選ばれる5つの理由
-
01
エンプラ・スーパーエンプラを
中心に約900種類のグレード、
3,000型超の成形実績 -
02
強化材の高充填
グレード(GF70%)など、
難易度の高い射出成形が可能 -
03
最適な材料選定・
金型設計によるVE提案 -
04
塗装・印刷・組立・
超音波溶着などの
二次加工までワンストップ対応 -
05
DX投資によるスマート工場
ヒューマンエラー抑止による
安定品質
01 エンプラ・スーパーエンプラを中心に約900種類のグレード、3,000型超の成形実績
01. 豊富な成形実績と専門知識で、最適な樹脂材質をご提案
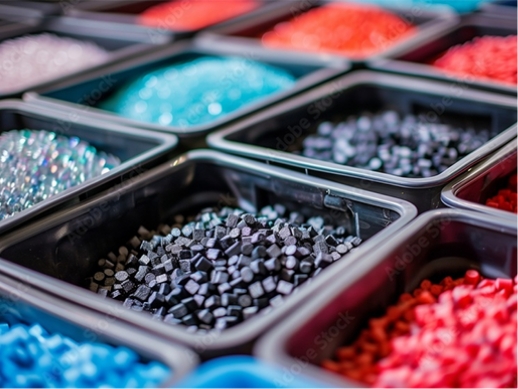
当社は、スーパーエンプラ、エンプラ、汎用プラスチックに至るまで、幅広い材質の成形実績を誇ります。これまでに約900種類に及ぶ主要グレードを網羅し、それぞれの特性を熟知しています。さらに、24年にわたる樹脂メーカーでの経験を持つプロフェッショナルが在籍し、お客様のニーズに最適な材質を提案いたします。樹脂メーカーとの強力なパートナーシップを活かし、最新の材料情報を踏まえたご提案が可能です。
02. あらゆる材質に対応した3,000型超の成形実績
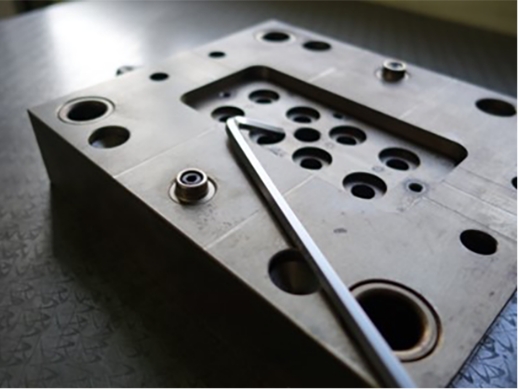
当社は、豊富な材質の受注実績に加え、各材質に対応した鋼材選定・金型設計でも確かな実績を築いております。その金型の総数は3,000型超にも上り、様々な材質や製品形状に柔軟に対応できるノウハウを蓄積してきました。
また、複数の金型製造業と数十年にわたる安定した取引関係を築き、強固な連携体制を確立しています。お客様の材質や製品形状、納期に応じて、最適なパートナー企業を選定し、品質と納期の両面で最善のご提案をいたします。
02 強化材の高充填グレード(GF70%)など、難易度の高い射出成形が可能
01. 高充填率のGF強化グレードの成形に対応
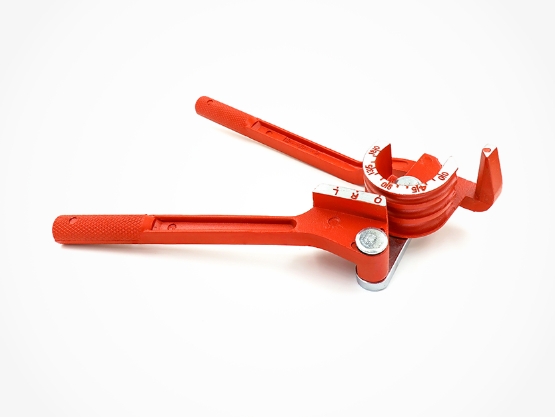
