環境応力割れ(ESC)を見逃すな!:射出成形部品が突然割れる(クラック)本当のリスクとその対策
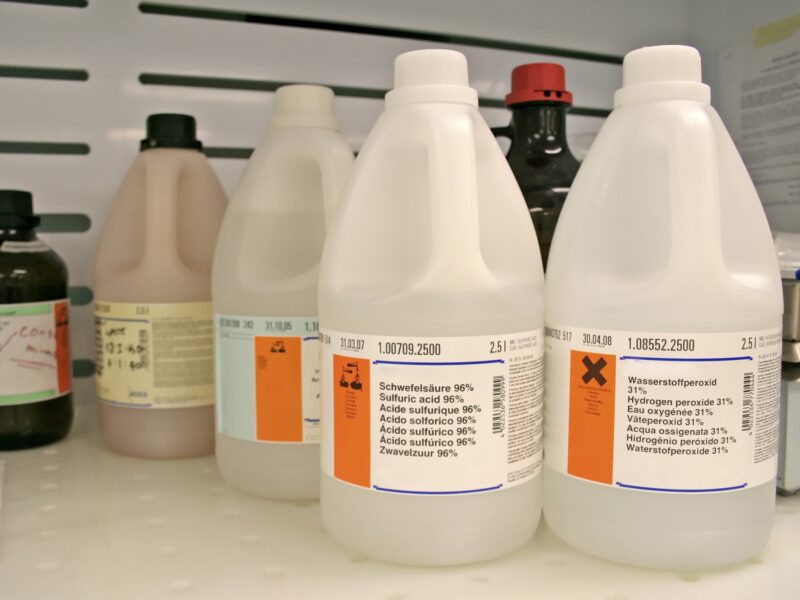
割れの原因は「力」だけではない
射出成形部品の破壊現象を考えるとき、「どれくらいの力が加わったか」、「材料の強度は十分か」という点に目を向けがちです。しかし、実際のトラブルシューティングの現場では、設計強度を大きく下回るような、ごくわずかな荷重条件で部品が割れてしまうケースが後を絶ちません。特に、高い強度を期待して採用したはずのエンプラで、「ある日突然、原因不明のクラックが発生した」というトラブルは少なくありません。
その背景に潜んでいるのが、「環境応力割れ(Environmental Stress Cracking、以下ESC)」という現象です。本コラムでは、ESCの正体を紐解き、設計者として、そしてモノづくりに関わる者として、それにどう立ち向かうべきかを体系的に整理していきます。
ESCとは何か?「応力×薬品」で進行する不可視の破壊
ESCとは、材料に応力が加わった状態で、特定の化学的環境(薬品)に晒されることによって引き起こされる、脆性的な割れ(クラック)の発生と進展を指します。ポイントは、「応力」と「化学的環境」の二つが同時に存在することで、初めて引き起こされる相乗効果による破壊であるという点です。
例えば、射出成形部品が特定の薬品に浸されていても、何の力もかかっていなければ、膨潤したり変色したりすることはあっても、すぐに割れることはないかもしれません。逆に、その薬品がない環境であれば、ある程度の力に耐えられるはずです。しかし、部品に応力がかかった状態でその薬品に触れた瞬間、事態は一変します。
化学物質がプラスチックの分子鎖の絡み合いを局所的に解きほぐし、そこに応力が作用することで、材料が本来持つ延性を失い、ガラスのように脆く割れてしまうのです。微小なクラックが表面に発生すると、そこから化学物質がさらに内部へ浸透し、応力によってクラックが次々と進展していきます。このプロセスは、目視では検知できないレベルで静かに進行し、ある日突然、致命的な破壊となって現れます。
この現象は、一般的に知られる「耐薬品性」の問題とは本質的に異なります。耐薬品性試験は、多くの場合、無応力状態で薬品に浸漬し、重量や外観、物性の変化を評価するものです。そのため、「耐薬品性データが良好な材料」を選んだとしても、ESCに対しては脆弱であるケースは珍しくありません。応力が加わった状態では、まったく異なる振る舞いを見せる――それがESCという現象の最大の罠なのです。
ESCが発生する三つの条件
ESCは、魔法のように突然発生するわけではありません。必ず、以下の三つの条件が“掛け算”のように重なったときに、そのリスクが顕在化します。設計者は、この三要素を常に頭に入れておく必要があります。
① 応力の存在
材料の内部または表面に応力が存在していることです。この「応力」には、二つの種類があります。一つは、製品使用中に外部から加わる「外部応力」です。ネジの締め付けトルクによる引張応力、部品の嵌合による圧縮応力、製品自重による曲げ応力などがこれにあたります。もう一つ、より見過ごされがちなのが、成形時に部品内部に閉じ込められる「残留応力」です。射出成形では、溶融した樹脂が金型内で不均一に冷却・固化するため、必ず内部に応力が残ります。特に、ゲート周辺や肉厚が急変する部分、ウェルドラインなどには高い残留応力が集中しがちです。たとえ外部から全く力がかかっていなくても、この残留応力だけでESCを引き起こすのに十分なトリガーとなり得ます。
