【入門】射出成形ってどんな技術? 設計者が知っておきたいプラスチック部品の作り方

「この複雑な形状、どうすればプラスチックで効率よく、かつ高いデザイン性を保ちながら実現できるだろうか?」
「要求される性能や強度を維持しつつ、材料費や製造コストをもっと抑える方法はないものか?」
製品設計や開発の現場では、日々このような課題や目標の中で、最適な解を模索されていることでしょう。スマートフォンやタブレット端末、私たちの移動を支える自動車の内外装部品、生活を豊かにする最新の家電製品、精密さが求められる医療機器、そして日々の暮らしに欠かせない雑貨類に至るまで、現代社会は多種多様なプラスチック製品によって形作られています。そして、これらの製品が驚くほど高精度に、複雑な形状をもって、しかも効率的に大量生産されている背景には、「射出成形」という非常に強力で洗練された製造技術の存在があります。この技術なくして、現代のものづくりは語れないと言っても過言ではありません。
本コラムでは、製品の設計者やエンジニア、プロダクト開発に携わるすべての皆様に向けて、プラスチック部品製造におけるまさに心臓部とも言える「射出成形」について、その基礎的な仕組みから、設計・製造現場で実際に役立つ重要なポイントまでを、数回にわたり分かりやすく解説していく予定です。単に技術の表面的な概要を紹介するだけでなく、設計者の視点から「なぜそうするのか」「どうすればより良くなるのか」という本質を理解し、日々の業務に活かせる実践的な知識を提供することを目指します。
今回は、「射出成形とは一体どのような技術なのか?」その全体像を掴んでいただくことから始めます。そして、なぜ製品の企画や設計に携わる皆様が、この一見すると製造現場寄りの技術とも思える射出成形について深く知る必要があるのか、その本質的な重要性について改めて考えていきます。射出成形は、単なる数ある製造方法の一つ、という位置づけではありません。それは、設計者の頭の中にあるアイデアやコンセプトを、手に取れる現実の製品へと具現化するための強力な手段であり、その製品の機能性、耐久性、美観、コスト、ひいては市場での競争力そのものを大きく左右する、まさに製品開発の根幹をなす基盤技術なのです。
射出成形の原理と可能性、そしてその限界を理解することが、設計の選択肢を広げ、より洗練された、より実現性の高い、そしてより市場に受け入れられる製品開発への確かな道筋を示してくれるはずです。まずは今回、その基礎となる全体像を共に学んでいきましょう。
射出成形とは?:プラスチックを「たい焼き」のように作る技術
射出成形とは何か、一言で表現するのは難しいかもしれませんが、身近な例でイメージを掴んでみましょう。それは、まるで「たい焼き」を作るプロセスに似ています。
たい焼きを作る時、小麦粉などを混ぜた生地(材料)を、魚の形をした金属製の「型」に流し込み、熱を加えて焼き固めます。型を開けると、そこには型の形状通りになった、たい焼きが出来上がっています。射出成形も、これと非常によく似た原理に基づいています。
・たい焼きの生地 → 溶かしたプラスチック(樹脂)
・たい焼きの型 → 金型(かながた)
・熱を加えて焼き固める → 金型内で冷却して固める
