エンプラの「摺動性」入門(後編):設計・成形技術とトラブルシューティング
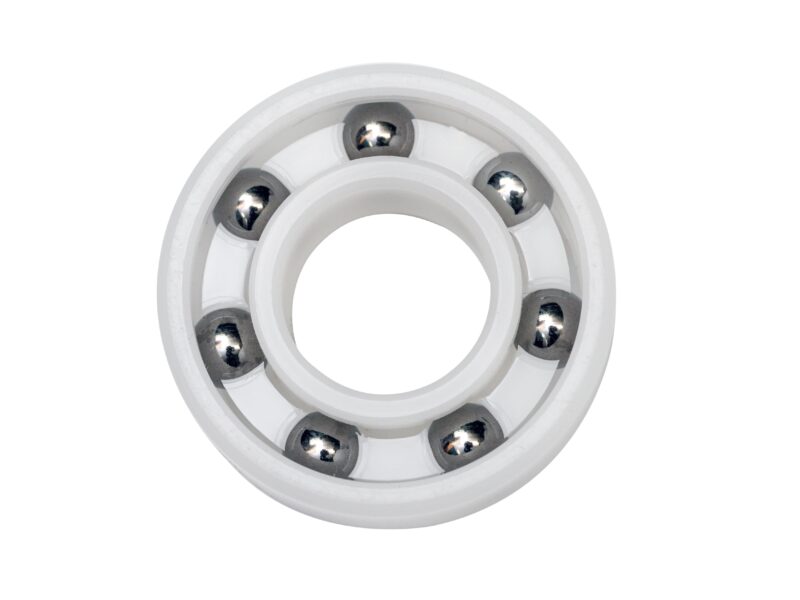
前編では、エンプラの摺動性に関する基礎知識、代表的な自己潤滑性材料、そして材料選定における基本的な考え方について概説しました。エンプラは、その軽量性、優れた機械的特性、そして設計自由度の高さから、多岐にわたる産業分野で不可欠な材料となっています。中でも「摺動部品」は、部品同士が接触しながら相対運動を行うため、材料の摺動性が製品の性能、信頼性、寿命を大きく左右する極めて重要な要素です。
後編となる本コラムでは、前編で選定したエンプラのポテンシャルを最大限に引き出し、さらに一歩進んだ摺動性能を実現するための具体的な技術的アプローチに深く踏み込みます。摺動性を向上させるための添加剤や強化繊維の活用法、高品質な摺動部品を製造するための射出成形プロセスにおける留意点、そして長期的な安定動作を確保するための設計上の重要ポイントについて解説します。最後に、摺動部品において遭遇しがちな一般的なトラブル事例を挙げ、その原因究明と対策立案に向けた実践的な糸口についても触れます。
エンプラの摺動性をさらに高める技術
ベースとなるエンプラを選定した後も、その摺動性をさらに引き上げるための多様な技術的選択肢が存在します。これらの技術を理解し、適切に組み合わせることは、設計の自由度を格段に高め、より高度な摺動性能要求に応えるための鍵となります。
摺動性を向上させる添加剤の活用
まず基本は、POMやPTFEといった自己潤滑性に優れるベース樹脂の特性を活かすことです。その上で、さらなる性能向上を目指し、摺動性向上添加剤(内部潤滑剤、固体潤滑剤)を活用します。
① PTFE粉末
他のエンプラに少量添加することで、摺動面にPTFEリッチな低摩擦薄膜を形成し、摩擦係数を大幅に低減、耐摩耗性を向上させます。スティックスリップ抑制にも有効です。
ベース樹脂の機械的強度(特に衝撃強度)を若干低下させる可能性があるため、PTFEの均一な分散が性能を発現させる鍵となります。
② シリコーンオイル
成形品表面に徐々に滲み出し(ブリードアウト)潤滑膜を形成。初期なじみ性向上やきしみ音防止に寄与します。ブリードアウトによる周辺部品への影響(汚染、電気接点不良など)や潤滑効果の持続性に注意が必要です。添加量とベース樹脂との相性が重要となります。
③ グラファイト(黒鉛)、二硫化モリブデン(MoS₂)
固体潤滑剤として摩擦係数の低減に加え、耐荷重性を向上させます。グラファイトは導電性を付与することも可能です。MoS₂は特に真空中や高温環境下で有効です。グラファイトは製品が黒色に限定されます。MoS₂は酸化雰囲気や高湿度下で性能低下する可能性があることに留意してください。
これらの添加剤は大きな効果をもたらす一方で、機械的物性の変化(強度低下など)やコストアップ、成形性への影響(ガス発生、金型汚染など)、さらには製品の色調が制限されるといったトレードオフも考慮する必要があります。期待する摺動特性と他の物性、コスト、成形性などを総合的に比較検討し、最適な添加剤と配合量を選定することが不可欠となります。
強化繊維の配合
エンプラの機械的強度や耐熱性向上を目的とする強化繊維も、摺動性に大きな影響を与えます。
① ガラス繊維(GF)
機械的強度、剛性、耐熱性が大幅に向上し、結果として耐摩耗性が向上する傾向があります。高面圧下での耐久性向上に寄与します。硬いガラス繊維が摺動相手材(特に軟質金属や他の樹脂)を攻撃し摩耗させる「アブレッシブ摩耗」のリスクがあります。相手材の材質・硬さとの組み合わせが極めて重要です。
② カーボン繊維(CF)
GF以上に機械的特性を向上させ、かつカーボン繊維自体が自己潤滑性を持つため、摩擦係数低減と耐摩耗性向上に大きく貢献します。GFに比べ相手材への攻撃性も低い傾向にあり、導電性の付与も可能ですが、GFより高価になることがネックです。導電性のため絶縁性が求められる箇所には不向きです。