GF強化グレードとは、樹脂にガラス繊維(GF)を添加することにより強度を向上させた樹脂素材です。しかし、GFの割合が増加するにつれて、樹脂の流動性が低下し、プロセスウィンドウが狭まるため、成形難易度が上がり、不良が発生しやすくなります。さらに、外観品質も劣化しやすいという課題があります。
当社では、これらの課題に対して、成形条件の最適化と高度な金型設計ノウハウを駆使し、最大70%のGF充填率を持つガラス繊維強化グレードにも対応可能な成形技術を確立しています。
02. 高難易度材質でも卓越した品質を実現する射出成形技術
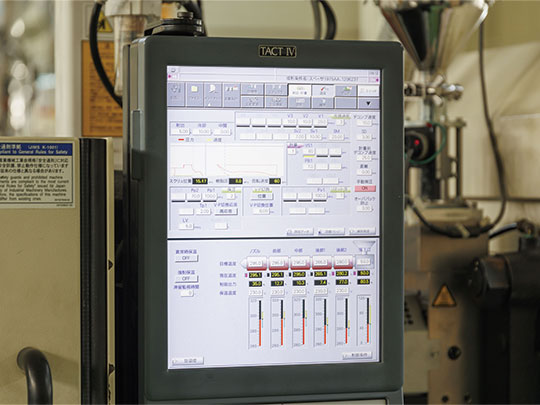
当社は、PEEK・PES・PEI等のスーパーエンプラをはじめとする、成形が難しい材質の射出成形を得意としております。例えば、ガスの発生しやすいMXD6のV0難燃グレードなど、扱いが難しい材質に対しても、豊富な経験と高度な技術で最適な成形を実現します。難易度の高い材質でも品質を損なうことなく、お客様の要求に応える製品を安定して提供いたします。
03. 複雑形状の金型設計もお任せ
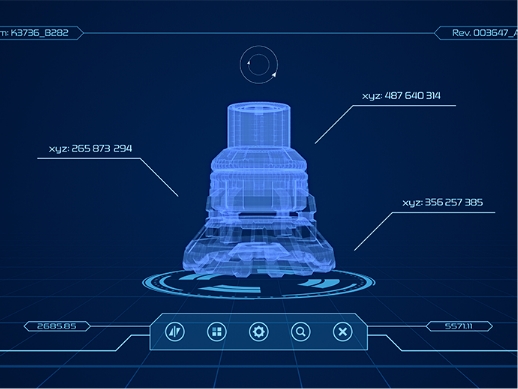
当社は、複雑な形状の製品に対し、従来なら多くの加工工程と費用が必要とされる製品でも、一度の成形で完成できる金型設計を行うことで、お客様の大幅な工数削減に貢献いたします。
具体的には、小ロット品においては、可能な限り駒の組み合わせや形状を工夫しています。大ロット品の場合、モータードライブによる自動ネジ抜き・シリンダー設置やスライドコア・傾斜スライド・斜め抜きスライド等の組み合わせを行っています。
04. 保有する成形機すべてが耐熱・耐食・耐摩耗仕様
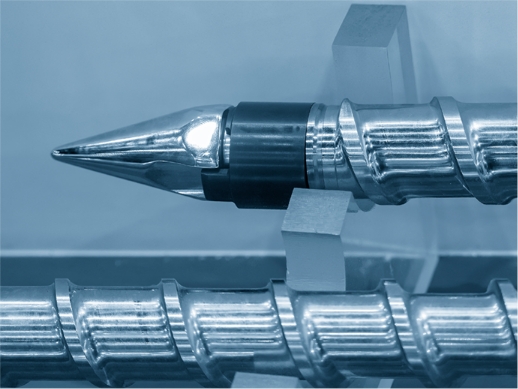
当社は、保有する31台の成形機すべてが高温(400℃の耐熱仕様)、耐食・耐摩耗仕様となっています。この設備により、先にご紹介した高難易度成形材料にも柔軟に対応することができます。さらに、協力工場を含めると成形機の総数は60台を超え、大ロットにも対応可能です。そのため、短納期での納品が実現でき、お客様の多様なニーズに迅速に応えることが可能です。
03 最適な材料選定・金型設計によるVE提案
