食品接触(フードコンタクト)部品のためのエンプラ選定と成形設計の実務ポイント
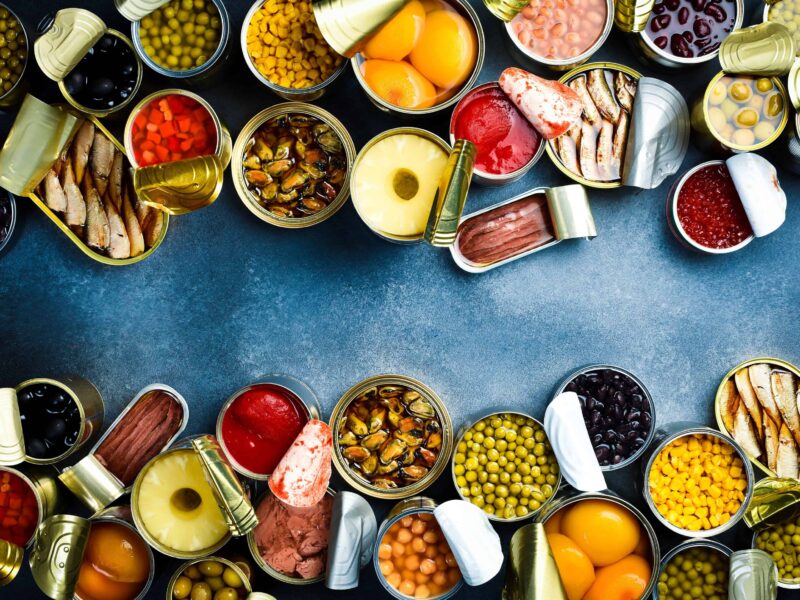
食品と直接接触するプラスチック部品では、安全性を確保するために法令対応が求められることは言うまでもありません。しかし実際の設計現場では、法令をクリアしていても「洗浄を繰り返したら部品が劣化・変色した」、「想定より早く部品が割れてしまった」といった、予期せぬトラブルが生じることがあります。これらの問題は、材料の持つ複合的な特性や、成形プロセスに潜むリスクまでを考慮した、より深い知見が求められます。
本コラムでは、府中プラが長年の経験で培ってきたノウハウをもとに、食品接触用途に求められる材料特性、安全性評価のポイント、成形時の衛生リスク、そして具体的な用途別の材料選定と設計の考え方まで、実務に直結する視点を体系的に解説します。
食品接触用途に求められる材料特性とは?
食品機器や調理器具、包装容器などに使われるプラスチック部品には、単一の性能だけではなく、使われる環境や食品の種類に応じた複合的な性能が求められます。ここでは、特に重要となる特性を解説します。
耐熱性:食洗機・加熱洗浄・滅菌工程への対応
業務用厨房や食品工場では、80℃以上の高温水や蒸気を用いた洗浄・殺菌が日常的に行われます。この熱に耐えられない材料では、変形や軟化による嵌合不良や機能不全を引き起こします。材料選定の際は、連続使用温度や荷重たわみ温度といった指標を確認し、使用環境の最高温度に対して十分なマージンを持つ材料を選ぶことが基本です。
耐薬品性:酢・アルカリ・油脂類・洗浄剤や消毒剤への耐性
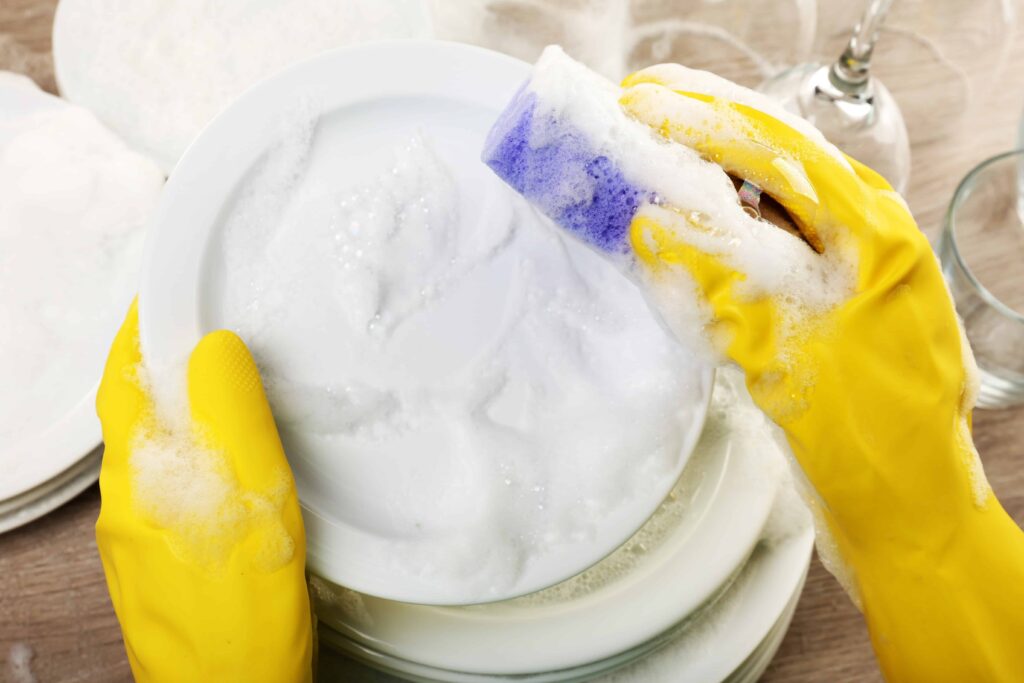
食品そのものにも、酢酸やクエン酸、塩基性、そして様々な油脂類が含まれます。また、洗浄工程では次亜塩素酸ナトリウムやアルコール系の消毒剤、界面活性剤を含む洗剤が使用されます。これらの化学物質に長期間触れることで、材料が膨潤したり、白化したり、最悪の場合は応力亀裂(ケミカルクラック)を引き起こすことがあります。特に非晶性プラスチックは、特定の薬品に弱い傾向があるため、想定される全ての接触物質に対する耐性を事前に評価することが不可欠です。
