「残留応力」が割れ(クラック)・反り・寸法不良を呼ぶ!射出成形に潜む“見えないひずみ”と品質トラブル対策
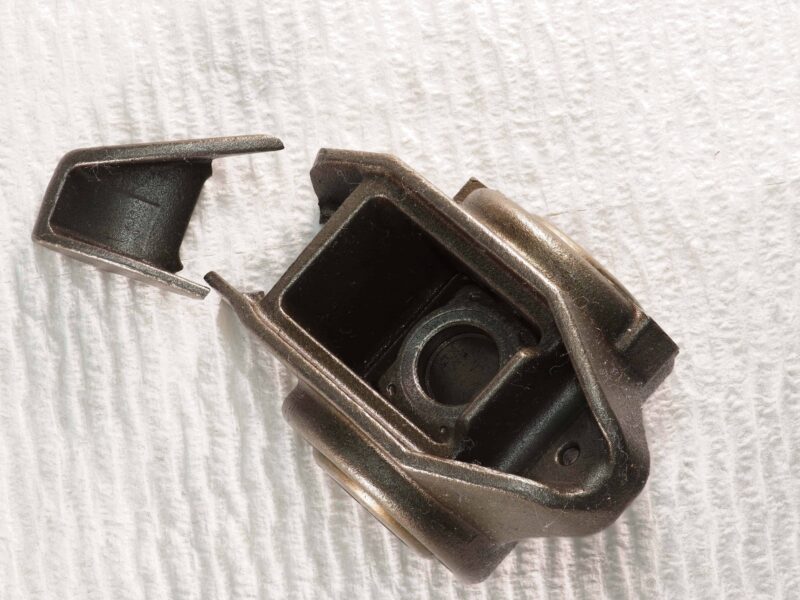
射出成形品における「割れ(クラック)」や「反り」、「寸法不良」。その多くは目に見える成形条件や金型設計に原因があると考えられがちですが、実は製品内部に潜む「残留応力」が根本的な要因となっているケースが少なくありません。残留応力は、外からは見えない“内部ひずみ”であり、製品の強度や寸法安定性に大きな影響を及ぼします。なぜ、きちんと成形したはずの製品が後から割れたり、変形したりするのでしょうか。本コラムでは、府中プラが射出成形における残留応力の正体と、具体的な品質トラブルとの関係、そして設計・成形現場での対策をわかりやすく整理します。
残留応力とは ― 射出成形品内部に潜む“見えない危険”
一見すると何の問題もなさそうな成形品も、その内部には見えない力が潜んでいることがあります。それが「残留応力」です。この力が、後のトラブルの引き金となります。
残留応力とは、成形品に外部から力がかかっていない状態でも、その内部に残り続けている応力(ひずみ)のことを指します。まるで、内部で引っ張り合ったり、押し合ったりする力が常に働いているような状態です。この“見えない力”は、成形プロセスにおける様々な要因が複雑に絡み合って発生します。
主な発生要因は三つあります。
第一に「不均一な冷却による収縮差」です。溶融樹脂が金型内で冷え固まる際、製品の表面は金型に接しているため早く冷えますが、内部はゆっくりと冷えます。この冷却速度の違いにより、収縮するタイミングや度合いにズレが生じます。先に固まった外層が、後から収縮しようとする内層を引っ張ることで、製品内部にアンバランスな力が生まれるのです。
第二に「金型内での圧力分布の偏り」です。樹脂を金型に充填し、固化するまで圧力をかける保圧工程において、ゲートに近い部分は高い圧力がかかり、遠い部分は圧力が低くなります。この圧力のムラが、そのまま固化後の製品内部に応力として残ってしまいます。
第三に「樹脂の分子配向による内部ひずみ」です。溶融状態の樹脂は、鎖状の分子(ポリマー)がランダムに絡み合っています。しかし、これがゲートなどの狭い流路を通過したり、金型内を流れたりする際に、分子が流れの方向に引き伸ばされて整列します。これを「分子配向」と呼びます。この引き伸ばされた分子は元の安定した状態に戻ろうとするため、その力が内部ひずみとして残留するのです。
