ポリアミド(ナイロン)の寸法が狂う本当の理由:PA樹脂の寸法変化メカニズムと実務的な対策を徹底解説
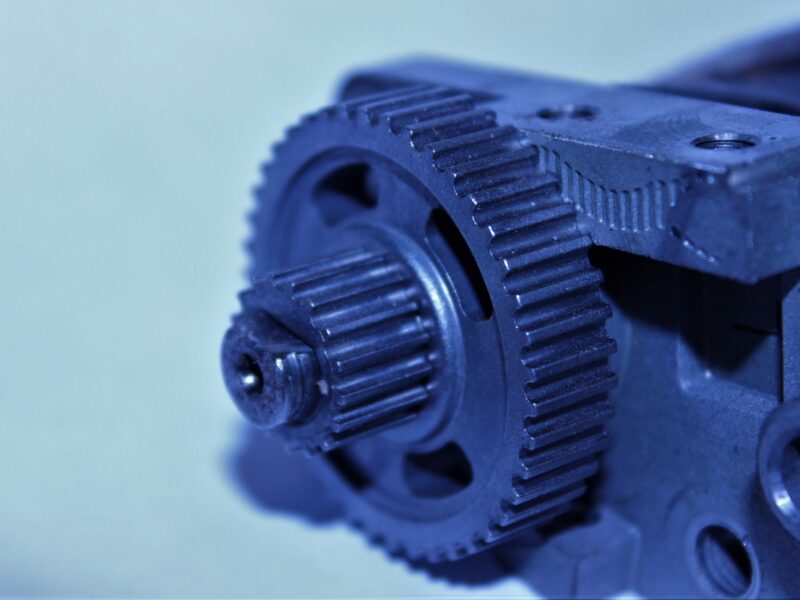
ポリアミド(ナイロン、以下PA)は、その優れた強度、耐熱性、耐摩耗性から、自動車部品や電子機器、産業機械など多岐にわたる分野で活躍するエンプラです。しかし、その優れた性能の裏で、多くの設計者や成形技術者が「寸法が安定しない」、「湿度環境で変形する」という課題に直面しています。この問題の根源は、単に「PAは水を吸いやすいから」という単純な理由だけでは説明できません。実は、吸水膨潤・再結晶・残留応力という三つの要因が複雑に絡み合った“三重苦”によって引き起こされているのです。府中プラは、この複合的なメカニズムを正しく理解することこそが、問題解決の第一歩であると考えます。本コラムでは、PAの寸法変化を引き起こす各要因を深掘りし、実務で直面する課題に対する具体的な対策を解説します。
吸水膨潤
PAの寸法変化を語る上で、避けて通れないのが「吸水」です。PAの分子構造中にはアミド結合(-CONH-)と呼ばれる極性基が存在します。このアミド結合が、水分子(H₂O)と強く引き合い、水素結合を形成しやすい性質を持っています。これにより、PAは他のエンプラと比較して高い吸水率を示します。例えば、代表的なPA6の飽和吸水率(23℃水中)は約9.5%にも達し、一般的な大気中(23℃、50%RH)でも約2.5%の水分を吸収します。PA66でも同様に、大気中で約1.5~2.0%の吸水が見られます。
この吸水が寸法変化に直結するメカニズムは「膨潤」です。PAの分子鎖の隙間に侵入した水分子は、分子鎖間の距離を物理的に押し広げます。結果として、樹脂全体の体積が増加し、製品の寸法が大きくなる(膨潤する)のです。この現象は、あたかもスポンジが水を吸って膨らむ様子に似ています。
特に、この吸水膨潤による変形は、非対称形状の部品顕著に現れます。吸水による膨張が不均一に発生し、製品全体として歪みや反りを引き起こします。また、薄肉の筐体部品は、体積に対して表面積が大きいため、外部の湿度変化の影響を素早く受けやすい特徴があります。筐体のような箱状の製品では、壁面が膨張することで口がすぼまったり、逆に開いたりといった変形が生じます。
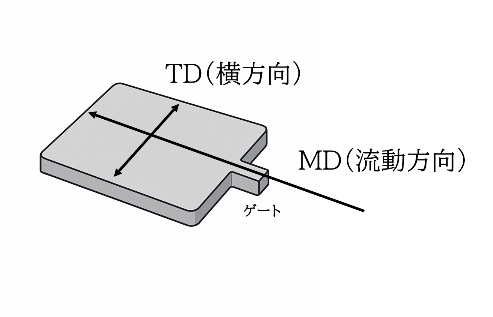
