エンプラの熱分解メカニズムと対策:焦げ・ガス・臭気を防ぐ材料選定と成形条件の最適化
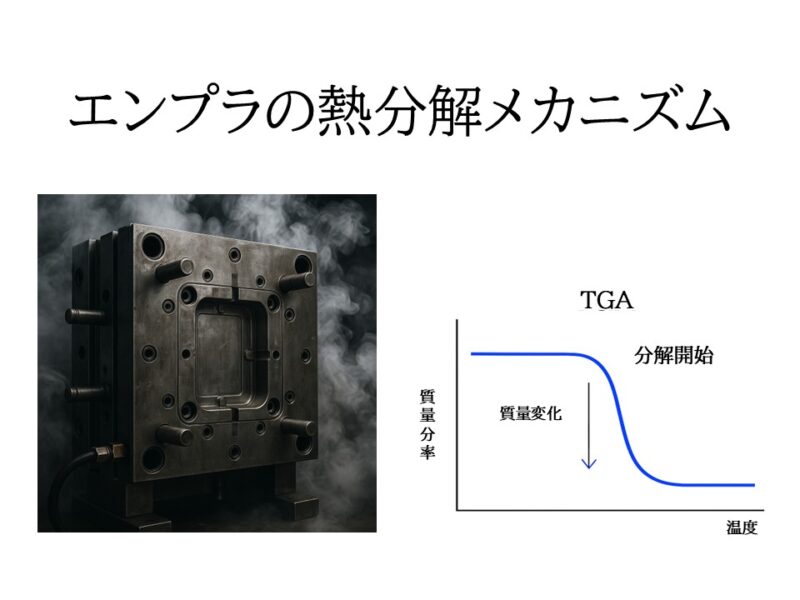
熱分解は、エンプラの成形加工において避けては通れない重大なトラブル要因です。「成形品に黒点(焦げ)が出た」、「ガス焼けがひどい」、「製品が変な臭いがする」といった不具合は、多くの成形現場で発生しています。私が材料メーカーに在籍していたころ、これらのお悩みでご相談いただくケースが後を絶ちませんでした。そして、その原因を深く探っていくと、材料自体の問題ではなく、実は成形機、特にショット重量に対してシリンダーサイズが不適切に大きいことに起因する熱分解が、驚くほど多かったのです。本コラムでは、こうした現場での経験も踏まえ、この厄介な熱分解のメカニズムを解き明かし、材料特性、成形条件、そしてトラブルの根源となりやすい設備選定という多角的な視点から、その予防策と実務的な対応のポイントを詳しく解説していきます。
熱分解とは何か
熱分解と熱劣化の違い
まず、しばしば混同されがちな「熱分解」と「熱劣化」の違いを明確にしておきましょう。これらは似ているようで、現象の深刻度が全く異なります。
「熱劣化」とは、熱エネルギーによってポリマーの物性が徐々に低下していく現象を指します。例えば、長時間の熱履歴によって分子量がわずかに低下したり、酸化が進んで靭性が失われたりしますが、ポリマーとしての基本的な骨格は維持されています。これは、人間で言えば「加齢による体力低下」のような、比較的緩やかな変化です。
一方、「熱分解」は、より過酷な熱が加わることで、ポリマーの主鎖そのものが断裂・崩壊してしまう、より深刻な現象です。分子構造が根本的に破壊されるため、元のポリマーとは異なる低分子量の化合物や、時には有害なガス、刺激臭を伴う物質、炭化物(焦げ)といった副生成物を発生させます。これは、病気によって身体組織が壊死してしまうような、不可逆的で劇的な変化と言えるでしょう。成形加工における「焦げ」や「ガス」は、まさにこの熱分解が引き起こす典型的な症状なのです。
熱分解が引き起こす成形不良
