「樹脂が割れる(クラック)」本当の理由:靭性を高める材料・設計・成形
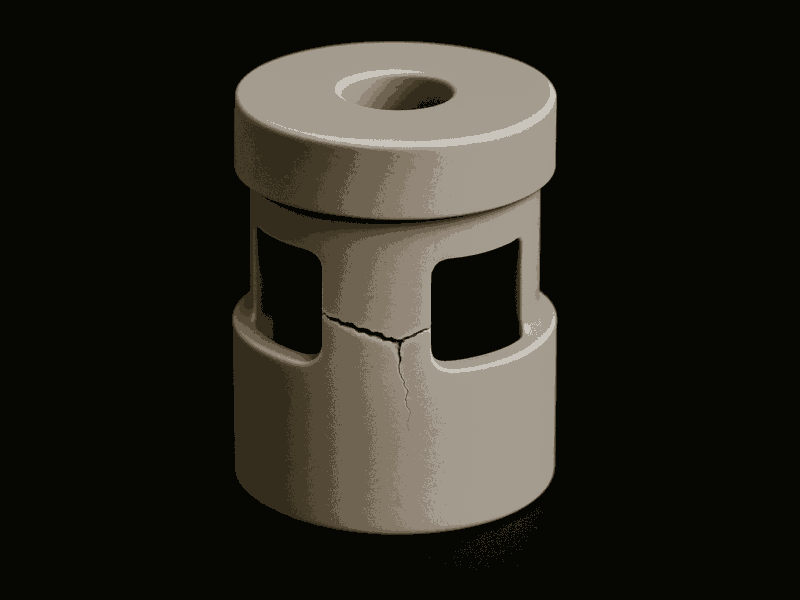
前編では、エンプラ部品が「割れる」メカニズムの基礎として、破壊のプロセスや壊れ方の違い、また「温度」「形状」「荷重速度」といった主な要因を解説しました。プラスチックの破壊は、材料の性質だけでなく、さまざまな外的要因が複雑に絡み合うことで起こる――それが現場で繰り返し目にする現実です。
私自身、材料メーカー在籍時に数多くのクラック分析を経験しましたが、その大半は「セオリーを正しく理解し、現場で再現できていない」ことが原因でした。逆に言えば、セオリーを正確に理解し、設計や成形に反映させることで、クラックの多くは確実に防ぐことができます。
後編では、設計者が最も気になる「どうすれば割れを防げるのか」という実践的な視点に立ち、破壊を防ぐ鍵となる「靭性(じんせい)」――すなわち材料の粘り強さや割れにくさを高めるための具体策を紹介します。材料選定、設計形状の工夫、成形プロセスのポイントという3つの側面から、信頼性の高い製品設計につながるノウハウをわかりやすくお伝えします。また、若手設計者が陥りやすい誤解とその対処法についても具体的に触れ、設計ミスによるトラブルを未然に防ぐ実践的なヒントをお届けします。
靭性を高める材料と設計の工夫
脆性破壊を防ぎ、部品の「割れにくさ」、すなわち「靭性」を高めるためには、どのようなアプローチがあるのでしょうか? 大きく分けて、「材料側の工夫」と「設計・成形側の工夫」があります。
材料側の工夫:より粘り強い材料を求めて
材料メーカーは、プラスチックの靭性を向上させるために、様々な技術開発を行っています。
– 靭性(高衝撃)グレードの開発: ベースポリマーの分子構造(分子量、共重合など)を工夫し、靭性を高めたグレードがあります。
– ポリマーアロイ化: 複数のポリマーを混ぜ合わせる(アロイ化)ことで、各々の長所を活かし、靭性を向上させます。代表例は、剛性と耐衝撃性のバランスが良いPC/ABSアロイです。
– ゴム(エラストマー)改質: プラスチック中に微細なゴム粒子を分散させる技術です。ゴム粒子がクラックのエネルギーを吸収し、靭性を大幅に向上させます。ゴム強化ナイロン(PA/エラストマー)などが代表的で、自動車バンパーなどに使われます。ゴム粒子の種類、サイズ、分散状態の制御が重要です。
これらの技術は、材料が本来持つ低いTg(低温での分子運動性)、柔軟な分子鎖、あるいはエネルギーを吸収する分散相(ゴム粒子など)といった要素を利用しています。ただし、一般に靭性を高めると、剛性や耐熱性が若干低下するトレードオフの関係にあることが多い点には注意が必要です。
強化繊維とのトレードオフ:強くなるけど脆くなる?