01. 金属製品の樹脂化実績多数
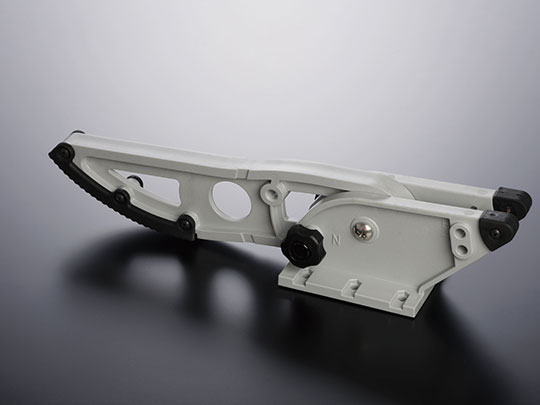
当社は、軽量化や量産性向上を目的とした金属製品の樹脂化において、50年以上にわたる豊富な実績を誇り、業界トップクラスの案件数を取り扱っています。スーパーエンプラ、エンプラ、汎用プラスチックといった幅広い材質に対応しており、これまでに約900種類に及ぶ主要グレードを網羅。その特性を熟知し、高度な成形技術でお客様のニーズに応えています。
さらに、樹脂メーカーで24年の経験を持つプロフェッショナルが在籍し、お客様のご要望に応じた最適な樹脂の選定に関する専門的なサポートをご提供いたします。
02. 部品統合・プロセス削減による、トータルでのコストダウン提案
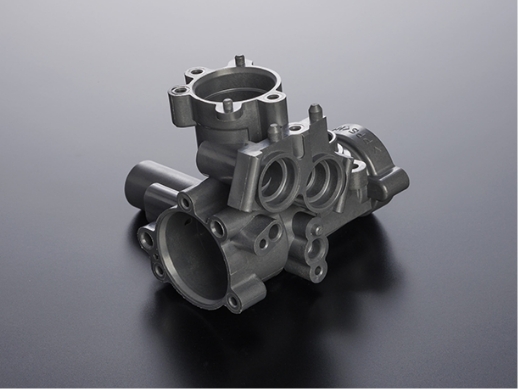
当社では、量産性の向上や工数削減を通じて、トータルでのコストダウンにつながるご提案を積極的に行っています。お客様のニーズに合わせた最適な樹脂を選定し、金属から樹脂への材料変更を行うことで、部品の統合を実現し、穴あけや研磨などの後加工工程を省略することが可能です。
さらに、複数の樹脂部品を射出成形によって一体化し、組立工程を削減したり、材質変更により塗装工程の削減を図ったりと、様々な成功事例があります。
コストダウンに直結する具体的な方法をご提案し、お客様の利益向上に貢献いたします。
03. 機能性強化・環境規制・BCPを考慮した材質提案

当社は、スーパーエンプラ、エンプラ、汎用プラスチックに至るまで、幅広い材質の成形実績を誇り、約900種類に及ぶ主要グレードを網羅し、それぞれの特性を熟知しています。この豊富な経験を基に、耐衝撃性・耐薬品性・耐候性・耐摩耗性などの機能強化に繋がる材質や、有機フッ素化合物(PFAS)・リサイクル・バイオマスプラスチックなどの各種規制を考慮した材質の提案が可能です。
さらに、入手性・コスト・性能等を考慮した、持続可能性のある材料選定を行い、BCP(事業継続計画)にも対応した提案を実施しています。
04 塗装・印刷・組立・超音波溶着などの二次加工までワンストップ対応
01. お客様の外観品質に合わせた塗装を実施
