エンプラのポリマーアロイの基本原理とメリットを解説
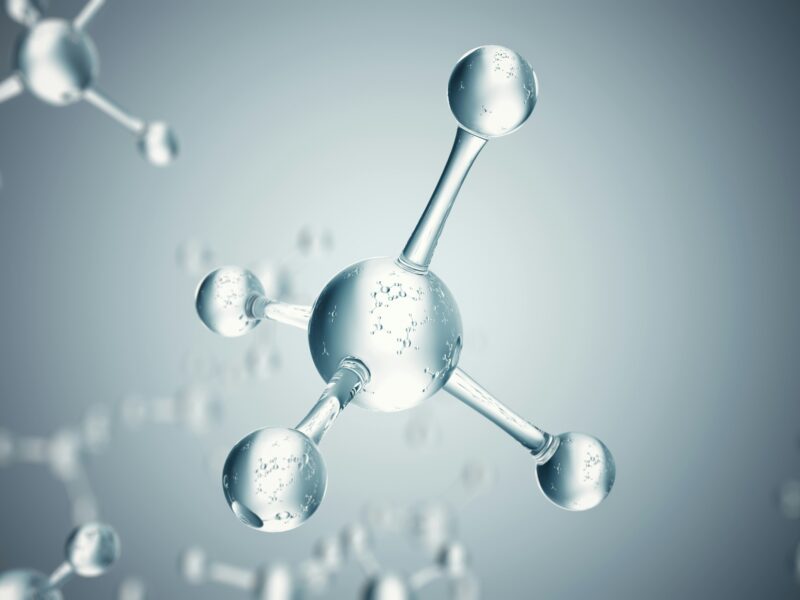
現代のものづくりにおいて、製品に求められる性能はますます高度化・多様化しています。軽量でありながら高強度、優れた耐熱性と同時に高い耐衝撃性など、時として相反するような特性を同時に満たすことが要求されるケースも少なくありません。こうした要求に対し、単一のプラスチック材料だけで応えることには限界があります。そこで注目されているのが「ポリマーアロイ」という技術です。エンジニアリングプラスチック(エンプラ)の世界では、このポリマーアロイ技術を駆使することで、単一材料では達成困難な特性バランスを実現し、製品の性能向上や新たな機能付与に貢献しています。
本コラムは二部構成でお届けします。この前編では、エンプラのポリマーアロイについて、その基本的な定義、構造、そしてポリマーアロイ化によって得られるメリット、基本的な設計指針を中心に解説していきます。
エンプラにおけるポリマーアロイとは
ポリマーアロイの基本定義
ポリマーアロイとは、その名の通り、2種類以上の異なるポリマー(高分子材料)を物理的あるいは化学的に組み合わせることで、新しい特性や機能を発現させた材料のことを指します。金属材料の世界で、異なる金属を混ぜ合わせることで強度や耐食性を向上させる「合金(Alloy)」がありますが、ポリマーアロイはその高分子版と考えると理解しやすいでしょう。目的は、それぞれのポリマーが持つ長所を活かし、短所を補い合うことにあります。例えば、ポリマーAは耐熱性に優れるが脆い、ポリマーBは衝撃に強いが耐熱性が低い、といった場合に、これらを適切に組み合わせることで、「耐熱性と耐衝撃性をバランス良く備えた材料」を生み出すことが可能になります。
特に、エンプラの分野では、汎用プラスチックよりも優れた耐熱性(一般的に100℃以上)、機械的強度、耐薬品性などが求められます。しかし、これらの高度な要求特性すべてを、単一種類のエンプラだけで完璧に満たすことは非常に困難です。ここに、ポリマーアロイ技術が活きる大きな意義が存在します。複数のエンプラや、時にはエンプラと汎用プラスチックを組み合わせることで、ターゲットとする性能をピンポイントで実現する「材料設計」が可能になるのです。
ポリマーアロイの基本構造と分類
ポリマーアロイは、構成されるポリマー同士がどのように混ざり合っているかによって、その構造や特性が大きく異なります。ここでは、その基本的な分類と、性能発現に重要な役割を果たす技術について解説します。
相溶型と非相溶型アロイとは
ポリマーアロイは、構成ポリマーの混ざり具合によって、大きく以下の2つに分類されます。
相溶型アロイ (Miscible Polymer Alloy / Compatible Polymer Blend)
これは、2種類以上のポリマーが分子レベルで均一に混ざり合い、全体として一つの相(均一な状態)を形成するタイプです。水とエタノールが完全に混ざり合うようなイメージです。相溶型アロイは、透明性が高くなる傾向があり、ガラス転移温度(Tg)などの熱的性質が、構成ポリマーの混合比に応じた単一の値を示すことが特徴です。しかし、一般的に化学構造が大きく異なるポリマー同士は、エントロピー的な要因(混ざりにくさ)から相溶しにくい性質があります。そのため、完全に相溶する組み合わせは限られています。代表的な例としては、m-PPE(変性ポリフェニレンエーテル)とPS(ポリスチレン)のアロイなどが挙げられます。
非相溶型アロイ (Immiscible Polymer Alloy / Incompatible Polymer Blend)