このように、「熱で溶かしたプラスチック材料を、精密な金型の中に注入し、冷やし固めることで、目的の形状の製品を作る技術」、それが射出成形です。たい焼きと違うのは、材料を高圧で金型に「射出」する点と、非常に高い精度で複雑な形状のものを大量に作れる点です。
基本的な仕組み(プロセス)
では、もう少し具体的に射出成形のプロセスを見ていきましょう。射出成形は、主に以下の4つのステップを連続的に繰り返すことで、プラスチック部品を次々と生産していきます。
1.溶かす(可塑化)
まず、原料となる米粒状や粉末状のプラスチック(ペレットやパウダーと呼ばれる)を、射出成形機の「ホッパー」という投入口に入れます。投入されたプラスチックは、内部にあるスクリュー(ネジのような部品)の回転によって前方に送られながら、ヒーターによって加熱され、ドロドロに溶けた状態になります。ちょうど、チョコレートを湯煎で溶かすようなイメージです。この工程を「可塑化」と呼びます。
2.射出する(充填)
次に、溶けて金型に注入できる状態になったプラスチックを、スクリューが前進する力(プランジャーのような役割)によって、金型のノズル(先端の射出口)から高圧で金型内部の空間(キャビティ)に一気に注入します。たい焼きの型に生地を流し込む工程に似ていますが、射出成形では非常に高い圧力で、短時間のうちに隅々まで材料を行き渡らせます。この工程が「射出」または「充填」です。
3.冷やす(冷却・固化)
金型内部に充填された溶けたプラスチックは、金型に設けられた冷却回路(内部に冷却水などが通っている)によって冷やされ、固まっていきます。
製品の形状や寸法精度を保つために、適切な時間と温度で均一に冷却することが重要です。たい焼きが焼き固まるのを待つ時間にあたります。
4.取り出す(離型)
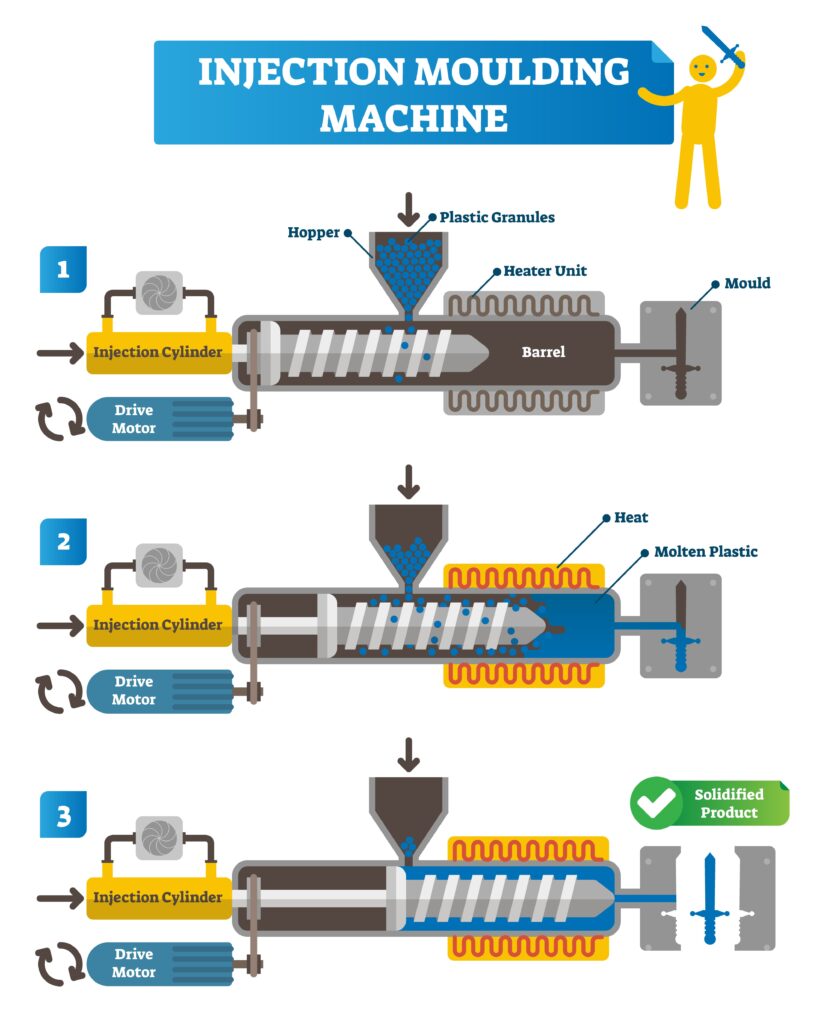
プラスチックが完全に固まったら、金型が開きます。そして、金型内部に組み込まれた「エジェクタピン」と呼ばれるピン(突き出し棒)が、固まった製品を金型から押し出して取り出します。これで、1サイクルの完了です。金型が閉じ、再びステップ1から繰り返すことで、同じ形状の製品が連続して生産されます。
この製品を取り出す工程を「離型」と呼びます。
この一連のサイクルタイム(1サイクルにかかる時間)は、製品の大きさや形状、材料によって異なりますが、数十秒~数分程度が一般的で、非常に効率的な生産が可能です。
どんなものが作れる?身近な製品例
射出成形は、その生産性の高さと形状自由度から、非常に幅広い分野で活用されています。皆さんの身の回りにも、射出成形で作られた製品がたくさんあります。
自動車分野:バンパー、インストルメントパネル(インパネ)、ドアトリム、各種スイッチ類、ランプハウジングなど、内外装の多くの部品。
家電・エレクトロニクス分野:テレビやパソコンの筐体、リモコン、スマートフォンのケース、コネクタ、ギア(歯車)などの機構部品。
日用品・雑貨分野:食品容器(タッパーなど)、ペットボトルのキャップ、洗面器、歯ブラシの柄、文房具(ボールペンの軸など)、おもちゃ(プラモデルやブロックなど)。
医療分野:注射器のシリンダーやプランジャー、シャーレ、各種検査キットの部品など、高い精度と清浄度が求められる部品。
これらはほんの一例です。複雑な形状のものから、精密な寸法が要求されるものまで、多種多様なプラスチック部品が射出成形によって生み出されているのです。
