射出圧力が製品品質を決める!ショートショット・バリ・寸法不良を防ぐ“見えない圧力設計”の実務ポイント
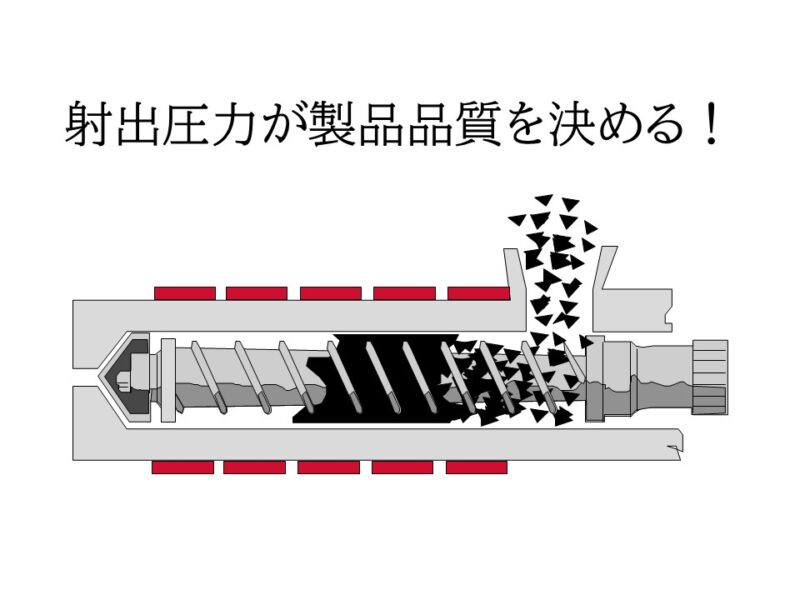
射出成形において「射出圧力」は、材料を金型に充填するための“駆動力”であり、製品の外観・寸法・強度に密接に関わる基本パラメータです。しかし、府中プラが現場でよく耳にするのは、「圧力が高いほど充填しやすい」、「低いほどバリが出にくい」といった表面的な理解です。もちろんそれは間違いではありませんが、圧力の本質を捉えているとは言えません。なぜその圧力が必要で、過不足がどのようなトラブルを招くのか。本コラムでは、射出圧力が成形不良とどのように関連し、どのように最適化すべきかを、設計と成形実務の両面からわかりやすく解説します。
射出圧力とは ― 成形プロセスを支える駆動力
成形条件を語る上で欠かせない「圧力」。まずはその定義と、混同されがちな他のパラメータとの違いを正確に理解することから始めましょう。
射出圧力とは、成形機のスクリューが前進して溶融樹脂を金型キャビティ内へ押し込む際に必要となる「力」のことを指します。一般的には「MPa(メガパスカル)」という単位で管理され、成形機のモニターに表示されるこの数値は、樹脂にどれだけの力をかけているかを示す指標です。この力があるからこそ、樹脂は細いランナーやゲートを通り抜け、複雑な形状のキャビティの隅々まで行き渡ることができます。具体的には、射出工程(スクリューが前進して樹脂を充填する工程)において、設定された射出速度を維持するためにかけられる圧力の上限値を指すことが多く、成形プロセスにおける最も初期の駆動力を担っています。
現場では「射出圧力」、「保圧」、「射出速度」という言葉が飛び交いますが、これらの役割は明確に異なります。
射出速度は、樹脂を金型へ「どれくらいの速さで」送り込むかというスピードの目標値です。一方、射出圧力は、その目標速度を達成するために「どれくらいの力まで」許容するかという上限設定、つまりパワーの源です。車で例えるなら、射出速度が「時速100kmで走りたい」という目標だとすれば、射出圧力はそれを実現するためのエンジンの力(トルク)に相当します。いくらアクセルを強く踏んでも、上り坂(流動抵抗)が険しければ、十分なエンジンパワーがなければ目標速度は出せません。射出成形も同様で、設定した射出速度を出すために必要な力が、設定した射出圧力の上限を超えてしまうと、実際の速度は低下してしまいます。
そして、保圧は、樹脂の充填が完了した後に、ヒケ(冷却収縮による窪み)を防ぐ目的でかけ続ける圧力のことです。充填を担う射出圧力とは、その目的とタイミングが根本的に異なります。射出圧力で製品の形を大まかに作り、保圧で寸法や外観を精密に仕上げる、という役割分担のイメージです。これら三者は別々のパラメータですが、互いに深く影響し合っており、一つだけを調整しても品質は安定しません。
射出圧力が引き起こす成形不良とその原因
射出圧力の過不足は、様々な成形不良の直接的な原因となります。ここでは代表的な不良と、圧力との因果関係を解き明かしていきます。
ショートショット
「ショートショット」は、溶融樹脂が金型キャビティの末端まで行き渡らず、製品形状が不完全になる充填不良です。この最も基本的な原因が、射出圧力の不足です。金型内部の流路は、樹脂にとって抵抗の連続です。特に、ランナーが長い、製品の肉厚が薄い、ゲートが微細であるといった場合、樹脂が先に進むためには大きな力(圧力)が必要になります。設定された射出圧力がこの流動抵抗に負けてしまうと、樹脂は途中で勢いを失い、冷えて固まってしまい、結果としてショートショットが発生します。リブやボスの先端など、金型内で最も遠く、最も流れにくい部分で発生しやすいのが特徴です。