さらに、射出成形品特有の「配向」も、変形を複雑にする要因です。成形時に溶融した樹脂が金型内を流れる際、PAの分子鎖は流れの方向(MD: Machine Direction)に沿って並びます。一方、流れに垂直な方向(TD: Transverse Direction)への配向は弱くなります。吸水による膨潤は、主に分子鎖と分子鎖の間で起こるため、分子鎖が密に詰まっているMD方向よりも、鎖間距離が広がりやすいTD方向でより大きく発生する傾向があります。このMDとTDでの吸水膨張率の差異(異方性)が、特に平板状の製品において、予測困難な反りを引き起こす主要因の一つとなるのです。
再結晶化
PAの寸法変化を複雑にする第二の要因が「再結晶化」です。これは、吸水による膨張とは逆に、縮みを引き起こす現象であり、時間差で発生するため、多くの技術者を悩ませます。
まず、PAは「半結晶性プラスチック」に分類されることを理解する必要があります。射出成形では、高温で溶融した樹脂を低温の金型に射出し、急速に冷却・固化させます。この急冷プロセスにより、PAの分子鎖は完全に整列して結晶化する時間が与えられず、規則正しく並んだ「結晶部」と、ランダムに絡み合った「非晶部」が混在した状態で固化します。この成形直後の状態は、熱力学的に不安定な「非平衡状態」です。
ここに「吸水」が作用します。前述の通り、PAに吸収された水分子は、分子鎖の隙間に入り込みます。この水分子は、分子鎖同士の結びつきを弱め、分子鎖を動きやすくする「可塑剤」のような働きをします。分子運動が活性化することで、これまで非晶部で凍結されていた分子鎖が、よりエネルギー的に安定な状態、すなわち「結晶構造」へと再配列を始めます。これが「再結晶化」です。
再結晶化が進行すると、製品には以下の変化が起こります。
体積収縮:結晶部は非晶部よりも分子が緻密に充填されているため、密度が高くなります。したがって、非晶部が結晶部に変化すると、その部分の体積は減少します。つまり、製品全体としては「縮む」方向に寸法が変化します。
物性変化:結晶化度が高まることで、製品の硬度、剛性、引張強度は向上しますが、逆の言い方をすれば「硬く、脆くなる」傾向を示します。
応力の再配置:内部構造が変化することで、成形時に発生した内部応力のバランスが崩れ、新たな変形を引き起こすきっかけにもなります。
このように、PAの寸法変化は「吸水で膨張する」という単純な一次現象だけではありません。「吸水によって分子運動が活発になり、結果として再結晶化が進み収縮する」という二次的な現象が時間差で発生します。この膨張と収縮という二つの相反する現象が混在するため、PA製品の長期的な寸法変化を正確に予測することは極めて困難になるのです。