射出成形時、溶融樹脂の流れによって強化繊維が特定の方向に並ぶ「繊維配向」が生じます。この配向は物性に異方性をもたらし、摺動特性にも影響します。一般的に、繊維が摺動方向に平行に配向すると耐摩耗性に優れるとされますが、摺動面に繊維端面が垂直に突き出すと相手材攻撃性を高める可能性があります。ゲート位置、肉厚設計などで繊維配向を考慮することが重要です。
摺動部品の射出成形における留意点
優れた材料と設計も、適切な射出成形技術が伴わなければ期待した摺動性能は得られません。設計者も成形に関する基本知識を持つことが、高品質な製品実現に繋がります。
金型設計の最適化
金型は成形品の形状、寸法精度、表面状態を決定づける最重要の要素となります。
① 摺動面の表面粗さのコントロール
摩擦特性、摩耗形態、潤滑剤保持性に直接影響します。低摩擦追求時は金型キャビティ表面を鏡面に近い滑らかな仕上げ(例:Ra 0.1μmオーダー)が望ましいです。一方、液体潤滑剤使用時や特定樹脂では、微細な凹凸(梨地仕上げ等、Ra 0.4~1.6μm程度)で潤滑剤を保持する「オイルリザーバー効果」を狙うこともあります。材料と潤滑条件に応じた最適化が必要です。
② PL、ゲート、EP跡の適切な処理
パーティングライン(PL): 摺動面にバリや段差が存在すると、相手材損傷、異常摩耗、動作不良の原因になります。PL位置は可能な限り摺動面を避けるのが原則です。
ゲート跡: 摺動面に存在すると同様の問題が発生します。ゲート種類(サイド、ピンポイント等)と位置は、ウェルドライン制御や充填バランスと共に、ゲート跡が性能に影響しないよう慎重に検討します。
エジェクタピン(EP)跡: 摺動面に段差や表面不均一を生じさせ、摺動特性を悪化させる可能性があります。EP配置は摺動面を避け、製品変形を起こさない位置を基本とします。
成形条件の最適化
材料が持つ本来の物性、特に摺動特性を最大限に引き出すには適切な成形条件が不可欠です。
① 結晶性樹脂における金型温度管理
POM、PA、PPS、PEEK等の結晶性エンプラでは、金型温度が結晶化度と結晶組織均一性に極めて大きな影響を与えます。結晶化度は硬さ、剛性、強度等の機械物性だけでなく、耐摩耗性や摩擦係数等の摺動性にも密接に関わります。一般に金型温度が高いほど結晶化がゆっくり進み、より完全で大きな球晶構造が形成されて結晶化度も高まる傾向があり、機械強度だけでなく、多くの場合、耐摩耗性も向上します。
材料メーカー推奨の金型温度範囲を遵守し、精密に管理することが安定品質の基本です。
② 射出・保圧・冷却条件とウェルドライン管理
射出圧力・速度、保圧、冷却時間: これらのパラメータは相互に関連し、寸法精度、内部応力、表面状態に影響し、間接的に摺動性能にも関わります。不足や過大は各種不良(ショートショット、ヒケ、バリ、樹脂劣化、繊維折損、変形等)の原因となります。
ウェルドライン: 樹脂合流部に発生する、線状の跡のことを指します。摺動面に存在すると摩耗起点や破損原因となり得るため、ゲート設計工夫等で摺動面や高負荷部を避けるように制御することが望まれます。ガスベント設置や成形条件調整(高温高圧での融着改善)も有効です。
特殊グレード(添加剤・強化繊維入り)固有の成形ノウハウ
これらの材料はベース樹脂のみと異なる注意点があります。
① 添加剤・強化繊維の均一分散とダメージ抑制
固体潤滑剤等の均一分散が性能ムラ防止の鍵になります。成形機スクリュー混練能力や予備乾燥・混合条件管理が重要です。GF/CFは過度なせん断応力で折損し、効果が減少します。低せん断な成形条件(スクリュー回転数、背圧、射出速度等)や金型設計(ゲート、ランナー形状)が必要です。
② 金型摩耗対策とメンテナンス
特にGF強化材等は金型摩耗を促進します。金型材質選定(高硬度鋼、表面硬化処理:窒化、コーティング等)が有効です。添加剤や樹脂分解ガスによる金型表面への付着物(モールドデポジット)は製品表面品質を損ない摺動特性にも悪影響を及ぼします。適切なガスベント、金型温度適正化、定期的金型清掃が重要です。