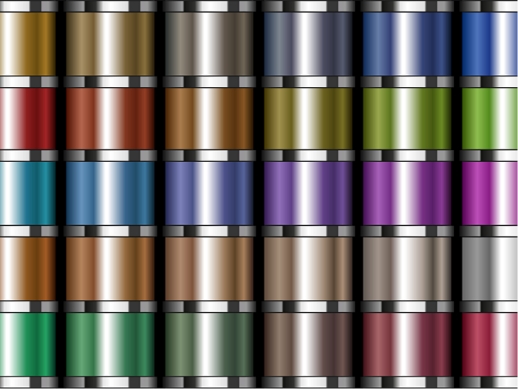
「金属のような光沢を保持したまま樹脂化したい」、「ウエルドラインが全く見えない仕上がりにしたい」などのご要望にも、当社は対応可能です。近隣の塗装工場と連携し、高品質な仕上がりを実現いたします。
特に、樹脂製品で表現が難しいシルバーや、高光沢のブラックやホワイトといった色味にも、塗装によって対応し、金属に匹敵する外観をご提供いたします。また、結晶性樹脂であるMXD6を含む様々な樹脂にも豊富な対応実績があり、難易度の高い仕上げも安心してお任せください。
02. パッド印刷やシルク印刷の対応が可能
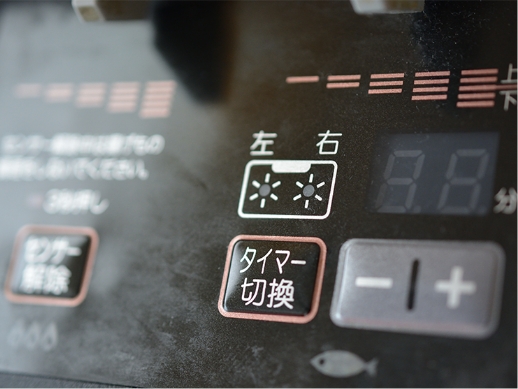
当社ではパッド印刷やシルク印刷によって製品に社名や製品名のロゴ、さらに裏面の各種マークを高品質に印刷することが可能です。
また、同一形状で型式の異なる製品についても樹脂成形品の特性を活かし、印刷の変更で柔軟に対応いたします。
結晶性樹脂への印刷実績も豊富で対応樹脂に最適なインキを選定し、印刷を実施します。
03. 必要に応じて組立まで実施し、完成品を納品
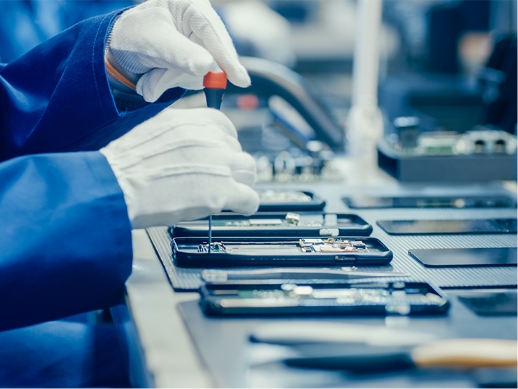
当社ではインサートビットの熱圧入や見切り板の貼り付け、パッキンの挿入といった組立作業に加え、リーク検査まで実施し、完成品として納入することが可能です。
また、塗装・印刷・組立のすべての工程について近隣の協力工場との連携体制が整っており、製品の仕様に応じて「塗装 ⇒ 印刷 ⇒ 組立(熱カシメや見切り板の貼り付け) ⇒ 検査」までを一貫して対応いたします。
04. 超音波溶着機による溶着を実施
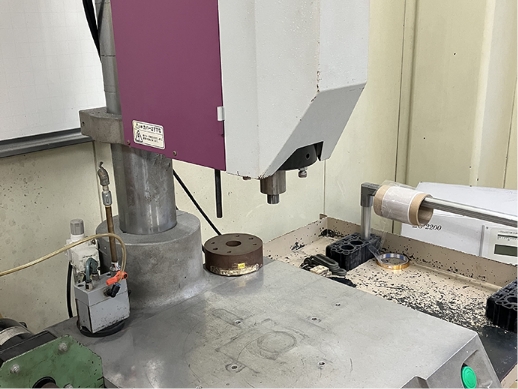
当社では超音波溶着機を用いた高精度な超音波溶着加工を提供しています。
特に流体制御用のノズルやポンプの羽根車など切削加工では実現が難しい複雑な形状に対しても成形後に中空部へ蓋形状を追加し、本体と蓋を超音波溶着することで漏れのない堅牢な封止を可能にしています。これにより、細部まで密閉が求められる複雑な製品にも対応可能です。