残留応力
三重苦の最後は、成形プロセスに起因する「残留応力」です。これは、成形品が完成した時点ですでに内部に抱え込んでいる“時限爆弾”のようなもので、吸水をきっかけに製品を変形させます。
PAのような結晶性樹脂は、非晶性樹脂に比べて成形収縮率が大きく(1.5~2.5%程度)、この大きな収縮が残留応力を生む主な原因となります。射出成形時、金型に接触している製品表面は急速に冷却され、先に固化します。一方、製品内部はゆっくりと冷却されるため、後から収縮しようとします。しかし、すでに固化している表面層が内部の収縮を妨げるため、製品内部には「引張応力」が、表面層には「圧縮応力」が閉じ込められた状態で固化します。これが「残留応力」の正体です。
成形直後の乾燥状態では、PAは比較的高い剛性(ヤング率)を持っているため、この内部応力を保持したまま形状を維持しています。しかし、製品が吸水すると状況は一変します。
吸水によって樹脂が可塑化されると、ヤング率が局所的に低下します。特に、高い応力がかかっている部分ほど、分子レベルでの変形が起こりやすくなります。これにより、それまで内部応力によって均衡を保っていた力のバランスが崩れ、応力を解放しようとする動き、すなわち「応力緩和」が進行します。この応力緩和が、目に見える形での“後変形”となって現れるのです。この現象は、以下のような複合的なリスクを内包しています。
材料特性:PA固有の高い成形収縮率
製品形状:肉厚の不均一さ(ヒケやボイド、応力集中の原因)
成形条件:不適切な金型温度、射出圧力、冷却時間
これらの要因が組み合わさることで、残留応力の大きさや分布が決まります。そして、その応力が使用環境下での吸水によって解放されることで、図面通りの寸法で完璧に成形されたはずの製品が、後になって反ったり、嵌合がずれたりといった不具合を引き起こすのです。
寸法変化が引き起こす事例
これら三重苦が引き起こすトラブルは、様々な製品で発生します。ここで代表的な事例を三つ紹介します。
事例①:ギヤのかみ合い不良
精密な寸法精度が要求されるPA製のギヤは、典型的なトラブル事例です。使用環境の湿度変化により、まず歯の厚み方向で「吸水膨潤」が起こり、歯が厚くなります。これにより、ギヤ同士の隙間が減少し、かみ合いが窮屈になります。さらに、長期的に「再結晶化」が進行すると、歯車全体が不均一に収縮し、ピッチ円直径が変化したり、真円度が悪化したりします。これらの複合的な寸法変化が、異音や振動、異常摩耗、最悪の場合はギヤの破損につながります。
