ゲート位置設計が決め手になる:射出成形の充填性と外観品質を左右する基本ルール
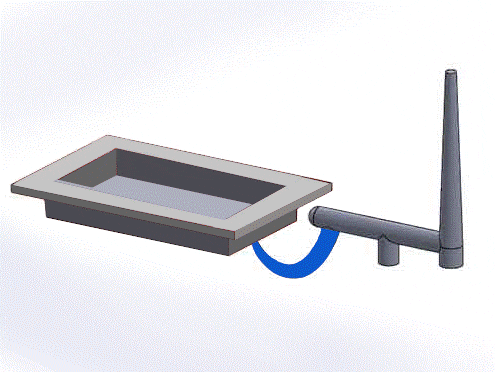
射出成形品の品質は、設計初期の「ゲート位置」の決定に大きく左右されます。ゲートは単なる樹脂の入口ではなく、その位置が充填性、外観、強度、寸法精度といった製品の根幹をなす品質を決定づけるからです。不適切なゲート位置は、ショートショットやウェルドラインといった不良に直結し、量産時のコスト増の原因となります。本コラムでは、射出成形におけるゲート位置設計の基本ルールを解説し、高品質なものづくりに不可欠な実務的ポイントをご紹介します。
ゲート位置が製品品質に与える影響
ゲート位置は、溶融した樹脂が金型キャビティに流れ込む最初の起点です。この起点の設定が、下流で起こるすべての現象を支配するといっても過言ではありません。
充填性とショートショットのリスク
ゲート位置が製品品質に与える最も基本的な影響は、「充填性」です。ゲート位置が不適切だと、樹脂の流れが途中で滞ったり、圧力損失が大きくなったりして、製品の末端まで樹脂が届かない充填不足が発生します。例えば、複雑な形状の製品において、薄肉部やリブなどを通過した先に充填すべき領域があると、その手前の障害物によって圧力が大幅に低下し、ショートショットのリスクが高まります。
特に、近年需要が高まっている薄肉・軽量化された部品や、精密で複雑な形状を持つ部品ほど、樹脂の流動抵抗は大きくなります。このような製品では、ゲート位置のわずかな違いが充填性を劇的に変化させるため、流動距離を最短にし、樹脂がスムーズに流れる経路を確保できる位置にゲートを設けることが、安定生産の絶対条件となります。
外観品質への影響
製品の外観は、その商品価値を決定づける重要な要素です。ゲート位置は、この外観品質に直接的な影響を及ぼします。
ウェルドライン:ゲートから流れ出た樹脂が、製品内のボス等の障害物を迂回した後や、複数のゲートから流れた樹脂が合流する地点に発生する線状の模様です。このウェルドラインは外観を損なうだけでなく、強度低下の原因にもなります。ゲート位置を工夫することで、ウェルドラインの発生位置を意匠面から目立たない場所へ移動させることが可能です。
フローマーク:ゲート周辺に発生する、樹脂が流れた跡が残る模様です。特に意匠面に直接ゲートを設けた場合、このフローマークが顕著に現れ、品質クレームの原因となります。
ヒケ:ゲートは最後に固化する部分であり、保圧をかける際の圧力導入点となります。しかし、ゲートが製品の他の部分より先に固化してしまうと、肉厚部の収縮を補う樹脂を供給できなくなり、ゲートから遠い部分に「ヒケ」が発生します。逆に、ゲート周辺の肉厚が厚いと、ゲート自体にヒケが発生することもあります。
ジェッティング:ゲートから射出された樹脂が、キャビティ壁面にぶつからずに、まるで糸を噴出するように蛇行しながら充填される現象です。これも外観不良となり、ゲートの位置や形状、射出条件が不適切な場合に発生します。
これらの外観不良を避けるためにも、「意匠面(製品の顔となる面)にはゲートを設けない」というのが、ゲート位置設計における鉄則となります。
機械的特性と寸法精度への影響
目に見える外観だけでなく、製品の信頼性を担保する機械的特性や寸法精度もゲート位置に左右されます。もし、強度の低いウェルドラインが、製品使用時に力がかかるフック部や、ネジで締め付けるボスの根元といった応力集中部に発生した場合、容易に破損するリスクを抱えることになります。ゲート位置を適切に設計し、ウェルドラインを応力のかからない安全な場所へ移動させることは、製品の信頼性設計そのものと言えます。
また、寸法精度にも影響を与えます。樹脂はゲートからの距離によって圧力のかかり方が異なり、それに伴って冷却時の収縮率も変化します。一般的にゲートに近い部分は圧力がよくかかり収縮が小さく、ゲートから遠い部分は圧力が低下し収縮が大きくなる傾向があります。この収縮率の差が、製品全体の「反り」や「寸法ばらつき」の原因となるのです。
ゲート位置設計の基本ルール
では、これらの影響を踏まえ、どのようにゲート位置を決定すればよいのでしょうか。ここでは、設計の基本となる3つのルールを解説します。
樹脂の流れを意識した配置
最も基本的なルールは、樹脂がキャビティ内をスムーズかつ均一に流れるようにゲートを配置することです。
原則として最も肉厚な部分にゲートを設ける:樹脂は「太いところから細いところへ」流れるのが理想です。最も肉厚な部分にゲートを設けることで、最後まで保圧が効きやすくなり、製品全体のヒケを効果的に抑制できます。肉薄部にゲートを設けると、そのゲートが早期に固化してしまい、奥にある肉厚部の収縮を補えなくなります。
流動距離が最短・均等になる位置を選ぶ:可能であれば製品の中心付近にゲートを設けることで、樹脂が放射状に広がり、末端までの流動距離を均等にできます。これにより、充填バランスが向上し、反りの原因となる収縮の偏りを最小限に抑えることができます。
複数ゲートの場合は流動バランスを最優先する:大型製品などで複数のゲートを設ける場合は、各ゲートから充填される樹脂が同時に末端に到達するように、ランナーの長さや太さを調整し、流動バランスを厳密に確保する必要があります。バランスが崩れると、ウェルドラインの位置がずれたり、片側でバリ、もう片側でショートショットといった問題が発生します。