バリ
「バリ」は、金型のパーティングライン(分割面)やエジェクタピンの隙間から樹脂がはみ出してしまう外観不良です。これは、射出圧力が過剰であることの典型的なサインです。射出成形機は、バリを防ぐために「型締め力」という強大な力で金型を閉じています。しかし、射出圧力がこの型締め力を上回ってしまうと、金型のパーティング面をわずかにこじ開け、その隙間に樹脂が侵入してバリとなるのです。言わば、圧力と型締め力の「綱引き」で圧力が勝ってしまった状態です。特に、製品の投影面積(金型が開く方向に見た面積)が大きい場合、樹脂が金型を押し開こうとする力も大きくなるため、より高い型締め力が必要となり、圧力と型締め力のバランスはさらにシビアになります。
アンダー、オーバー
製品の寸法が設計値よりも小さくなる「アンダー」、または大きくなる「オーバー」といった寸法不良も、射出圧力と深く関わっています。これは、圧力が金型内の樹脂の「充填密度」を左右するためです。射出圧力が不足していると、キャビティ内に詰め込まれる樹脂の密度が低くなります。その結果、冷却・固化する際の体積収縮が大きくなり、製品寸法は設計値よりも小さくなりがちです(寸法アンダー)。逆に、射出圧力が過剰だと、樹脂がキャビティ内に無理やり詰め込まれる「過充填」状態になります。充填密度が高いため、冷却収縮が抑制され、製品寸法は設計値よりも大きくなる傾向があります(寸法オーバー)。精密な寸法が求められる部品において、圧力管理は品質を維持するための生命線と言えます。
反り(ソリ)、変形
製品の反りや変形は、前回のコラムで解説した「残留応力」が主な原因ですが、その残留応力を生み出す引き金の一つが、金型内部における圧力分布の偏りです。樹脂がゲートから注入され、キャビティ内を満たしていく過程で、ゲートに近い部分は高い圧力がかかり、ゲートから遠い末端部は圧力が低下します。この圧力のムラが、そのまま製品内部の密度ムラや収縮ムラにつながり、冷却後に製品を反らせたり歪ませたりする力として作用します。特に、局所的に過剰な圧力がかかると、その部分だけが過充填となって周囲との収縮バランスが崩れ、大きな変形を引き起こす原因となります。
射出圧力の適正化に向けた考え方
では、これらの不良を防ぎ、適切な品質を確保するために、射出圧力をどのように考え、設定していけばよいのでしょうか。
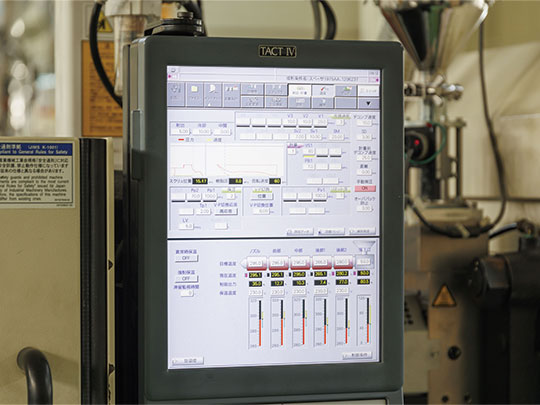
最適な射出圧力を設定するための第一歩は、成形しようとする製品と金型の「流動抵抗」を正しく把握することです。ゲートの径はどれくらいか、ランナーは長く複雑か、製品の肉厚は薄いか厚いか。これらの金型構造によって、樹脂が流れる際の抵抗は大きく変化し、それに伴って必要となる射出圧力も変わります。例えば、細いゲートや薄肉形状の製品では、高い流動抵抗に打ち勝つために比較的高めの圧力が必要になります。逆に、厚肉で面積の大きい製品では、低い抵抗で充填できるため、不必要に高い圧力をかけるとバリや過充填のリスクが高まります。
府中プラでは、CAEによる流動解析などを活用し、設計段階で必要な圧力を予測することで、成形現場でのトラブルを未然に防ぐアプローチを重視しています。
