エンプラによる金属代替:射出成形が可能にする10の設計メリット
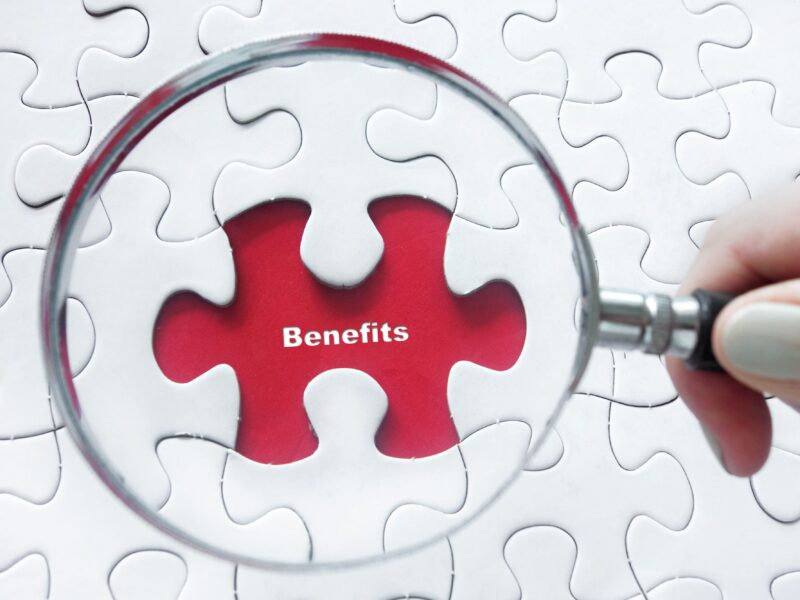
自動車の燃費向上、電子機器の軽量化、製造コストの削減、そして環境負荷の低減──。現代のものづくりにおいて、これらの要求はますます高まっています。こうした課題を解決する有効な手段の一つとして、「金属部品の樹脂化」、特にエンジニアリングプラスチック(エンプラ)を用いた射出成形による金属代替が大きな注目を集めています。しかし、ここで重要なのは、金属代替は単に材料を置き換えるだけではない、ということです。鉄やアルミなどの金属と、エンプラでは、材料特性も最適な加工方法も全く異なります。金属の設計思想のまま材料だけをエンプラに変えても、期待した性能が得られなかったり、かえってコストが上がってしまったりすることもあります。
射出成形による金属代替を成功させる鍵は、「設計と生産の再設計」という視点を持つことです。エンプラと射出成形の特性を深く理解し、そのメリットを最大限に引き出す設計を行うことで、単なる材料置換を超えた、製品価値の向上や新たな可能性が生まれます。
本コラムでは、設計者の皆様が金属代替を検討する際の第一歩として、射出成形ならではのメリットを10の視点から具体的に解説します。これは、既存の設計を見直し、より付加価値の高い製品を生み出すためのヒントとなるはずです。
軽量化と取り扱い性向上:製品価値を高める基本性能
金属代替を検討する最も大きな動機の一つが「軽量化」です。エンプラの比重は、一般的に鉄(約7.8)やアルミニウム(約2.7)と比較して1.0~1.5程度と非常に小さく、劇的な軽量化を実現できます。
輸送コストの削減
製品単体の重量が軽くなることで、輸送時のエネルギー消費量やコストを削減できます。特に、自動車や航空機などの輸送機器においては、燃費向上に直結する重要な要素です。部品単体だけでなく、製品全体のライフサイクルにおけるCO2排出量削減にも貢献します。
組立時の作業性・安全性向上
部品が軽くなることで、組立ラインでの作業者の負担が軽減され、作業効率や安全性が向上します。特に、大型の部品や、頻繁に取り扱う部品においてその効果は顕著です。ロボットによる自動組立においても、可搬重量の制約緩和につながります。
重量バランス最適化
医療機器や精密機器、ロボットアームの先端部品など、製品の重心位置や慣性モーメントが性能を左右する分野では、軽量化による重量バランスの最適化が可能です。これにより、操作性の向上や応答速度の改善、駆動モーターの小型化といったメリットが生まれます。
軽量化は、単に「軽くなる」だけでなく、エネルギー効率、作業性、安全性、そして製品の基本性能向上に繋がる、金属代替の基本的な、そして非常に大きなベネフィットなのです。設計段階からエンプラの比重を考慮し、軽量化効果を最大限に引き出す形状を検討することが重要です。
設計自由度の向上:金属加工の制約からの解放
金属加工は、板金プレス、切削、鋳造、鍛造など様々な方法がありますが、それぞれに形状的な制約が存在します。例えば、板金では複雑な三次元曲面の成形が難しく、切削では加工時間やコストがかさみます。一方、射出成形は、溶融した樹脂を金型内に高圧で射出・充填し、冷却固化させる工法です。金型さえ製作できれば、非常に複雑な形状でも比較的容易に、かつ高い生産性で再現できます。
複雑形状・アンダーカット・3D曲面の実現
金属では複数部品の組み合わせや特殊な加工が必要だった滑らかな三次元曲面、内部に凹凸を持つアンダーカット形状(金型のスライド機構などを利用)なども、射出成形なら一体で成形可能です。これにより、意匠性の高いデザインや、機能性を追求した形状が実現しやすくなります。
樹脂ならではの機能形状の付与
射出成形では、補強のための「リブ」や、ねじ止め・位置決め用の「ボス」、部品同士をはめ合わせる「スナップフィット」といった、樹脂設計特有の機能形状を容易に盛り込めます。これらは金属設計の考え方とは異なりますが、部品点数の削減や組立性の向上に大きく貢献します。
エンプラの材料特性と射出成形のプロセス特性を理解することで、従来の金属加工の制約から解放され、より自由な発想で、機能的かつ合理的な設計を行うことが可能になります。
