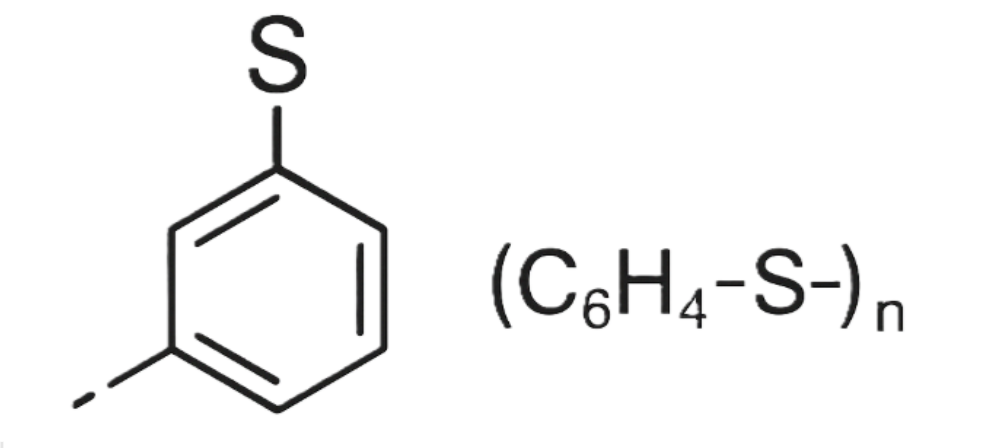
直鎖型PPSの分子構造
直鎖型PPS(リニア型PPSとも呼ばれます)は、その名の通り、上記の基本構造が長く、分岐なく直線状に連なった高分子量ポリマーです。イメージとしては、長い鎖が多数集まっている状態です。分子鎖が長い(=分子量が高い)ため、分子鎖同士の絡み合いが多くなり、これが後述する高い靭性(粘り強さ)などの特性に繋がります。製造プロセスにおいては、分岐や架橋を抑制する工夫がなされています。
架橋型PPSの分子構造
一方、架橋型PPS(クロスリンク型PPSとも呼ばれます)は、直鎖型とは異なるアプローチで作られます。まず、比較的分子量の低い(短い)直鎖状のPPSポリマーを合成します。その後、製造工程中の熱処理(キュアリング)などによって、これらのポリマー鎖の間で部分的に化学的な結合(架橋)を形成させます。これにより、分子鎖同士が橋渡しされたような、三次元的な網目構造が部分的に導入されます。この架橋構造が、架橋型PPS特有の特性、例えば高温での寸法安定性(クリープ特性)や、特定の条件下での流動性などに影響を与えます。架橋の度合いは、グレードによってコントロールされています。
製造プロセスの違い
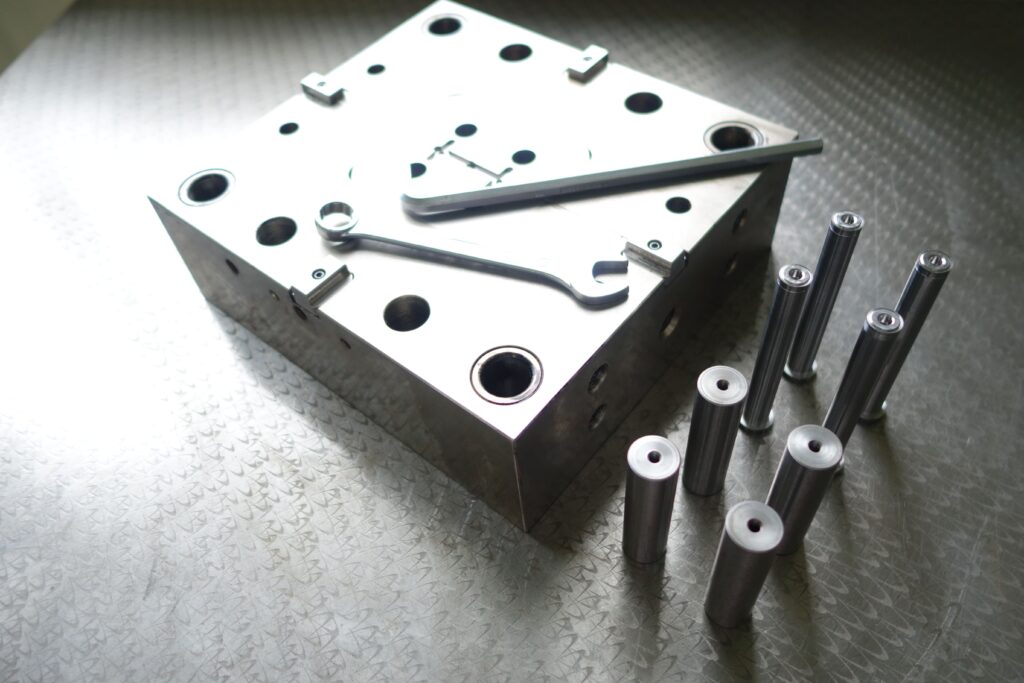
直鎖型PPSは、一般的にNMP(N-メチル-2-ピロリドン)などの極性溶媒中で、p-DCB(パラジクロロベンゼン)と硫化ナトリウムなどを反応させて重合します。高分子量化や分岐抑制のための技術が用いられます。一方、架橋型PPSは、比較的低分子量のPPSを合成した後、空気中での熱処理などを加えて架橋構造を導入するプロセスが一般的です。これらの製造プロセスの違いが、最終的な分子構造、そして物性の差となって現れるのです。
直鎖型PPSと架橋型PPSの特性比較
分子構造の違いが、具体的にどのような特性の差となって現れるのか、設計者が特に注目すべき項目を中心に比較していきましょう。ここでは主に、ガラス繊維などで強化されていない非強化グレードや、代表的なGF(ガラス繊維)強化グレードを念頭に解説します。
流動性
射出成形において、溶融した樹脂の「流れやすさ」、すなわち流動性は、成形品の形状自由度や生産性を左右する非常に重要な特性です。
溶融粘度/MFR(メルトフローレート): 一般的に、架橋型PPSの方が低粘度(高流動)なグレードを設計しやすい傾向にあります※。これは、ベースとなるポリマーの分子量が比較的低いためです。一方、直鎖型PPSは高分子量であるため、本質的に高粘度となる傾向があります。ただし、近年では直鎖型でも高流動グレードが開発されています。
※分子量が低い方が分子鎖は動きやすく、流動性は高くなります。架橋構造は流動を妨げる要因にもなり得ますが、ベース分子量の低さが勝り、結果的に高流動グレードが作りやすいと考えられます。
