ホットランナーが量産現場を変える:材料ロス削減・サイクル短縮・品質安定を実現する導入メリットとは?
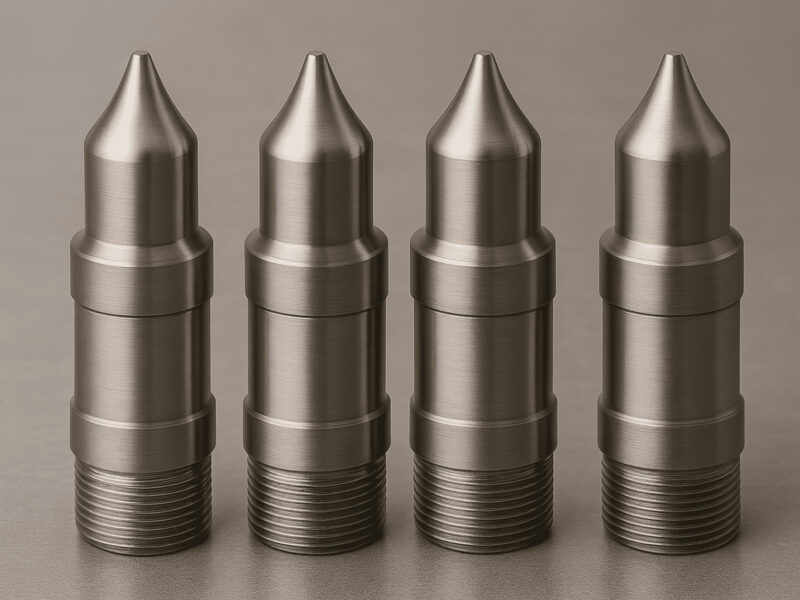
射出成形の量産現場では、品質の安定化とともに、材料ロスの削減や生産性向上が常に求められます。そうした課題を解決する有効な手段のひとつがホットランナーの活用です。本コラムでは、ホットランナーがもたらす具体的なメリットを、コスト・品質・生産性の観点から実務目線で解説します。
材料ロス削減:ランナー不要で無駄を省く
射出成形におけるコスト管理において、材料費の最適化は最重要課題の一つです。特に、製品の高機能化に伴い、高価なエンプラやスーパーエンプラの採用が増える中、材料の無駄をいかに無くすかが企業の収益性を左右します。この課題に対し、ホットランナーは非常に直接的かつ効果的な解決策を提示します。
コールドランナーの課題
従来の射出成形で広く用いられてきたコールドランナー方式では、成形機から射出された溶融樹脂が製品の形(キャビティ)に充填されるまでの通り道であるスプルーとランナーも、製品と同時に金型内で冷却・固化します。
つまり、製品を1つ作るごとに、必ずスプルーとランナーがロスとして発生するのです。この固化したランナーは、製品から切り離された後、粉砕して再利用されるか、廃棄されます。
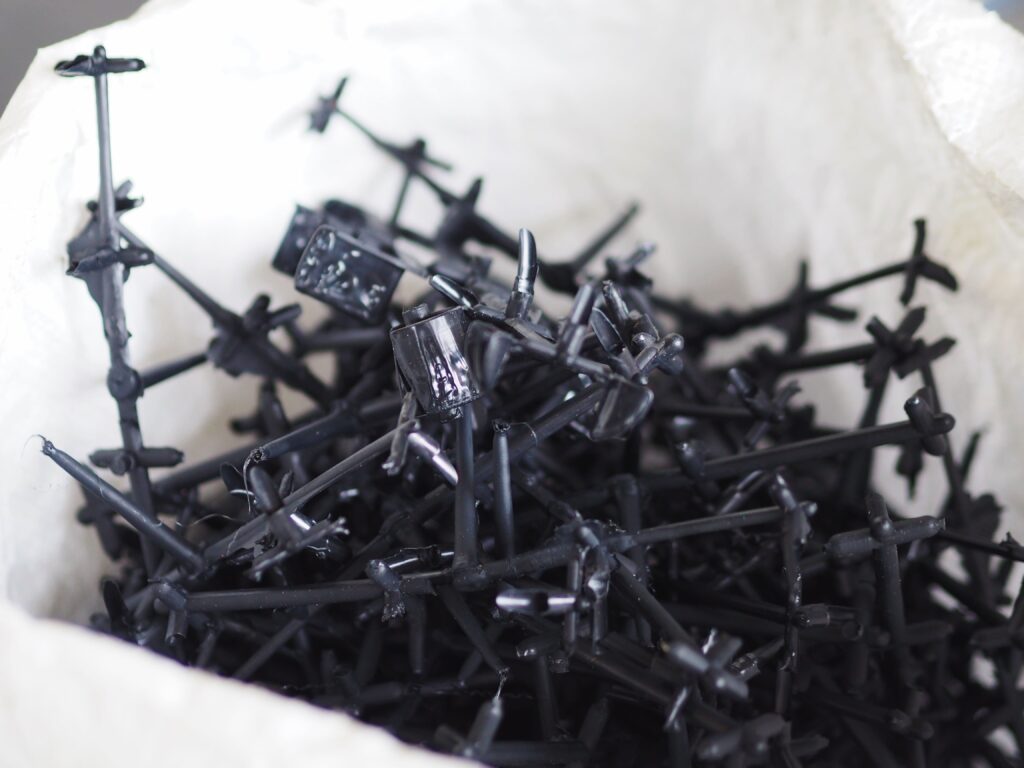
しかし、リグラインド材の利用には限界があります。粉砕・再溶融という熱履歴を繰り返すことで樹脂の物性が低下するリスクは避けられません。また、粉砕時に異物が混入する可能性もゼロではなく、品質への影響を懸念してリグラインド材の使用を制限、あるいは全面的に禁止しているケースも少なくありません。特にガラス繊維などで強化された樹脂の場合、粉砕によって繊維が短くなり、本来の強度を発揮できなくなるという問題もあります。
その結果、発生したランナーの多くが、最終的に産業廃棄物として処分されることになります。製品そのものよりもランナーの方が重いということも珍しくなく、高価な材料であればあるほど、この材料ロスは大きなコスト負担としてのしかかります。
ホットランナーによるランナーレス成形
ホットランナーシステムは、こうしたコールドランナーの構造的な課題を根本から解決します。金型内部にヒーターで加熱・温度制御された流路(マニホールド)と射出ノズルを内蔵し、樹脂を常に溶融状態に保ちながら、製品が成形されるキャビティの直前まで送り届けます。
これにより、金型が開くときには製品部分だけが固化しており、スプルーやランナーは発生しません。これがランナーレス成形です。製品を作るために必要な樹脂だけを使用するため、材料使用量を大幅に削減し、歩留まりを劇的に向上させることができます。