組立工数・部品点数の削減:一体成形による生産革新
設計自由度の向上とも密接に関連しますが、射出成形による金属代替は、組立工程の劇的な簡略化をもたらします。金属の場合、複数の板金部品を溶接したり、切削部品をネジで締結したりと、多くの部品と組立工程が必要になるケースが少なくありません。射出成形では、これらの複数部品の機能を一つの樹脂部品に集約する「一体成形」が可能です。
アセンブリ統合によるメリット
例えば、従来は金属板のブラケットに、スペーサーとなるボスを溶接し、さらにナットを圧入していた部品があったとします。これをエンプラの射出成形で設計し直せば、ブラケット形状とボス形状を一体で成形し、必要であればインサートナットを同時に成形することも可能です(インサート成形)。これにより、部品点数は3点から1点に削減され、溶接や圧入といった組立工程も不要になります。
コスト削減と品質向上
部品点数と組立工数が削減されれば、直接的なコストダウンはもちろん、部品在庫管理の手間、組立ラインのスペース、組立不良のリスクも低減できます。また、一体成形によって部品間の締結箇所が減るため、組立精度が向上し、製品全体の品質安定にも繋がります。
金属代替を検討する際は、「この機能とこの機能は一体化できないか?」という視点で既存設計を見直すことが、大きなコスト削減と生産性向上に繋がる鍵となります。
優れた耐環境性:錆・腐食の問題を解決
金属部品の大きな弱点の一つが「錆」や「腐食」です。特に水や薬品にさらされる環境、湿度の高い環境では、防錆処理や定期的なメンテナンスが不可欠となり、コストや手間がかかります。エンプラの多くは、金属と比較して優れた耐食性・耐薬品性を持っています。
多様な環境への適用
例えば、POM(ポリアセタール)やPPS(ポリフェニレンサルファイド)、PEEK(ポリエーテルエーテルケトン)といったエンプラは、耐薬品性や耐加水分解性に優れており、ポンプ部品、バルブ、医療機器、食品機械など、水や薬液、蒸気に触れる過酷な環境でも使用されています。材料を適切に選定することで、これまで金属では対応が難しかった用途への展開も可能になります。
表面処理・防錆剤の不要化
樹脂化により、メッキや塗装といった防錆のための表面処理工程や、防錆剤の塗布といった手間が不要になります。これにより、コスト削減はもちろん、表面処理工程で発生する可能性のある環境負荷物質の削減にも繋がります。
ただし、エンプラの種類によって耐薬品性や耐候性は大きく異なるため、使用環境を十分に考慮した材料選定が不可欠です。薬品の種類、濃度、温度、紫外線暴露の有無などを明確にし、最適なエンプラを選択することが重要です。
表面処理レスの実現(無塗装化):外観品質と環境対応の両立
製品の外観品質を高めるために、金属部品には塗装やメッキなどの表面処理が施されることが一般的です。しかし、これらの工程はコストがかかるだけでなく、VOC(揮発性有機化合物)の排出など、環境負荷の観点からも課題があります。射出成形では、材料自体に着色顔料を練り込んだ「着色ペレット」を使用することで、成形と同時に部品に色を付けることができます。
成形段階での外観仕上げ
材料着色により、塗装工程そのものを省略できます。また、金型表面に微細な凹凸模様(シボ加工)を施すことで、成形品表面にレザー調、梨地調、木目調といった様々な質感やデザインを付与することも可能です。これにより、塗装では表現が難しい意匠性の実現や、指紋・傷の目立ちにくさといった機能的なメリットも得られます。
コスト・環境負荷の低減
塗装工程が不要になることで、塗料コスト、塗装設備費、乾燥時間、マスキングの手間などが削減されます。同時に、VOC排出量の削減や、塗料スラッジなどの廃棄物削減にも繋がり、環境負荷低減に大きく貢献します。また、成形色がそのまま製品色となるため、使用中の傷による塗装剥がれといった問題も起こりません。
外観部品の金属代替においては、単に形状を再現するだけでなく、着色やシボ加工といった射出成形ならではの加飾技術を活用することで、コスト、品質、環境対応のすべてにおいてメリットを享受できます。
