乾燥を制する者は成形を制す:エンプラ射出成形における乾燥の重要性
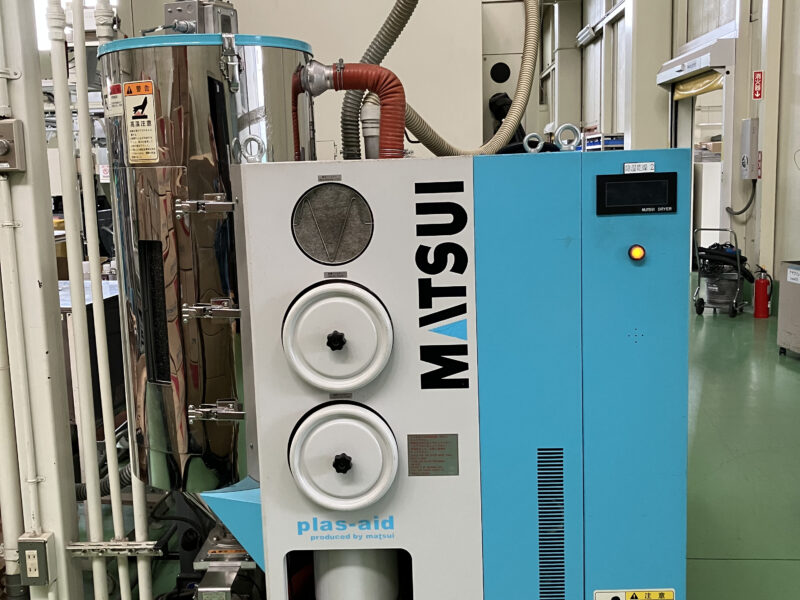
エンジニアリングプラスチック(エンプラ)を用いた射出成形において、材料の「乾燥」工程は、製品の品質を左右する極めて重要なプロセスです。しかし、その重要性が見過ごされたり、管理が不十分であったりする事例を聞くこともしばしばあります。エンプラの多くは吸湿性を持ち、乾燥が不十分なまま成形すると、外観不良、強度低下、寸法不安定といった様々な問題を引き起こし、製品の信頼性を著しく損ないます。一方で、「しっかり乾燥させれば良い」という単純な話でもなく、過度な乾燥は材料の劣化や別の成形不良を招くこともあります。
本コラムでは、まず「なぜエンプラの乾燥が必要なのか」を分子レベルの化学的視点から解説します。次に、乾燥不足や過乾燥が具体的にどのような成形不良を引き起こすのか、代表的な事例を整理。そして、トラブルを未然に防ぎ、常に安定した高品質な成形品を得るために、適切な乾燥条件の設定や管理方法、現場で起こりがちなミスとその対策について、実務的な観点から具体的な指針を示します。エンプラのポテンシャルを最大限に引き出し、歩留まり向上と品質安定化を実現するための「乾燥管理」の要点を、本コラムを通じて明確にしていきましょう。
なぜ乾燥が必要か?
エンプラの多くが乾燥を必要とする根源的な理由は、その分子構造と水分子との化学的な親和性、そして成形時の高温が引き起こす「加水分解」という劣化反応にあります。
多くのエンプラ、例えば、PA(ポリアミド、ナイロン)、PBT(ポリブチレンテレフタレート、PC(ポリカーボネート)、PES(ポリエーテルサルホン)などは、その主鎖や側鎖に酸素原子(O)や窒素原子(N)を含む官能基を持っています。代表的なものとして、PAのアミド結合(-CO-NH-)、PBTやPCのエステル結合(-CO-O-)やカーボネート結合(-O-CO-O-)が挙げられます。これらの官能基は、構成原子の電気陰性度の違いから分極しており(例えば、C=O結合では酸素原子がわずかに負に、炭素原子がわずかに正に帯電)、極性を有します。一方、水分子(H₂O)もまた、酸素原子と水素原子の電気陰性度の差により、酸素側が負に、水素側が正に分極した極性分子です。
このため、極性官能基を持つエンプラは、同じく極性分子である水分子と電気的な引力(分子間力の一種である水素結合や双極子-双極子相互作用)によって引き合いやすく、大気中の水分を容易に吸着・吸収します。これが「吸湿」です。吸着水(表面付着水)は比較的除去しやすいものの、ポリマー内部に浸透し、極性官能基と水素結合を形成した「結合水(吸収水)」は、より強固に保持されるため、除去には適切な熱と時間が必要となります。
問題は、これらの水分が残留したまま材料が射出成形機に投入され、シリンダー内で200℃~400℃といった高温にさらされた時に起こります。この高温環境下では、水分子がポリマー鎖中の特定の結合点を攻撃し、化学的に切断してしまう「加水分解」が活発に進行します。
PA(ポリアミド、ナイロン)
PAの主鎖を形成するアミド結合(-CO-NH-)は、高温の水分子によって攻撃を受けます。具体的には、水分子の酸素原子がアミド結合のカルボニル炭素(C=Oの炭素)に求核攻撃し、続いてプロトン移動が起こることで、結合が開裂し、カルボン酸末端(-COOH)とアミン末端(-NH₂)を生成します。この反応は、ポリマー鎖が短くなることを意味し、結果として分子量が著しく低下します。分子量が低下すると、分子鎖同士の絡み合いが減少し、材料の粘り強さ(靭性)や機械的強度が大幅に損なわれます。
