エンプラの「摺動性」入門(前編):基礎知識と材料選定の指針
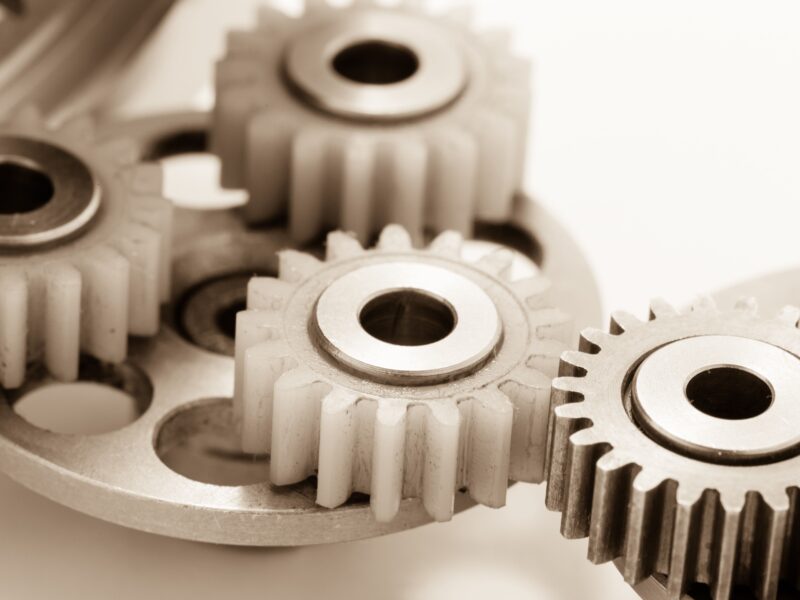
私たちの身の回りにある多くの工業製品は、部品同士が接触しながら滑らかに動くことで、その機能を発揮しています。この「滑らかに動く」という性能の鍵を握るのが「摺動性(しゅうどうせい)」です。特に、軽量化や複雑形状の実現、錆びないといった利点から多用されるエンジニアリングプラスチック(エンプラ)において、摺動性は部品設計の重要なテーマの一つと言えるでしょう。本稿では、このエンプラの摺動性について、前編・後編の2回にわたり、基礎的な知識から材料選定、設計・成形のポイント、そして一般的なトラブルとその対策の糸口までを解説していきます。前編となる今回は、摺動性の基本的な概念と、摺動性に優れた代表的なエンプラ、そして材料を選定する上での基本的な考え方を中心に述べます。
摺動性を理解する:その定義と重要性
まず、「摺動」とは、物体同士が接触しながら相対的に滑り動く現象を指します。そして「摺動性」とは、この動きをいかに円滑に、かつ長期間安定して維持できるかを示す材料や部品の性質を意味します。この摺動性を評価する上で重要な要素は、主に以下の2点です。
摩擦係数の小ささ(滑りやすさ)
物体が滑る際の抵抗が少ないことを示します。摩擦係数が小さいほど、小さな力で動かすことができ、動作時のエネルギー損失や不要な発熱を抑制できます。
耐摩耗性の高さ(すり減りにくさ)
繰り返しの摺動によって部品が摩耗しにくいことを示します。耐摩耗性が高いほど、部品の寸法変化が少なく、長期にわたり初期の性能を維持し、製品寿命の延長に貢献します。
これらに加え、材料によっては「自己潤滑性」という特性も重要視されます。これは、外部から潤滑油やグリースなどを供給しなくても、材料自体が潤滑効果を発揮し、良好な摺動性を示す性質のことです。自己潤滑性を持つ材料は、メンテナンスの手間を削減できるだけでなく、潤滑剤による汚染を嫌うクリーンな環境での使用や、給油が困難な箇所の部品に適しています。
摺動性は、製品の性能、耐久性、そして信頼性に直接関わるため、設計において極めて重要な特性です。例えば、自動車のエンジン内部品やトランスミッションの構成部品、家電製品の駆動機構、OA機器の精密な紙送りローラー、医療機器の繊細な可動部など、枚挙にいとまがないほど多くの場面で、優れた摺動性が求められています。これらの部品において摺動性が不足すると、動作不良、不快な異音の発生、早期の故障といった問題を引き起こし、製品全体の価値を著しく損なう可能性があります。したがって、摺動性のメカニズムを理解し、適切な材料を選定することは、高品質な製品開発の基礎となります。
摺動性が求められる部品とその役割
具体的な部品を例に挙げることで、摺動性の重要性がより明確になるでしょう。以下に代表的な例を示します。
① ギア(歯車)
動力伝達に不可欠な部品であり、歯面同士が滑り接触しながら回転力を伝達します。滑らかな回転を実現するための低摩擦性と、長期的な噛み合い精度を維持するための耐摩耗性が共に不可欠です。
② 軸受(ベアリング、ブッシュ)
回転する軸を支持し、その摩擦抵抗を低減させる役割を担います。特に自己潤滑性に優れたエンプラ製軸受は、給油が困難な箇所や、油による汚染を嫌う環境での使用に適しています。
③ スライダー、ガイドレール
特定の部品を直線的に案内するための機構部品です。スムーズな往復運動と、繰り返しの使用に耐える耐久性が求められます。
④ カム機構
回転運動を複雑な往復運動や揺動運動に変換する機構です。カムフォロワーとカム面の摺動は、高い面圧がかかることもあり、耐摩耗性と共に衝撃への強さも重要となる場合があります。
これらの例からもわかるように、摺動部品は機械や装置の根幹をなす機能部品であり、その性能が製品全体の品質を左右すると言っても過言ではありません。