エンプラの強度・剛性を向上させる一般的な手法として、ガラス繊維(GF)や炭素繊維(CF)などの強化繊維を配合する繊維強化プラスチック(FRP)があります。これにより機械的特性は大幅に向上し、金属代替が可能になります。しかし、強度・剛性が向上する一方で、靭性(特に衝撃強度)は低下し、材料がより脆くなる傾向があることに注意が必要です。硬くて伸びにくい繊維がマトリックスの塑性変形を妨げ、エネルギー吸収能力を低下させてしまうためです。特に繊維量が多い高強度グレードほど、この傾向は顕著になります。
設計においては、高い剛性が必要な場合でも、繊維強化グレードを選択する際には、同時に衝撃強度などの靭性データも確認し、想定される衝撃荷重に対する耐性を評価する必要があります。「剛性を上げすぎたために、かえって衝撃で割れやすくなった」という失敗を避けるため、強度・剛性と靭性のトレードオフを常に意識しましょう。
成形時の応力残留を避ける:見えない「ひずみ」が破壊を招く
材料固有の特性だけでなく、射出成形プロセスも、最終製品の割れやすさに大きな影響を与えます。特に問題となるのが、成形品内部に残る「残留応力」です。これは、成形時の溶融樹脂の流動(分子配向)や、冷却固化時の不均一な収縮によって発生します。
分子配向: 樹脂が金型内を流れる際に分子が引き伸ばされて特定の方向に並び、固化後もその配向が残ると、内部応力や異方性の原因となります。
冷却ムラ: 特に肉厚が不均一な場合、表面と内部の冷却速度差により、引張応力や圧縮応力が残留します。
過剰な保圧: 樹脂の収縮(ヒケ)を補うための保圧が強すぎると、分子が無理に詰め込まれ、高い残留応力を生みます。
内部に残った残留応力は、外部から力が加わった際にそれに上乗せされる形で作用し、見かけ上の強度を低下させ、破壊を誘発しやすくします。また、残留応力はESC(環境応力割れ)の引き金にもなります。したがって、割れにくい製品を作るためには、材料選定や形状設計だけでなく、成形プロセスにおいても残留応力を可能な限り低減する工夫が重要です。適切なゲート設計、均一な肉厚設計、最適な成形条件(温度、圧力、時間など)の設定が求められ、成形メーカーとの連携が不可欠です。
設計段階での「靭性確保」の考え方
破壊メカニズムや割れの要因を踏まえ、設計段階で十分な「靭性」を確保するためには、どのような点に注意すべきでしょうか?
応力を分散させる形状の設計:力の流れを滑らかに
破壊の多くは応力集中箇所から始まります。設計の基本は、応力集中を極力避ける、あるいは緩和する形状を心がけることです。
– ノッチを避け、Rを付ける: 部品の内角や切り欠きの根元には、可能な限り大きなR(丸み)を付けます(推奨:R≧0.5t、tは肉厚)。Rが小さいほど応力集中は激しくなります。
– 肉厚の急変を避ける: 厚い部分から薄い部分へは、なだらかなテーパー形状で繋ぎます。
– リブやボスの根元にもR: 補強リブやボスの根元にも必ず適切なRを設けます。ピン角は厳禁です。
これらの形状的な配慮は、有限要素法(FEM)を用いた応力解析で効果を確認し、最適化することが有効です。設計初期段階で応力集中箇所を特定し、対策を打つことが重要です。
実環境と材料特性値を結びつける:カタログスペックの裏を読む
材料データシートの数値は、特定の条件下での値であり、そのまま実性能を保証するものではありません。特に靭性は温度や荷重速度に大きく依存するため、実使用環境を想定して特性値を解釈することが重要です。
– Tgと使用温度: 特に非晶性エンプラでは、使用温度範囲(特に最低温度)がTgに対してどのあたりかを確認します。Tg以下の低温では脆化リスクが高まります。
– 衝撃荷重の有無: 落下や衝突が想定される場合は、静的強度だけでなく衝撃強度(アイゾッド、シャルピー)データを重視します。ノッチ付きの値はノッチ感度の目安になります。
– 荷重速度の影響: 高速での衝突など、標準試験より速い荷重が加わる場合は、さらに脆くなる可能性を考慮します。
カタログスペックを鵜呑みにせず、測定条件を理解し、実際の使用環境(温度、荷重の種類・速度、形状効果など)で材料がどう振る舞うかを予測・評価する視点が不可欠です。
靭性評価と信頼性試験の導入:強度だけでは見えないもの
部品の「割れにくさ」を評価するには、「強度」データだけでは不十分です。「靭性」、すなわち破壊に至るまでのエネルギー吸収能力を評価することが重要になります。
衝撃試験の活用: アイゾッドやシャルピー衝撃試験は、材料の衝撃に対する粘り強さを評価する標準的な方法です。異なる温度でのデータを比較すれば、低温脆性も評価できます。
破壊靭性評価: より専門的な評価として、材料の亀裂進展抵抗力を定量的に測る方法もあります。
繰返し荷重試験(疲労試験): 繰り返し力がかかる部品では、疲労破壊に対する耐性(疲労強度)の評価が不可欠です。
実機評価・信頼性試験: 最終的には、試作品や実機を用いた信頼性試験(落下試験、振動試験、温湿度サイクル試験など)で、製品としての「割れにくさ」を検証することが最も重要です。
強度だけでなく、靭性、疲労、クリープといった特性、さらには実環境での挙動を多角的に評価する視点が求められます。
若手設計者が陥りやすい誤解と対処法
最後に、「割れ」に関する若手設計者が陥りやすい誤解と、それを避けるための考え方について触れます。
誤解①:「強度が高い材料ほど、割れにくい」→ NO!
