成形不良が続くなら見直しのチャンス!射出成形部品の見積依頼で品質改善
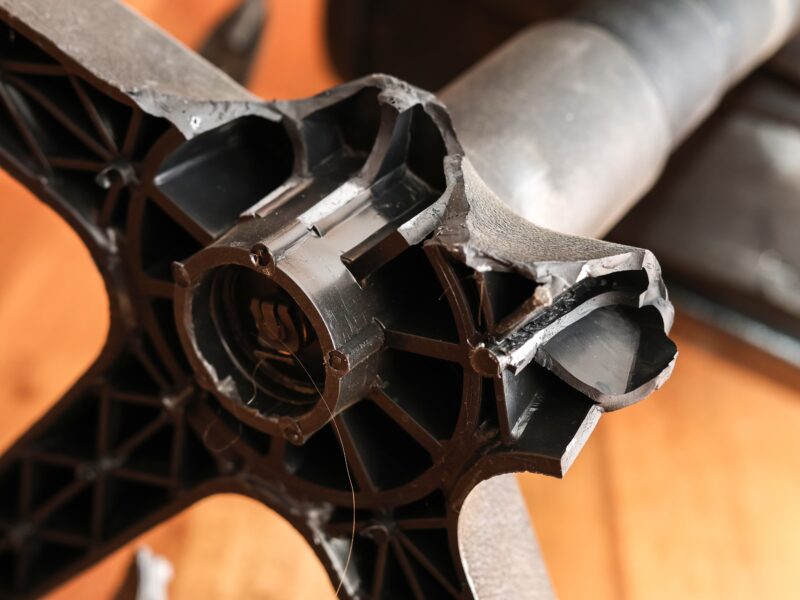
「また不良が出た…」、「調整しても品質が安定しない」。射出成形品の繰り返す品質トラブルは、多くのご担当者様にとって悩みの種です。現場の努力だけでは解決が難しいこの問題、実は「見積依頼」をきっかけに、根本から改善できる可能性があります。
本コラムでは、射出成形の品質不良がなぜ繰り返されるのか、その根本原因を解き明かし、新しいサプライヤーへの「見積依頼」がいかにして品質改善の突破口となるのかを解説します。コスト比較のためだけではない、戦略的な見積依頼の活用法をご紹介します。
繰り返す品質不良の背景と課題
射出成形は「設計」、「金型」、「材料」、「成形」の4要素が複雑に絡み合うため、一度問題が発生すると原因特定が難しく、トラブルが長期化しがちです。現場では、以下のような不良が頻繁に発生します。これらの不良は、単独で発生することもあれば、複合的に現れることもあります。
収縮・反り・ヒケ
成形品が冷えて固まる際に体積が縮むことで発生します。製品の肉厚が不均一だったり、金型の温度管理が不適切だったりすると、製品が意図せず曲がってしまう「反り」や、表面が凹んでしまう「ヒケ」につながります。
ガス焼け・ショートショット
金型内に樹脂を充填する際、内部の空気や樹脂から発生したガスが抜けきらないことで起こる不良です。ガスが断熱圧縮されて製品の一部が黒く焦げる「ガス焼け」や、ガスの圧力で樹脂が末端まで行き届かない「ショートショット(充填不足)」を引き起こします。
寸法不良
製品の寸法が、図面で指示された公差内に収まらない不良です。特に精密さが求められる機構部品や嵌合部品では、組み立て不良に直結する致命的な問題となります。
割れ(クラック)
成形品に亀裂が入る不良です。成形時に発生する内部応力(残留応力)が大きすぎたり、金型から製品を突き出す際の力が強すぎたりすることが原因で発生します。特に、鋭い角(シャープエッジ)があるデザインは応力が集中しやすく、割れのリスクが高まります。
品質不良が常態化すると、現場では成形条件の微調整や検査の強化といった「対症療法」に追われがちです。しかし、これらは一時しのぎに過ぎず、根本原因が放置されたままでは、いつまでたっても問題は解決しません。特定のベテラン作業員のスキルに依存する体制は、安定生産のリスクにもなります。これが現場の努力だけでは品質改善に至らない「限界」です。繰り返す不良の根本原因は、多くの場合、以下の3つのいずれか、あるいは複合的な要因に起因します。
① 設計上の課題(製品設計・金型設計)
実は、成形不良の約7割は設計段階に原因があると言われています。製品形状に無理があったり、金型のゲート位置や冷却、ガス抜きの設計が不適切だったりすると、後工程の成形技術だけではカバーしきれない問題が発生します。
② 不適切な材料選定
製品に求められる機能だけで材料を選び、その材料の「成形性」を考慮していないケースです。流動性が低い、収縮率が大きすぎるなど、製品形状や金型構造に合わない材料を選んでしまうと、様々な不良の直接的な原因となります。
③ 成形条件の不適合
現在のサプライヤーが保有する成形機や技術ノウハウが、製品・金型・材料の組み合わせに対して最適でない場合です。特にスーパーエンプラなど、特殊な知見が求められる材料では、 成形メーカーの技術不足が品質の不安定さとなって現れます。
これらの根本原因は、既存のサプライヤーとの関係性が長いほど「特に大きな変化点はないので問題ないはずだ」という固定観念に縛られ、見過ごされがちになります。そして、不良が収まったと思った矢先にまた再発・・・という繰り返しが起こるのです。
見積依頼によるプロのアドバイス活用
こうした膠着状態を打破する強力な一手、それが「新しいサプライヤーへの見積依頼」です。これは単なる相見積もりではなく、プロによる「セカンドオピニオン」を得るための戦略的なアクションです。