摺動性に優れた代表的なエンプラ
エンプラの中には、分子構造レベルで優れた摺動特性を持つものが数多く存在します。ここでは、代表的な材料とその特徴、そしてなぜそれらが摺動性に優れるのかという化学的な背景にも触れながら紹介します。
POM(ポリアセタール)
POMは、その優れた自己潤滑性と低い摩擦係数、高い耐摩耗性から、摺動材料の代表格として広く認識されています。機械的強度、剛性、耐疲労性にも優れ、吸水性が極めて低いために寸法安定性が高いという利点も持ち合わせています。
POMの主鎖は、酸素原子(-O-)とメチレン基(-CH₂-)が交互に規則正しく繰り返されるシンプルな直鎖状構造(例:ホルムアルデヒドのポリマーであるホモポリマーでは -[CH₂-O]n- )をしています。この規則正しい構造は高い結晶化度をもたらし、表面の硬度と平滑性を高めます。また、分子鎖間の凝集エネルギーが比較的小さく、分子表面のエネルギーも低いため、他の物質との相互作用が弱く、結果として摩擦係数が低くなります。さらに、POMの分子は比較的柔軟であり、相手材表面の微細な凹凸に追従しやすく、真実接触面積を小さく保つ効果もあると考えられています。これらの要因が複合的に作用し、優れた自己潤滑性と低摩擦・高耐摩耗性を実現しています。
主な用途としては、ギア、カム、ローラー、精密機械部品などが挙げられます。
PA(ポリアミド、ナイロン)
PAは、アミド結合(-CO-NH-)を繰り返し単位として持つポリマーの総称で、PA6、PA66、PA12など多くの種類が存在します。高い機械的強度、特に靭性(粘り強さ)に優れており、耐摩耗性も良好です。
PAの分子鎖中には極性の高いアミド基が存在し、これが水素結合を形成することで高い機械的強度や耐熱性を発現します。摺動性に関しては、このアミド基の存在が必ずしも直接的な低摩擦性に繋がるわけではありませんが、PAは相手材へのなじみ性が良く、ある程度の自己潤滑性を示すことが知られています。特に金属との摺動において、金属表面の酸化物層などとアミド基が相互作用し、安定した潤滑膜を形成しやすいと言われています。また、PAは適度な弾力性を持ち、衝撃的な負荷を緩和する能力があるため、衝撃荷重が加わる摺動部にも適しています。ただし、アミド基は親水性であるため、PAは一般的に吸水性が高く、これが寸法変化や機械的特性、摺動特性に影響を与える点には注意が必要です。
主な用途としては、高負荷・衝撃荷重がかかるギアや軸受、摺動時の相手材への攻撃性を抑えたい場合などに用いられます。
PTFE(ポリテトラフルオロエチレン)
PTFEは、フッ素原子(F)と炭素原子(C)のみから構成されるフッ素樹脂の一種で、「テフロン®」(ケマーズ社の登録商標)としても広く知られています。あらゆる固体物質の中で最も低い摩擦係数を持つことが最大の特徴です。
PTFEの分子構造は、炭素主鎖の周りを電気陰性度が極めて大きいフッ素原子が密に覆っている形(-[CF₂-CF₂]n-)をしています。フッ素原子はファンデルワールス半径が比較的小さく、かつ炭素-フッ素結合は非常に強固で安定しています。このフッ素原子による「鞘(さや)」のような構造が、分子間の凝集エネルギーを極めて小さくし、また表面エネルギーを著しく低下させます。これにより、他の物質との付着力が極めて弱くなり、結果として極めて低い摩擦係数(自己潤滑性)を実現します。また、この安定した化学構造は、優れた耐薬品性や耐熱性にも寄与しています。
PTFEは単体でシール材、パッキン、摺動テープ、コーティング材として用いられるほか、他のエンプラに添加剤として配合され、その摺動性を飛躍的に向上させる役割も担います。機械的強度は他のエンプラに比べて低いですが、その特異な低摩擦性は唯一無二の価値を提供します。
その他の高機能エンプラ
上記以外にも、特定の厳しい条件下での使用に適した高機能エンプラが存在します。
PPS(ポリフェニレンサルファイド)