残留応力の現れ方は、使用する樹脂の種類によっても異なります。樹脂は大きく「結晶性樹脂」と「非結晶性樹脂」に分けられますが、それぞれで注意すべき点が異なります。
結晶性樹脂(例:PA、POM、PP)は、固化する際に分子が規則正しく並んだ「結晶部分」を形成します。この結晶化に伴い、体積が大きく収縮するのが特徴です。そのため、製品内の冷却ムラによる収縮差が大きくなりやすく、これが主に「反り」や「ねじれ」といった寸法不良として現れます。
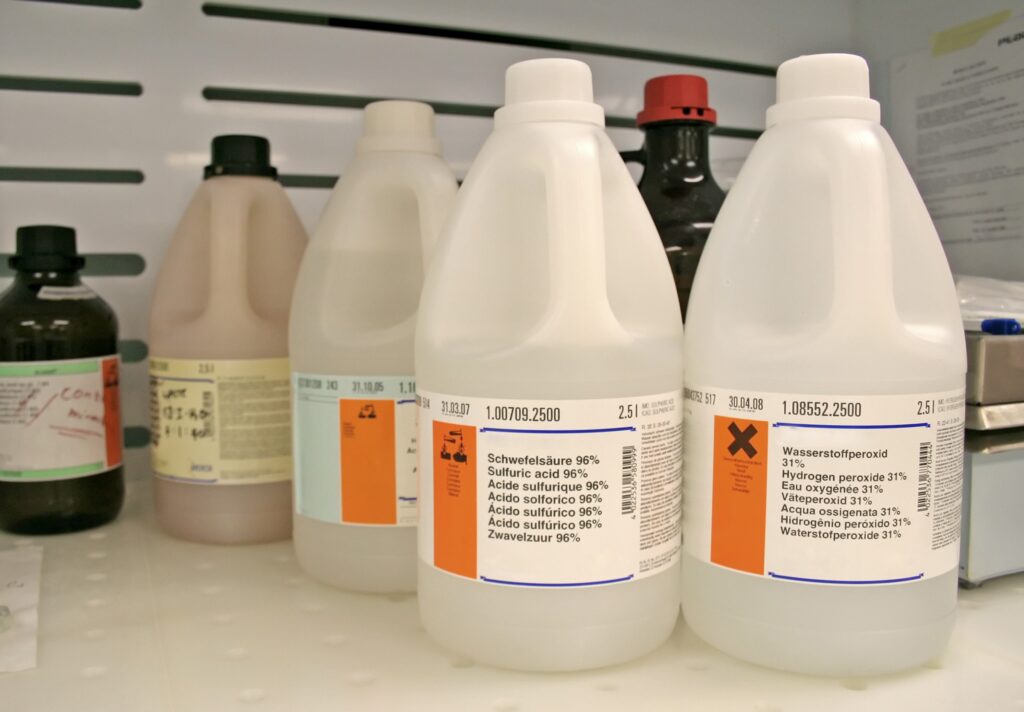
一方、非結晶性樹脂(例:PC、PMMA、ABS)は、固化しても分子がランダムなままで、明確な結晶構造を持ちません。収縮率は結晶性樹脂ほど大きくありませんが、分子配向の影響を強く受けやすい傾向があります。引き伸ばされた分子が元に戻ろうとする力が強く残留するため、応力集中箇所から「割れ(クラック)」が発生しやすくなります。特に、薬品や溶剤に触れることで割れが促進される「環境応力割れ(ソルベントクラック)」は、非結晶性樹脂で顕著に見られる現象です。
残留応力が引き起こす代表的な成形不良
製品内部に蓄積された残留応力は、すぐには問題として現れないこともありますが、時間の経過や外部環境の変化をきっかけに、様々な品質不良を引き起こします。
成形直後は問題なかった製品が、輸送中や保管中、あるいは顧客の手元に渡ってから突然割れてしまう現象。この最大の原因が残留応力です。製品内部に高いひずみが蓄積された状態は、言わば“割れの待機状態”です。そこに、組み立て時の締め付け力、わずかな衝撃、急激な温度変化といった外部からの力が加わると、蓄えられていた応力が限界を超え、一気にクラックとして解放されます。特に、鋭い角(シャープエッジ)やインサート金具の周辺は応力が集中しやすいため、割れの起点となりがちです。残留応力が大きい製品ほど、わずかなきっかけで破損に至るリスクが高まります。
平板状の製品が意図せず弓なりに曲がってしまう「反り」や、製品全体がねじれる「変形」も、残留応力が引き起こす典型的な不良です。これは主に、製品の表裏や部分的な冷却速度の違い、あるいは分子配向の偏りによって、収縮のバランスが崩れることで発生します。例えば、製品の片面だけを急激に冷やすと、その面は大きく収縮しようとしますが、もう片面はゆっくり収縮するため、収縮の大きい側に製品が引っ張られて反ってしまいます。また、リブやボスのような付属構造がある場合、その周辺は肉厚が不均一になりやすく、冷却と収縮のアンバランスから局所的な変形が起こりやすくなります。
