金属代替でコスト削減と軽量化!樹脂化のメリットと具体的事例を徹底解説
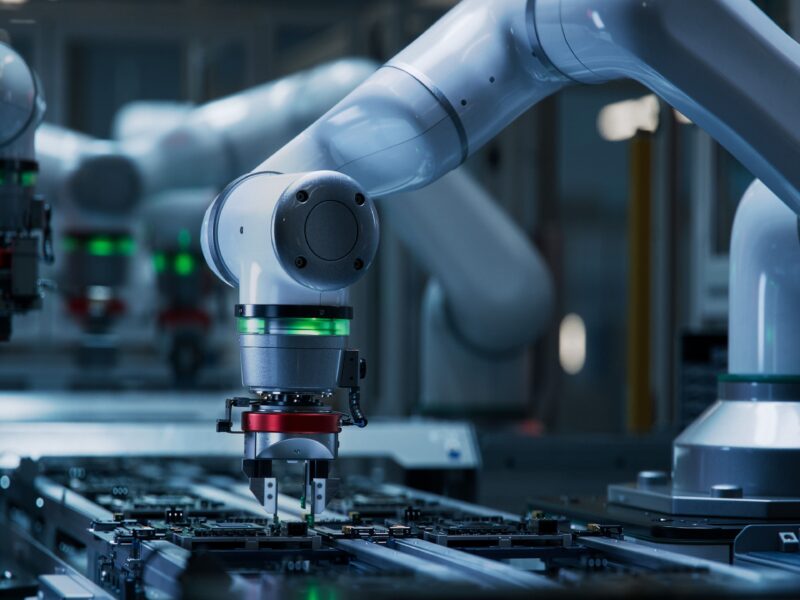
金属代替がしやすい部品とは?(前編)
近年、製造業におけるコスト競争の激化や環境負荷低減への意識の高まりを背景に、金属部品をエンプラやスーパーエンプラへ置き換える動きが加速しています。しかし、全ての金属部品がエンプラに代替可能というわけではなく、材料の特性を理解し、適切な部品に適用することが重要です。金属からエンプラへの置き換えには、向き・不向きが存在します。「どのような部品が代替しやすいのか」という傾向を掴むことで、設計の初期段階から効率的かつ効果的な樹脂化の検討が可能となり、開発の方向性が明確になります。適切な部品選定と設計は、コスト削減、軽量化、機能向上といった多くのメリットをもたらす一方で、不適切な適用は性能不足や思わぬトラブルを引き起こしかねます。
本コラム前編では、特に産業機器、配管機器、搬送装置といった分野の部品設計に焦点を当て、金属からエンプラへの代替が進む背景、代替を検討しやすい部品の傾向、具体的事例について解説します。金属代替を検討する上での“最初の一歩”として、ぜひご活用ください。
金属代替の進展と背景
金属部品からエンプラへの代替は、単なる材料の置き換えに留まらず、製品の価値向上や製造プロセスの革新に繋がる重要な取り組みとして、多くの産業分野で進展しています。その背景には、以下のような要因が挙げられます。
加工コストの削減、軽量化、省工程化へのニーズ
金属部品の製造には、切削、研削、溶接、プレス、鋳造といった多くの加工工程が必要となり、それに伴うエネルギー消費や加工時間、設備投資がコストを押し上げる一因となっています。特に複雑な形状や多数の部品で構成されるアセンブリ品の場合、その傾向は顕著です。
一方、エンプラの射出成形は、金型に溶融した樹脂を注入し冷却固化させることで、複雑な形状の部品でも一度の工程で大量生産が可能です。これにより、大幅な加工コストの削減とリードタイムの短縮が期待できます。
また、エンプラの比重は金属(例えば鉄の約7.8 g/cm³、アルミニウムの約2.7 g/cm³)と比較して非常に小さく(例えばPOMで約1.4 g/cm³、スーパーエンプラのPEEKで約1.3 g/cm³)、製品の軽量化に大きく貢献します。装置の軽量化は、搬送効率の向上、設置作業の容易化、さらには装置全体のエネルギー効率改善にも繋がります。
「切削・溶接」から「成形一体化」
従来の金属加工では、複数の部品を製造し、それらを溶接やボルト締結などで組み立てるのが一般的でした。この方法は部品点数の増加、組立工数の発生、接合部の強度管理といった課題を伴います。射出成形技術の進化により、エンプラでは従来複数の金属部品で構成されていた機能を一つの部品に集約する「一体成形」が可能になりました。例えば、軸受部、固定部、カバー部などを一体で成形することで、部品点数の削減、組立工数の削減、さらには部品間の接合部が無くなることによる信頼性の向上も期待できます。
絶縁性、耐薬品性、防錆性といった金属の苦手分野を補完できるのがエンプラの強み
金属材料は高い強度や剛性、耐熱性を持つ一方で、電気を通しやすい(導電性)、特定の薬品に侵されやすい(腐食性)、錆びやすいといった特性も持ち合わせています。これらの特性が問題となる用途では、絶縁処理や防錆処理、耐食性の高い高価な金属材料の使用が必要となり、コスト増や工程増に繋がります。
エンプラは、その種類によって優れた電気絶縁性、多様な薬品に対する耐性(耐薬品性)、そして金属のように錆びることがない(防錆性)といった特性を有しています。これらの特性は、金属が苦手とする分野を効果的に補完し、製品の機能性向上や長寿命化に貢献します。例えば、電気機器のハウジングやコネクタ、薬液を扱うポンプ部品、水回りで使用される部品などにエンプラが活用されるのは、これらの強みがあるためです。