外観面・重要機能面を避ける
製品の価値を損なわないために、ゲートを設けてはならない「禁止領域」を明確に定義することが重要です。
意匠面・光学面:製品の「顔」となるデザイン面や、レンズのような透明性が求められる光学的な機能を持つ面には、ゲート痕やフローマークが外観・性能を著しく損なうため、原則としてゲートを設けてはいけません。
気密面・摺動面:Oリングが接触するシール面や、他の部品とこすれ合う摺動面にゲート痕の凹凸があると、液漏れや摩耗、動作不良の原因となります。これらの機能面もゲートの配置を避けるべきです。
もし、製品の構造上、どうしてもこれらの面へのゲート設置が避けられない場合は、ゲート痕が極力目立たない種類のゲート(後述のサブマリンゲートなど)を選定したり、後加工でゲート痕を除去したりといった特別な対策が必要になります。
ウェルドラインの位置と強度設計
ウェルドラインの発生は避けられない場合も多いため、その「位置をコントロールする」という発想が重要になります。
ゲートの位置を変えれば、樹脂の合流地点、すなわちウェルドラインの発生位置も変わります。この性質を利用して、製品使用時に応力が集中する部分(ネジ止め部、勘合用の爪、薄肉のヒンジ部など)にウェルドラインが形成されないようにゲート位置を設計します。 これは、製品の強度を確保するための非常に重要な設計アプローチです。
近年では、流動解析シミュレーションの活用が一般的になっています。流動解析を用いれば、金型を製作する前に、コンピュータ上でゲート位置による樹脂の充填パターンやウェルドラインの発生位置を高い精度で予測できます。これにより、設計段階で強度的なリスクを洗い出し、最適なゲート位置を論理的に見つけ出すことが可能になります。勘や経験則に頼るだけでなく、シミュレーションによる事前検証を行うことが、手戻りのない効率的な開発の鍵です。
これらの知見を踏まえ、単なる経験や勘だけでなく、科学的根拠や標準規格に基づき論理的にゲート位置を決定することが、安定した高品質成形への近道となります。
ゲート種類ごとの注意点と使い分け
ゲートには様々な種類があり、製品の形状、材質、要求品質に応じて使い分けられます。各種ゲートの詳細は別のコラムに譲りますが、代表的なものの特徴を簡単にご紹介します。
ピンゲート:ゲートを自動で切断でき、量産性に優れます。ゲート痕が点状に残るため、外観が重視される箇所への採用は慎重な検討が必要です。
サイドゲート:製品の側面に設ける最も基本的なゲートです。流れの方向性を制御しやすく、比較的大きな断面積を確保できますが、ゲートカットの工程が必要です。
ダイレクトゲート: 圧力損失が極めて少なく、流動性に優れるため、大型製品や肉厚製品に適しています。ゲート痕が大きく残るため、後処理が必須です。
サブマリンゲート(トンネルゲート):金型が開く際に自動でゲートが切断され、かつゲート痕が製品の側面や裏面など目立たない場所に隠れるため、外観を重視する製品に多用されます。
ゲート位置設計で失敗しないための実務ポイント
最後に、ゲート位置の設計で失敗を避けるための、より実務的なポイントを5つ挙げます。
形状・用途・外観要求を正確に把握する:設計の第一歩です。その製品がどのように使われ、どこに力がかかり、どの面がお客様の目に触れるのかを設計者が正確に理解していなければ、最適なゲート位置は決められません。
材料特性(流動性・収縮率・ガス抜け性)を考慮する:材料によって樹脂の流れやすさや固まりやすさは大きく異なります。ガラス繊維入りのような流動性の低い材料であれば流動距離を短く、PPのような収縮率の大きい材料であればヒケ対策をより重視するなど、材料特性に合わせたゲート設計が不可欠です。
可能な限り流動解析を実施する:経験則も重要ですが、複雑な形状の製品では限界があります。流動解析を活用することで、充填パターン、ウェルドライン、ヒケ、反りといった潜在的な問題を可視化し、設計段階で対策を講じることができます。これは、後工程での手戻りを防ぐ最も有効な手段の一つです。
金型構造(スライド・インサートの有無)も考慮する:アンダーカット処理のためのスライドコアや、金属部品をインサート成形する場合、それらが樹脂の流れを妨げる障害物になります。金型の構造を理解し、これらの機構部品を避ける、あるいは影響を最小限にするゲート位置を検討する必要があります。
初回試作でゲート位置変更の余地を残す設計を意識する:設計とシミュレーションで万全を期しても、実際の成形では予期せぬ現象が起こり得ます。そのため、金型製作時に、後からゲート位置の変更や追加がしやすいように、あらかじめ候補地に肉盛りをしておくなどの「逃げ」を設けておくことも、量産立ち上げをスムーズに進めるための賢明な判断です。
まとめ
射出成形の品質は、設計初期のゲート位置選定に大きく依存します。充填性、外観、強度といった多面的な要求をバランス良く満たすには、理論と経験、そしてシミュレーションの活用が不可欠です。最適なゲート位置の追求は、不良リスクを低減し、安定した品質の製品を生み出すための「設計の要」と言えます。当社では、お客様の製品に最適なゲート設計をご提案し、高品質なものづくりをサポートします。設計段階からぜひご相談ください。