設計・成形への影響: 架橋型の高流動性は、薄肉成形や複雑な形状を持つ部品、あるいは多数個取り金型(一度に多くの製品を成形する金型)での充填性を向上させるメリットがあります。しかし、流動性が良すぎると、金型のわずかな隙間から樹脂が漏れ出す「バリ」が発生しやすくなるというデメリットもあります。逆に、直鎖型の高粘度は、充填不足(ショートショット)のリスクを高める可能性がありますが、バリは発生しにくい傾向があります。材料選定時には、部品形状や金型構造、成形機の能力などを考慮して、適切な流動性のグレードを選ぶ必要があります。
機械的特性
部品が使用される環境で、力や衝撃にどれだけ耐えられるかを示すのが機械的特性です。
靭性(引張伸び、衝撃強度): 材料の「粘り強さ」や「壊れにくさ」を示す指標です。特に非強化グレードで比較すると、直鎖型PPSの方が本質的に靭性に優れる傾向があります。引張試験での伸びや、シャルピー衝撃強度などの値が高くなることが多いです。 直鎖型は分子量が高く、分子鎖が長く絡み合っているため、外部から力が加わった際に、分子鎖がほどけたり滑ったりすることでエネルギーを吸収しやすく、破壊に至るまでの抵抗が大きいと考えられます。
設計・成形への影響: 部品に衝撃が加わる可能性がある場合や、組み立て時のはめ込み(スナップフィット)などで割れにくさが求められる場合には、直鎖型PPSが有利な選択肢となり得ます。ただし、ガラス繊維などを強化材として添加すると、靭性は低下する傾向にあるため、強化グレードでの選定では注意が必要です。
強度・剛性(引張強度、曲げ弾性率): 材料の「強さ」や「硬さ(変形しにくさ)」を示す基本的な指標です。PPSは本来、高い強度と剛性を持っていますが、実用上はガラス繊維(GF)などで強化されたグレードが多く用いられます。GF強化グレードで比較した場合、タイプによる強度・剛性の顕著な差は、同程度のGF含有量であれば比較的小さいことが多いですが、ポリマー自体の特性や結晶化度、繊維との界面接着性などの違いが影響する可能性はあります。架橋構造が剛性の向上にわずかに寄与するとも言われます。
クリープ特性: 材料に一定の荷重をかけ続けたときに、時間とともに変形が進行する現象をクリープと呼びます。特に高温環境下での長期的な寸法安定性が求められる部品(例:精密機構部品、高温環境下の支持部品など)では、クリープ特性が重要になります。架橋型PPSの方が、一般的に高温でのクリープ特性に優れる傾向があります。
疲労特性: 繰り返し応力がかかる部品(例:スイッチ機構、振動する部品など)の耐久性に関わる特性です。PPSは一般に良好な耐疲労性を示しますが、タイプやグレードによる差については、具体的なデータに基づいた評価が必要です。
熱的特性
部品が使用される温度環境への耐性を示す特性です。融点(Tm)、ガラス転移点(Tg): 融点(結晶が溶ける温度)は両タイプとも約280℃、ガラス転移点(非晶部分が動きやすくなる温度)は約90℃であり、タイプによる顕著な差はありません。
荷重たわみ温度(HDT): 規定の荷重をかけた状態で、材料が一定量たわむ温度を示し、短期的な耐熱性の指標となります。GF強化グレードでは、両タイプとも非常に高いHDT(例:GF40%強化で260℃以上)を示します。ポリマー構造や結晶化度の違いにより、わずかな差が見られることもあります。