前述の通り、射出圧力と射出速度は密接に連動します。高い速度で充填しようとすれば、必然的に高い圧力が必要になります。しかし、「高速×高圧」の組み合わせは、せん断発熱を増大させ、樹脂のヤケやガス焼け、バリといった別の不良を誘発する諸刃の剣です。そこで有効なのが、多段速度制御を活用した圧力制御です。充填初期は低速(=低圧)でジェッティングを防ぎ、中盤は高速(=高圧)で一気に充填してショートショットを防ぎ、終盤は再び低速(=低圧)にしてガス抜けを促しバリを抑制する。このように射出速度にメリハリをつけることで、圧力の急激な変動を抑え、プロセス全体を安定させることができます。これは、単に圧力を上げ下げするよりもはるかに高度で効果的な圧力マネジメントです。
射出成形における品質トラブルは、射出圧力という一つのパラメータだけで解決できるものではありません。常に他の条件とのバランス、すなわち「全体最適」の視点が必要です。例えば、ショートショット気味だからといって射出圧力を上げる前に、金型温度を上げることを検討します。金型温度を上げれば樹脂の流動性が向上し、より低い圧力で充填できるようになるからです。圧力で無理やり押し込むのではなく、樹脂が流れやすい環境を整えてあげるという発想です。また、寸法不良に対しては、射出圧力だけでなく、充填後の保圧の設定がより直接的に影響します。射出圧力はあくまで充填のための駆動力と捉え、最終的な寸法調整は保圧に委ねる、という役割分担を意識することが、安定した成形条件を見つけ出すための鍵となります。
実務での射出圧力調整ポイント
最後に、生産現場で不良が発生した際の、射出圧力に関する調整のヒントをまとめます。
ショートショット発生時には、まず射出速度を段階的に上げることを試みます。速度を上げることで充填末端への勢いを増すためです。それでも改善しない場合に、射出圧力の上限設定を少しずつ上げて、必要なパワーを供給できるようにします。
バリ発生時には、第一に射出圧力の設定を下げることが基本です。特に、保圧に切り替わる直前の圧力が高い場合は、そこをピンポイントで下げるのが有効です。それでも収まらなければ、型締め力が不足していないか、あるいは金型の合わせ面に摩耗や異物がないかを再確認する必要があります。
寸法不良(アンダー・オーバー)に対しては、射出圧力よりも保圧の調整が主となります。寸法アンダーなら保圧を上げ、オーバーなら保圧を下げるのがセオリーです。ただし、射出圧力も充填密度に影響するため、微調整の要素として考慮します。冷却時間も収縮に大きく関わるため、圧力・保圧・時間の三点セットで調整します。
反り・歪み発生時は、圧力の偏りを緩和することが目標です。多段射出制御を導入して充填パターンを変化させたり、金型温度のバランスを調整して均一な冷却を目指したりすることで、圧力分布の均一化を図ります。
まとめ
射出圧力は、単なる成形条件の一項目ではなく、金型内で起こる全ての物理現象の源となる、射出成形における「見えない力の設計」そのものです。その圧力の過不足が、ショートショット、バリ、寸法不良、反りといった目に見える品質トラブルの直接的な原因となります。だからこそ、金型設計の段階から圧力を予測し、成形現場では射出速度、保圧、金型温度と連動させた「全体最適」の視点で適正化を図ることが不可欠です。一つの条件だけを追いかけるのではなく、プロセス全体を見渡すことが、安定した成形条件を確立する唯一の近道だと、府中プラは考えています。こうした現場課題の解決に向けた実践的な成形条件の最適化もご支援しております。
現在調達されている成形部品の品質でお困りの際は、ぜひ府中プラまでお気軽にご相談ください。