さらに、溶着が難しいとされるPPS樹脂についても多くの実績があり、確実な品質を保証いたします。
05 最先端のDX投資による品質の安定化
01. 独自基幹システムで実現する品質の安定と、ヒューマンエラーの抑制
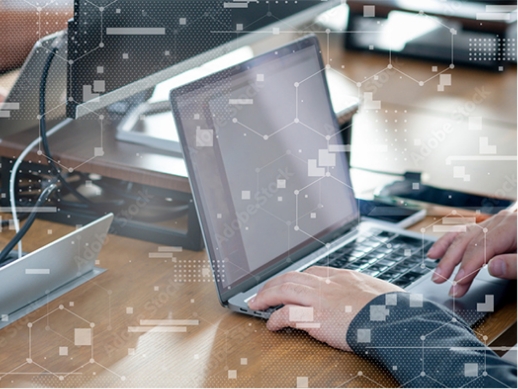
当社は、独自に開発した基幹システムを専任SEが運用し、製造プロセスを徹底的に最適化しています。この基幹システム内で、生産履歴・不良履歴・出荷履歴・見積履歴・在庫情報を一元管理することで、業務ミスを防止し、品質情報を記録・蓄積しています。測定した製品データも基幹システムに保存し、品質の安定性をさらに高めています。
これらの取り組みにより、効率的かつ高品質な生産環境を実現し、ペーパーレス工場の運営を達成しています。
さらに、お客様からお預かりした金型は、基幹システムと連動した自動倉庫で保管しており、腐食等のリスクを回避しています。
02. 成形機全台に端末を導入し、安定品質を実現
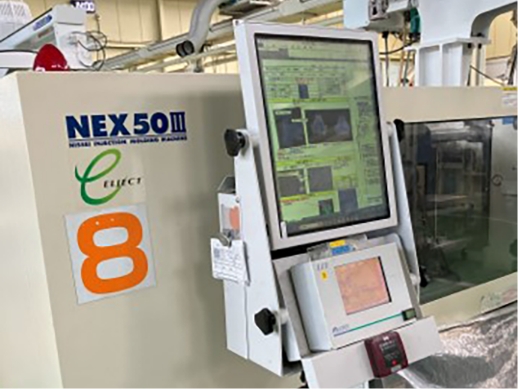
当社では、保有している成形機全台に端末を付けており、この端末と上記でご紹介した基幹システムを連携させています。
端末に、生産品目のスペックや、成形条件、作業手順書などの情報を表示させることで、人の勘や経験に頼ることなく、品質のばらつきを最小限に抑え、安定した製品品質を実現しています。
03. 生産管理システム「MICS」を21世紀初頭から活用
当社では、2001年に生産管理システムのトップランナーであるムラテック社にカスタマイズ開発を依頼し、導入しました。さらに、2005年には基幹システムと連携させ、以降も定期的にバージョンアップを行い、常に最新の状態を維持しています。
この生産管理システムにより、成形機のショット数を正確に管理できるため、最適なタイミングで金型のメンテナンスが可能です。また、樹脂金型専用の超音波洗浄機やドライアイス洗浄機を使用することで、金型の長寿命化によるコストメリットをお客様に提供しています。最新技術を駆使したシステム管理により、効率性とコストメリットを両立した高品質な生産体制を実現しています。