② 特定の化学物質との接触
ESCを誘発する化学物質(ケミカル)との接触です。私たちの身の回りには、ESCの引き金となる物質が溢れています。
例えば、界面活性剤を含む洗剤や洗浄液、アルコール類、各種の油(潤滑油、切削油、食用油など)、可塑剤、接着剤、特定の有機溶剤、さらには一部のガスまでもが原因物質となり得ます。重要なのは、これらの化学物質がプラスチックを「溶解」させる必要はないということです。プラスチックの表面に作用し、分子の運動を助長するだけで、ESCは進行します。
③ 材料の感受性
材料そのものがESCに対して敏感である、つまり「感受性」を持っていることです。プラスチックの種類によって、ESCの起こりやすさは大きく異なります。
例えば、PCやPOM、PS、PMMA、一部のポリアミド(PA66など)は、代表的なESC感受性材料として知られています。これらの材料は、機械的強度や剛性に優れている一方で、特定の化学環境と応力の組み合わせには非常に弱いという二面性を持っています。逆に、PPやPE、あるいはPBTやPPSといった樹脂は、比較的ESCへの耐性が高いとされていますが、これも絶対ではありません。
このようにESCは、材料単体の性能ではなく、「使用環境の化学的要素」×「部品の応力状態」×「材料の感受性」という三つの要素が複雑に絡み合って発生する複合的な現象なのです。このうち一つでも条件が欠ければ、ESCのリスクは劇的に低下します。
ESCの典型的な発生パターン
ESCのリスクは、特定の業界、用途に限られたものではなく、私たちの身の回りのあらゆる製品に潜んでいます。ここでは、典型的な発生パターンをいくつか見てみましょう。
医療機器の分野
医療現場では、機器の消毒や洗浄が日常的に行われます。アルコール系の消毒液や、界面活性剤を含む洗浄液が、機器の筐体や操作ボタンに付着することは避けられません。もし、筐体がPCやABSで作られており、ネジ止めによる応力や成形時の残留応力がかかっていると、消毒作業を繰り返すうちにクラックが発生し、ある日突然筐体が破損する、といった事態が起こり得ます。
家庭用製品・家電製品の分野
キッチン用品や掃除機、洗濯機などでは、住居用洗剤や油汚れ用クリーナーが使われます。これらの製品に含まれる界面活性剤が、プラスチック部品の隙間に浸透することがあります。特に、応力が集中しやすいゲート周辺や、シャープエッジを持つリブの根元、ボスの周囲などは、残留応力が高く、かつ薬品が滞留しやすいため、ESCの起点となりやすい危険なポイントです。数日、あるいは数ヶ月後に、原因不明のクラックとして現れることがよくあります。
産業用途・自動車部品の分野
工場で使われる機械の部品や、自動車のエンジンルーム内パーツは、潤滑油、グリス、切削油、燃料といった様々な油や薬品にさらされます。例えば、PA66やPOMで作られた配管部品やギア、軸受などが、作動油に触れながら振動による応力を受け続けることで、脆化して破壊に至るケースが報告されています。
これらのケースに共通するのは、「応力が集中する部位」と「化学物質が接触・滞留しやすい部位」が一致しているという点です。設計上、応力が集中しやすいシャープなコーナーや、薬品が溜まりやすい溝やくぼみは、まさにESCの温床となります。設計者は、自分の作った部品がどのような環境で、どのように使われ、どのようにメンテナンスされるのかを具体的に想像し、この危険な交差点が生まれないように配慮する必要があります。
ESCを評価するには?
