エラストマー(TPE・TPU・TPO・TPSなど)とは
エラストマー(Thermoplastic Elastomer, TPE)は、ゴムの弾性と熱可塑性樹脂の加工性を兼ね備えた材料群であり、熱可塑性エラストマーとも呼ばれます。TPEには、TPU(熱可塑性ポリウレタン)、TPO(熱可塑性オレフィン)、TPS(スチレン系エラストマー)、TPEE(熱可塑性ポリエステルエラストマー)など、用途や特性に応じたさまざまな種類があり、主な特徴は下記の通りです。TPEは従来の加硫ゴムと比較して、成形加工が容易であり、リサイクル性にも優れています。そのため、環境負荷低減が求められる現代の製造業において、ますます需要が高まっています。
1.成形加工性
エラストマーは熱可塑性樹脂の性質を持つため、射出成形、押出成形、ブロー成形が可能です。従来の加硫ゴムのような長時間の加硫工程が不要で、短時間で成形できることが大きなメリットです。
2.優れた弾性
エラストマーは、ゴムと同様に弾性を持ち、伸縮性が高いのが特徴です。特にTPSやTPUは、優れた柔軟性を持ち、繰り返し変形しても元の形に戻る特性があります。
3.環境性能
エラストマーは加硫ゴムと異なり、リサイクルが可能です。また、PVC(ポリ塩化ビニル)の代替材料として環境負荷の少ない材料としても注目されています。
TPEの代表的な材料として、TPU(熱可塑性ポリウレタン)、TPO(熱可塑性オレフィン)、TPS(スチレン系エラストマー)、TPEE(熱可塑性ポリエステルエラストマー)を取り上げ、その特徴、用途を詳述します。
TPU(熱可塑性ポリウレタン)
TPU(Thermoplastic Polyurethane)は、耐摩耗性、耐薬品性、柔軟性に優れたエラストマーであり、靴底、ホース、キャスター、工業用ベルト、振動吸収材などに広く使用されています。
– 耐摩耗性: 非常に高く、摩擦が多い環境でも優れた耐久性を発揮。
– 耐薬品性: 油や溶剤に強く、工業用途に適している。
– 柔軟性: 非常に柔らかく、衝撃吸収材としても使用可能。
– 耐熱性: 150℃程度まで耐えられるが、高温下での長期使用には注意が必要。
主な用途: 靴底、工業用ベルト、耐摩耗部品、振動吸収材
TPO(熱可塑性オレフィン)
TPO(Thermoplastic Olefin)は、PP(ポリプロピレン)をベースにしたエラストマーで、耐候性や耐衝撃性に優れています。特に屋外用途に強く、自動車バンパーや建材などに利用されます。
– 耐候性: 紫外線・オゾン・湿気に強く、屋外用途に最適。
– 耐衝撃性: 低温下でも靭性を維持し、衝撃による破損が少ない。
– 加工性: 射出成形、押出成形が可能で、大型部品にも対応しやすい。
– 耐薬品性: 一部の溶剤には弱いが、水や一般的な酸・アルカリには比較的強い。
主な用途: 自動車バンパー、建材、屋外用品、配管材
TPS(スチレン系エラストマー)