金属代替が検討しやすい4つの傾向
全ての金属部品がエンプラへの代替に適しているわけではありません。しかし、特定の傾向を持つ部品は、比較的スムーズに代替検討を進められ、かつ樹脂化のメリットを享受しやすいと言えます。ここでは、その代表的な4つの傾向を紹介します。
傾向① 形状が複雑または薄肉で、金属加工では非効率
金属で複雑な三次元形状や薄肉構造を実現しようとすると、多軸マシニング加工や精密鋳造、板金加工後の溶接など、高度な技術と多くの工数が必要となり、コストが大幅に上昇します。また、切削加工では材料のロスも多く発生します。
一方、射出成形は金型を用いるため、一度金型を製作すれば、複雑なリブ構造やボス、薄肉部を持つ部品でも比較的容易に、かつ高精度に量産できます。材料のロスも少なく、ネットシェイプに近い成形が可能です。したがって、金属では加工が困難、あるいはコスト的に見合わない複雑形状・薄肉形状の部品は、エンプラ代替の有力な候補となります。
傾向② 使用応力・荷重が比較的低く、補強設計が容易
一般的にエンプラの機械的強度(引張強さ、曲げ強さなど)や剛性は、金属に比べて低い傾向にあります。そのため、非常に大きな荷重がかかる構造部材や、高い衝撃を受ける部品の全てを単純にエンプラに置き換えることは困難です。
しかし、部品にかかる応力や荷重が比較的低い場合、あるいは衝撃が少ない用途であれば、エンプラの強度でも十分に機能する可能性があります。さらに、リブの追加や肉厚の最適化、ガラス繊維や炭素繊維による強化グレードの選定といった補強設計を施すことで、必要な強度を確保することも可能です。設計の自由度が高い射出成形であれば、このような補強構造も比較的容易に組み込めます。
傾向③ 防錆・絶縁・非磁性など、金属では過剰な性能が求められる、あるいは特殊処理が必要となる
部品の機能として、防錆性、電気絶縁性、非磁性といった特性が求められる場合があります。金属でこれらの要求を満たすためには、ステンレス鋼のような高価な材料を選定したり、メッキ処理、アルマイト処理、樹脂コーティングといった二次加工を施したりする必要があり、コストやリードタイムが増加します。
エンプラは、材料自体が優れた防錆性、高い電気絶縁性、非磁性といった特性を持つものが多く存在します。これらの特性が主たる要求である場合、金属を用いるよりもエンプラの方が本質的に適しており、特別な処理なしで要求性能を満たせるため、コストメリットも大きくなります。例えば、水環境下で使用される部品や、電気回路周辺の部品、磁気センサーに影響を与えたくない部品などが該当します。
傾向④ 成形化による量産効果や部品点数削減が見込める設計
ある程度の生産量が見込める部品であれば、射出成形による量産効果は非常に大きくなります。初期投資として金型費用が発生しますが、生産数量が増えるほど部品一個あたりのコストは大幅に低下します。
また、前述の通り、射出成形では複数の機能を一体化して成形できるため、従来複数の金属部品と締結部品で構成されていたアセンブリを、単一のエンプラ部品に置き換えることが可能です。これにより、部品点数の削減、在庫管理の簡素化、組立工数の大幅な削減、そして接合部の廃止による信頼性向上など、多岐にわたるメリットが期待できます。このような設計変更が見込める部品は、積極的にエンプラ化を検討する価値があります。
※これらはあくまで「金属代替の検討が進めやすい傾向」を示すものであり、これらに該当しない部品でも、材料選定や設計の工夫次第で代替が可能なケースは多数存在します。当社のような経験のあるメーカーへの相談を通じて、可能性を探ることが重要です。
金属代替が成功しやすい用途・部品事例
上記の傾向を踏まえ、実際にどのような部品で金属代替が成功し、エンプラの特性が活かされているのか、業界別に具体的な事例を見ていきましょう。
制御・計装機器
制御盤や計測機器内部では、電気的な安全性が求められる部品が多く使用されます。
① 端子台ホルダー、絶縁ブラケット