こちらは、ポリマー同士がミクロあるいはマクロなスケールで分離し、それぞれが独立したドメイン(相、島のような構造)を形成するタイプです。水と油が分離するイメージに近いですが、ポリマーアロイの場合は、多くの場合、一方のポリマー(マトリックス相、海)の中にもう一方のポリマー(分散相、島)が微細に分散した「海島構造」と呼ばれるモルフォロジー(形態)をとります。ポリマー同士は基本的に化学構造が異なるため、ほとんどのポリマーアロイはこの非相溶型に分類されます。非相溶型アロイの特性は、マトリックスと分散相それぞれの特性だけでなく、分散相の大きさ、形状、分布状態、そして両者の界面の状態に大きく依存します。
相溶化技術(コンパチビライザーの役割)
非相溶型アロイにおいて最も重要な課題は、異なるポリマー間の界面(境界面)の接着性をいかに高めるかという点です。水と油のように、本来混ざり合わないもの同士を無理に混ぜても、界面での結合が弱いため、外部から力が加わると簡単に剥離してしまい、材料全体の強度が著しく低下してしまいます(層間剥離、デラミネーション)。この問題を解決するために用いられるのが、「相溶化剤(Compatibilizer)」と呼ばれる特殊な添加剤です。相溶化剤は、まるで「仲人役」や、水と油を混ぜる「界面活性剤」のような働きをします。相溶化剤の分子は、アロイを構成する両方のポリマーと親和性を持つ部分構造(例えば、一方のポリマーと相溶するブロックと、もう一方のポリマーと相溶するブロックを持つブロックコポリマーなど)を持っています。この相溶化剤が、非相溶なポリマー同士の界面に選択的に集まり、両者を繋ぎとめる「架け橋」となります。これにより、以下の効果が得られます。
界面接着力の向上: 界面での剥離を抑制し、応力伝達をスムーズにすることで、材料全体の強度、特に衝撃強度や靱性を向上させます。
分散相の微細化・安定化: 分散相(島)が凝集して粗大化するのを防ぎ、より微細で均一な分散状態を維持します。これにより、安定した物性発現に繋がります。
モルフォロジー制御: 海島構造だけでなく、共連続構造(両方の相が連続的につながった構造)など、目的に応じたモルフォロジー形成を助ける場合もあります。
この相溶化技術の進化が、高性能な非相溶型ポリマーアロイの開発を可能にしてきました。適切な相溶化剤の選定と添加量の最適化は、ポリマーアロイ設計における核心技術の一つです。
ポリマーアロイ化の目的とメリット
なぜわざわざ複数のポリマーを混ぜ合わせるのでしょうか? ポリマーアロイ化には、単一のポリマーでは得られない、数多くのメリットがあります。ここでは、その主な目的と利点について解説します。
単一材料では両立できない特性バランスの実現
これがポリマーアロイ化の最大の目的であり、最大のメリットと言えるでしょう。プラスチック材料の特性には、トレードオフの関係にあるものが少なくありません。例えば、以下のような組み合わせが代表的です。
剛性(硬さ)と靱性(粘り強さ、割れにくさ): 一般的に、材料は硬くすると脆くなり、粘り強くすると柔らかくなる傾向があります。
耐熱性と加工性(流動性): 耐熱性の高いポリマーは分子鎖の動きが制限されるため、溶融時の流動性が低く、成形が難しくなる傾向があります。
耐薬品性と耐衝撃性: 特定の薬品に強い構造を持つポリマーが、必ずしも衝撃に強いとは限りません。
ポリマーアロイ技術を用いることで、これらの相反する特性を、目標とするレベルでバランスさせることが可能になります。例えば、非常に高い剛性を持つが衝撃に弱いポリマーに、ゴム成分などの柔軟なポリマーを微分散させることで、剛性を維持しつつ耐衝撃性を大幅に改善することができます。このように、要求される性能に合わせて特性を「デザイン」できる点が、ポリマーアロイの大きな魅力です。