残留応力は、製品の寸法安定性にも深刻な影響を及ぼします。成形直後は規定の寸法を満たしていても、内部に残った応力が時間とともにゆっくりと解放される過程で、製品がわずかに収縮したり変形したりすることがあります。これを「経時変化」と呼びます。この現象は、特に精密な寸法精度が求められる嵌合部品や機構部品において致命的な問題となります。組み立てた後で勘合が緩くなったり、きつくなったりする不具合は、この経時変化が原因であるケースが少なくありません。残留応力を管理することは、長期的な品質保証の観点からも極めて重要です。
残留応力を低減するための設計・成形の考え方
やっかいな残留応力ですが、発生を完全にゼロにすることは困難です。しかし、設計や成形の工夫によって、その大きさを許容範囲内にコントロールすることは可能です。
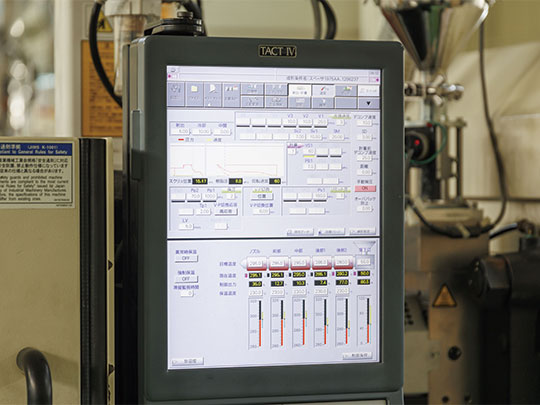
残留応力対策の基本にして最も重要なのが、金型での冷却管理です。特に金型温度の設定は決定的な役割を果たします。金型温度が低すぎると、溶融樹脂は金型に触れた瞬間に急冷され、表面だけが固化してしまいます。その内部では、まだ高温の樹脂がゆっくりと冷えながら収縮しようとするため、表面と内部の間に大きな収縮差が生まれ、高い残留応力が発生します。これを防ぐためには、樹脂の種類に応じた適切な金型温度に設定し、製品全体をなるべく均一に、そして穏やかに冷却することが基本です。金型内の冷却回路を適切に配置し、製品のどこか一部分だけが極端に冷えたり、熱がこもったりしないよう、冷却バランスを最適化することが求められます。
射出・保圧工程の条件設定も、残留応力の大きさに直結します。特に射出圧力や保圧が過剰だと、樹脂を金型キャビティ内に無理やり詰め込むことになり、分子が過度に圧縮された状態で固化するため、高い内部応力が残ります。製品のヒケを防ぐために保圧を高く設定しがちですが、必要以上の圧力は残留応力を増大させるだけです。ショートショットやヒケが発生しない範囲で、できるだけ低い圧力に設定することが理想です。また、射出速度が不適切だと、樹脂の分子配向が偏り、局所的な応力集中を招きます。安定した充填を保ちつつ、過度なせん断や配向を引き起こさない速度を見極めることが重要です。
