射出成形におけるランナー設計の基本と実務ポイント:材料ロス・品質・量産安定性を左右する“見えない流路”の設計基準
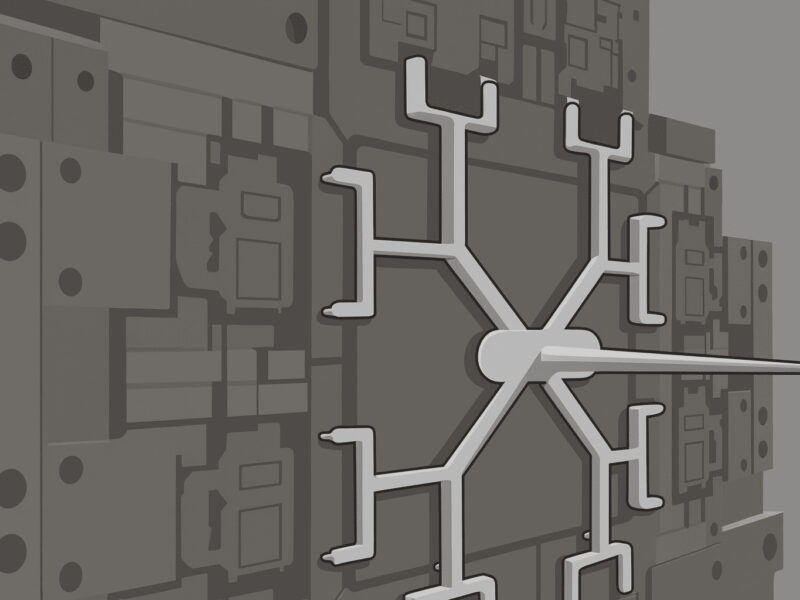
射出成形の金型において、ランナーは単なる樹脂の通り道ではありません。ランナー設計の巧拙は、樹脂の流れ方から製品品質、材料ロス、成形サイクルにまで大きく影響を及ぼします。特にコールドランナー方式では、ランナー形状や配置の最適化が、安定した量産とコスト削減に欠かせない重要設計要素です。この一見“捨てられる部分”の設計こそが、高品質なモノづくりを根底から支えているのです。本コラムでは、コールドランナー金型における基本設計と、現場でよくあるトラブルを防ぐための実務ポイントを解説します。
ランナーの役割と設計の重要性
ランナーの最も基本的な役割は、射出成形機のノズルから射出された溶融樹脂を、製品形状をかたどる空間である「キャビティ」の入り口、すなわち「ゲート」まで、確実かつ均一に搬送することです。このシンプルな役割の裏には、高品質な製品を安定して生み出すための重要な要素が隠されています。
「確実」に搬送するとは、必要な圧力と速度を保ち、樹脂が途中で冷え固まることなく、キャビティの隅々まで行き渡らせることを意味します。もしランナーが細すぎたり、長すぎたりすれば、樹脂が流れる際の抵抗(圧力損失)が大きくなり、充填不足、いわゆる「ショートショット」を引き起こします。
さらに重要なのが「均一」に搬送するという点です。特に、一つの金型で複数の製品を同時に成形する「多個取り」の場合、各キャビティに樹脂が同じタイミングで、同じ圧力、同じ温度で到達しなければ、製品ごとに寸法や重量、外観にばらつきが生じてしまいます。適切なランナー設計は、こうした充填バランスをコントロールし、製品品質のばらつきを抑制する上で不可欠なのです。
また、ランナー設計はコスト面にも直接的な影響を与えます。コールドランナー方式では、ランナー部分の樹脂は製品と共に固化し、成形後に製品から切り離されて廃棄されるのが一般的です。つまり、ランナーの体積が大きいほど、材料のロスが増大します。さらに、ランナー部分が冷え固まる時間も成形サイクルの一部です。不必要に太いランナーは冷却に時間がかかり、結果として生産性を低下させ、量産コストを押し上げる要因となります。
このように、ランナーは単なる「通り道」ではなく、品質、コスト、生産性を同時に最適化するための、極めて戦略的な設計要素であると言えます。
コールドランナーの基本構造
コールドランナーの構造を理解することは、適切な設計を行うための第一歩です。ランナーシステムは、主に3つの部分から構成されています。
スプルー (Sprue)
スプルーは、射出成形機のノズルから射出された溶融樹脂が、最初に金型内に入ってくる部分です。ノズルとの接触を確実にするため、先端は球面状にくぼんでいます。樹脂はここから金型の分割面(パーティングライン)に向かって、テーパー状(先細り)の流路を通過します。このテーパー、すなわち離型勾配は、成形後に固化したスプルーを金型からスムーズに取り出すために不可欠な設計です。
メインランナー (Main Runner)
スプルーを通過した樹脂は、次にメインランナーへと流れ込みます。メインランナーは、スプルーから分岐し、各製品キャビティへと樹脂を分配するための、いわば幹線道路のような役割を担います。多個取り金型の場合、メインランナーからさらに細い流路へと枝分かれしていきます。