成形プロセス中に熱分解が起こると、製品品質や生産性に甚大な被害をもたらします。代表的な成形不良としては、まず、最も目に見えやすい「黒点・シルバーストリーク・ガス焼け」が挙げられます。分解によって生成された炭化物が成形品に混入し、黒い点となって現れます。また、発生したガスが金型内で断熱圧縮されると、その部分の樹脂が燃焼して「ガス焼け」と呼ばれる焦げ跡が残ります。ガスが製品表面に筋状の模様を作る「シルバーストリーク」の原因にもなります。
次に「寸法ばらつき」です。熱分解によってポリマーの粘度が低下するため、金型への充填挙動が不安定になり、製品の寸法がショットごとにばらつく原因となります。精密部品においては致命的な欠陥です。
さらに「異臭・変色」も深刻な問題です。分解生成物が製品に残留することで、特に自動車内装部品や食品容器、医療機器など、臭気や安全性が厳しく問われる用途ではクレームに直結します。PA(ポリアミド)の黄変なども、分解が関わる代表的な変色事例です。
これらの不良は製品だけの問題に留まりません。発生したガスや分解物は金型や成形機内部を汚染し、メンテナンスの手間を増大させます。特に腐食性ガスを発生する樹脂の場合、高価な金型やスクリューを早期に傷める原因にもなり、作業環境の悪化や作業者の健康被害といったリスクも無視できません。
各種エンプラの熱分解特性
熱分解の起点となる温度とメカニズム
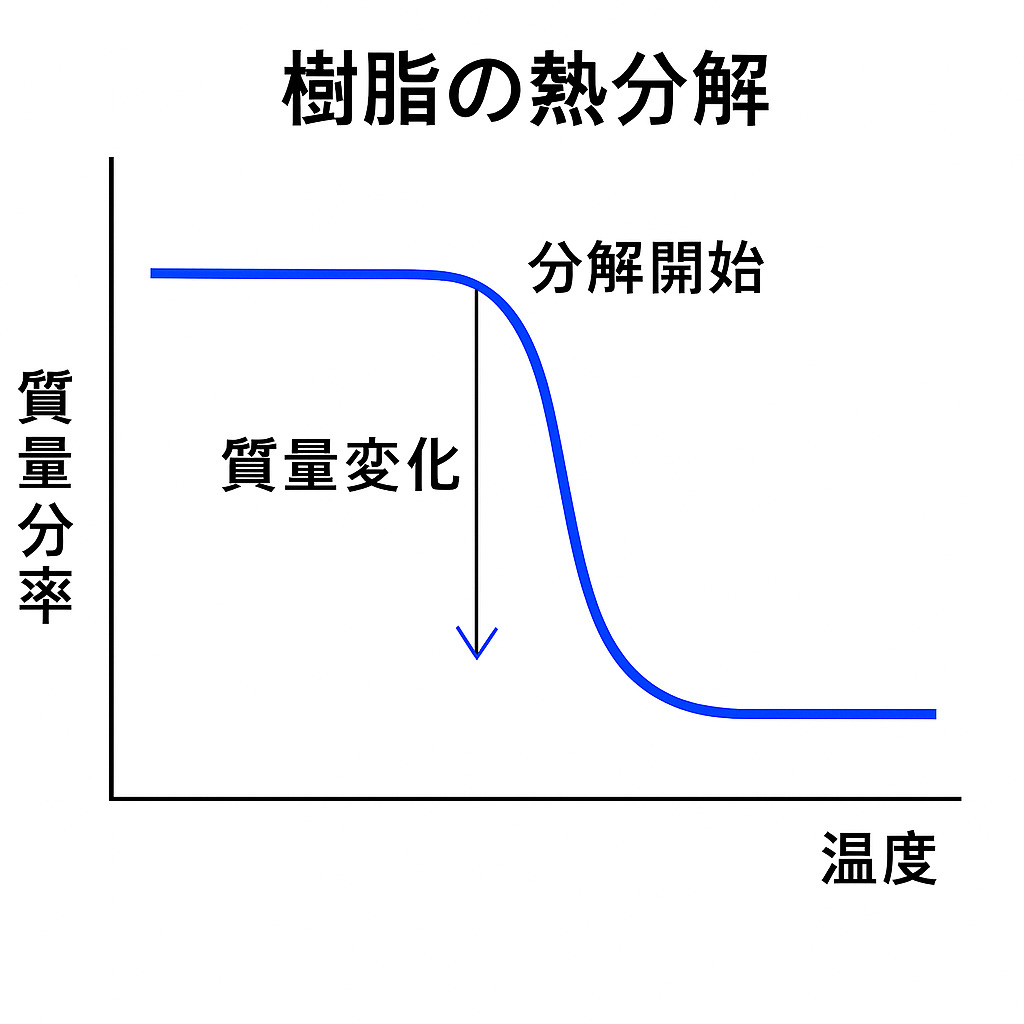
では、どのくらいの温度で熱分解は始まるのでしょうか。この指標となるのが、TGA(Thermogravimetric Analysis:熱重量測定)によって得られる「分解開始温度」です。TGAは、試料を一定の速度で昇温させながら、その重量変化を測定する分析手法です。樹脂が分解してガス化すると重量が減少するため、重量が減少し始める温度を「分解開始温度」と定義します。
しかし、このTGAで得られる値はあくまで一つの目安です。実際の成形プロセスでは、樹脂は単に加熱されるだけでなく、スクリューによるせん断発熱や、酸素・水分・触媒となる不純物の存在など、様々な要因に晒されます。そのため、カタログに記載されている分解開始温度と、実際に設定する成形温度との間には、十分な「安全マージン」を確保することが極めて重要になります。このマージンが小さい樹脂ほど、少しの温度変動や滞留時間の延長で、すぐに熱分解のリスクに直面することになります。
材料別の傾向と注意点
エンプラは種類によって熱分解の挙動が大きく異なります。ここでは代表的な材料の傾向と、府中プラが現場で特に注意している点についてお話しします。
