失敗しない金属代替!樹脂化の注意点と設計・材料選定の秘訣を解説
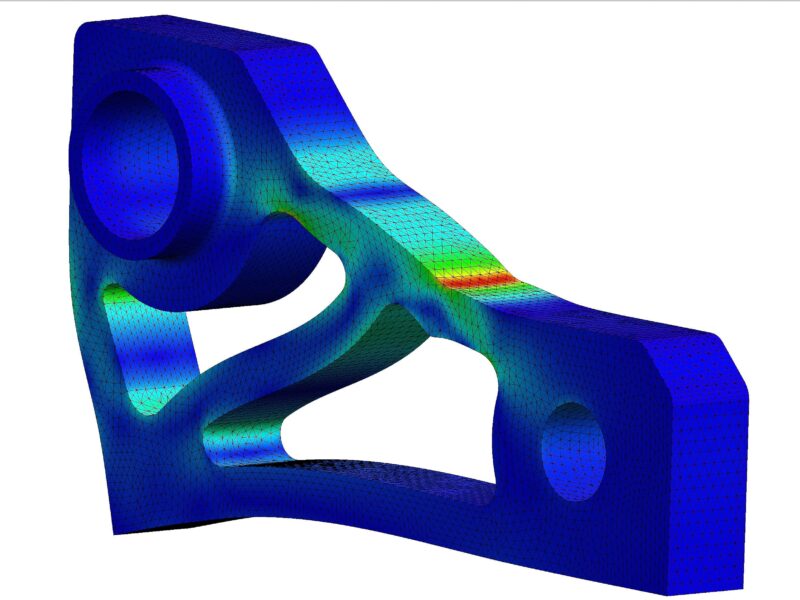
金属代替がしやすい部品とは?(後編)
金属部品からエンプラへの代替は、コスト削減、軽量化、機能性向上といった多くのメリットをもたらす可能性があります。コラム前編では、金属代替が進む背景や検討しやすい部品の傾向、そして具体的な成功事例について解説しました。
しかし、エンプラへの代替を成功させるためには、単に材料を置き換えるだけでなく、エンプラの特性を深く理解し、設計段階から適切な配慮を行うことが不可欠です。また、全ての部品が容易に代替できるわけではなく、注意が必要なケースも存在します。
本コラム後編では、金属代替、金属樹脂化を進める上で特に注意すべき部品の特性、エンプラ化を成功に導くための設計上の重要なポイント、そして代表的なエンプラ材料の選定指針について、より具体的に掘り下げて解説します。金属代替プロジェクトをより確実なものにするために、ぜひ本稿の情報をご活用ください。
金属代替に注意が必要な部品
エンプラは多くのメリットを持つ一方で、金属と比較していくつか留意すべき点もあります。以下のような部品を代替する際には、特に慎重な検討と設計上の配慮が必要です。
高荷重・衝撃が加わる機械的支持部
装置のフレームや、大きな力が繰り返し加わるシャフト、ギアなどの機械的支持部は、高い剛性、強度、耐疲労性が求められます。汎用的なエンプラではこれらの要求を満たせない場合が多く、安易な代替は破損や事故に繋がる可能性があります。
ただし、スーパーエンプラの中には金属に匹敵する強度を持つものや、炭素繊維などで大幅に強化されたグレードも存在します。CAE解析による応力評価を徹底し、リブ構造の最適化や肉厚の確保、適切な材料選定(炭素繊維強化PEEK、LCP)を行うことで、限定的ながら代替可能なケースもあります。
±10μmを下回る寸法精度が求められる機構部品
精密な位置決めが要求される部品や、嵌合公差が非常に厳しい機構部品など、ミクロンオーダーの寸法精度が求められる場合、エンプラの成形収縮や吸水による寸法変化、温度変化による線膨張が問題となることがあります。
金属は熱膨張係数が比較的小さく、寸法安定性に優れていますが、エンプラは種類によってこれらの影響を受けやすいため注意が必要です。対策としては、成形収縮率が小さく吸水性の低い材料(LCP、PPS、MXD6、半芳香族PA)を選定する、アニール処理(熱処理による内部応力の除去と結晶化促進)を施して寸法安定性を向上させる、使用環境の温湿度変化を考慮した公差設計を行う、といった配慮が不可欠です。
熱伝導や高表面硬度を必要とする部位
モーターの放熱フィンやヒートシンクのように高い熱伝導性が求められる部品、あるいは耐摩耗性が重要で高い表面硬度が必要な部品(カッター刃、高負荷摺動部)は、一般的に金属の得意分野です。
エンプラは基本的に熱伝導性が低く、表面硬度も金属に比べて劣ります。ただし、近年では熱伝導性フィラー(窒化ホウ素、グラファイト)を高充填した熱伝導性エンプラや、表面硬度を高めた特殊グレードも開発されています。しかし、金属と同等の性能を出すのは難しい場合が多く、コストとのバランスも考慮する必要があります。代替を検討する際は、要求される熱伝導率や硬度のレベルを明確にし、本当にそのレベルが必要なのか、オーバースペックではないかという視点も重要です。