サブランナー (Secondary or Sub-Runner)
メインランナーから分岐し、最終的に各キャビティのゲートへと樹脂を導く細い流路がサブランナーです。生活道路に例えることができるでしょう。多個取り金型では、このサブランナーの長さや太さを均等に設計することで、前述した充填バランスを保つことが求められます。例えば、4個取りの金型であれば、スプルーを中心にH型やX型(トーナメント方式)にランナーを配置し、スプルーから各ゲートまでの距離と形状が全く同じになるように設計するのが理想的です。
これらのランナーは、金型のパーティングライン上に、固定側と可動側の両方にまたがって半円状などの溝として加工され、金型が閉じたときに円形や台形といった一つの閉じた流路を形成します。製品の数(取り個数)やゲートを設けたい位置に応じて、これらのランナーをいかに効率よく、かつバランスを考慮して配置するかが、設計者の腕の見せ所となります。
ランナー設計の基礎と実務ポイント
優れたランナー設計を行うためには、いくつかの基本的な基準と実践的なポイントを理解しておく必要があります。これらは相互に関連し合っており、一つをおろそかにすると全体のバランスが崩れてしまいます。
ランナー径の設定
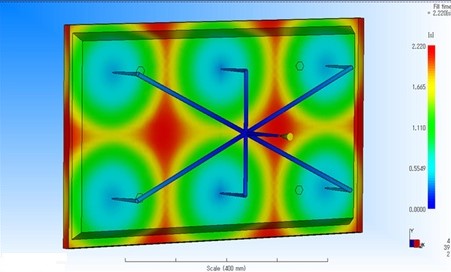
ランナーの直径(断面積)は、「太すぎず、細すぎず」という絶妙なバランスが求められます。細すぎると圧力損失でショートショットやヒケを招き、せん断発熱による樹脂劣化のリスクも高まります。一方、太すぎると材料ロスが増大し、冷却時間が長引くため成形サイクルが延長します。最適な径は、使用樹脂の流動性、製品サイズ、充填速度などを総合的に判断し、CAE流動解析なども活用しながら決定します。
なお、CAE流動解析を活用したランナー設計は、樹脂の充填バランスや圧力損失の予測精度向上に有効であることが学術的に報告されています。
ランナー長さと配置
ランナーはスプルーから各ゲートまでを「最短距離」で結ぶのが基本です。流路が長くなるほど、圧力損失、材料ロス、樹脂の温度低下が大きくなるためです。多個取り金型では「ランナーバランス」が極めて重要で、スプルーから各ゲートまでの流路長や形状をすべて等しく設計します。これにより、全キャビティに樹脂が均等に充填される「バランス充填」が実現でき、品質のばらつきを抑えます。
ランナー径や配置の最適化は、ウェルドライン発生位置や製品強度に大きく影響することが、成形加工学会誌のシミュレーション研究でも示されています。
角部のR(丸み)処理
ランナーの分岐点やコーナー部には、必ず滑らかなR(丸み)を付けます。角が鋭角だと樹脂の流れが滞留し、圧力損失や材料劣化(焼け)の原因となります。適切なRは、樹脂をスムーズに方向転換させ、圧力損失と品質劣化のリスクを低減します。
ランナー冷却設計
コールドランナーは製品同様に冷却が必要です。特に径が太い部分は完全に固化するのに時間がかかり、冷却不足はランナーの変形や金型内での破損に繋がります。太いランナーの周囲に冷却水管を効果的に配置し、効率的な冷却を促す設計が、成形サイクルの最適化と安定生産に不可欠です。
ランナー設計に起因するトラブルと対策
慎重な設計でも現場ではトラブルが発生しがちですが、ランナー設計に起因することが珍しくありません。