二次加工の排除:成形プロセスで機能を完結
金属部品の場合、基本的な形状を作った後に、ネジ穴を開ける(タッピング)、バリを取る、曲げ加工を行うなど、多くの二次加工が必要となることが一般的です。これらの工程は、加工時間、コスト、そして精度のばらつき要因となり得ます。射出成形では、これらの二次加工で付与していた機能を、成形プロセスの中で同時に作り込むことが可能です。
機能形状の一体成形
ネジ止めが必要な箇所には、タッピング不要のセルフタップ用ボス形状や、インサートナットを埋め込むためのポケット形状を設計段階で盛り込めます。また、部品同士の位置決めピンや、配線・配管を固定するためのクリップ受け、シール材をはめ込むための溝なども、金型で形状を作り込むことで、後加工なしに実現できます。
工程短縮と精度向上
二次加工が不要になることで、工程全体のリードタイムが短縮され、加工コストも削減されます。また、二次加工による位置ずれや寸法誤差のリスクがなくなり、部品精度、ひいては製品全体の組立精度が向上します。
設計段階で、最終製品に必要な機能を洗い出し、「射出成形でどこまで作り込めるか」を検討することで、生産プロセス全体の効率化と品質向上を図ることができます。
絶縁性とノイズ対策:電気・電子分野での優位性
金属が導電体であるのに対し、ほとんどのエンプラは電気絶縁性に優れています。これは、電気・電子機器の分野において大きなメリットとなります。
安全性の確保と設計の簡略化
金属製の筐体や部品の場合、意図しない箇所での短絡(ショート)を防ぐために、絶縁シートを挟んだり、部品間に十分な空間距離(沿面距離・空間距離)を確保したりする必要があります。エンプラ部品であれば、材料自体が絶縁性を持つため、このような配慮が簡略化され、設計の自由度が高まります。感電防止など、安全性の向上にも貢献します。
ノイズ対策における役割
電子機器におけるノイズ対策では、不要な電磁波を遮断するために金属製のシールドケースなどが用いられます。一方で、部品自体がノイズ源とならないように、あるいはノイズの影響を受けにくいように、絶縁性の高いエンプラ部品を効果的に配置することも重要です。金属シールドと絶縁性エンプラ部品を適材適所で使い分けることで、効果的なノイズ対策設計が可能になります。
ただし、静電気対策が必要な場合には、導電性フィラーを配合したエンプラ材料も存在します。用途に応じて適切な電気特性を持つ材料を選択することが重要です。
潤滑レス設計・メンテナンスフリー:クリーンで手間いらず
機械部品、特に摺動部(すべり運動する部分)を持つ部品では、摩耗や焼き付きを防ぐために潤滑油やグリスが不可欠です。しかし、定期的な給油作業は手間がかかり、油が周囲に飛散することで汚染の原因にもなります。エンプラの中には、優れた自己潤滑性を持つものが存在します。
オイルフリー化の実現
POM(ポリアセタール)や、PTFE(ポリテトラフルオロエチレン)を配合したコンパウンド材料、摺動グレードのPA(ポリアミド、ナイロン)などは、金属や他の樹脂との組み合わせにおいて、潤滑剤なしでも低い摩擦係数と優れた耐摩耗性を示します。これらのエンプラを歯車や軸受、カムなどの摺動部品に適用することで、給油が不要な「潤滑レス設計」が可能になります。
クリーン環境・メンテナンスフリー
潤滑油を使わないため、油による汚染の心配がなく、食品機械や医療機器、クリーンルーム内で使用される装置など、清浄度が要求される分野に最適です。また、定期的な給油メンテナンスが不要になるため、メンテナンスフリー化を実現し、製品のライフサイクルコストを低減できます。
ただし、摺動部品の設計においては、相手材との相性、面圧、摺動速度、使用温度などを考慮し、適切な材料選定と形状設計(摩耗や発熱への配慮)が必要です。
振動吸収性・減衰性:静音化と信頼性向上
金属は叩くとキーンと響くように、一般的に振動を伝えやすく、特定の周波数で共振しやすい性質があります。一方、エンプラを含む多くの樹脂材料は、材料内部でのエネルギー損失(内部摩擦)が大きく、振動を吸収・減衰させる効果が高いという特長があります。
静音化への貢献
