保圧が甘いと成形不良は防げない:ヒケ・バリ・ボイド…射出成形における保圧と品質トラブルの本当の関係
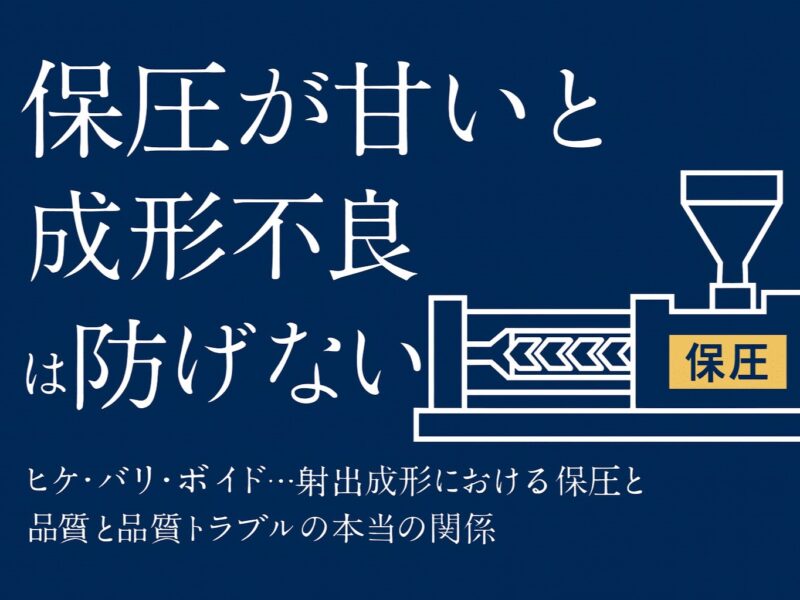
射出成形において、成形不良は材料や金型の問題だけでなく、成形条件のわずかなズレが原因となることが少なくありません。中でも「保圧」は、製品の外観・寸法・内部品質に大きな影響を与える、見落とされがちな重要パラメータです。しかし、その役割や設定の根拠が曖昧なまま、対症療法的な調整に留まっている現場も多いのではないでしょうか。本コラムでは、射出成形における保圧と成形不良の関係を体系的に整理し、ヒケ、バリ、寸法不良といった具体的なトラブル事例とともに、保圧設定の基本を解説します。保圧を正しく理解し、コントロールすることこそが、品質トラブルを未然に防ぐ鍵となります。
保圧とは ― 射出成形の「見えない品質」を決める条件
保圧の役割
射出成形プロセスにおける保圧とは、金型キャビティ内への樹脂の射出充填が完了した後、樹脂が冷却・固化する過程で発生する体積収縮を補うために、一定時間、圧力をかけ続ける工程を指します。
高温の溶融樹脂は、冷えて固まる際に必ず収縮します。もし充填後にすぐ圧力を抜いてしまうと、収縮によって樹脂の体積が減少し、製品表面のくぼみ(ヒケ)や内部の空洞(ボイド)といった致命的な不良につながります。
保圧は、ゲートを通じて追加の樹脂をキャビティ内に押し込むことで、この収縮分を補填します。これにより、樹脂を金型の隅々まで行き渡らせ、形状を安定させることができます。つまり、保圧は金型への転写性を高め、狙い通りの寸法精度や精緻な外観品質を確保するために不可欠な工程なのです。射出工程が製品の「形」を作るのに対し、保圧工程は製品の「質」を固める重要な役割を担っています。
保圧が不十分・過剰な場合の典型的な影響
保圧設定は、製品品質を左右する繊細なパラメータであり、適正範囲から外れると様々な問題を引き起こします。樹脂の冷却収縮を十分に補いきれず、体積不足に起因する不良が発生します。
ヒケ、ショートショット、ボイド:収縮を補填できずに発生する、最も代表的な不良です。
寸法不良(アンダー):成形品の収縮が大きくなり、設計値より寸法が小さくなります。
反り:製品内の圧力分布が不均一になることで、冷却後の収縮差から反りや変形が生じます。 逆に保圧が過剰になると、別の問題を引き起こします。
バリ:過剰な圧力が金型の型締め力を上回り、パーティングラインなどから樹脂がはみ出します。
寸法不良(オーバー):樹脂の収縮が抑制されすぎ、設計値より寸法が大きくなることがあります。
金型への負荷増大: 成形品が金型に固着しやすくなるほか、金型自体に過大な負荷がかかり、寿命を縮める一因となります。
材料ロス:必要以上の材料を使用することになり、コストアップにつながります。
このように、保圧は多すぎても少なすぎても品質トラブルを招くため、製品ごとに最適なバランスを見つけることが求められます。
保圧と成形不良の具体的な関係
ここでは、代表的な成形不良と保圧の関連性について、より具体的に見ていきましょう。
ヒケ・ボイド ― 保圧不足の典型例
ヒケ(表面のくぼみ)やボイド(内部の空洞)は、保圧設定が不適切であることを示す最も分かりやすいサインです。これらは共に、樹脂の冷却収縮を保圧による追加充填で補いきれていない、という単純明快な原因で発生します。