非吸着性/無臭性:食品の風味やにおいを損なわない安定性
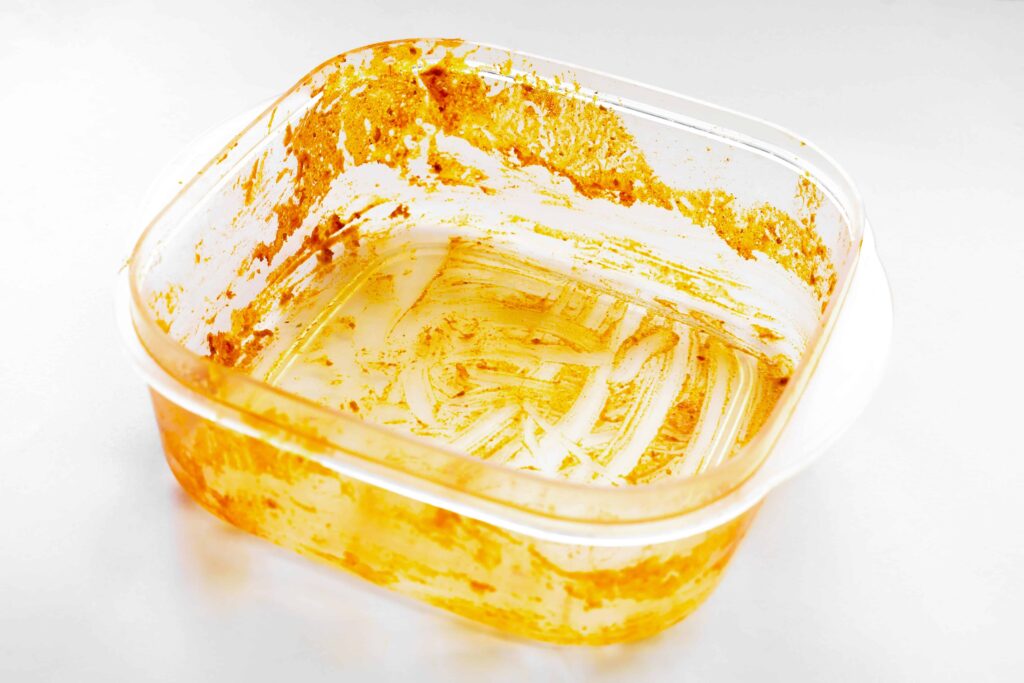
プラスチックは、種類によって食品のにおいを吸着しやすいものがあります。例えば、コーヒーやカレーといった香りの強い食品を扱う部品ににおいが残ると、次に使用する食品の風味を損なう原因となります。また、材料自体が持つ特有のにおいや、成形時に発生する分解ガスが食品に移ることも避けなければなりません。化学的に安定し、においの吸着や発生が極めて少ない材料選定が、製品の品質を左右する重要なポイントです。
透明性/色安定性/意匠性:視認性や外観品質の確保
飲料ディスペンサーの流路や食品保存容器など、内容物を視認する必要がある部品には、高い透明性が求められます。また、製品のデザイン性を高めるために、鮮やかな着色や安定した色調も重要です。ただし、着色剤は後述する安全性評価の対象となるため、食品接触用途で使用が認められたグレードを選択する必要があります。長期間の使用や洗浄によって変色・黄変しにくい色安定性も、製品価値を維持するために欠かせません。
寸法安定性/低吸湿性:嵌合・精度維持のための基本特性
ギアやポンプ、バルブといった精密な動作が求められる部品では、温度や湿度の変化によって寸法が変わってしまうと、性能低下や作動不良に直結します。PA(ポリアミド)系の樹脂は吸湿による寸法変化が大きいため、高湿環境で使用する場合は注意が必要です。吸水率が低く、線膨張係数が小さい材料を選ぶことで、厳しい環境下でも安定した精度を維持できます。
耐加水分解性:蒸気・高湿環境でも性能が低下しない材料
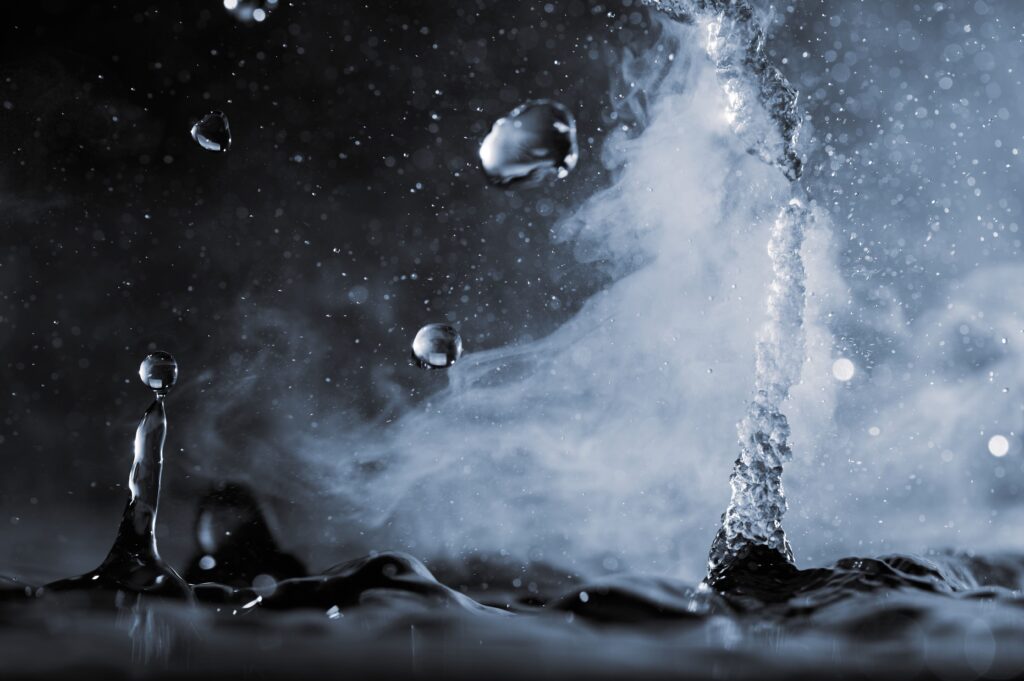
耐熱性と密接に関わるのが、この耐加水分解性です。高温の蒸気や熱水に繰り返し晒される環境では、材料が水分と反応して化学的に分解され、強度や靭性が著しく低下することがあります。特にポリエステル系の樹脂(PET、PBT)は、この影響を受けやすい傾向にあります。スチーム滅菌や高温洗浄が頻繁に行われる用途では、PEEK、PPSU、PEIといったスーパーエンプラが優れた耐加水分解性を発揮します。
安全性:低溶出性、化学的安定性、着色剤・添加剤の適切な制御