この特性を利用することで、製品の動作音を低減する「静音化設計」が可能になります。例えば、金属製ギアをエンプラ製ギアに置き換えることで、噛み合い音や打撃音を大幅に低減できます。また、モーターやファンなどの振動源を覆うカバーや筐体にエンプラを用いることで、振動の伝達を抑え、騒音レベルを下げることができます。オフィス機器、家電製品、自動車の内装部品など、静粛性が求められる製品において非常に有効なアプローチです。
信頼性・耐久性の向上
振動は、騒音だけでなく、部品の疲労破壊や、ネジ・ボルトの緩みの原因にもなります。エンプラの振動減衰性は、これらの振動に起因する問題を抑制し、製品の信頼性や耐久性を高める効果も期待できます。衝撃吸収性に優れる材料もあり、落下衝撃などから内部部品を保護する目的でも利用されます。防振ゴムの代替や、ダンパー部品としての活用も可能です。
設計上のポイント
エンプラの種類によって振動減衰性のレベルは異なります。一般的に、柔軟なエラストマーなどは高い減衰性を示しますが、ガラス繊維などで強化された硬いエンプラは、金属に近い挙動を示す場合もあります。また、部品の形状(リブの配置や肉厚など)も振動特性に影響を与えるため、材料選定と合わせた設計的な配慮が必要です。
製品の付加価値として「静かさ」や「低振動」が求められる場合、エンプラの振動吸収性・減衰性は、金属代替を検討する上で見逃せない重要なメリットとなります。
コスト削減:トータルコストで考える優位性
金属代替によるコスト削減効果を考える上で重要なのは、「トータルコスト」の視点です。
エンプラの材料単価は、汎用的な鉄鋼材料などと比較すると高価な場合があります。しかし、これまで述べてきた様々なメリットを考慮すると、製品ライフサイクル全体で見たトータルコストでは、射出成形による樹脂化が優位になるケースが多くあります。
工程短縮と量産効果
射出成形は、複雑形状の一体成形や二次加工の排除により、加工工程数と組立工数を大幅に削減できます。これにより、人件費、設備費、管理費などが低減されます。また、射出成形は一度金型を作れば、高速かつ自動で大量生産が可能であり、量産性が非常に高い工法です。生産数量が多いほど、一個あたりのコストは劇的に下がります。
軽量化による間接コスト削減
軽量化による輸送コストの削減や、メンテナンスフリー化による維持管理コストの削減も、トータルコスト低減に寄与します。
初期投資と柔軟な対応
金型製作には初期投資が必要ですが、量産効果によって十分に回収可能です。また、近年では、製品ライフサイクルの短期化に対応するため、比較的安価で製作期間の短い「簡易金型」を用いた小〜中量生産や、3Dプリンターによる試作・検証を組み合わせることで、開発リードタイムの短縮とリスク低減を図るアプローチも広がっています。
材料費だけで判断するのではなく、設計、製造、組立、輸送、メンテナンスといった、製品に関わるあらゆる工程とコスト要素を総合的に評価することが、金属代替の費用対効果を正しく判断する上で不可欠です。
まとめ:金属代替は、設計の再構築による価値創造
射出成形によるエンプラを用いた金属代替は、単に重い材料を軽い材料に置き換えるだけの作業ではありません。それは、射出成形という生産プロセスとエンプラという材料の特性を最大限に活かすための「設計の再構築」であり、製品に新たな価値を与えるチャンスです。
軽量化、複雑形状の実現、部品点数削減、耐環境性の向上、加飾の自由度、二次加工レス、絶縁性、潤滑レス、振動吸収性、そしてトータルコストの削減──。この10のメリットは、それぞれが独立しているのではなく、互いに関連し合っています。
設計者の皆様には、金属での設計が当たり前だと思っていた部品に対しても、「射出成形ならもっと良くできるのではないか?」という視点をぜひ持っていただきたいと思います。そのためには、エンプラの材料特性と射出成形のプロセスを深く理解することが第一歩となります。今回のコラムでご紹介した10のメリットを参考に、ぜひ既存製品の改善や新製品開発において、射出成形による金属代替の可能性を追求してみてください。それはきっと、お客様にとっても、そして自社の競争力向上にとっても、大きな価値を生み出すきっかけとなるはずです。