射出成形のメリット・デメリット
非常に便利な射出成形ですが、他の加工方法と同様に、得意なこと(メリット)と苦手なこと(デメリット)があります。設計を行う上では、これらの特性を理解しておくことが重要です。
メリット(得意なこと)
・大量生産性に優れる:一度金型を作ってしまえば、短いサイクルタイムで同じ形状の製品を連続して大量に生産できます。生産数量が多くなればなるほど、製品1個あたりのコストを低く抑えることができます。
・複雑な形状の製品が作れる:金型を工夫することで、曲面や凹凸、リブ(補強)、ボス(ねじ穴の土台)などを持つ、複雑な三次元形状の製品を一体で成形できます。切削加工など他の方法では難しい形状も実現可能です。
・寸法精度が高い:金型は非常に精密に作られており、成形条件を適切に管理することで、寸法精度の高い製品を安定して生産できます。製品ごとのばらつきも少なく、組み立て部品などに適しています。
・材料の選択肢が広い:熱可塑性プラスチック(加熱すると軟化し、冷やすと固まる)を中心に、様々な種類の樹脂材料(ポリプロピレン(PP)、ポリエチレン(PE)、ABS樹脂、ポリカーボネート(PC)、ナイロン(PA)、PSUなど)を使用できます。一部、熱硬化性プラスチックやエラストマー(ゴム状の弾性を持つ材料)の成形も可能です。
・後加工が少ない(または不要):成形された製品は、多くの場合、そのままの状態で(あるいは簡単な仕上げ処理だけで)使用できます。切削加工のように、材料の大部分を削り取る必要がなく、材料の無駄も比較的少ないです。
デメリット(苦手なこと・注意点)
・金型の初期費用が高い:射出成形における最大のデメリットは、金型の製作コストが高いことです。金型は、製品形状を精密に転写するため、高価な金属材料(特殊鋼など)を用いて、複雑な加工(切削、研磨、放電加工など)を経て作られます。製品形状が複雑になればなるほど、金型構造も複雑になり、コストはさらに上昇します。このため、生産数量が少ない場合には、金型費用を回収できず、製品単価が非常に高くなってしまいます。
・少量生産には不向き:上記の金型コストのため、試作品や数十個程度の小ロット生産には、コスト的に見合いません。このような場合は、3Dプリンターや切削加工など、他の工法が適している場合があります。
・金型製作に時間がかかる:金型は設計から製作、調整まで含めると、数週間から数ヶ月単位のリードタイムが必要です。製品開発スケジュールにおいて、金型製作期間を考慮に入れる必要があります。
・設計上の制約がある:射出成形品を設計する際には、金型から製品をスムーズに取り出すための配慮が必要です。代表的なものに「抜き勾配(ぬきこうばい)」があります。これは、金型が開く方向に沿って、製品側面にわずかな傾斜をつけることです。垂直な壁だと、金型と製品が擦れてしまい、取り出しにくくなったり、製品表面に傷がついたりするためです。その他にも、均一な肉厚にする、鋭い角を避ける(Rをつける)、アンダーカット(金型が開く方向だけでは抜けない形状)を避ける、といった設計上の配慮が求められます。これらの制約を無視した設計は、成形不良の原因になったり、金型構造を複雑化させコストアップを招いたりします。
なぜ設計者が射出成形を知るべきなのか?