これら全ての特性の土台となるのが「安全性」です。材料から食品へ、有害な物質が溶け出さないこと(低溶出性)が絶対条件です。これは、ベースとなる樹脂だけでなく、強度や摺動性を向上させるための添加剤や、製品に色を付けるための着色剤も含まれます。食品衛生法などの規制に適合したグレードであることはもちろん、その材料が化学的に安定しており、長期間の使用においても安全性を維持できることが求められます。
食品接触材料に求められる「安全性評価」
フードコンタクト部品の安全性を担保するためには、客観的なデータに基づいた評価が不可欠です。設計者は、材料メーカーが提供する規制適合証明書を確認するだけでなく、その背景にある評価の内容を理解しておく必要があります。
溶出試験・耐薬品試験
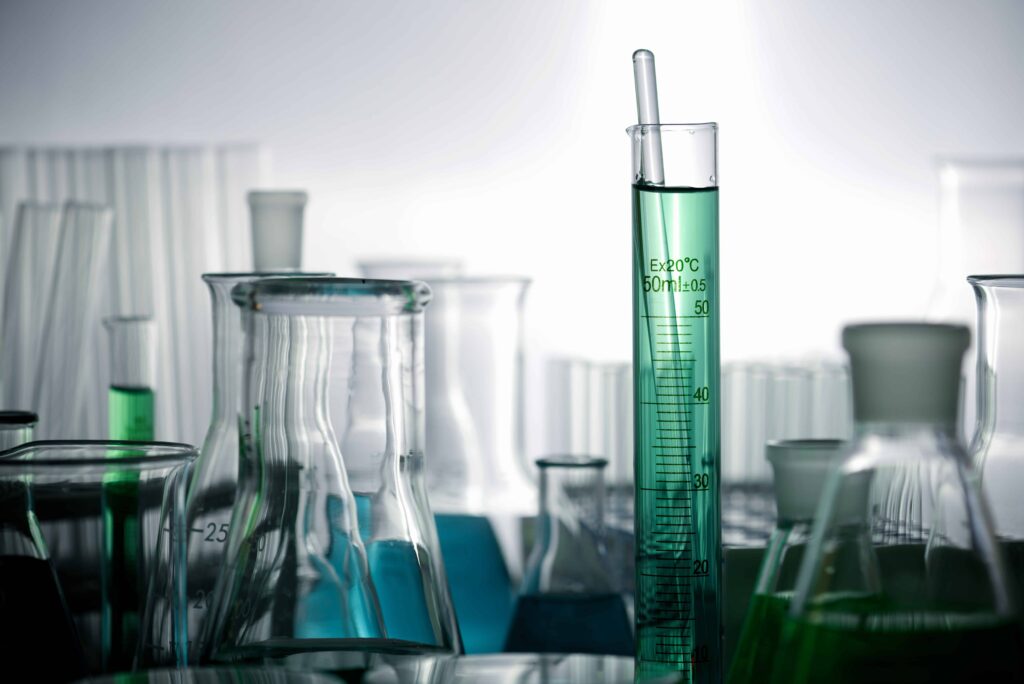
材料から食品へどのような物質がどの程度溶け出すかを評価するのが溶出試験です。日本では「食品衛生法」、欧州では「EU No.10/2011」、米国では「FDA(食品医薬品局)」、中国では「GB規格」など、各国・地域で独自の規制が定められています。
これらの規格では、水、酸、アルカリ、アルコール、油脂といった模擬溶媒を用いて、一定条件下で溶出する物質の総量(総移行量)や、特定の物質の量を測定します。グローバルに製品を展開する場合は、販売先の規制に適合した材料を選定、あるいは製品として試験を実施する必要があります。日本国内向けの製品の場合、ポジティブリスト収載グレードを選定することが必須です。グレード選定は府中プラにご用命ください。
着色剤・可塑剤・添加剤の制限と選定基準
プラスチックの性能や外観を向上させるために添加される物質も、厳しく管理されます。特に、発がん性やアレルギー性が懸念される特定の着色剤や、内分泌かく乱作用が指摘される一部の可塑剤(フタル酸エステル類など)は、使用が禁止または制限されています。
材料メーカーは、これらの規制に対応した安全な物質のみを使用した「食品グレード」や「FDAグレード」といった製品群を用意しています。設計者は、これらの規格適合グレードの中から、要求性能を満たす材料を選ぶことが安全確保の第一歩となります。
異物混入・残留モノマー・可溶成分の制御
