クリープ現象による破損を防ぐには? エンプラ設計で見落とされがちな時間依存変形の考え方
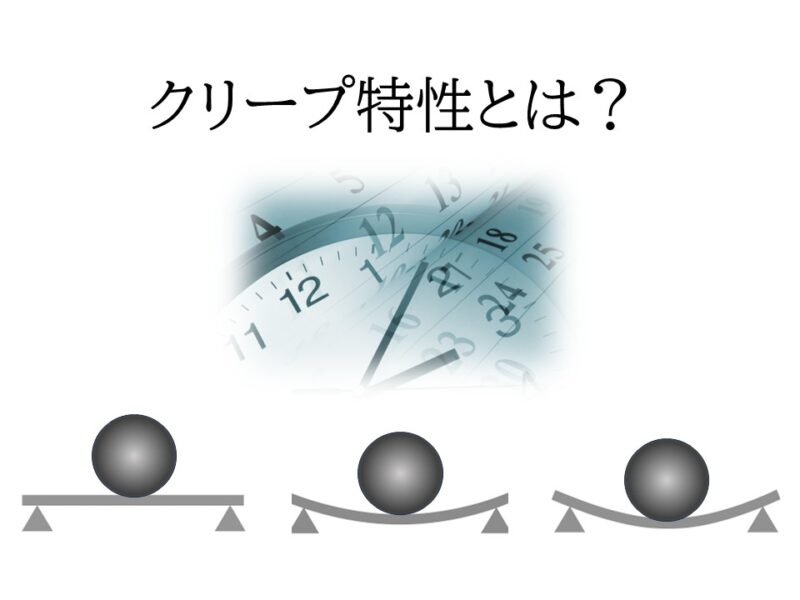
エンプラは、その軽量性、優れた成形加工性、そして高い力学特性から、電子機器、産業機械、自動車など多岐にわたる分野で金属の代替や複雑形状部品の実現に貢献しています。しかし、その設計において、引張強度や曲げ弾性率といったカタログに大きく記載された「短期的な力学特性」のみに注目してしまうと、思わぬ落とし穴にはまることがあります。それが、「時間依存変形」、すなわちクリープと呼ばれる現象です。
クリープとは、材料に一定の荷重(応力)がかかり続けることで、時間の経過と共にじわじわと変形が進行する現象を指します。たとえ弾性限度以下の低い応力であっても、この変形は進行し、不可逆的なものとなります。特にエンプラは、その特性が温度や湿度に大きく影響されるため、高温環境下や高湿条件下ではクリープが著しく加速され、想定外の寸法変化や機能不全を引き起こすことがあります。
「しっかり締めたはずのネジが、いつの間にか緩んでいる」
「ぴったりだった嵌合部品が、使用しているうちにガタついてきた」
これらのトラブルの多くは、クリープ現象が根本原因です。本コラムでは、エンプラ部品の設計者が見落としがちな「クリープ特性」に焦点を当て、その基本的なメカニズムから、信頼性を確保するための材料選定、そして具体的な設計対策まで体系的に解説します。
クリープとは何か?―時間と共に変形するプラスチックの宿命
金属材料にもクリープは存在しますが、それは融点に近い高温域で顕著になる現象です。一方、エンプラのような高分子材料は、常温域でもクリープが問題となる点が大きな特徴です。これは、プラスチックが持つ「粘弾性」という性質に起因します。
粘弾性モデルで理解するクリープ
プラスチックの挙動は、完全な弾性体(力を加えると瞬時に変形し、除くと瞬時に戻る「バネ」)でも、完全な粘性体(力を加えると時間をかけて変形し、除いても戻らない「ダッシュポット」)でもありません。この両方の性質を併せ持つのが粘弾性体です。
弾性変形:応力を加えた瞬間に生じる変形。分子鎖の結合角や結合長がわずかに変化することによるもので、可逆的です。
粘性流動(クリープ変形):時間をかけて進行する変形。凍結されていた分子鎖のセグメントが動き出し、分子鎖全体がゆっくりと滑るように再配列(コンフォメーション変化)することで生じます。この変形はエネルギーを熱として散逸しながら進むため、荷重を取り除いても完全には元に戻りません(永久ひずみ)。
クリープ変形の3つのステージ
クリープによるひずみ(変形量)の時間変化をグラフにすると、一般的に以下の3つの領域に分けられます。これは製品の寿命予測において極めて重要な概念です。
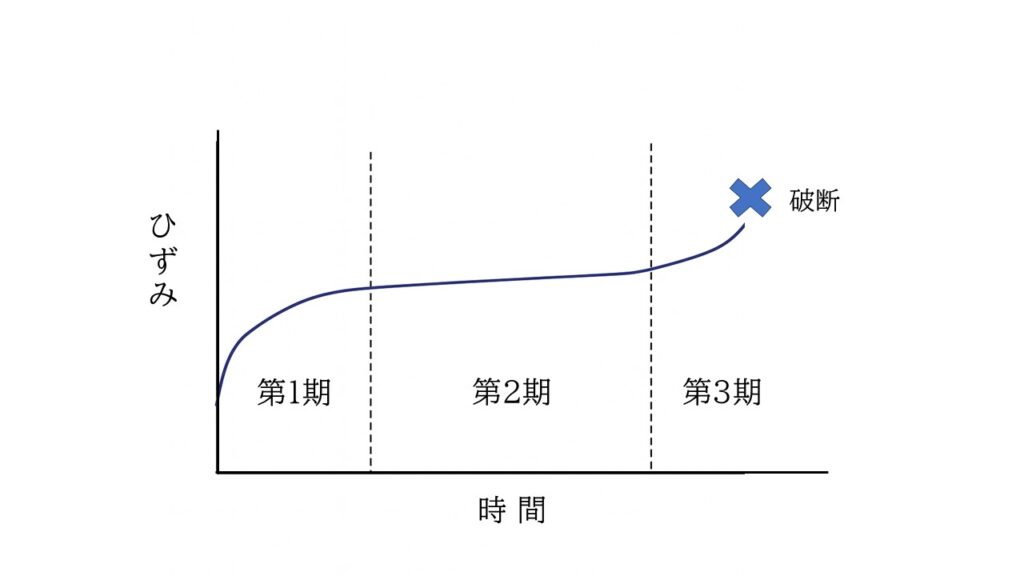
第1期(遷移クリープ):応力を負荷した直後。変形速度は時間と共に減少し、比較的安定した状態に向かいます。分子鎖のほぐれと再配列が活発に起こる段階です。
第2期(定常クリープ):変形速度がほぼ一定となる領域。分子鎖の変形と、内部ひずみによる硬化が釣り合った状態です。多くの製品はこの領域内で使用されることを前提に設計されます。
第3期(加速クリープ):変形速度が急激に増大し、最終的に破断に至る領域。材料内部に微小な亀裂(マイクロクラック)や空隙(ボイド)が発生・成長し、有効断面積が減少することで応力が増大し、破壊が加速します。
設計においては、製品寿命がこの第3期クリープ領域に突入しないよう、応力レベルや使用環境を管理することが絶対条件となります。
設計トラブルの陰にクリープあり―具体的な不具合事例とメカニズム
実務においてクリープを軽視すると、どのような問題が発生するのでしょうか。代表的な3つの事例と、その背後にあるメカニズムを解説します。