事例②:筐体部品のフタが閉まらない
電子機器や車載部品の筐体も、よく問題となる製品です。特に、フタと本体を固定するためスナップフィットやリブ構造を持つ部品でトラブルが多発します。成形直後は問題なく嵌合できていたにもかかわらず、輸送中や保管中、あるいは市場投入後の高湿度環境下で吸水が進むと、筐体の壁面が膨潤して反ります。これにより嵌合部の位置が微妙にずれ、フタが閉まらない、あるいは一度閉めると固くて開けられないといったクレームに発展するケースもあります。
事例③:ガラス繊維非強化グレードの反り変形
ガラス繊維で強化されていない非強化グレードのPA部品、特に板状の製品では、長期的な反り変形が問題となります。これは、成形時に発生した大きな「残留応力」が、使用環境下での緩やかな吸水によって、時間をかけて徐々に解放されるために起こる現象です。成形直後は真っ直ぐだった部品が、数週間から数ヶ月かけてゆっくりと反り上がっていくため、原因究明が困難な場合があります。これはまさに、残留応力という“時限爆弾”が、吸水という“導火線”に火をつけられた結果と言えるでしょう。
対策の方向性と材料選定・設計・成形の工夫
この三重苦を克服するためには、単一の対策では不十分です。材料選定、製品設計、成形技術という三つの側面から、総合的なアプローチが求められます。
材料選定の視点
まず、寸法安定性を最優先するならば、PA以外の選択肢も視野に入れるべきです。しかし、PAの優れた特性が必要な場合は、PAの中でも低吸水性のグレードを選定することが有効です。 一般的なPA6やPA66から、アミド基の密度が低い長鎖PA(PA11, PA12)や、分子構造に芳香環を含み剛直で吸水しにくい半芳香族ポリアミド(PA9T, PPA)へ変更することで、吸水率そのものを大幅に低減できます。また、PBTやm-PPEなど、吸水率が極めて低い他のエンプラとの比較検討も重要です。
アロイ化やGF強化による物性改善
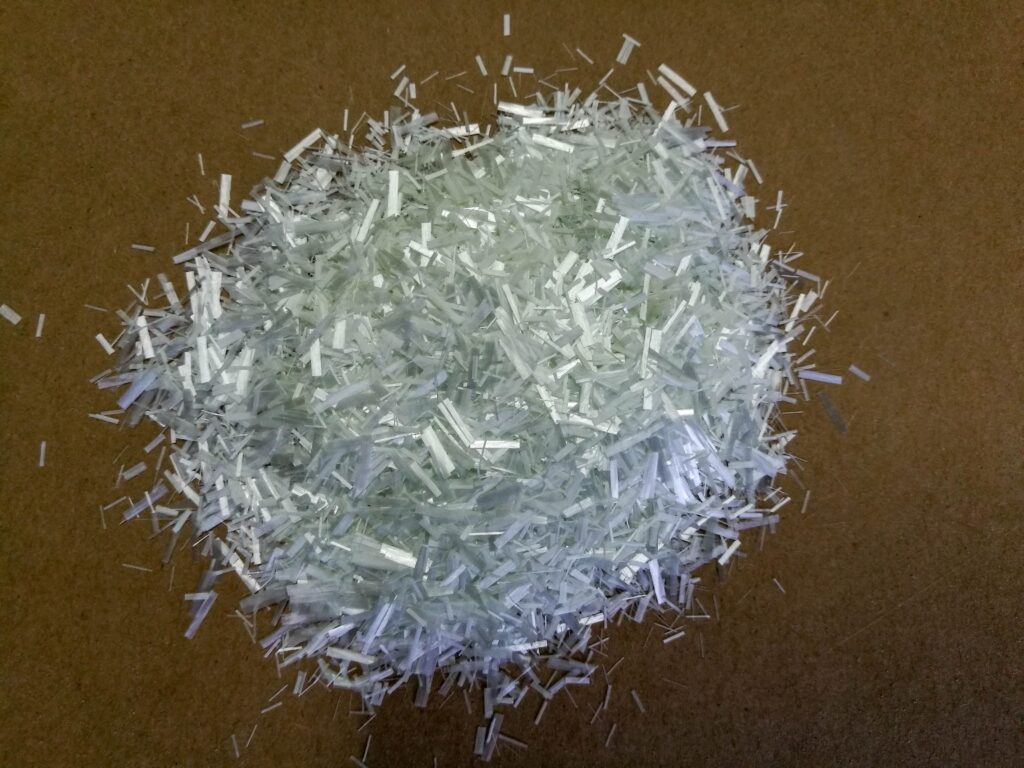
PAにABSやPPEといった低吸水性の樹脂を配合したアロイ材(例:PA/ABS, PA/PPE)は、PAの強靭性を維持しつつ、吸水率とそれに伴う寸法変化を抑制する効果的な選択肢です。また、ガラス繊維(GF)を充填することで、繊維がマトリックス樹脂の動きを物理的に拘束します。これにより、吸水による膨潤や成形収縮が大幅に抑制され、寸法安定性は劇的に向上します。特に収縮の異方性が低減されるため、反り対策として極めて有効です。