TPS(Thermoplastic Styrene)は、スチレンをベースとしたエラストマーで、柔軟性と加工性が特に優れています。ソフトな触感が求められる用途に適しており、グリップ材やスポーツ用品、玩具などに使用されます。
– 柔軟性: 非常に高く、手触りが良い。
– 加工性: 熱可塑性樹脂と相溶性があり、異素材とのオーバーモールド成形が可能。
– 耐候性: 紫外線やオゾンにはやや弱く、屋外用途には適さない。
– 耐熱性: 高温下では形状が維持しにくいため、高耐熱用途には不向き。
主な用途: グリップ材、スポーツ用品、玩具、生活用品
TPEE(熱可塑性ポリエステルエラストマー)
TPEE(Thermoplastic Polyester Elastomer)は、耐熱性、耐薬品性、耐摩耗性に優れたエラストマーであり、高い機械的強度を持つのが特徴です。自動車部品や電子部品など、高い耐久性が求められる用途に適しています。
– 耐薬品性: 非常に高く、工業用途に適している。
– 耐摩耗性: TPUに次いで優れるが、硬度が高いため用途が限定される。
– 耐熱性: TPUよりも高温に耐え、170~200℃の環境でも使用可能。
– 機械的強度: 高剛性で、構造材としても利用可能。
主な用途: 自動車部品、電子部品、工業用機械部品
主要TPEの特性比較
当社で使用している主なTPEは下記の通りです。
1.Sunprene™(三菱ケミカル)
原材料と製法: 主にポリ塩化ビニル(PVC)をベースにした熱可塑性エラストマーで、可塑剤や安定剤を添加して柔軟性を高めています。製造工程では、PVC樹脂と添加剤を混合し、押出機で溶融混練してペレット化します。
特徴: 耐候性、耐油性、柔軟性に優れ、射出成形が容易です。
用途: 自動車部品、電線被覆材、シール材
2.Hytrel®(東レ・セラニーズ)
原材料と製法: ポリエステルとポリエーテルのブロック共重合体。ポリエステル部分が硬質セグメントとして強度を提供し、ポリエーテル部分が柔軟性を付与します。共重合体をペレット化し、乾燥後に射出成形します。
特徴: 高い耐熱性と耐薬品性、優れた弾性
用途: 自動車用ホースやベルト、工業用部品
3.PELPRENE™(東洋紡エムシー)
原材料と製法: ポリエステル系熱可塑性エラストマー(TPEE)。1,4-ブタンジオールテレフタレートとポリブチレングリコールの共重合体。硬質セグメントと軟質セグメントの比率を調整して物性を最適化します。
特徴: 高い耐摩耗性と耐熱性、低温での柔軟性
用途: 自動車部品(シール材、ギア)、電子機器部品
4.Santoprene™(セラニーズ)
原材料と製法: PP(ポリプロピレン)とEPDMゴムのブレンド。動的加硫技術を使用し、ゴム相を硬化させることでゴム特有の弾性を持ちながら熱可塑性樹脂の加工性を実現しています。
特徴: 耐候性、耐油性に優れ、高いリサイクル性。
用途: 自動車用シール材(窓枠やドアシール)、医療機器
5.MILASTOMER™(三井化学)
原材料と製法: ポリオレフィン系エラストマーであり、PP(ポリプロピレン)やPE(ポリエチレン)をベースにしたブレンド。架橋構造を持たないため熱可塑性加工が可能です。