締結部の応力低下(応力緩和)
ねじやボルトで締結された樹脂部品では、初期の締付力によって部品に圧縮ひずみが生じます。この「ひずみが一定に保たれた状態」で発生するのが応力緩和です。応力緩和はクリープと表裏一体の現象で、材料がクリープ変形しようとすることで、内部の応力が時間と共に低下していきます。
学術的には、「一定ひずみ下において、そのひずみを維持するのに必要な応力が時間とともに減少する現象」と定義されます。例えば、日本機械学会の研究報告などでは、特定の条件下でエンプラ製ボルトの軸力が1000時間後には初期値の40~60%にまで低下するケースが示されています。[1]
この結果、締結力が不足し、液漏れや部品の緩み、振動による異音などを引き起こします。対策として、接地面積の大きいフランジ形状の採用や、クリープしにくい金属製のカラー・ワッシャーを併用することが有効です。
嵌合部のゆるみ
圧入やスナップフィット構造も、応力緩和と密接に関係します。圧入された軸や、撓んだ状態でロックされているスナップフィットの爪は、常に相手部品から反力を受け、応力がかかった状態にあります。この応力によってクリープ変形が進行すると、接触面の圧力が徐々に低下し、保持力が失われます。結果として、がたつきや位置ずれ、最悪の場合は部品の脱落につながります。
密封構造の劣化
Oリングを保持する溝や、パッキンが接触するシール面も、長期にわたって圧縮応力を受け続けます。クリープによって溝が変形したり、シール面の圧力が低下(永久ひずみ)したりすると、密封性が損なわれ、気密・水密不良の原因となります。特に高温の流体を扱うバルブ部品などでは、熱によるクリープの加速が致命的な不具合につながることがあります。
材料選定が勝負を分ける―エンプラのクリープ特性比較
クリープ特性は、エンプラの種類によって大きく異なります。材料の結晶構造やガラス転移温度(Tg)、強化材の有無が重要なファクターとなります。
結晶性樹脂 vs 非晶性樹脂
一般的に、分子鎖が規則正しく並んだ結晶性樹脂(例: PPS、PA、POM)は、分子鎖がランダムに絡み合った非晶性樹脂(例: PEI、PC)に比べて、分子鎖の運動が束縛されているため、クリープ変形しにくい傾向があります。
POM(ポリアセタール):結晶性が高く、剛性、耐疲労性に優れ、クリープ特性もエンプラの中ではトップクラスです。
PA66(ポリアミド66):高強度・高靭性ですが、吸水によって物性が大きく変化する点に注意が必要です。複数の研究論文で、PA66は相対湿度50%の環境下では、乾燥状態に比べてクリープひずみが2倍以上に増大することが報告されています。[2]これは、吸水した水分子が分子鎖の間に入り込み、可塑剤のように作用して分子鎖の運動を活発にするためです。
PPS(ポリフェニレンサルファイド):ガラス転移温度が約90℃と高く、耐熱性に非常に優れます。200℃近い高温環境下でも優れたクリープ特性を維持します。
PC(ポリカーボネート):非晶性のため透明性や耐衝撃性に優れますが、クリープ耐性はPOMなどに劣ります。特に応力集中部では、ソルベントクラックのリスクも考慮が必要です。
PEI(ポリエーテルイミド):Tgが217℃と非常に高い非晶性のスーパーエンプラ。高温での連続使用が可能ですが、応力レベルによっては長期変形のリスク評価が不可欠です。
ガラス繊維(GF)強化による劇的な改善
クリープ特性を向上させる最も効果的な方法の一つが、ガラス繊維(GF)や炭素繊維(CF)による強化です。材料メーカーの技術資料によれば、例えば30%のガラス繊維で強化したPA66(PA66-GF30)は、非強化品(ナチュラル材)と比較して、同じ応力・温度条件下でのクリープひずみ量を1/3~1/5以下に抑制できます。
これは、荷重の大部分を剛性の高いガラス繊維が担い、母材である樹脂(マトリックス)の変形を物理的に抑制するためです。長期的な荷重がかかる構造部品やハウジングには、GF強化グレードの採用が第一選択肢となります。