R₁-CO-NH-R₂ + H₂O → R₁-COOH + H₂N-R₂
PC(ポリカーボネート)
PCの主鎖を形成する炭酸エステル結合(-O-CO-O-)も同様に加水分解の影響を受けます。高温下で水分子が炭酸エステル結合のカルボニル炭素に求核攻撃し、結合が切断されると、ヒドロキシ末端(-OH)を持つフェノール化合物と、もう一方のヒドロキシ末端、そして二酸化炭素(CO₂)ガスが生成されます(反応経路は複数あり、pHなどによっても変わります)。PAと同様に分子量が低下し、機械的特性が劣化するだけでなく、発生したCO₂ガスは成形品内部にボイドを形成したり、シルバーストリークとして表面に現れたりする原因となります。また、分解生成物であるフェノール類は、さらなる酸化反応や着色を引き起こす可能性もあります。
このように、水分は単に「湿っている」という状態以上に、成形プロセスにおいてポリマーを化学的に「攻撃」し、その構造と特性を根本から変えてしまうのです。この不可逆的な化学変化を防ぐために、成形前の徹底した乾燥が不可欠となります。
乾燥不足で起こる代表的な成形不良
エンプラの乾燥が不十分な場合、加水分解による分子レベルでの劣化が引き金となり、成形品には様々な不良現象が現れます。これらは外観、機械的特性、寸法安定性の全てに悪影響を及ぼします。
外観不良
シルバーストリーク(銀筋): 材料中の水分が気化し、樹脂の流れに沿って表面に銀白色の筋状模様として現れます。外観を損なうだけでなく、強度低下の原因にもなります。
ウェルドライン部の強度低下と割れ: 分子量低下によりウェルドライン部での樹脂融着が不完全になり、強度が著しく低下。使用中に割れや破損が発生するリスクが高まります。
ボイド・気泡: 水分が気化したガスが成形品内部に閉じ込められ、空隙を形成。内部欠陥として強度や絶縁性に影響します。
表面光沢の悪化・曇り: 分解ガスを巻き込んだり、均一な充填が妨げられたりすることで、表面光沢が失われたり、曇った外観になったりします。
機械的特性の低下
分子量低下による脆性破壊: 材料の粘り強さ(靭性)が失われ、衝撃強度が著しく低下。わずかな衝撃で簡単に割れたり欠けたりします。
クリープ耐性の劣化: 分子鎖の絡み合いが減少し、クリープ変形(時間経過に伴う変形)が起こりやすくなります。長期間荷重がかかる部品では、早期にたわんだり緩んだりする可能性があります。
長期使用中の割れ・破断トラブル: 初期特性のわずかな低下でも、長期的な応力や過酷な環境下で影響が顕在化。疲労破壊の起点や環境ストレスクラック(ESC)の感受性を高め、製品寿命を縮めます。
寸法安定性の低下
成形後の吸湿・放湿による寸法変動: 乾燥不足の部品は成形直後の含水率が不安定なため、その後の環境変化による寸法変動の予測が困難になります。特にPA系材料は吸水による寸法変化が大きく、乾燥不足ではこの変化量がさらに増大します。精密な嵌合部品で組付け不良や動作不良を引き起こすことがあります。
これらの不良は単独または複合的に発生し、製品価値を著しく低下させるため、乾燥管理は必須です。
過乾燥も要注意
エンプラの成形において乾燥は重要ですが、「乾燥させればさせるほど良い」わけではありません。「過乾燥」も材料の劣化や別の成形不良を引き起こします。