ここまで射出成形の基本を解説してきましたが、なぜ製品の設計に携わるエンジニアや設計者が、この製造技術について知っておく必要があるのでしょうか? それは、設計と製造が密接に結びついているからです。
設計の自由度と限界を知るため
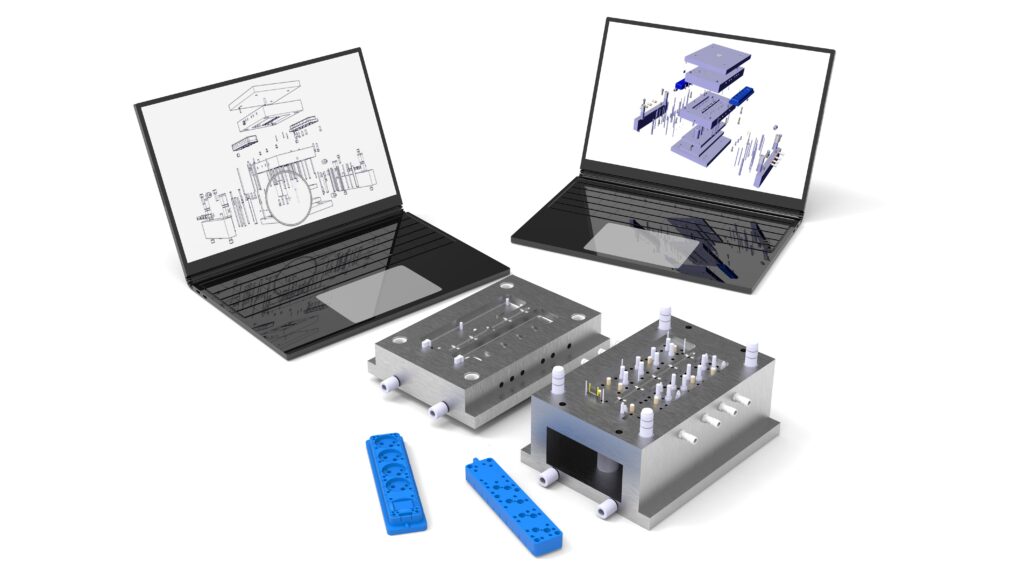
設計者は、製品の機能や性能、デザインを実現するために、自由な発想で形状を考えます。しかし、その形状が実際に製造可能でなければ、絵に描いた餅になってしまいます。射出成形の原理や、前述したような設計上の制約(抜き勾配、肉厚、アンダーカット処理方法など)を理解していれば、「どのような形状なら実現可能か」「どのような形状は難しいのか、あるいはコストがかかるのか」を設計段階で判断できます。
例えば、「この部分に補強のリブを立てたいが、抜き勾配はつけられるか?」「この部品を薄肉化したいが、樹脂が流れきるか? 強度は大丈夫か?」といった具体的な検討が可能になります。製造の限界を知ることで、
より現実的で、かつ最適な設計が可能になるのです。
コストを意識した設計のため
製品のコストは、材料費だけでなく、製造コスト(加工費)も大きな割合を占めます。射出成形の場合、特に金型コストと生産性(サイクルタイム)が製品単価に大きく影響します。設計のわずかな違いが、金型構造を複雑にし(例えば、アンダーカット形状を実現するためにスライド機構などを追加する必要がある場合)、金型費用を大幅に増加させることがあります。また、肉厚が不均一だったり、極端に厚かったりすると、冷却時間が長くなり、サイクルタイムが悪化して生産コストが上昇します。
設計段階で、抜き勾配を適切につける、アンダーカットを避ける工夫をする、肉厚をできるだけ均一にする、といった「製造しやすい設計」(DFM:Design for Manufacturability)を心がけることで、金型コストや成形コストを抑え、製品全体のコスト競争力を高めることができます。射出成金の知識は、コスト意識を持った設計に不可欠なのです。
より良い製品開発のため
優れた製品は、設計部門だけで生まれるものではありません。設計、製造、品質管理など、関係する部門が連携して初めて実現します。設計者が製造プロセスである射出成形について理解していれば、製造部門の担当者と具体的な議論をすることができます。「この設計では、ここにウェルドライン(樹脂が合流する部分にできる線状の跡)が出やすいのではないか?」「ゲート(樹脂の入り口)の位置をここに変えられないか?」といった、より専門的で建設的なコミュニケーションが可能になります。
これにより、開発の初期段階で問題点を洗い出し、設計変更の手戻りを減らすことによる結果として、開発期間の短縮、製品品質の向上、そしてスムーズな量産立ち上げにつながるのです。
まとめ
今回は、プラスチック製品の代表的な製造方法である「射出成形」について、その基本的な仕組み、メリット・デメリット、そして設計者が知るべき理由を解説しました。射出成形は、溶かしたプラスチックを金型に注入し、冷却・固化させることで製品を作るといった原理の技術です。
大量生産に適し、複雑な形状を高精度で作れる一方、金型の初期費用が高く、設計上の制約もありますが、設計者が射出成形を理解することは、設計の自由度と限界を知り、コストを意識し、より良い製品開発を進める上で非常に重要です。
射出成形は奥が深い技術であり、今回ご紹介したのはその入り口に過ぎません。しかし、基本的な概念を理解しておくことで、日々の設計業務や関連部門との連携に必ず役立つはずです。さらに詳しい情報や、具体的な製品開発に関するご相談がありましたら、お気軽に弊社までお問い合わせください。