「強度」と「靭性」は別物です。GF強化材のように強度・剛性が高くても、衝撃には脆くなることがあります。用途に応じてどちらが重要か判断が必要です。
誤解②:「剛性が高い材料ほど、丈夫で割れにくい」→ NO!
「剛性」は変形しにくさ(硬さ)であり、「割れにくさ(靭性)」とは直接関係ありません。高剛性材料は変形による応力緩和ができず、衝撃に脆いことがあります。剛性と靭性のバランスが重要です。
誤解③:「プラスチックは金属より弱いから、割れても仕方ない」→ NO!
「なぜ割れたのか」を追求する姿勢が重要です。プラスチックは条件次第で挙動が大きく変わる材料です。「条件次第で割れる」ことを前提に、破壊を防ぐ、あるいは被害を最小限にする設計思考が求められます。
設計初期から強度だけでなく靭性や破壊メカニズムを意識し、材料特性、力学、形状、環境を総合的に考慮する視点が、これらの誤解を避け、より良い設計に繋がります。
実際のクラック解決事例のご紹介
こちらは水中ポンプ用オイルケーシングのクラックの発生を解決した事例です。
元々、他社で成形されていた製品ですが、使用中にクラックが発生し、シール面の幾何公差が非常に厳しい仕様や、成形過程で充填が不均衡になることが原因でした。そこで当社では、クラックの再発を防ぐために成形プロセス全体を見直し、高い品質と信頼性を兼ね備えたオイルケーシングの提供を実現しました。詳細は下図ボタンよりご覧ください。
まとめ
今回のコラムでは、「樹脂が割れる」という現象の背景にある破壊メカニズム、脆性・延性という壊れ方の違い、そして割れを引き起こす主な要因(温度、形状、荷重速度)を解説しました。さらに、破壊を防ぐ鍵となる「靭性」を高めるための材料、設計、成形における工夫と考え方について述べました。「割れる」ことは物理現象ですが、それを「防ぐ」ことは設計思想そのものです。単に材料の強度や肉厚を上げるだけでは根本解決になりません。重要なのは、「なぜ、そこで、どのように割れるのか?」その理由を、材料特性、力学、形状、使用環境という多角的な視点から深く理解し、得られた知見を具体的な設計や材料選定、成形プロセスへとフィードバックしていくことです。応力集中を避ける形状、使用環境に適した靭性を持つ材料の選択、残留応力を低減する成形への配慮など、具体的な対策はすべて、この「割れる理由」の理解から始まります。
そして、靭性の確保は「材料」「設計」「成形」の三位一体で取り組むべき課題です。優れた材料も、不適切な設計や成形では性能を発揮できません。これらの要素が互いにどう影響し合うかを常に意識し、開発プロセス全体で最適化を図る視点が不可欠です。特にプラスチックの挙動は、温度や速度によって複雑に変化し、金属とは異なる注意が必要です。若手設計者の皆さんには、強度・剛性だけでなく、靭性や破壊といったテーマの背景にある原理を学び続けることをお勧めします。データシートを正しく読み解き、シミュレーションを活用し、時には実験で確かめる力を養うことが、将来の信頼性設計に繋がる確かな基盤となります。このコラムが、皆さんの「割れない」製品設計への取り組みを後押しし、プラスチック材料とのより良い付き合い方を考えるきっかけとなれば幸いです。