充填不足やショートショット
主な原因は、ランナー径の不足、流路長の不均衡、不適切なゲート位置です。対策は、ランナー径の拡大や、流路長を短く均等にするレイアウトの見直しが基本です。樹脂が流れにくい箇所へのゲート設定も原因となるため、ゲート位置の変更も有効です。
ウェルドラインの強度低下
複数の樹脂流が合流するウェルドラインは強度が低下しがちです。ランナーの配置やゲート数を調整し、ウェルドラインの発生位置を強度が求められない箇所や目立たない箇所へ移動させます。また、樹脂がより高い温度・圧力で合流するよう設計を調整し、融着を改善することも重要です。
ランナー取り外し性の悪化
スプルーやランナーが金型から離れないトラブルは、離型勾配の不足や表面の粗さ、冷却不足が原因です。適切な離型勾配を確保し、ランナー表面を研磨するほか、突き出しピンの配置バランスを最適化して破損を防ぐ設計が求められます。
材料ロスの増大
過剰に太いランナー径や不必要に長い流路は、直接的なコスト増に繋がります。CAE解析などを活用し、品質を担保できる必要最小限のランナー径と最短の流路を追求する、コストを意識した設計が不可欠です。 ランナー体積の最小化による材料ロス削減は、コスト低減の観点からも重要です。
ランナー設計と金型コスト・量産性の関係
適切なランナー設計は、品質だけでなくコストと量産性にも直結し、大きな経済的メリットをもたらします。まず、無駄な材料ロスを抑制できます。最適化されたランナーは体積が最小限に抑えられ、成形ごとに廃棄される樹脂量が減り、直接的な材料コストの削減に繋がります。
次に、成形サイクルの短縮に貢献します。ランナーが細く短ければ冷却時間も短縮され、長期的な量産では大きな生産性向上とコスト削減効果を生み出します。 さらに、量産安定性が向上します。バランスの取れたランナーは成形条件の許容範囲を広げ、不良率を低減させます。これにより、設備の安定稼働と管理工数の削減が実現します。
これらの効果を最大化するには、金型設計の初期段階で製品仕様とランナー設計の整合性を確保することが極めて重要です。後工程での修正は多大なコストと時間を要します。コストと品質安定を両立させるには、初期投資とランニングコストを見極めた設計アプローチが求められます。
まとめ
コールドランナー金型において、ランナー設計は製品の陰に隠れた「見えない流路」かもしれませんが、その役割は製品品質、コスト、そして量産体制の安定性を根底から支える、極めて重要な設計要素です。単に樹脂を流すだけの通路と考えるのではなく、製品形状や樹脂の特性を深く理解し、流体力学的な観点から最適な形状、サイズ、配置を追求する緻密な設計が求められます。
ショートショットやウェルドライン、材料ロスといった現場の課題の多くは、このランナー設計を見直すことで解決の糸口が見つかります。そして、その最適解は、理論的な設計基準だけでなく、成形現場で培われた経験やノウハウを融合させることによって初めて導き出されます。
CAE解析や流動シミュレーターの活用、現場ノウハウの融合が最適解を導くことが学術的にも示されています。
安定した量産を実現するためには、金型の設計初期段階から、製品設計者と府中プラのような成形メーカーが密に連携し、ゴールを共有することが成功への近道です。無駄のない品質を確保し、真のコスト低減を達成するために、ぜひ一度、金型の「見えない流路」であるランナー設計に目を向けてみてはいかがでしょうか。