過乾燥による材料の劣化
酸化劣化・変色
特にPC(ポリカーボネート)やPPSU(ポリフェニルサルホン)のような芳香族ポリマーは、高温で長時間、酸素(空気)にさらされると酸化劣化を起こしやすくなります。これは、ポリマー鎖中の特定の部位(例えば、ベンゼン環に結合したメチレン基や、エーテル結合など)が、熱と酸素の作用によってラジカル化し、連鎖的な酸化反応が進行する現象です。この結果、発色団(光を吸収して色を呈する化学構造)が生成され、材料が黄変したり茶褐色に変色したりします。さらに深刻なのは、酸化によってポリマー主鎖が切断されたり、あるいは架橋構造が形成されたりすることで、機械的物性(靭性の低下、脆化など)や流動性が変化してしまう点です。推奨される乾燥温度や時間を大幅に超えると、この酸化劣化が顕著になります。
熱分解
たとえ酸素が存在しなくても、極端に高い温度(材料の分解温度に近い温度)で長時間加熱すると、ポリマー鎖を構成する共有結合そのものが熱エネルギーによって切断される「熱分解」が起こります。これは、分子振動が激しくなり、結合エネルギーを超えることで発生します。熱分解によって分子量が低下すると、材料の粘度が著しく低下し、成形時にバリが発生しやすくなったり、機械的強度が大幅に低下したりします。また、熱分解によって低分子量の揮発性物質が生成され、これがガスとなって成形不良(シルバーストリークやボイド)の原因となることもあります。過乾燥は、必ずしも材料の分解温度に達していなくても、長時間高温にさらすことで、部分的な熱分解を促進する可能性があります。
加工時流動性の変化・ゲート白化
前述の酸化劣化や熱分解がわずかに進行しただけでも、成形時の溶融粘度に影響が出ることがあります。分子量低下は一般的に流動性を向上させますが、一部の材料では分解生成物が架橋反応(分子鎖同士が結合する反応)を起こし、逆に流動性が低下(ゲル化)することもあります。また、特にPCなどで見られるゲート白化は、過乾燥によって材料がわずかに脆化し、射出時の高いせん断応力や急激な圧力変化によってゲート部で微細なクラック(クレーズ)が発生しやすくなるために起こると考えられています。
静電気・ブリッジ・ホッパートラブル
帯電と粉化によるフィーダー詰まり
過乾燥で静電気が発生しやすくなり、帯電したペレットがホッパーや輸送ラインに付着。また、ペレット表面が脆化・粉化し、フィーダー詰まりの原因となります。
ブリッジ現象の発生
ホッパー内でペレット同士がアーチ状に固まり、スムーズな供給を妨げるブリッジ現象を助長。ショートショットや計量不安定に繋がります。
過乾燥は材料を化学的に劣化させるだけでなく、物理的なハンドリング性も悪化させます。
適切な乾燥条件とは?
エンプラの乾燥不足も過乾燥も避けるには、各材料に最適な「適切な乾燥条件」の遵守が不可欠です。これは主に「乾燥温度」「乾燥時間」「露点」の3要素で規定され、材料メーカーの推奨値を基準とします。
材料ごとの適正乾燥条件(温度・時間・露点)
材料メーカーは各グレードの推奨乾燥条件を提供しています。例として、PPSU:150℃×4時間、PBT:120℃×4時間、PC:120℃×5時間などがありますが、必ず使用材料の推奨値を確認してください。特に「露点」管理が重要で、多くのエンプラでは-30℃以下の低露点空気が推奨されます。
乾燥装置の種類と選定