材料そのものの安全性だけでなく、それが部品として成形され、出荷されるまでの全工程における衛生管理も問われます。例えば、成形工場での管理が不十分な場合、他の材料のコンタミや、成形機内に残った洗浄剤が製品に付着するリスクがあります。また、重合しきれずに材料中に残ったモノマー(単量体)やオリゴマー(低重合体)が、後から溶出して異味・異臭の原因となることもあります。
安全なフードコンタクト部品の製造は、適切な材料選定と、それをクリーンな環境で安定して加工する成形技術・管理体制の両輪があって初めて実現します。
用途別にみる材料選定例と設計の勘所
ここでは、具体的な用途を例に、要求性能とそれに適した材料、そして設計上のポイントを解説します。
用途例 | 要求性能 | 適した材料 | 設計の勘所・特記事項 |
飲料ディスペンサーの流路部品 | 透明性・耐薬品性・耐熱性 | PEI, PPSU, 半芳香族PA, 非晶性PA, mPPE, TPX | コーヒー等の酸性飲料や洗浄剤(界面活性剤)への耐性が求められます。内容物の確認や衛生管理のために透明性が重要視されることが多く、透明性と耐薬品性、耐熱性を高いレベルで両立できるPEIやPPSUが有力な選択肢です。設計時には、流体の滞留を防ぎ、洗浄しやすい滑らかな流路形状(R形状)とすることがポイントです。 |
食品充填装置のギア・バルブ | 耐摩耗性・耐薬品性・耐熱性・寸法安定性 | PPSU, PEI, PES, PPS, 半芳香族PA | 高速で回転・摺動するため、優れた耐摩耗性と自己潤滑性が求められます。また、洗浄時の薬品や熱にも耐える必要があります。従来は金属が使われてきた部位ですが、軽量化による慣性低減や、グリスレス化による衛生性向上、錆びによる異物混入リスクの排除といったメリットから樹脂化が進んでいます。かかるトルクや荷重、洗浄頻度を考慮し、摺動グレードや強化グレードのPPSやPEIなどを選定します。 |
自動充填機の搬送部品(回転プレート、アーム、ストッパー等) | 寸法安定性・耐熱性・繰返し洗浄耐性・剛性 | PEEK, PEI | 多数の容器を高速かつ正確にハンドリングするため、軽量でありながら高い剛性と、長期にわたる寸法安定性が不可欠です。ここでも金属からの代替が進んでおり、腐食せず、洗浄性に優れ、万が一の接触時にも相手材を傷つけにくいという利点があります。最高の耐薬品性と機械強度、耐熱性を誇るPEEKや、コストと性能のバランスに優れたPEIが活躍します。 |