芳香環と硫黄原子が交互に結合した構造を持ち、非常に高い耐熱性と耐薬品性、寸法安定性を示します。その剛直な分子構造と高い結晶性により、高温環境下でも良好な摺動性を維持します。
PEEK(ポリエーテルエーテルケトン)
芳香環がエーテル結合とケトン結合で繋がった複雑な構造を持つスーパーエンジニアリングプラスチックです。極めて高い耐熱性、機械的強度、耐薬品性を有し、高温・高荷重・高速といった非常に過酷な摺動条件下でも優れた性能を発揮します。
これらの高機能エンプラは、その優れた特性ゆえに高価であり、成形加工にも高度な技術が要求される場合があります。そのため、用途や要求性能、コストを総合的に判断して選定されます。なお、エンプラとは分類が異なりますが、超高分子量ポリエチレン(UHMWPE:Ultra-High Molecular Weight Polyethylene)も非常に優れた摺動特性を持つ材料です。ポリエチレンの分子量を極端に高めることで、高い耐摩耗性、自己潤滑性、耐衝撃性を実現しています。食品機械の部品や搬送ラインのガイド材など、その特性を活かした用途で広く利用されています。
材料選定の基本的な考え方
適切な摺動材料を選定することは、摺動部品の性能を最大限に引き出すための第一歩であり、設計の成否を左右すると言っても過言ではありません。多種多様なエンプラの中から最適なものを選ぶためには、系統だったアプローチが必要です。
まず最も重要なのは、部品に要求される性能を明確化することです。その摺動部品には、具体的にどのような機能が、どの程度のレベルで求められているのでしょうか。以下のような点を具体的にリストアップすると良いでしょう。
– 摩擦係数の目標値(例:できるだけ低い方が良い、特定の範囲内であれば可など)
– 許容される摩耗量、期待される寿命
– 静音性の要求レベル
– 動作のスムーズさ、スティックスリップ(びびり現象)の許容度
– 衝撃荷重の有無、その大きさ
– 寸法精度の要求レベル
次に、部品が使用される環境を詳細に把握する必要があります。これは、材料が持つべき耐性や、環境変化による特性変化を予測するために不可欠です。
① 温度条件
– 常時使用温度(上限、下限)
– 一時的に曝される最高・最低温度
– 温度サイクルの有無と範囲
② 負荷条件
– 摺動面にかかる荷重、そこから算出される面圧(P)
– 摺動速度(V)
– PとVの積であるP/V値(これは材料の耐荷重能力を示す重要な指標です)
– 荷重の種類(連続的か断続的か、衝撃的か)
③ 雰囲気・接触物質
– 屋外使用か屋内使用か(紫外線暴露の有無)
– 湿度環境(乾燥状態か、高湿度か、水中か)
– 接触する可能性のある化学薬品(油、溶剤、酸、アルカリなど)の種類と濃度
④ 相手材の情報
– 摺動する相手の材質(金属の種類、樹脂の種類、セラミックなど)
– 相手材の硬さ
– 相手材の表面粗さ
これらの要求性能と使用環境を整理した上で、コストと入手性を考慮します。高性能な材料は一般的に高価になる傾向があります。製品全体のコスト目標の中で、摺動部品にかけられるコストには限りがあるため、性能とコストのバランスを見極める必要があります。また、特殊な材料やグレードは、調達に時間がかかったり、安定供給が難しかったりする可能性もあるため、特に量産を視野に入れる場合は、入手性や供給安定性も重要な選定基準となります。
以上の情報を総合的に勘案し、各材料メーカーが提供する技術データシートを参照します。データシートには、摩擦係数、摩耗試験結果、PV限界値、機械的特性(引張強さ、曲げ弾性率、衝撃強さなど)、熱的特性(荷重たわみ温度、連続使用温度など)、電気的特性、吸水率といった詳細な数値情報が記載されています。これらのデータを比較検討することで、適切な材料候補を絞り込むことができます。不明な点や、より詳細な情報が必要な場合は、材料メーカーの技術担当者に相談することも有効な手段です。