機械的特性の向上
エンプラが使用される用途、特に構造部品などでは、単に強度(引張強さ、曲げ強さなど)が高いだけでなく、衝撃に対する強さ(耐衝撃性)、長期間の荷重に対する変形のしにくさ(クリープ特性)、繰り返し荷重に対する耐久性(疲労特性)などが重要になります。
ポリマーアロイ化は、これらの機械的特性を総合的に向上させる有効な手段です。
高剛性・高靱性バランス: 前述の通り、硬さと粘り強さのバランスを最適化できます。例えば、ガラス繊維などで強化された高剛性ポリアミド(PA)に、特殊なエラストマー(ゴム状高分子)をアロイ化することで、衝撃に弱いというPAの弱点を克服し、自動車のエンジン周辺部品など、過酷な条件下で使用される部品への適用を可能にしています。
耐衝撃性の向上: 特に低温環境下での耐衝撃性(低温靱性)は、寒冷地で使用される製品にとって重要な特性です。特定のポリマー(例:ABS、エラストマー)をアロイ化することで、ベースとなるエンプラの低温脆性を改善できます。
クリープ特性、疲労特性の改善: アロイ化によって分子鎖の絡み合いや結晶構造を制御し、これらの長期的な信頼性に関わる特性を改善することも可能です。
耐熱性、耐薬品性、寸法安定性の向上
ポリマーアロイは、機械的特性だけでなく、他の重要な特性の改善にも貢献します。
耐熱性の向上: より高い耐熱性を持つポリマーをアロイ化することで、アロイ全体の耐熱性(荷重たわみ温度(HDT)や連続使用温度など)を引き上げることができます。例えば、比較的安価で加工性の良いポリマーに、少量の高耐熱ポリマーをアロイ化することで、コストを抑えつつ耐熱性を要求レベルまで向上させる、といったアプローチが可能です。
耐薬品性の向上: 特定の薬品(酸、アルカリ、油、溶剤など)に対する耐性は、ポリマーの化学構造に依存します。耐薬品性に劣るエンプラに、耐薬品性に優れたポリマーをアロイ化することで、その弱点を補うことができます。例えば、耐衝撃性に優れるが耐薬品性に劣るPC(ポリカーボネート)に、耐薬品性に優れるPBT(ポリブチレンテレフタレート)をアロイ化したPC/PBTアロイは、自動車の外装部品など、薬品(ワックス、洗浄剤など)に触れる可能性のある用途で広く使われています。
寸法安定性の向上(低吸水化): PA(ポリアミド)系エンプラのように吸水性が高い材料は、湿度環境によって寸法や物性が変化しやすいという課題があります。吸水性の低いポリマー(例:PPE(ポリフェニレンエーテル))とアロイ化することで、吸水率を低減させ、寸法安定性を向上させることができます。PA/PPEアロイなどがその代表例です。
ポリマーアロイの基本的な設計指針
ポリマーアロイは非常に有用な材料ですが、その性能を最大限に引き出すためには、適切な材料選定と設計への理解が不可欠です。ここでは、ポリマーアロイを活用する上での基本的な考え方について解説します。
ベース樹脂選定の考え方
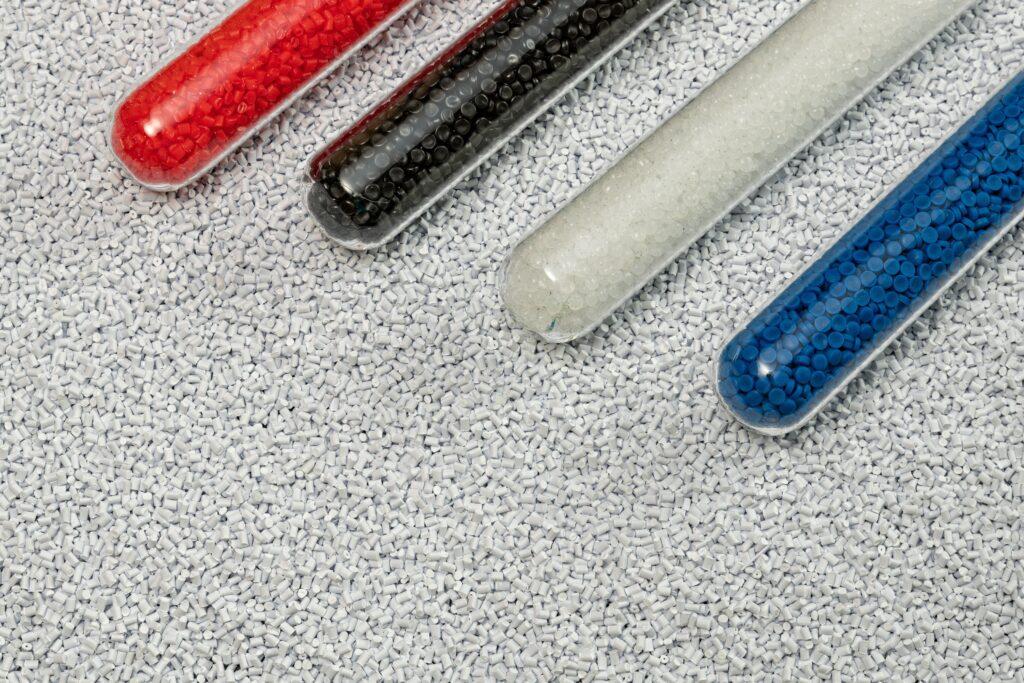
ポリマーアロイを設計・選定する際の出発点は、「どの特性を最も重視するか」を明確にすることです。要求される性能には様々なものがありますが、その中でも絶対に譲れないコアとなる特性があるはずです。ベースとなるポリマー(マトリックス相になることが多い)は、この最も重要な要求特性を持つものを選ぶのが基本です。例えば、高い耐熱性が最優先であれば、PPE、SPS、PEEKなどをベースに検討する。優れた耐薬品性が不可欠であれば、PBT、PPS、フッ素樹脂などをベースにする。コストと強度のバランスが重要であれば、PA、PCなどをベースに考える。