POM(ポリアセタール)は、結晶性が高く、優れた機械特性と摺動性を持つ一方で、熱安定性には特に注意が必要な材料です。その熱分解は、連鎖的な解重合反応によって進行し、刺激臭のあるホルムアルデヒドガスを発生させます。この反応は一度始まると自己触媒的に加速する性質があり、非常に危険です。特にシリンダー内での滞留や過昇温は絶対に避けなければなりません。成形を中断する際は、必ずシリンダー内をパージし、温度をPOMの融点以下まで下げる、あるいはヒーターをオフにするという手順を徹底する必要があります。
PA(ポリアミド)は、強靭で耐薬品性に優れますが、そのアミド結合は高温の酸素存在下で酸化分解を起こしやすく、特に「黄変」という形で現れやすいのが特徴です。乾燥が不十分な場合、加水分解も起こり物性低下を招きます。長時間高温に晒されると、黄変だけでなく、粘度低下によるバリや寸法変化を引き起こすことがあります。
PC(ポリカーボネート)は、透明性、耐衝撃性に優れ、広く使われるエンプラですが、熱安定性は中程度です。高温下での滞留は分子量低下と黄変を招きます。PCの分解で特に注意すべきは、水分の存在です。高温で水分が存在すると容易に加水分解を起こし、著しく物性が低下します。成形前の予備乾燥は絶対条件です。
PEEK、PES、PEI、PPSといったスーパーエンプラは、極めて高い耐熱性を誇ります。分解開始温度も400℃を超えるものが多く、通常の成形温度域では非常に安定しています。しかし油断は禁物で、万が一推奨温度を大幅に超えると、硬い炭化物を生成します。この炭化物はスクリューやシリンダーに固着しやすく、除去が非常に困難です。
最後に、添加剤の影響も忘れてはなりません。例えば、難燃剤や滑剤は、樹脂本体よりも低い温度で分解を始めることがあります。これが引き金となって樹脂全体の分解を促進したり、腐食性ガスを発生させたりするケースは少なくありません。材料選定の際は、ベース樹脂だけでなく、添加されている成分の熱安定性まで確認することが重要です。
成形条件と設備が熱分解を引き起こす場合
熱分解は材料固有の問題だけでなく、成形プロセスそのものに起因して発生することが非常に多いのです。むしろ、現場で遭遇するトラブルの多くは、運用上の問題が根本原因となっています。
シリンダー内での滞留がもたらすリスク