摺動部品の設計における重要ポイント
長期的な安定動作のためには、設計段階での細やかで戦略的な配慮が不可欠です。
適切なクリアランスの設定
摺動部品間のクリアランスは、性能を左右する基本かつ重要な要素です。クリアランスが小さすぎると熱膨張(摩擦熱含む)、吸水膨張、加工誤差で動きが渋くなったり、最悪焼き付く可能性が生じます。逆に大きすぎると、ガタつき、異音、偏摩耗、位置決め精度が低下します。そこで、クリアランスを設定する際は、まず、線膨張係数を十分に考慮する必要があります。エンプラの線膨張係数は金属より大きいため、使用温度範囲での寸法変化を考慮します。異種材組み合わせ時は特に注意をしなければなりません。次に、吸水膨張率です。PA等吸水性の高い材料では、湿度環境による寸法変化も考慮することが必要です。飽和吸水時を見越した設計を行います。加工公差と組付け公差も重要です。 個々の部品公差と累積公差を考慮し、最悪ケースでも機能するクリアランスを設定します。
P/V値(面圧×摺動速度)の管理
P/V値(面圧P × 摺動速度V)は摺動面の発熱量に関わる重要指標です。多くのエンプラには安定的に使用可能な上限「PV限界値」があります。これは材料の耐熱性、熱伝導性、機械強度、摩耗特性等が複合的に影響する値です。設計部品のP/V値が材料のPV限界値に対して十分な安全マージンを確保しているか確認することが極めて重要です。限界を超えてしまうと、急激な発熱、摩耗、溶融、変形等を招き早期破損に至ります。荷重・速度低減、接触面積拡大(面圧低減)、高PV限界値材料への変更や、放熱設計の改善で対応します。
摺動相手材との適合性
摺動性能は二つの材料の組み合わせで大きく変化するものです。
樹脂 vs 金属: 一般に良好な摺動性。金属側の表面粗さ(Ra0.2~0.8μm程度推奨が多い)や硬度が重要。軟質金属相手の場合、GF強化材等による攻撃性に注意が必要です。。
樹脂 vs 樹脂: 同種樹脂同士は凝着摩耗しやすいため避けるのが原則。異なる種類でもPTFE配合材等潤滑メカニズムを持つ材料の採用を推奨されます。
相手材の硬度: エンプラより硬い相手材選定が望ましい(特にGF強化材使用時)。
化学的適合性: 使用環境によっては化学反応(腐食、膨潤等)も考慮します。
摩耗対策を施した形状設計
摩耗進行抑制と長期安定動作のため、形状設計に細やかな工夫が必要です。
エッジ部のR処理・面取り: カジリや引っかかりを防ぎ、初期なじみ性向上、応力集中緩和します。
接触面積と面圧分布最適化: 面圧コントロール。クラウニング等でエッジロードを防ぎ、面圧分布を均一化します。
潤滑機構の設計: 油溝(螺旋状、格子状等)やグリス溜まりで潤滑剤を効果的に保持・供給します。 摺動面に潤滑成分が供給されやすい表面設計(微細凹凸でトランスファーフィルム保持等)にします。
摩耗粉対策とシール構造:摩耗粉はさらなる摩耗促進や動作不良原因になります。自然排出構造(開放型、排出溝等)や一時的滞留空間(摩耗粉ポケット)を検討します。外部からの異物侵入防止にシール(Oリング、オイルシール等)も有効です。
摺動部品にまつわる一般的なトラブルとその対策
注意を払っても予期せぬトラブルは発生し得ます。ここでは一般的なトラブルと原因究明・対策の考え方に触れます。
代表的なトラブル事例
① 早期摩耗・想定外の寿命の短さ: P/V値超過、不適切な材料選定(耐摩耗性・耐熱性等不足)、相手材との不適合(アブレッシブ摩耗、凝着摩耗)、潤滑不良・潤滑切れ、異物混入、成形不良(結晶化度不足、ウェルド強度不足等)、設計上の問題(不適切クリアランス、エッジ部のカジリ、摩耗粉堆積)が原因となります。
② 異音の発生(きしみ音、ビビリ音など):スティックスリップ現象(静摩擦係数と動摩擦係数の差大)、クリアランス不備(過大でガタつき音、過小で摺動抵抗増大音)、部品の共振、摺動面状態悪化(荒れ、傷、凝着物)、潤滑剤不適合・劣化が原因となります。