この効果は、製品サイズが小さいほど、また1つの金型で多くの製品を同時に作る多数個取りであるほど顕著になります。例えば、製品1個の重量が5g、ランナー重量が20gの8個取り金型があったとします。コールドランナーの場合、1ショットで消費する樹脂は(5g×8個)+ 20g = 60gとなり、そのうちの3分の1にあたる20gがロスになっていました。ホットランナーを導入すれば、この20gのロスがゼロになり、材料使用量を33%も削減できる計算になります。
材料費の削減は、企業の利益に直接貢献します。特に年間数百万ショットに及ぶような大量生産品においては、その効果は計り知れません。
サイクルタイム短縮:生産性とコストの両立
製造現場における時間は、そのままコストに直結します。成形加工費は成形機の稼働時間で決まるため、1ショットあたりのサイクルタイムをいかに短縮するかが、生産能力と価格競争力を高める上での鍵となります。
冷却時間の短縮
射出成形の全工程(型締め→射出→保圧→冷却→型開き→製品取り出し)の中で、最も多くの時間を占めるのが冷却時間です。製品が金型内で十分に冷えて固まらなければ、取り出す際に変形したり、突き出しピンの跡が強く残ったりする原因となるため、この時間は非常に重要です。
コールドランナー方式の場合、製品だけでなく、ランナー、特に最も肉厚になるスプルー部分が完全に固化するまで型を開くことができません。製品部分の冷却は終わっていても、分厚いランナーが固まるのを待つ必要があるため、冷却時間が不必要に長くなってしまうのです。
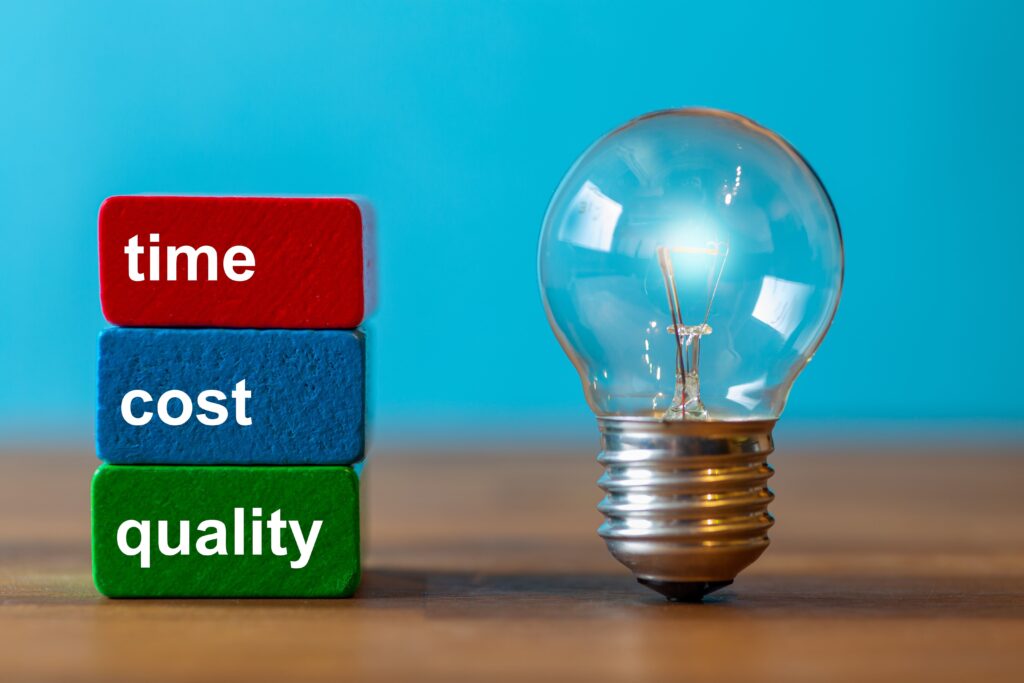
一方、ホットランナーでは冷却・固化させるのは製品部分のみです。ランナー部分は常に溶融しているため、その冷却を待つ必要が一切ありません。冷却時間は、純粋に製品の形状と肉厚に応じて決まる、物理的に必要な最短時間で設定できます。
これにより、1ショットあたりのサイクルタイムを数秒、場合によっては数十パーセント短縮することも可能です。仮にサイクルタイムが25秒から20秒に短縮された場合、時間あたりの生産量は25%も向上します。この積み重ねが、納期短縮や成形加工費の低減に繋がり、生産計画全体の柔軟性を高めることに貢献します。
自動化との相性の良さ
人手不足が深刻化する現代の製造業において、生産ラインの自動化は避けて通れないテーマです。ホットランナーは、この自動化と極めて相性が良いという大きなメリットを持っています。
コールドランナーの場合、成形された製品とランナーを切り離すゲートカットという工程が必ず発生します。これを人手で行えば労務費がかかり、作業者による品質のばらつきも生じます。また、切り離したランナーを回収し、粉砕機へ運ぶといった付帯作業も必要です。