連続使用温度(UL温度認定): 長期的な熱安定性を示す指標です。PPSは、両タイプとも高い連続使用温度(例:200~240℃程度、グレードによる)が認定されています。架橋構造は、熱酸化安定性に寄与するとも言われています。
線膨張係数
温度変化によって材料がどれだけ膨張・収縮するかを示す係数です。金属と組み合わせて使用する場合や、精密な寸法精度が要求される部品では特に重要です。線膨張係数は、GFの含有量によって大きく変化しますが、ポリマータイプによる差もあります。一般に直鎖型の方が結晶化度が高くなりやすく、その影響で線膨張係数がやや低くなる傾向が見られることがあります。
耐薬品性
PPSの最も優れた特徴の一つが、その広範な耐薬品性です。直鎖型、架橋型ともに、極めて優れた耐薬品性を示します。200℃以下の温度域では、PPSを溶解できる汎用的な溶剤はほとんど存在しません。酸、アルカリ、有機溶剤、油脂類など、多くの薬品に対して高い耐性を持つため、化学プラントの部品、ポンプ部品、配管機器部品などに適しています。特定の強酸化剤や高温の特定薬品に対しては、わずかな差が見られる可能性もありますが、実用上、大きな違いとして意識されることは少ないでしょう。
結晶化挙動
PPSは結晶性樹脂であり、溶融状態から冷却される際に分子が規則正しく配列して結晶構造を形成します。この結晶化のしやすさ(結晶化速度)や、最終的にどれだけの割合が結晶になるか(結晶化度)は、成形性や最終物性に影響を与えます。
結晶化速度・結晶化度: 一般的に、直鎖型PPSの方が分子鎖の規則性が高く、結晶化しやすい(結晶化速度が速く、到達結晶化度も高い)傾向があります。
設計・成形への影響: 結晶化速度が速いと、成形サイクルを短縮できる可能性があります。また、高い結晶化度は、剛性、耐熱性、耐薬品性、寸法安定性の向上に寄与します。一方で、結晶化に伴う体積収縮が大きくなるため、ヒケが発生しやすくなったり、成形収縮率が大きくなったりする傾向があります(後編で詳述)。架橋型は結晶化がやや遅いため、金型温度などの条件設定がより重要になる場合があります。
その他の特性
電気的特性: 両タイプとも、高い体積抵抗率、優れた絶縁破壊強さ、低い誘電率・誘電正接を示し、優れた電気絶縁材料として利用されます。高温・高湿環境下でも特性変化が少ないのが特徴です。
難燃性: PPSは、難燃剤を添加しなくても、本質的に高い難燃性(UL94規格でV-0相当)を示します。これは、分子構造に由来する特徴であり、タイプによる大きな差はありません。
吸水率: 吸水率は極めて低く、寸法安定性に優れています。多湿環境下での物性変化や寸法変化が非常に小さい点は、精密部品にとって大きなメリットです。タイプによる差はほとんどありません。
コスト
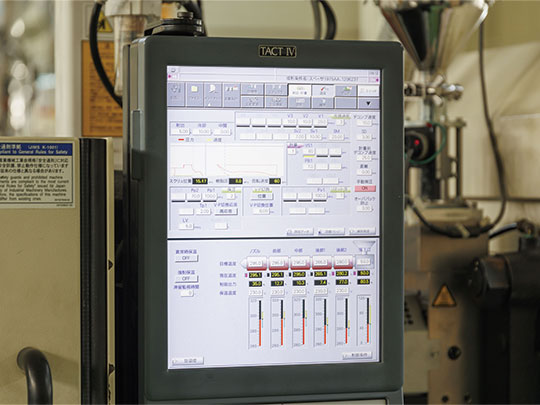