トングなどの調理器具 | 耐熱性・無臭性・洗浄耐久性 | PPSU, PEI, PES、PSU | 直接食品に触れ、加熱された鍋やフライパンの縁に触れることもあるため、高い耐熱性が求められます。また、繰り返し食洗機で洗浄されるため、耐加水分解性と耐薬品性も重要です。食品の風味を損なわない無臭性も必須です。ガラスのような透明感と高い耐久性を持つPPSUは、デザイン性と機能性を両立できるため、近年採用が増えています。 |
パッキン・摺動部材 | 摺動性・耐薬品性・シール性 | POM | 可動部のシールや、部品間の滑りを良くするために使用されます。自己潤滑性に優れるPOMが多用されますが、必ず食品衛生法やFDAに適合したグレードを選定する必要があります。摩耗によって発生する摩耗粉や、吸水による寸法変化が食品汚染やシール不良につながらないよう、使用環境や相手材との相性を考慮したグレード選定が極めて重要です。 |
成形時に気を付けたい“衛生リスク”
優れた材料を選定しても、成形プロセスに問題があれば、その安全性は損なわれてしまいます。フードコンタクト部品の製造においては、以下の点に特に注意を払う必要があります。
材料乾燥不良による揮発成分や異臭の発生
多くのエンプラは吸湿性があり、成形前に十分に乾燥させる必要があります。乾燥が不十分なまま高温のシリンダーに投入すると、材料が加水分解を起こして物性が低下するだけでなく、分解によって発生した揮発成分やガスが製品に残り、異臭の原因となります。これは、完成した部品の安全性を直接脅かすリスクです。
成形機内の残留物による異物混入・着色・におい移り
一台の成形機で様々な材料や色の製品を生産する場合、前の材料や着色剤がシリンダーやスクリュー内にわずかでも残留していると、次の成形品に混入してしまいます。特にフードコンタクト部品では、黒点などの異物はもちろん、意図しない着色や、前の材料のにおいが移ることは避けなければなりません。
パージ不足に起因する不良品混入