熱風乾燥機: 構造がシンプルで安価ですが、外気湿度に影響されやすく、露点管理はできません。
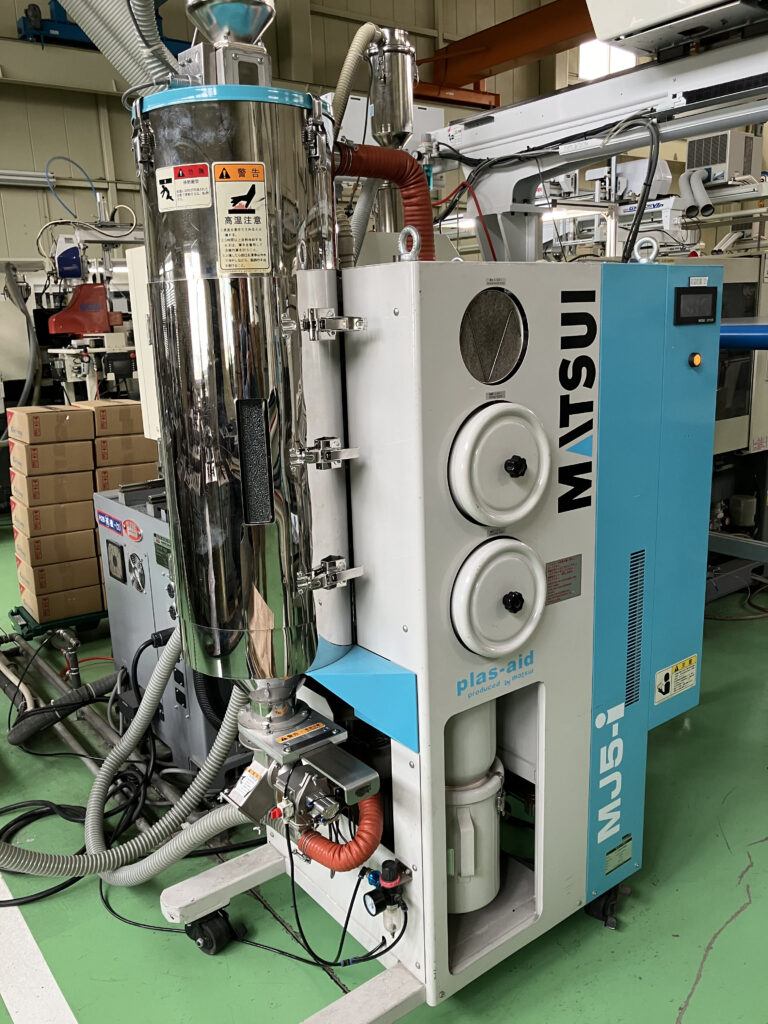
除湿乾燥機: 吸湿剤で低露点の乾燥空気を生成。外気の影響を受けにくく、安定した乾燥が可能で、エンプラ成形にはこちらが推奨されます。当社では主に除湿乾燥機を稼働させています。精密な乾燥管理が求められるエンプラ・スーパーエンプラ向けに、安定した低露点エアを連続供給できるハニカムローター式の除湿乾燥機を標準設備と位置付けています。これにより材料の特性を最大限に活かした成形と、材料の吸湿に起因する成形不良を抑制し、高品質な製品の安定供給に努めています。
真空乾燥機: 低温で水分を蒸発させるため熱に敏感な材料に適しますが、バッチ処理です。
エンプラの安定成形には、露点管理が可能で連続的に安定した乾燥空気を供給できる除湿乾燥機の導入が望ましいとされています。
含水率の測定方法
乾燥が適切に行われているかを確認するには、乾燥後のペレット含水率の実測が確実です。
– 赤外線水分計: 簡便・迅速ですが、揮発性成分もカウントする可能性があります。
– カールフィッシャー法水分計: 微量水分も精密に測定可能で、エンプラの含水率管理には最も信頼性が高い方法です。
日常的には乾燥機の露点・温度を監視しつつ、定期的にカールフィッシャー法などで実測値を確認し、乾燥プロセスの妥当性を検証することが理想的です。
現場でよくある乾燥ミスとその対策
適切な知識があっても、現場では人的ミスや管理不備から乾燥不良が発生します。
乾燥時間が不足: 生産計画変更や油断で規定時間を待たずに使用。
材料温度が不足: 乾燥機の能力不足、故障、センサー不具合で設定温度まで加熱されず。
乾燥済み材料の再吸湿: ライン停止中や材料交換時に大気に触れ、再吸湿。
乾燥機の露点異常に未対応: 露点計の異常を放置し、乾燥不良の材料を使用。
材料変更時の乾燥条件未変更: 材料替えの際、前の材料の条件のまま乾燥。
対策と管理手順
乾燥完了確認システムの導入: タイマーや表示札、自動記録システムで管理。
実温度の監視と検証: 複数箇所の温度センサー設置や携帯型温度計での実測。
再吸湿防止策の徹底: 長時間停止時は材料を密閉容器に戻す、大気開放時間を最小限にする。
乾燥装置の定期的なメンテナンスと校正: 露点計の校正、フィルター清掃・交換。
作業標準の整備と教育訓練: 材料ごとの乾燥条件を明記した標準書の作成・掲示、作業者教育の徹底。
これらの対策を地道に実行し、現場の管理体制を強化することが乾燥ミスを防ぐ鍵です。
まとめ
エンプラの射出成形品質は、「乾燥に始まり、乾燥に終わる」と言っても過言ではありません。乾燥管理の軽視は、外観、強度、寸法、信頼性すべてに悪影響を及ぼします。目に見えない水分が、成形プロセス中の高温下でポリマーを分子レベルから劣化させ、様々なトラブルを引き起こすのです。本コラムで解説したように、乾燥不足も過乾燥も避け、各材料の特性を理解し、適切な乾燥条件(温度・時間・露点)を厳密に守ることが重要です。そのためには、材料の化学的挙動の理解と、乾燥装置の適切な運用、含水率測定、現場での作業標準徹底といった実務的な管理体制の両立が不可欠となります。材料特性と適切な乾燥条件を熟知した成形メーカーとの連携は、ロスを防ぎ、品質を安定化させるための確実な道筋です。乾燥に関連する品質問題でお困りでしたら、当社までお気軽にご相談ください。