ホットランナーによるランナーレス成形では、これらの工程がすべて不要になります。取り出しロボットは、金型から製品だけをシンプルに取り出し、そのまま次の工程へ移送できます。ランナーが製品に絡まったり、ロボットのチャック部に引っかかったりするトラブルがないため、ロボットの動作を高速かつ安定させることができ、信頼性の高い自動化ラインを構築しやすくなります。人の介在を最小限にすることで、ヒューマンエラーをなくし、24時間稼働のような安定した連続量産体制を確立できます。
品質の安定化と外観不良の低減
成形品の品質は、溶融した樹脂が金型内のキャビティをどのように流れ、どのように固まるかによって決まります。ホットランナーは、樹脂の温度と圧力を精密にコントロールすることで、コールドランナーでは解決が難しかった品質課題にも優れた効果を発揮します。
流動性・充填性の向上
コールドランナー方式では、溶融樹脂が長いランナーを通過する間に金型に熱を奪われ、温度が徐々に低下してしまいます。これにより樹脂の流動性が悪化し、ショートショットやウェルドラインといった成形不良が発生しやすくなります。
対してホットランナーは、ゲートの直前までヒーターによって樹脂温度を理想的な状態に保ちます。そのため、樹脂は高い流動性を維持したままキャビティに充填され、成形機からの射出圧力も効率的に伝わります。結果として、薄肉の製品や複雑な形状であっても、安定して隅々まで樹脂を充填することができ、ショットごとの充填状態が安定します。これにより、製品寸法のばらつきも低減し、常に均一な品質の製品を量産することが可能になるのです。
ゲート痕の改善
製品に必ず残るゲートの痕跡は、外観品質を左右する重要な要素です。特に、家電製品の筐体や化粧品容器など、ユーザーの目に直接触れる部品では、ゲート痕の美しさが製品価値を決めると言っても過言ではありません。
コールドランナーで一般的に用いられるピンポイントゲートは、ゲート痕が小さく目立ちにくい利点がありますが、どうしても小さな突起や白化した痕が残り、後工程でニッパーによる手作業のカットが必要になることもあります。
この課題に対し、ホットランナーではバルブゲートという方式が非常に有効です。これは、ゲート部に内蔵されたピンを機械的に前後させ、ゲートを開閉する仕組みです。射出・保圧が完了した瞬間にピンがゲートを物理的に塞ぐため、樹脂の糸引きや垂れを防ぎ、ゲート痕を極めて平滑で目立ちにくく仕上げることができます。この滑らかなゲート痕は、ゲートカットという後工程そのものを不要にし、コストダウンと品質向上を同時に実現します。
歪み・反り・ヒケの低減にも寄与
成形品が設計通りの形状にならず、変形してしまう歪み、反りや、表面が凹んでしまうヒケは、成形後の冷却収縮が不均一であることが主な原因です。ホットランナーは、コールドランナーに比べて圧力損失が少ないため、キャビティ内の隅々まで均一な圧力をかけることができます。これにより、製品全体の保圧効果が高まり、収縮を均等にコントロールしやすくなるため、内部応力のバランスが整い、寸法不良のリスクを抑制する効果が期待できます。