では、設計段階でESCのリスクをどのように評価すればよいのでしょうか。残念ながら、材料メーカーが提供するカタログスペックだけでは、その答えを得ることはできません。物性データシートに記載されている引張強度や曲げ弾性率といった数値は、あくまで標準的な条件下で測定されたものであり、「応力」と「薬品」の複合作用であるESCのリスクを直接示すものではないからです。
ESCの感受性を評価するための専門的な試験法も存在します。例えば、ISO 22088シリーズやASTM D1693などがそれに該当します。これらの試験では、試験片に一定のひずみを与えた状態で薬品に接触させ、クラックが発生するまでの時間を測定します。こうしたデータは、材料を選定する上での非常に重要な判断材料となります。
しかし、規格化された試験法でさえ、実使用環境を完全に再現できるわけではありません。実際の製品では、応力の種類(引張、圧縮、曲げ)や状態、薬品の濃度、温度、接触時間など、無数のパラメータが複雑に絡み合います。
したがって、最も信頼性の高い評価方法は、試作段階での実機に近い形での検証です。
ベンチテスト: 実際の製品やそれに近い形状の試作品に、想定される応力を加え、問題となる薬品を塗布または浸漬して、クラックの発生状況を観察します。
薬液浸漬クリープ試験: 一定の荷重をかけ続けた状態で薬品に浸漬し、破断するまでの時間を測定します。
ノッチ付き試験片の利用: 意図的に応力集中部(ノッチ)を設けた試験片を用いることで、より厳しい条件下での耐性を評価します。
机上の計算やデータシートの比較だけでなく、実際の使用環境をできる限り模倣した物理的なテストを行うこと。それが、見えないリスクであるESCを可視化し、定量的に把握するための唯一確実な道筋です。
ESCを防ぐには?
ESCは複合的な要因で発生するため、その対策も単一の手段に頼るのではなく、材料選定、製品設計、成形プロセスの各段階で、一貫したアプローチを取る必要があります。
① 材料面での対策
すべての基本は、適切な材料を選ぶことです。まず、製品がさらされる化学環境をリストアップし、それに対して感受性の低い樹脂を選定します。その際、単なる「耐薬品性」だけでなく、「耐環境応力割れ性」が明確に評価されたグレードを選ぶことが重要です。例えば、同じPBTやPPSであっても、グレードやガラス繊維などの充填材の有無・種類によってESC感受性は大きく異なります。必要であれば、材料メーカーに特定の薬品に対する耐ESC性のデータ提供を依頼し、候補材料を絞り込みます。
② 設計面での対策
設計段階での配慮は、ESC対策において最も効果的かつ低コストな手段です。クラックの起点となる応力集中を徹底的に避けます。具体的には、リブやボスの根元、コーナー部にはできるだけ大きなRを設けます。シャープエッジは、応力集中の元凶です。
洗浄液や油などが溜まりやすい溝、くぼみ、深いリブ構造は、可能な限り排除します。表面張力によって薬品が毛細管現象で入り込み、長期間にわたって影響を及ぼすことを防ぎます。水抜き穴を設けるなどの工夫も有効です。
急激な肉厚変化は、大きな残留応力を生み出します。できるだけ肉厚を均一にし、滑らかに変化させることで、成形時のひずみを低減します。
ネジ止めや圧入を行う場合は、過大な応力がかからないよう、トルク管理の指示や、金属カラーのインサート成形による応力緩和策を検討します。
③ 成形面での対策
成形プロセスにおける最大のテーマは、残留応力の低減です。設計がいかに優れていても、成形が悪ければ高い残留応力が残り、ESCのリスクを高めます。
ゲートの位置やサイズ、種類を工夫し、樹脂の充填がスムーズに行われ、圧力損失が少なくなるようにします。ウェルドラインが応力の高い箇所に発生しないようなゲート設計が理想です。
過剰な射出圧力や保圧は、金型内で樹脂を無理やり押し込むことになり、高い残留応力の原因となります。金型温度を適切に設定し、冷却ムラをなくすことも、ひずみの低減に繋がります。
成形後に製品を加熱処理(アニーリング)することで、内部の残留応力を緩和させる方法も、特に高精度が求められる部品や、厳しい環境で使われる部品には有効な手段です。
まとめ
環境応力割れ(ESC)は、材料の強度特性だけでは語れない、設計形状、成形プロセス、そして使用環境との複雑な相互作用によって発生する、非常に実務的な課題です。単なる強度計算や耐薬品性データの確認だけでは防ぐことはできず、部品が置かれる環境と応力の状態を深く理解したうえで、材料・設計・成形が三位一体となった総合的なアプローチが求められます。
カタログデータだけに頼らず、製造の実務とユーザーの現実を直視し、そこに根ざしたESC対策を講じること。それは、目に見える破壊だけでなく、「見えないクラック」の発生そのものを防ぐという、より高度な設計思想の試金石と言えるでしょう。この視点を持つか持たないかが、最終的に製品の寿命と、顧客からの信頼性を大きく左右するのです。