金属製のブラケットでは別途絶縁シートを挟んだり、絶縁コーティングを施したりする必要がありましたが、エンプラ(変性PPE、PBT)を用いることで部品自体が優れた電気絶縁性を持ち、感電や短絡のリスクを低減できます。また、難燃グレードを選定することで、万が一の発火時にも燃え広がりにくく、安全性を高めることができます。
② 筐体カバー、センサーケース
軽量化による取り扱いの容易さ、複雑な形状の実現によるデザイン性の向上、そして内部の電子部品を保護するための絶縁性が求められます。エンプラ(PC、変性PPE)はこれらの要求を満たしつつ、電磁波シールド性が必要な場合は導電性フィラーを配合したグレードも選択可能です。耐熱寸法安定性に優れた材料(PEI、PPS)は、発熱する部品の近傍や高温環境下での使用にも適しています。
配管・流体制御機器
薬液や純水、ガスなど様々な流体を扱う配管・流体制御機器では、耐薬品性と非腐食性が重要となります。
① 継手、逆止弁ボディ
金属製の継手や弁は、流体の種類によって腐食やイオン溶出の問題が生じることがあります。エンプラ(PPS、半芳香族PA)は優れた耐薬品性を持ち、幅広い流体に対して安定しています。また、射出成形により複雑な流路を持つ部品も一体で成形できるため、漏れリスクの低減や小型化にも貢献します。
② 圧力センサーケース、Oリング保持部
流体に直接接するセンサーケースや、シール性を担保するOリングの保持部には、流体への耐性と共に寸法精度が求められます。PEEKやPPSといったスーパーエンプラは、高温・高圧下でも寸法安定性が高く、精密な成形が可能です。金属と異なり錆びないため、流体を汚染する心配もありません。
機械装置・ユーティリティ設備
人や機械が直接触れる機会のある部品や、構造的な負荷が比較的小さいカバー類などで代替が進んでいます。
① ノブ、操作ハンドル
金属製のノブやハンドルは、触れた際の冷たさや、長期間の使用による錆の発生が問題となることがあります。エンプラ(PA6、PA66、半芳香族PA)は熱伝導率が低く、触感が良く、着色も容易なためデザイン性も向上します。また、軽量化により操作性の向上も期待できます。
② シャッターカバー、構造部カバー類
装置の美観を保つカバー類や、内部機構を保護するカバーは、必ずしも高い強度を必要としない場合があります。エンプラ(ABS、PC/ABS)を用いることで、軽量化、複雑なデザインの実現、そして金属加工に比べてコストダウンが可能です。塗装レスで意匠性を高めることもできます。
搬送装置・ロボット周辺部品
軽量化による高速動作や省エネルギー化、摺動性が求められる部品でエンプラの採用が広がっています。
① スライダー、リフター部
部品を滑らせたり、持ち上げたりする機構では、相手材との摩擦係数が低いこと(摺動性)と、軽量であることが求められます。自己潤滑性を持つエンプラ(PEEK、PA、POM)は、オイルレスでの使用やメンテナンスフリー化に貢献し、金属粉の発生も抑えられます。軽量化は、アームの先端など可動部の慣性モーメントを低減し、高速化や高精度化に繋がります。
② 保持ユニット、可動カバー類
ワークを掴むハンド部分や、頻繁に開閉するカバー類なども、軽量化の恩恵が大きい部品です。エンプラの一体成形性を活かせば、従来複数の部品で構成されていた複雑な形状の保持ユニットも、部品点数を削減して製造できます。PAやPPSにガラス繊維を配合した強化グレードは、軽量でありながら高い剛性を実現できます。
まとめ(前編)
ここまで、金属部品をエンプラに代替するメリットや背景、そしてどのような部品が代替の検討に適しているか、具体的な業界別の成功事例を交えて解説しました。樹脂化は、コスト削減、軽量化、機能向上など、多くの魅力的な可能性を秘めています。
コラム後編では、金属代替を進める上で注意すべき部品、設計時に考慮すべき具体的なポイント、そして代表的なエンプラの推奨材料と用途のマッチングについて詳しく掘り下げていきます。ぜひ合わせてご覧ください。