設計自由度の向上と複雑形状への対応
ホットランナーは、既存の成形を効率化するだけでなく、これまでの成形技術では実現が難しかった製品設計や複雑な形状を可能にするポテンシャルを持っています。
ゲート配置の最適化が可能
製品の品質は、樹脂を注入する入り口であるゲートをどこに配置するかによって大きく左右されます。理想的なゲート位置は、樹脂の流れを最適化し、ウェルドラインや反りの発生を最小限に抑える場所に設定されるべきです。
しかし、コールドランナーの場合、ランナーの物理的な通り道を確保する必要があるため、ゲートを配置できる位置が制限されてしまうことが少なくありません。「品質的にはここがベストだが、ランナーが通せない」という理由で、妥協した位置にゲートを設けざるを得ないケースは多々あります。
ホットランナーは、金型内の任意の位置にノズルを配置できるため、ゲート位置の自由度が格段に向上します。流動解析によって導き出された、品質上最も理想的な場所にピンポイントでゲートを設定することが可能になり、設計者が意図した通りの品質を、より高いレベルで実現することができます。
複雑形状・多点取り製品への対応力
大型製品や、リブやボスが入り組んだ複雑な形状の製品では、1点のゲートから樹脂を充填するだけでは均一に行き渡らせることは困難です。
こうした製品に対し、ホットランナーは複数のゲートを製品の要所に配置する多点ゲートで対応できます。さらに、各ゲートのバルブピンの開閉タイミングを個別に制御するシーケンシャル制御を用いれば、ウェルドラインの位置を目立たない箇所へ移動させたり、充填バランスを最適化したりすることが可能です。これにより、大型で薄肉な製品や、意匠性と機能性が両立する部品の一体成形が可能となり、部品点数の削減や製品の軽量化にも大きく貢献します。
まとめ
ホットランナーは、単なるランナー削減の仕組みにとどまらず、材料ロス削減によるコスト競争力、サイクル短縮と自動化による生産性、そして充填性向上やゲート痕改善による製品品質という、量産現場が求める3つの要素を同時に高めることができる、極めて実践的なソリューションです。
その導入には初期投資が伴いますが、材料費の大幅な削減効果や生産性の向上、不良率の低減といったメリットを考慮すれば、トータルコストでは大きなリターンが期待できます。ただし、その効果を最大限発揮するには、製品設計や材料選定、金型仕様に応じた適切な計画と運用が不可欠です。
府中プラは、長年にわたり培ってきた金型製作と射出成形のノウハウを基に、こうしたホットランナーの導入・活用を含め、お客様の課題解決に繋がる最適な金型・成形ソリューションをご提案します。ホットランナーによる生産革新にご興味がございましたら、ぜひ一度ご相談ください。