特徴: 軽量、高い耐衝撃性と耐候性
用途: 自動車内装材、玩具、スポーツ用品
6.EARNESTON™(クラレ)
原材料と製法: エチレン系エラストマーであり、HMWPE(高分子量ポリエチレン基材として使用。特殊な触媒技術によって分子構造を制御しています。
特徴: 高い柔軟性と耐薬品性
用途: 電線被覆材、自動車部品
7.MAXIRON™(昭和化成工業)
原材料と製法: スチレン系エラストマー(TPS)。SBS(スチレン-ブタジエン-スチレン)またはSEBS(スチレン-エチレン-ブチレン-スチレン)の構造を持つ共重合体
特徴: ソフトな触感、高い加工適応性
用途: グリップ材や玩具、自動車内装部品
8.レザミン(大日精化工業)
原材料と製法: ポリアミド系エラストマー。ナイロン樹脂に柔軟成分を混合し、高温高圧下で溶融混練して作られます。
特徴: 高い機械的強度と耐摩耗性
用途: 工業用ギア、自動車部品
9.ミラクトラン®(日本ミラクトラン)
原材料と製法: ポリエステル系熱可塑性エラストマー。ポリエステル硬質セグメントとポリカーボネート軟質セグメントからなる共重合体です。
特徴: 高い透明度、優れた耐熱・耐薬品性能
用途: 医療機器、自動車内装材
各製品の種類、硬度
エラストマー(TPE・TPU・TPO・TPSなど)を推奨する用途・ニーズ
01 人間工学的デザインが求められるグリップ・ハンドル用途
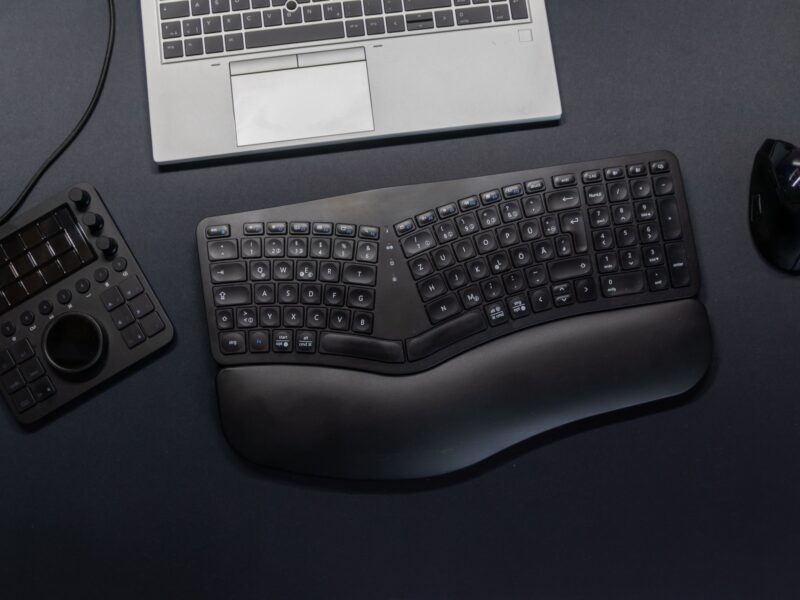
TPEは、ゴムのような柔軟性と成形加工性を兼ね備えており、滑りにくく快適な触感を提供するため、グリップやハンドル用途に最適な材料です。特に、スポーツ用品、電動工具、家電製品の持ち手部分に使用され、操作性の向上に寄与します。また、TPEはオーバーモールド成形が可能で、硬質プラスチック(PC、PP、ABSなど)との一体成形によるデザインの自由度が高く、耐衝撃性や耐摩耗性を向上させることができます。さらに、環境規制をクリアしたグレードもあり、安全性を重視する医療機器や食品関連機器のハンドルにも適用可能です。当社では、TPEの特性を最大限に活かした高品質なグリップ・ハンドル製品の量産体制を整えており、耐久性やデザイン性を重視した成形品の提供が可能です。
02 防振・防音性能が求められるシール材・ガスケット用途
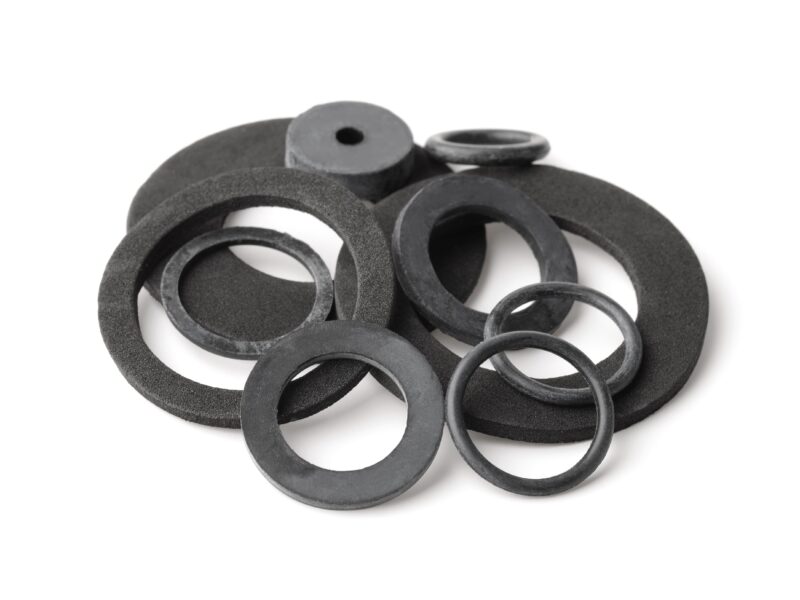
TPEは優れた弾性と耐久性を持ち、振動吸収や防音性が求められるシール材やガスケットに適した材料です。特に、電子機器、住宅設備のシール部品として広く使用され、長期間にわたり安定したシール性能を維持します。TPEの低圧縮永久歪特性により、繰り返しの圧縮や変形後でも弾力を維持し、高い密閉性を確保します。また、耐油性や耐薬品性を向上させたグレードもあり、厳しい環境条件下での使用にも対応可能です。当社では、精密金型技術と成形条件の最適化により、高精度なシール部品の量産を実現。用途に応じた最適なTPEグレードの選定から製品設計、量産対応まで、一貫した技術サポートを提供します。