これらの注意が必要な部品であっても、適切な材料選定、CAEを活用した綿密な設計検証、補強リブの最適配置、成形後のアニール処理といった設計・製造上の工夫を凝らすことで、金属代替の道が開けることもあります。専門的な知識と経験が求められる領域と言えるでしょう。
設計時に考慮すべきポイント
金属からエンプラへ部品を置き換える際には、単に材料を変更するだけでなく、エンプラの特性を最大限に活かし、かつ弱点を補うための設計上の工夫が不可欠です。
応力集中の回避(肉厚分布、リブ配置)
エンプラは金属に比べてノッチ感度(切り欠き部などに応力が集中しやすい性質)が高い傾向があります。そのため、部品の角部には適切なR(丸み)を設け、応力集中を緩和することが重要です。また、急激な肉厚変化はヒケ(成形品の表面が凹む現象)やソリの原因となるだけでなく、応力集中の要因にもなります。できるだけ均一な肉厚設計を心がけ、強度が必要な箇所には効果的にリブを配置することで、軽量化と高剛性を両立させることができます。リブの高さや厚み、配置間隔なども強度に大きく影響するため、CAE解析などを活用して最適化を図ることが望ましいです。
金型設計を意識したアンダーカット/抜き勾配処理
射出成形は金型を用いて部品を製造するため、金型からスムーズに製品を取り出せるような設計(離型性)が重要です。金型の開閉方向に沿って勾配(抜き勾配)を設けるのが基本です。抜き勾配が不十分だと、製品の取り出し時に傷が付いたり、変形したりする可能性があります。
また、金型の開閉方向に対して凹凸となる形状(アンダーカット)は、そのままでは金型から取り出せません。スライドコアなどの特殊な金型機構が必要となり、金型コストの上昇や成形サイクルの長期化に繋がります。設計段階でアンダーカットを回避する形状変更を検討するか、どうしても必要な場合は最小限に留める工夫が求められます。
吸水・温度変化による寸法変動と補正設計
多くのエンプラは、使用環境の湿度によって水分を吸収し、寸法が変化する特性(吸水性)を持っています。また、温度変化によっても金属より大きく膨張・収縮します(線膨張係数が大きい)。これらの寸法変動は、精密な嵌合が求められる部品や、異なる材料と組み合わせる場合に問題となることがあります。
設計時には、使用するエンプラの吸水率や線膨張係数を把握し、想定される使用環境(温度、湿度)における寸法変化量を見込んだ上で、クリアランスや公差を設定する必要があります。また、吸水性の低い材料を選定したり、ガラス繊維などで強化して寸法安定性を高めたりすることも有効な対策です。
組立工程の簡略化(ねじ固定→嵌合、部品一体化など)
エンプラの設計自由度の高さを活かせば、組立工程を大幅に簡略化できます。例えば、従来ネジで固定していた箇所を、スナップフィット(弾性変形を利用した嵌合構造)に置き換えることで、ネジ部品の削減と組立時間の短縮が可能です。また、複数の部品を一体成形することで、部品点数そのものを減らし、組立作業自体を不要にすることもできます。インサート成形(金属部品などを金型内にセットして樹脂と一体化させる技術)やアウトサート成形(成形品に後から別部品を組み込む技術)も、組立工程の簡略化に貢献します。
推奨材料と用途マッチング
金属代替を検討する上で、どのようなエンプラを選定するかが成功の鍵を握ります。ここでは、代表的なエンプラ・スーパーエンプラとその特徴、適した用途例を紹介します。
材料例 | 特徴 | 適した用途例 |