材料や色を切り替える際には、パージ(シリンダー内の清掃)を徹底的に行う必要があります。このパージが不十分だと、切り替え後の初期ショットだけでなく、生産途中でも断続的に前材料のコンタミが発生する可能性があります。府中プラでは、適切にパージをすることでコンタミ対策を慎重に行っています。
成形設備・金型の洗浄/履歴管理が安全確保に直結
フードコンタクト部品を成形する際は、専用の成形機を用意するか、あるいは使用する設備や金型の洗浄手順、使用履歴を厳格に管理する体制が不可欠です。府中プラでは、こうした衛生リスクを排除するため、クリーンな環境の維持と徹底した管理体制を構築しています。
試作開発支援と設計最適化のアプローチ
フードコンタクト部品の開発成功の鍵は、単なる形状確認の試作に留まらず、「機能と安全の両立」を初期段階から追求することにあります。
材質選定 × 部品形状設計の同時最適化
要求される機能を実現する材料を選び、同時にその材料の特性を最大限に引き出す形状を設計することが重要です。例えば、洗浄性を高めるためには、角をなくして滑らかなR形状にしたり、液だまりができないような抜き勾配を設けたりする工夫が必要です。また、流路部品であれば、流体力学の観点から圧力損失が少なく、乱流が起きにくい形状を検討します。
金属代替
軽量化とメンテナンス性向上
部品が軽くなることで装置の駆動負荷が減り、省エネに貢献します。また、錆びることがないため、腐食による異物混入のリスクがなくなり、メンテナンス性が向上します。
高洗浄頻度・蒸気洗浄への対応
PEEKやPPSUといったスーパーエンプラは、金属に匹敵する耐熱性・耐薬品性を持ち、過酷な洗浄環境にも耐えられます。
高寸法精度・低たわみ性の確保
ガラス繊維や炭素繊維で強化したグレードを用いることで、金属に迫る高い剛性(たわみにくさ)と寸法精度を実現できます。
まとめ
府中プラは、お客様の製品コンセプトや課題をお伺いし、最適な材料選定から、量産を見据えた設計提案まで、一貫してサポートいたします。小ロット試作にも対応しており、実機に近い環境での機能評価や安全性評価をスピーディに行うことが可能です。
食品接触部品の開発は、部品単体の視点だけでなく、それが組み込まれる装置やシステム全体としての価値をどう高めるかという視点が不可欠です。材料と成形加工のプロフェッショナルとして、お客様の製品開発を力強く支援させていただきますので、ぜひお気軽にご相談ください。