そして、そのベース樹脂が持つ弱点を補う形で、もう一方のポリマー(分散相となることが多い)や添加剤を選定していく、というアプローチが一般的です。例えば、耐熱性を重視してPPEをベースに選んだが、成形性が悪いという弱点がある場合、流動性に優れるPSやPAをアロイ化して成形性を改善する(PPE/PSアロイ、PPE/PAアロイ)、といった具合です。
単に高性能なポリマー同士を組み合わせれば良いというわけではなく、コスト、供給安定性、成形性なども考慮しながら、最適な組み合わせを見つける必要があります。
強化繊維や添加剤との組み合わせを考慮する場合
エンプラやポリマーアロイには、性能をさらに向上させる目的で、GF(ガラス繊維)やCF(炭素繊維)といった強化繊維、タルクやマイカなどの無機フィラー(充填材)、難燃剤、摺動性向上剤、耐候性安定剤などが添加されることが一般的です。ポリマーアロイにこれらの添加剤を配合する場合、アロイを構成する各ポリマーと添加剤との相性(親和性、界面接着性)を考慮することが非常に重要になります。
強化繊維の効果: 繊維とマトリックスポリマーとの界面接着性が低いと、せっかく強化繊維を配合しても十分な補強効果が得られません。ポリマーアロイの場合、繊維がどちらの相(マトリックス or 分散相)とより強く接着するかによって、最終的な物性が変わってくる可能性があります。
フィラーの分散性: フィラーが均一に分散せず、凝集したり偏ったりすると、強度低下や外観不良の原因となります。アロイのどちらかの相に選択的に偏在することもあります。
難燃剤の効果と物性低下: 難燃剤の種類によっては、ポリマーアロイの機械的特性や耐熱性を低下させる副作用を持つものがあります。難燃性と他の物性とのバランスを考慮した選択が必要です。
これらの添加剤は、ポリマーアロイの複雑な相構造(モルフォロジー)形成にも影響を与える可能性があります。単に混ぜ合わせるだけでなく、混練プロセスにおけるせん断力や温度条件なども含めて、添加剤がアロイ中でどのように分布し、相互作用するかを理解しておくことが、安定した品質を得るために重要です。
用途別に求められる特性とアロイの適合性
ポリマーアロイの選定・設計においては、最終製品がどのような用途で、どのような環境下で使用され、具体的にどのような性能が求められるのかを明確にすることが不可欠です。
以下に、用途例と求められる主な特性の考え方を示します。
OA機器の筐体(プリンター、PCなど)
要求特性:難燃性、剛性、寸法精度、耐衝撃性、良好な外観(塗装性)
アロイの考え方:PC/ABS(難燃グレード)、PPE/PS(難燃グレード)など。
電気・電子部品のコネクタ
要求特性:耐熱性、電気絶縁性、寸法安定性(低吸水性)、難燃性、強度
アロイの考え方:PBT/PC、PA/PPE、LCP(液晶ポリマー)ベースのアロイなど。
水回り部品(配管継手など)
要求特性:耐熱水性、耐薬品性、クリープ特性、強度
アロイの考え方:PPE/PS、PPSベースのアロイ、変性PPEなど。
ギアなどの摺動部品
要求特性:耐摩耗性、摺動性、強度、耐熱性
アロイの考え方:POMやPAをベースにPTFE(フッ素樹脂)やシリコーンオイルなどを配合・アロイ化したもの。
これらはあくまで一例であり、実際にはさらに細かな要求(色、コスト、環境規制対応など)が存在します。用途に応じて要求特性の優先順位をつけ、それに最も合致するポリマーアロイ材料を選択、あるいはカスタム設計していくプロセスが重要になります。