樹脂の分解は「温度」と「時間」の掛け算で進行します。つまり、たとえ設定温度が推奨範囲内であっても、樹脂がシリンダー内に滞留する時間が長引けば、分解は着実に進んでいきます。金型のトラブルで一時的に成形を中断した際、ヒーターを入れたまま放置してしまうのは最悪のケースです。熱分解は、過昇温という「イベント」だけでなく、滞留という「プロセス」によっても引き起こされることを肝に銘じるべきです。
過大なシリンダーサイズによる典型トラブル
これは、私が多くの成形工場で目にしてきた、熱分解トラブルの典型的な原因の一つです。それは「小さな成形品を、不必要に大きな成形機で生産している」ケースです。
以前、私が、あるお客様から受けた相談で印象的だったのが「m-PPE製の電子部品で、どうしてもガス焼けが解消しない」というものでした。金型のガスベントを追加工するなど、様々な対策を試みても、製品の末端部には必ず茶色い焦げ跡が発生してしまうとのことでした。工場に伺ってまず確認したのは、使用している成形機と金型です。問題の部品は小物でしたが、使われていたのはこの部品に不釣り合いに大型の成形機でした。その結果、1ショットで射出される樹脂量が、成形機の最大射出容量に対して極端に少ない状態であることが分かりました。
これが何を意味するか。シリンダー内に充填された樹脂のうち、1回のショットで使われるのはごく一部で、残りの大部分はシリンダー内に残り、次のショット、さらにその次のショットまで加熱され続けることになります。つまり、樹脂のシリンダー内平均滞留時間が極端に長くなっていたのです。これこそが、慢性的なガス焼けの根本原因でした。m-PPE、特に難燃グレードは滞留によって添加剤などが分解しやすく、多量のガスを発生させることがあります。このシリンダー内で発生した過剰な分解ガスが、金型の排気能力(ガスベント)を超えてしまい、金型内で断熱圧縮されて燃焼、ガス焼けを引き起こしていたのです。
一般的に、安定した成形を行うための適正なショット率(ショット重量 ÷ シリンダー容量 × 100)は、30%~80%が目安とされています。これを大きく下回る場合、どんなに成形条件を工夫しても、滞留による熱分解を根本的に解決することは困難です。設備選定のミスは、後から条件調整でカバーできる範囲を超えた、プロセスの根幹に関わる問題なのです。
熱分解を防ぐ設計・選定・運用のポイント