PPS(ポリフェニレンスルファイド) | 高い耐熱性(連続使用温度200℃以上)、優れた耐薬品性、寸法安定性、機械的強度、難燃性(UL94 V-0相当)。ガラス繊維強化でさらに高強度・高剛性化。 | ポンプ部品、バルブ部品、コネクタ、センサーハウジング、電気・電子部品の絶縁構造部、流体接続部。特に高温環境下や薬液に触れる部品。 |
PSU/PES(ポリサルホン/ポリエーテルサルホン) | 高い耐熱性、透明性(非晶性)、耐スチーム性、耐加水分解性、寸法安定性。PESはPSUよりさらに耐熱性が高い。 | 医療機器部品(滅菌対応)、食品機械部品、分析装置のフローセルや観察窓、耐熱水配管部品、透明な耐熱カバー。 |
PEI(ポリエーテルイミド) | 非常に高い耐熱性(連続使用温度約170℃)、高強度・高剛性、優れた電気絶縁性、耐薬品性、難燃性、寸法安定性。 | 電気・電子部品(コネクタ、ソケット)、医療機器部品、半導体製造装置部品、耐熱性が求められる機器フレーム。 |
変性PPE(変性ポリフェニレンエーテル) | バランスの取れた機械的特性、優れた電気絶縁性、低吸水性、良好な寸法安定性、多くのグレードで難燃性を付与可能。比較的安価。 | 電気・電子機器の筐体や内部部品(端子台、スイッチ部品、OA機器シャーシ)水処理関連部品、制御ボックス類。 |
MXD6 | 芳香族環を含むため高強度・高剛性。標準的なポリアミド(PA6, PA66)に比べ吸水性が低く、寸法安定性に優れる。ガスバリア性も良好。 | 精密機構部品、電子部品コネクタ、薄肉構造体、高精度な嵌合が求められる部品。 |
半芳香族PA(半芳香族ポリアミド) | 主鎖に芳香環と脂肪鎖を併せ持ち、PA6やPA66に比べて高強度・高剛性、高耐熱性、低吸水性、良好な耐薬品性を持つ。摺動性も良好なグレードがある。 | ギア、ベアリングリテーナー、搬送ガイド、高負荷がかかる機構部材、構造補強部品。金属代替として幅広い用途に。 |
これらの材料はあくまで一例であり、各材料メーカーから多様なグレード(強化材の種類や量、摺動性付与、導電性付与など)が提供されています。要求される性能、コスト、成形性などを総合的に比較検討し、最適な材料を選定することが重要です。
まとめ
金属部品からエンプラへの代替は、単に材料を変えるだけでなく、製品の付加価値向上や製造プロセスの合理化に繋がる戦略的な一手となり得ます。その成功は、「どの部品を代替対象として選ぶか(部品の適性)」と「どのように設計し、材料を選定するか(設計の工夫)」という二つの要素の組み合わせによって大きく左右されます。
本コラム後編では前編に続き、金属代替における注意点、設計時のポイント、そして推奨材料について解説しました。最初に着手すべきは、構造的負荷が低く、成形一体化の利点が出やすい部品であることは変わりませんが、より高度な要求に応えるためには、材料の深い理解と設計の工夫が不可欠です。
実際には個々の部品の要求性能や使用環境は千差万別であり、最適な解決策を見出すには専門的な知識と経験が不可欠です。当社では、お客様の具体的な課題やニーズをヒアリングさせていただいた上で、最適な材料の提案から、CAE解析を駆使した設計支援、そして金型製作、試作成形、量産まで一貫してサポートできる体制を整えております。
「この部品、もしかしたら樹脂化できるのでは?」「金属部品のコストや重量に課題を感じ
代替による新たな可能性を一緒に探ってみませんか。貴社の製品開発と競争力強化に貢献できることを楽しみにしております。