成形条件だけでなく、製品そのものの設計段階での配慮も欠かせません。残留応力を低減する設計の基本は「均一肉厚」です。製品内に厚い部分と薄い部分が混在していると、厚い部分は冷えにくく、収縮量も大きくなるため、その境界に応力が集中し、反りや割れの原因となります。製品の機能上どうしても肉厚を変える必要がある場合は、その変化をできるだけ緩やかに(テーパーを設けるなど)することが有効です。また、補強のために設けられるリブやボスの形状にも工夫が必要です。リブの根元などが鋭角になっていると応力集中点になるため、滑らかなR(丸み)を付けて応力を分散させることが、割れを防ぐ上で非常に効果的な対策となります。
実務現場でのトラブル対策ポイント
実際の生産現場で残留応力に起因する不良が発生した場合、どのように対策を進めればよいでしょうか。不良現象に応じたアプローチのポイントを整理します。
製品に「割れ(クラック)」が頻発する場合、まずは急冷による応力蓄積を疑います。対策の第一歩は、金型温度の見直しです。現在の設定温度が低すぎないかを確認し、段階的に温度を上げて、より穏やかな冷却を目指します。同時に、金型の冷却水量を調整するなどして、冷却バランスを改善することも有効です。
「反り」や「歪み」が目立つ場合は、収縮のアンバランスが主な原因と考えられます。この対策としては、射出圧力や保圧の最適化が効果的です。過剰な圧力がかかっていないかを確認し、必要最低限まで下げることで、内部応力を緩和します。また、射出速度を調整して分子配向の偏りを是正したり、金型構造そのもの(ゲート位置や冷却回路)に問題がないかを再確認したりすることも重要です。
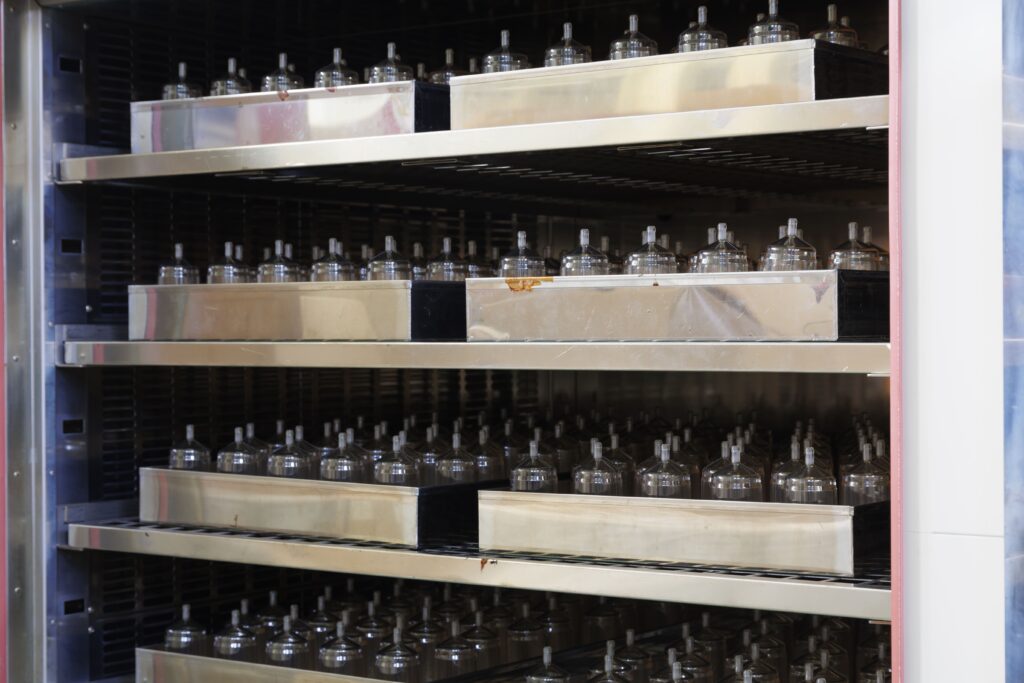
「寸法不良」や「経時変化」が問題となる高精度品では、上記のような成形・設計対策を尽くしてもなお残留応力が問題になることがあります。その場合の最終手段として、成形後に製品を加熱して応力を緩和させる「アニール」という後処理を検討する価値があります。これは追加コストと手間がかかりますが、極めて高い寸法安定性が求められる製品においては有効な選択肢となります。
まとめ
残留応力は、目に見えずとも射出成形品の品質を大きく左右する“隠れたリスク”です。特に、原因不明とされがちな割れ・反り・寸法不良といったトラブルの裏側には、しばしばこの内部ひずみが潜んでいます。私たち府中プラは、この見えないリスクをコントロールすることの重要性を深く認識しています。設計段階からの均一肉厚化や応力集中を避ける形状配慮、そして成形現場における金型温度や圧力、冷却管理の適正化が、残留応力の低減と安定した品質の製品を生み出すためのカギとなります。現在調達されている成形部品の品質でお困りの際は、ぜひ府中プラまでお気軽にご相談ください。