破断を防ぐための設計戦略―明日から使える4つのアプローチ
クリープによる破損を防ぐには、材料選定と並行して、設計段階での対策が不可欠です。
アプローチ1:応力レベルを低減する
クリープ変形量は応力レベルに大きく依存するため、部品にかかる応力を可能な限り低く、そして均一にすることが基本です。
- 応力集中の緩和:部品の隅や角、穴の周辺などのシャープエッジは応力集中の原因となります。有限要素法解析を用いた研究では、フィレット(R形状)の半径を大きくするだけで、局所的な応力が半減し、クリープ寿命が数倍に延びることも示されています。
- 荷重伝達構造の工夫:荷重が一点に集中しないよう、リブやボスを効果的に配置して面で荷重を分散させる設計が有効です。
アプローチ2:変形を構造で許容する
ある程度のクリープ変形が避けられない場合は、その変形が機能に影響しないような設計も考え方の一つです。例えば、クリアランスを大きめに取る、可動範囲を制限しない、といった配慮です。
アプローチ3:環境要因を厳しく見積もる
クリープは温度と湿度に敏感です。設計時には、想定される最高温度・最高湿度に安全マージンを上乗せした条件で評価を行うべきです。特に熱源の近くや屋外で使用される部品では、このマージン設計が製品の信頼性を大きく左右します。
アプローチ4:長期特性データを正しく使いこなす
信頼性設計の鍵は、短期的な物性データではなく、長期的な特性データを活用することです。材料メーカーのデータシートに記載されている以下のグラフは、必ず確認すべきです。
- クリープ曲線:「ひずみ vs 時間」のグラフ。特定の応力・温度下で、時間と共にどれだけ変形するかを直接的に示します。
- 等時応力線図:クリープ曲線から「100時間後」「1000時間後」など、特定の時間断面を切り出してプロットした「応力 vs ひずみ」のグラフ。これを使えば、目標とする製品寿命(例:10000時間)において、許容できるひずみ量から逆算して、許容応力を見積もることが可能です。
- クリープ破壊曲線:「応力 vs 破断に至るまでの時間」のグラフ。製品にかけられる応力と、その製品が破壊せずに耐えられる時間(寿命)の関係を示します。設計応力がこの曲線を下回るように設定することが、長期信頼性確保の基本となります。
これらのデータは、ISO 899-1(引張クリープ)やISO 899-2(曲げクリープ)といった国際規格に準拠して取得されており、信頼性の高い設計の拠り所となります。
まとめ
クリープは、静かに、しかし確実に進行し、製品の機能を蝕む現象です。特に、金属の感覚でエンプラを設計してしまうと、この「時間軸」の概念が抜け落ち、予期せぬ市場トラブルを招くことになります。
製品の長期信頼性を確保するためには、単に「強い材料」を選ぶのではなく、「時間と共にどう変化するか」を理解することが不可欠です。本コラムで紹介したように、
- クリープのメカニズムを正しく理解する。
- 材料ごとの時間・温度・湿度依存性を把握する。
- 応力緩和や集中を避ける設計を徹底する。
- 等時応力線図などの長期データを活用し、定量的に評価する。
これらのアプローチを設計プロセスに組み込むことで、エンプラの真価を最大限に引き出し、製品寿命の延伸と信頼性向上を実現できるはずです。
【参考文献・引用元】
[1]田中一郎ら「樹脂製ねじ締結体における応力緩和の時間依存性に関する研究」『日本機械学会論文集C編』Vol.71, No.702, pp.1821–1828, 2005.
[2]Y. Zhang et al., “Effect of humidity on the creep behavior of polyamide 66,” Journal of Applied Polymer Science, Vol.132, Issue 45, 2015.