成形時の工夫
残留応力を低減し、結晶化度を安定させることが目標です。
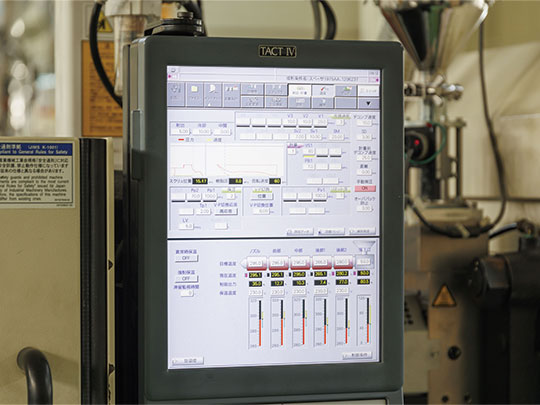
予備乾燥の徹底:成形前にペレットを規定の条件で十分に乾燥させることが、全ての基本です。材料内の水分量がばらつくと、成形品の物性や収縮挙動も不安定になります。
金型温度の最適化・均一化:金型温度を比較的高め(例:80~120℃)に設定し、均一に管理することで、成形中に結晶化を十分に促進させることができます。これにより、成形後の再結晶による寸法変化を最小限に抑えられます。
冷却バランスの調整:製品の肉厚部と肉薄部で冷却速度に差が出ないよう、冷却回路を適切に設計することが残留応力の低減に繋がります。
アニール処理による安定化
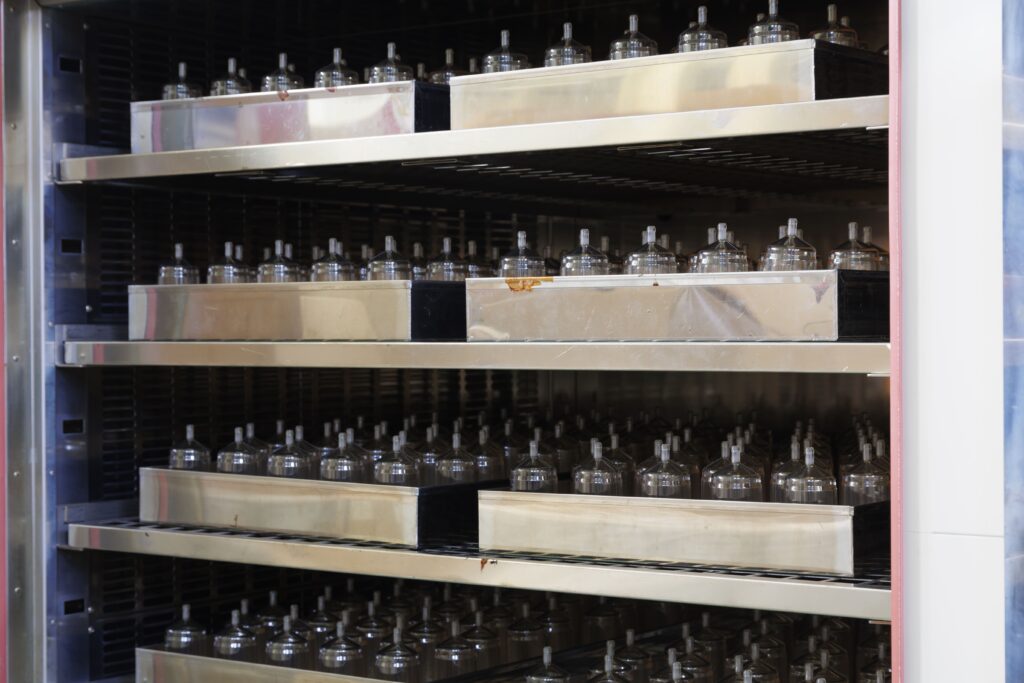
成形後の製品を、ガラス転移温度以上かつ融点以下の温度で一定時間加熱する「アニール処理」は、寸法安定化の最終手段として有効です。この処理により、①残留応力の緩和、②再結晶化の促進、を意図的に行うことができます。これにより、使用環境下で発生するであろう寸法変化を先取りして完了させ、形状を安定させることが可能です。
設計対応
物理的な変化を完全にゼロにできない以上、それを許容する設計思想も重要です。
クリアランスの確保:吸水膨潤や熱膨張をあらかじめ計算に入れ、嵌合部や摺動部には十分なクリアランス(隙間)を設けます。
変形を許容する設計:わずかな変形では機能に支障が出ないよう、弾性変形を利用した嵌合構造にしたり、意図的に「逃げ」を設けたりする設計アプローチです。
反り補正設計:経験則やCAE解析に基づき、発生する反り量を予測し、金型設計の段階で予め逆方向の反りをつけた形状(逆反り)にしておくことで、成形品が狙いの形状になるように調整します。
まとめ
ポリアミド(PA)は非常に有用な材料ですが、その取り扱いには深い知見が求められます。寸法変化の問題は、単なる「吸水」だけでなく、「吸水膨潤」による膨張、「吸水による再結晶化」による収縮、そして「残留応力」の解放による後変形という、三重苦が複雑に絡み合った結果として生じます。これらのメカニズムを正しく理解し、課題に応じて材料選定・製品設計・成形条件のそれぞれを見直し、総合的に対策を講じることが不可欠です。府中プラは、この三位一体のアプローチこそが、PA製品の安定した品質と長期信頼性を実現する鍵であると確信しています。
「PA樹脂の吸水対策まとめ資料(PDF)」をダウンロードする