特に、製品の肉厚が厚い部分や、リブ・ボスの周辺は、他の部分より冷却に時間がかかるため、収縮量が大きくなります。保圧が不足していると、この部分的な大きな収縮に対応できず、ヒケやボイドが顕著に現れます。したがって、これらの不良を発見した場合、まず第一に疑うべきは保圧不足(圧力または時間の不足)です。
バリ ― 保圧過剰が招く外観不良
バリは、金型の分割面(パーティングライン)やエジェクタピンの隙間から、溶融樹脂がはみ出して固まる外観不良です。その直接的な原因は、キャビティ内の樹脂圧力が、金型を閉じている型締め力を上回ってしまうことにあります。
保圧はキャビティ内圧を高く維持する工程であるため、この設定が過剰であるとバリの発生リスクは一気に高まります。特に、金型の合わせ面の精度が経年劣化などで低下している場合、わずかな保圧過多でもバリにつながりやすくなります。バリ対策の基本は保圧を下げることですが、それによってヒケが発生するようなら、型締め力や金型の状態といった、より根本的な要因に目を向ける必要があります。
寸法不良・反り ― 保圧と冷却条件の複合要因
製品の寸法や形状の安定性も、保圧と密接に関係しています。保圧が不足すれば樹脂の収縮が大きくなり、製品寸法は設計値より小さくなる傾向があります。逆に保圧が過剰だと収縮が抑制され、寸法は大きくなりがちです。
また、「反り」は製品内部の残留ひずみが不均一であるために発生しますが、保圧のかけ方がこの残留ひずみの分布に大きく影響します。例えば、製品内で圧力のかかり方が偏ると、それが冷却後の収縮差となり、反りを引き起こす原因となります。ただし、反りは保圧だけでなく、金型温度の均一性といった冷却条件との複合要因で発生することが大半です。寸法や反りの問題を解決するには、保圧と冷却の両面からバランスの取れたアプローチが求められます。
ウェルドライン不良・銀条・ヤケとの関連
一見、直接的な関係がなさそうな不良にも、保圧は関わっています。
ウェルドライン不良:樹脂の合流部であるウェルドラインは、もともと強度が低い部分です。保圧が不十分だと、合流部を十分に押し固めることができず、融着が弱まって強度のさらなる低下や外観不良を誘発します。適切な保圧は、ウェルドラインの品質を向上させる効果があります。
銀条・ヤケ:銀条は材料中のガスが原因ですが、保圧が低いとキャビティ内でガスが膨張しやすくなり、銀条が目立つことがあります。逆にヤケや黒点は、保圧が過剰な場合に発生リスクが高まります。高すぎる保圧がゲート付近で断熱圧縮を引き起こし、樹脂を熱分解させてしまうことがあるためです。
このように、保圧は様々な不良現象と相互に関連しており、総合的な視点での管理が重要です。
適切な保圧設定の考え方と現場の注意点
最適な保圧設定は、試行錯誤の中で見つけ出す必要がありますが、その基本となる考え方と注意点を押さえておきましょう。
保圧圧力と保圧時間の基準
保圧は「圧力」と「時間」の組み合わせで設定します。
保圧圧力:明確な正解はありませんが、一般的には射出圧力(1次圧)の50~80%程度を目安として調整を始めます。重要なのは、実際の成形品を見ながら、ヒケがなく、かつバリも出ない圧力範囲を探ることです。材料の粘度や製品形状に応じて最適値は変わります。