これまで述べてきたメカニズムと原因を踏まえ、熱分解を未然に防ぐための具体的なポイントを「材料選定」、「成形条件」、「設備管理」の3つの観点から整理します。
なお、射出成形時の熱分解ガス発生メカニズムやガス焼け対策については、ポリプラスチックス社の技術コラムでも詳細に解説されています。現場でのトラブル事例や具体的な対策例を知りたい方は、同コラムも参考にしてください。
材料選定時の注意点
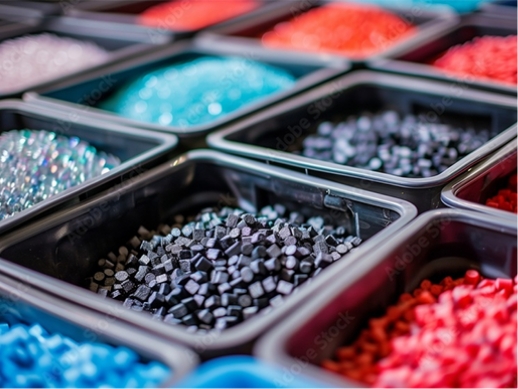
まず、製品の使用温度に対し、材料の分解温度との「安全マージン」が十分にあるグレードを選定することが基本です。耐熱性がギリギリの選定はプロセス変動に弱く、不良の温床となります。また、自動車内装や医療・食品用途では、分解によって生じるガスや臭気にも配慮が必要です。用途に応じたグレードを選びましょう。
成形条件の最適化
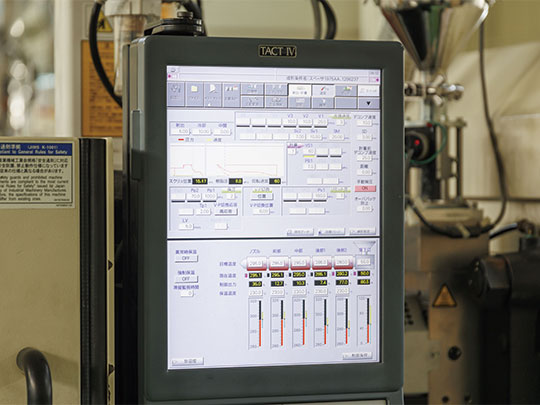
シリンダー温度は推奨範囲のできるだけ低い側で設定し、成形停止時はヒーターをオフにするか温度を下げるルールを徹底してください。また、過剰なスクリュー回転数や背圧は、剪断発熱による分解を招きます。品質を損なわない範囲で、これらは可能な限り低く設定するのが熱分解対策の鉄則です。
成形機の適正選定と管理
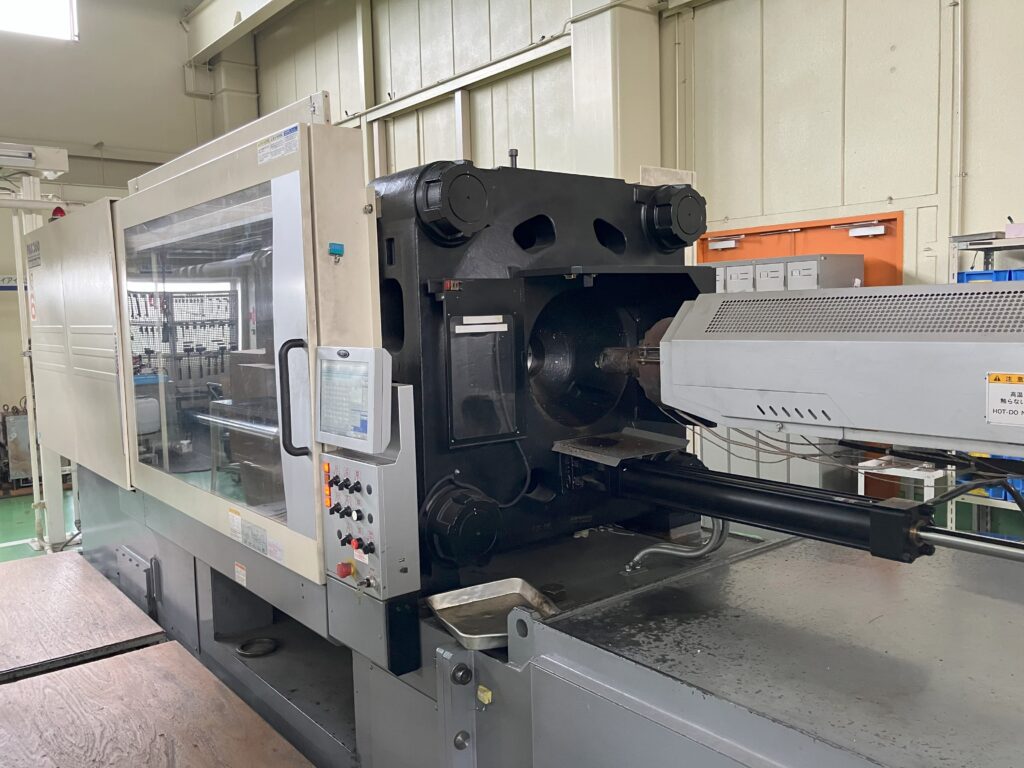
ショット重量に対しシリンダー容量が過大な成形機は、樹脂の滞留を招き、分解の温床となります。ショット率(ショット重量÷シリンダー容量)が30~80%の範囲に収まる成形機選定を強く推奨します。また、材料を切り替える際の念入りなパージ洗浄や、炭化物を除去するための定期的なスクリュー清掃は、安定した品質を維持するための必須作業です。
まとめ
エンプラの熱分解は、「見えにくい劣化現象」ですが、成形不良や製品信頼性低下の大きな要因となります。この問題に対処するには、材料特性の理解だけでなく、成形条件、そして成形機や金型といった設備仕様の視点から、総合的に管理していくことが不可欠です。設備の選定や運用方法を今一度見直すことこそが、優れたエンプラの性能を最大限に引き出し、高品質なものづくりを実現するための第一歩なのです。
参考文献
射出成形時のガス発生メカニズムを解明する新評価法(ポリプラスチックス社 技術コラム)