③ 動作不良(動きが重い、引っかかる、焼き付き、溶着):クリアランス不足(熱膨張、吸水膨張、加工誤差)、過熱による変形・溶融(P/V値超過、放熱不足)、潤滑切れ・潤滑剤炭化(高温下での劣化)、異物噛み込み、凝着摩耗進行(特に樹脂同士や軟質金属)、クリープ変形、成形品の寸法不良・反りが原因となります。
トラブルシューティングの実践的アプローチ
摺動部品にまつわるトラブルシューティングでは、系統的かつ論理的なアプローチで原因を究明し、的確な対策を講じることが重要です。「When」「(Where」「Who」「What」「Why」「How」という5W1Hの観点から、トラブルが発生した状況や具体的な症状を詳細に観察し、記録します。この際、写真や動画、現物のスケッチ、採取可能であれば摩耗粉のサンプルなども、後の分析に役立つ貴重な情報源となります。
次に、収集した情報をもとに、原因を多角的に分析していきます。ここでは、「4M+1E」といったフレームワークを活用すると、要因の洗い出しが体系的に行えます。
Material(材料)の観点では、選定した材料が適切であったか、材料のロット間にばらつきはなかったか、保管状況に問題はなかったかなどを検証します。
Machine(機械・設備)の観点では、クリアランス設定やP/V値の評価、部品形状といった設計自体の妥当性に加え、金型や成形機、そして摺動相手となる部品の状態に問題がなかったかを確認します。
Method(方法・プロセス)の観点では、成形条件が適切であったか、組付け方法や運転方法、メンテナンス方法に不備はなかったかを見直します。
また、人的要因が関与する可能性がある場合はMan(人)の観点から、作業者のスキルレベルや作業手順の遵守、ヒューマンエラーの可能性も考慮に入れます。
さらに、Environment(環境)の観点として、実際に使用されている環境(温度、湿度、雰囲気、振動、汚染物質の有無など)が、設計時に想定していた条件と異なっていないかを確認することも重要です。
これらの多角的な視点から考えられる要因を幅広く洗い出し、それらの関連性を考慮しながら、トラブルの根本原因に関する仮説を立てていきます。
続いて、立案した仮説の中から、最も可能性の高い原因について検証を行います。検証のためには、実際にトラブルを再現させる試験を行ったり、問題が発生した部品の摩耗痕を詳細に観察したり、寸法測定や表面粗さ測定を実施したりします。場合によっては、材料分析や非破壊検査、CAEシミュレーションなどを活用することも有効です。
最後に、検証結果に基づいて具体的な対策を実施し、その効果を確認します。対策を施す際には、一度に多くの変更を加えるのではなく、一つずつ変更してその都度効果を確認することが、原因の特定と対策の有効性を正確に評価するための原則です。効果が確認され、問題が解決した後は、その対策を恒久的なものとするために、設計変更、材料変更、成形条件の改訂、作業標準の見直しなどを行い、再発防止に努めます。こうして得られた知見は、将来の製品開発や品質改善活動に活かしていくことが重要です。
まとめ
エンプラの摺動性は、材料の特性、それを最大限に活かす設計技術、高品質なものづくりを実現する成形技術、そして実際に使用される環境条件という、数多くの要因が複雑に絡み合って決定される、非常に奥深く、かつ魅力的なテーマです。本稿では、その摺動性向上技術、射出成形および設計における重要なポイント、そしてトラブルシューティングの基本的な考え方について解説しました。
ここで述べた内容は、広範な摺動技術の世界における入り口に過ぎませんが、日々の業務で摺動部品の設計、開発、製造、あるいは品質改善に取り組んでおられるエンジニアの皆様にとって、何らかの具体的な指針や新たな視点、問題解決のヒントを提供できたのであれば幸いです。より具体的な材料選定、設計上の課題、試作や量産に関するご相談がございましたら、どうぞご遠慮なくお問い合わせください。長年にわたり培ってきた専門知識と経験を基に、お客様の製品開発をサポートさせていただきます。