保圧時間:保圧をかける時間は「ゲートシールタイム」と連動させることが基本です。ゲートシールタイムとは、キャビティの入口であるゲートが固化して塞がるまでの時間です。ゲートが固まる前に保圧を止めると、樹脂が逆流してヒケの原因となります。逆に、固まった後も圧力をかけ続けるのは無駄です。したがって、保圧時間はゲートが固まるまでかけ続けることを原則とし、その時間を基準に設定します。
なお、保圧条件の最適化は学術論文や業界技術報告でも繰り返し指摘されており、たとえば「保圧力の増加は樹脂の充填密度を高め、冷却時の体積収縮を抑制することで成形収縮の安定化に寄与する」ことが実験的に示されています(古河電工時報第133号)。また、保圧圧力は射出圧力の1/2~1/3を目安に、ヒケが発生しない範囲で低めに設定することが推奨されており、保圧時間はゲートが固化するまで継続することが重要であると各種技術資料でも明記されています。さらに、JISやISOなどの業界標準でも、射出成形品の寸法安定性や品質管理のために保圧工程の適切な設定が重要であると規定されています(例:JIS K 6911、ISO 294-3)。
金型構造と製品形状を踏まえた設定
成形条件の数値だけでなく、金型や製品の形状を理解することが、より良い保圧設定につながります。ゲートの位置や大きさ、製品の肉厚分布などを考慮し、圧力がキャビティの隅々まで効果的に伝わっているかを意識する必要があります。例えば、ゲートから遠い箇所でヒケが発生している場合、単純に保圧を上げるだけでなく、圧力の伝わり方を改善するアプローチ(多段保圧など)も有効です。
不良発生時のトラブルシューティング
不良発生時の保圧調整は、他の要因との関係性を念頭に置くことが大切です。
ヒケ・ボイド発生時:まずは保圧圧力や保圧時間を上げることを検討します。それでも改善しない場合は、樹脂温度や金型温度が低すぎないかなど、他の条件も見直します。
バリ発生時:第一に保圧の低減を試みます。しかし、それでヒケが出る場合は、保圧以外の要因、特に金型の合わせ精度や型締め力に問題がないかを確認することが不可欠です。
寸法不良・反り発生時:寸法に応じて保圧を上下させると同時に、反りの原因となりやすい冷却バランス(金型温度の均一性など)を見直すことが、根本的な解決につながります。
銀条・ヤケ発生時:銀条には材料乾燥を徹底した上で保圧をやや高めに、ヤケには保圧が高すぎないかを確認し、温度条件と合わせて総合的に調整します。
まとめ
本コラムで見てきたように、保圧は単なる後工程の圧力設定ではなく、製品の歩留まりと品質を決定づける「見えない品質管理」の要です。ヒケ、バリ、ボイドといった不良を個別の現象として捉えるのではなく、その背景にある保圧と、他の成形条件や金型との関係性を常に意識することが、安定した量産と不良削減への最短ルートとなります。現場で日々向き合う品質トラブルを未然に防ぐためにも、今一度、保圧の役割とその最適設定について見直してみてはいかがでしょうか。当社、府中プラは、そうした品質改善への取り組みをサポートいたします。
引用元
- 古河電工時報第133号「射出成形における保圧条件と成形品品質の関係」
- JIS K 6911「プラスチック-射出成形品-一般的特徴」/ISO 294-3「Plastics — Injection moulding of test specimens of thermoplastic materials — Part 3: Small plates」