見積依頼が品質改善のきっかけとなる理由は、新しいサプライヤーが「ゼロベース」で課題を客観的に分析してくれる点にあります。これまでの経緯や固定観念に縛られず、「そもそもこの設計で正しいのか?」、「もっと適した材料や工法があるのではないか?」といった根本的な視点から、最適な製造方法を再検討します。
これにより、自社や既存サプライヤーでは気づけなかった問題点や、流動解析などの最新技術を活用した新たな解決策が見つかる可能性が飛躍的に高まるのです。
経験豊富な成形メーカーは、単なる価格提示だけでなく、品質を改善するために以下のような具体的な技術提案を行います。
① 金型設計の見直し
プロは製品図面と不良情報から、最適な樹脂の流れをシミュレーションし、金型設計にまで踏み込んだ提案を行います。流動解析を活用し、充填パターン、ウェルドラインやガス溜まりの位置を科学的に予測し、最適なゲート位置やガスベントの設計を提案します。反りを抑制するため、製品形状に合わせて効率的に冷却できる回路設計を提案します。
② 材料変更や成形条件の最適化
材料のプロフェッショナルとして、より成形しやすく、かつ要求性能を満たす代替材料を提案します。同じ材質でも、流動性や収縮率が異なるグレードの中から、製品形状に最適なものを提案します。材料変更や金型改善により、品質を維持したまま生産性を高め、コストダウンにつなげる提案も行います。
③ 不良リスク低減のための設計提案
時には、製品の設計そのものへのフィードバックを行うこともあります。これは、成形メーカーが顧客のパートナーとして、製品の成功にコミットしている証拠です。ヒケや反りの原因となる極端な肉厚差を解消するための「肉盗み」などを提案します。割れの原因となる応力集中を避けるため、シャープエッジに適切なRを追加することを提案します。
プロの提案を受け入れることで得られるメリットは、「不良の根本原因が解消され、恒久的な品質安定が実現すること」、そしてそれに伴い、不良コストや検査コストが削減され、「結果としてトータルコストが最適化されること」の2点に集約されます。
コストと品質の両立を実現する流れ
では、実際にプロの力を借りて品質改善を実現するには、どうすればよいのでしょうか。成功の鍵は、見積依頼時の「情報提供」にあります。
見積依頼時の準備情報
的確な提案を引き出すためには、自社の状況を正確に伝えることが不可欠です。少なくとも、以下の情報を整理し、メーカーに提供しましょう。
製品図面や仕様:3Dデータと2D図面。製品に求められる性能(強度、耐熱性、外観要求レベルなど)。
不良状況の整理:「何が、どこに、どれくらい」起こっているか(不良現象、発生箇所、不良率)。不良の状況がわかる写真や現物サンプル(良品・不良品)。
目標品質・コスト:達成したい品質レベル(例:不良率0.5%未満)。目標とする製品単価や金型費用。
これらの情報が詳細であるほど、成形メーカーはより深く、的確な診断と処方箋(改善提案)を出すことができます。情報提供後、メーカーから技術的な改善提案を含んだ見積もりが提示されます。ここからは、成形メーカーを単なる外注先ではなく「パートナー」として捉え、技術的なディスカッションを重ねることが重要です。
CAE解析の結果などを共有してもらいながら、なぜその改善策が有効なのかを論理的に理解し、品質・コスト・納期のバランスが最も良い案を選択します。合意形成ができたら、改善策を盛り込んだ金型での試作成形へと進み、試作品の品質を評価した上で、量産移行を決定します。
まとめ
繰り返す品質不良は、現場の対症療法だけでは解決できません。しかし、その根深い問題は、「新しいサプライヤーへの見積依頼」というアクションをきっかけに、根本から解決できる可能性があります。
これは単なるコスト比較ではなく、社外のプロの知見を取り入れ、自社だけでは到達できなかった品質レベルとコスト競争力を手に入れるための、極めて戦略的な一手です。
見積依頼の際には、製品図面、詳細な不良状況、目標品質とコストを正確に伝えることが、的確な改善提案を引き出す鍵となります。
もし今、貴社が射出成形部品の品質問題でお困りであれば、ぜひ一度、その課題を府中プラに相談してみてはいかがでしょうか。そこには、貴社の製品の未来を大きく変える、新たな可能性が広がっているはずです。