材料選定において、コストは無視できない要素です。一般的に、直鎖型PPSの方が、架橋型PPSよりも高価になる傾向があります。 直鎖型は高分子量化や分岐抑制など、製造プロセスに高度な技術が必要とされることが一因と考えられます。要求される性能(特に靭性など)が直鎖型でなければ達成できない場合を除き、コストと性能のバランスから架橋型が選択されるケースも多くあります。最終的な部品コストは、材料費だけでなく、成形加工性(サイクルタイム、不良率)なども含めて総合的に判断する必要があります。
特性比較のまとめ
これまでの比較を簡潔にまとめると、以下のようになります。(◎:優れる、○:良好、△:やや劣る/注意、-:同等)
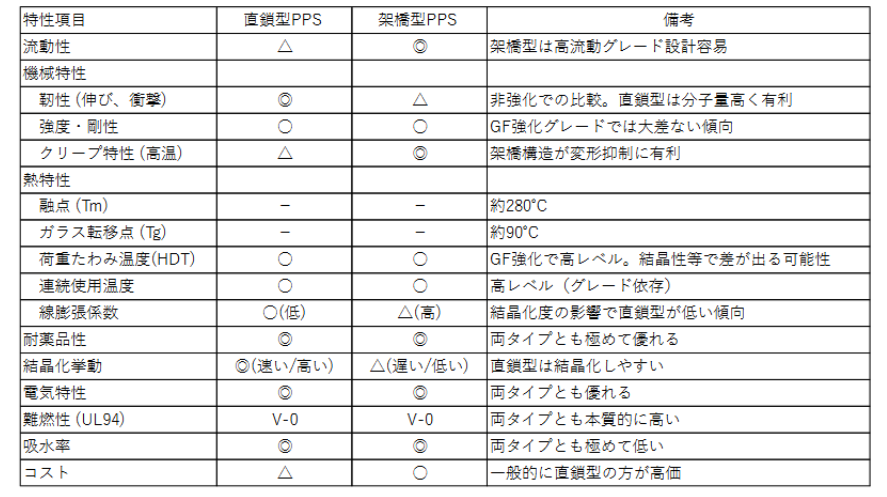
※注意: 上記は一般的な傾向を示すものであり、実際の特性は個々の材料グレード(フィラーの種類や含有量、添加剤など)によって異なります。必ず詳細な材料データをご確認ください。
前編のまとめ
本稿(前編)では、スーパーエンプラPPSの2つの主要なタイプ、直鎖型と架橋型について、その分子構造の違いから説き起こし、基本的な物性(流動性、機械特性、熱特性、耐薬品性、結晶化挙動など)にどのような差が現れるかを比較解説しました。
まとめると、直鎖型PPSは、高分子量で分子鎖の絡み合いが多く、優れた靭性を持つ一方、溶融粘度が高く、結晶化しやすい傾向があります。コストは比較的高めです。
架橋型PPSは、部分的な架橋構造を持ち、流動性に優れ、高温でのクリープ特性が良い一方、靭性は直鎖型に劣る傾向があります。結晶化はやや遅く、コストパフォーマンスに優れます。これらの基本的な特性の違いを理解することは、設計する部品に求められる要求特性、例えば「衝撃に耐える粘り強さが必要か?」「複雑な形状を確実に充填できる流れやすさが必要か?」「高温下での長期的な寸法安定性が重要か?」といった点を考慮し、どちらのタイプのPPSが候補となり得るか、その大枠を掴むための重要な第一歩と言えます。
しかし、材料の基本的な特性を理解しただけでは、最適な材料選定や安定した成形には繋がりません。これらの特性の違いが、実際の「射出成形プロセス」において具体的にどのような影響を及ぼすのでしょうか? 例えば、流動性の違いは推奨される成形条件(温度、圧力、速度)にどう影響するのか? 結晶化挙動の違いは、成形サイクルタイムやヒケ・ソリといった不良の発生しやすさにどう関わるのか? また、PPS特有の成形上の注意点(ガス対策など)は?
次回の後編では、これらの疑問に答えるべく、直鎖型・架橋型PPSの特性差が射出成形プロセス(推奨成形条件、発生しやすい不良とその対策、金型設計上の注意点)に与える具体的な影響について、さらに深く掘り下げて解説します。また、一般的な用途例を挙げながら、最終的な材料選定のポイントについても考察します。設計段階での知識が、実際の製造現場でどのように活かされるのか、より実践的な視点でお届けする予定です。ぜひ後編もご覧いただき、皆様のPPS部品開発にお役立てください。
【後編】直鎖型PPS、架橋型PPSの違い~成形加工性と材料選定のポイント~