03 柔軟性と安全性が求められる医療・介護製品用途
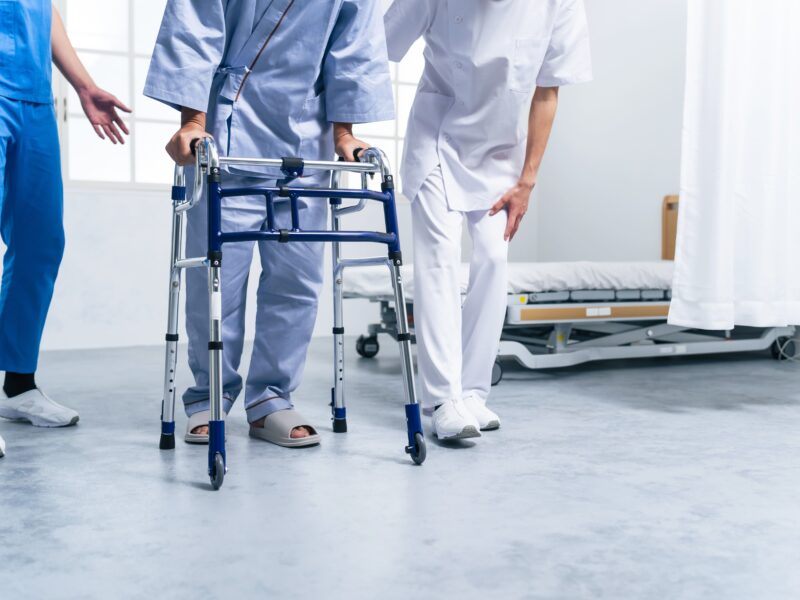
TPEは無毒性で肌触りがよく、医療・介護分野での安全性が求められる用途に最適な材料です。特に、点滴バッグのコネクタ、マスクシール部分、介護用グリップなどに使用され、ゴムのような弾力性を持ちながら、可塑剤を含まないグレードを選択できるため、生体適合性にも優れています。また、耐薬品性や滅菌耐性が高く、オートクレーブ(高温高圧滅菌)やガンマ線滅菌にも対応可能なタイプが存在し、医療現場での使用にも適しています。設計段階からの材料選定、試作、量産まで包括的なサポートを提供し、安全性と快適性を両立する製品開発を支援します。
当社のエラストマー(TPE・TPU・TPO・TPSなど)成形における強み
01 製品デザイン、金型デザインに関するノウハウ
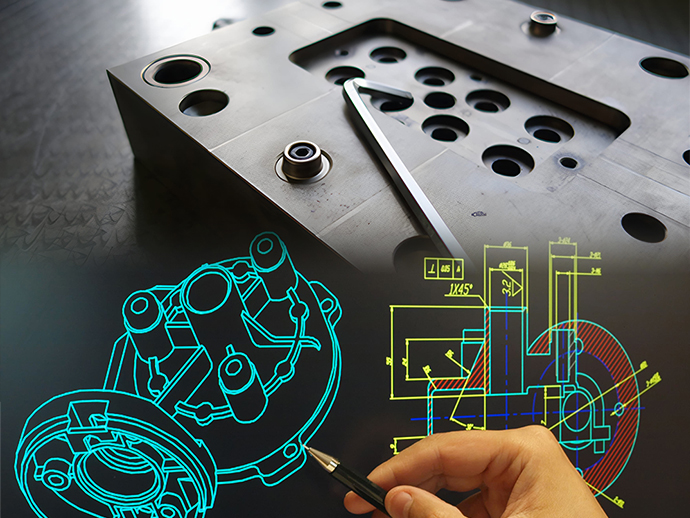
当社は、TPEの特性を最大限に活かした製品設計および金型設計のノウハウを有しており、成形後の寸法安定性や機械的強度を向上させるための最適な形状設計を提案いたします。TPEは優れた柔軟性と耐摩耗性を持つ一方で、流動性が高く、成形時にバリが発生しやすい特性があります。そのため、当社では金型合わせ面の精度向上や射出圧力の適切な管理を行い、ゲート設計や金型の冷却機構を工夫し、安定した成形を実現します。また、オーバーモールド成形においても、異材接着性を高めるための接着面処理やクリアランス設計を工夫し、硬質材料と軟質材料間で生じる収縮率差による反りや剥離リスクにも対応し、金型の高精度化による製品品質の向上を図ります。製品形状については、リブ設計や肉厚管理によって反りや収縮を抑制しつつ、高い剛性と強度を実現しています。リブの肉厚は母材厚さの50~70%以内に設定し、肉盗み技術を活用して冷却時間差による成形不良も防止しています。加えて、TPUやPP、ABSなどの異材との相性を考慮し、最適な組み合わせによる製品設計にも対応可能です。また、均一な冷却を実現するための金型温度管理や、最適な離型勾配の設計によって、成形品の品質を向上させています。
当社では、これらの技術とノウハウに基づき、お客様ごとのニーズに応じた最適な成形条件を提案します。試作段階から量産まで一貫したサポート体制を整え、高品質な製品を提供いたします。
02 最適な成形条件の設定
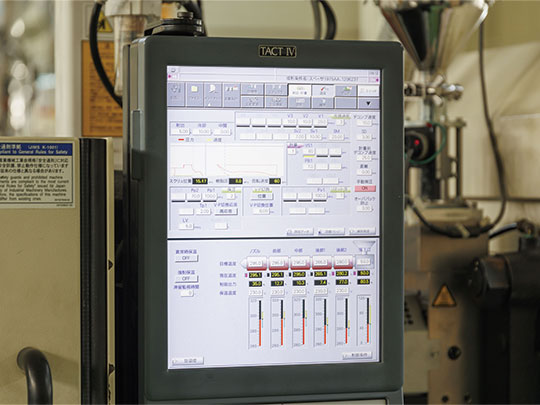
TPEの成形には、適切な温度管理と成形圧力の調整が不可欠です。当社は、TPEの特性を考慮し、樹脂温度を180~230℃に、金型温度を20~60℃の範囲で管理することで、製品の寸法精度を向上させています。特に、TPEは冷却速度が品質に大きく影響を及ぼすため、冷却工程を最適化することで、成形収縮や変形を最小限に抑えます。また、TPEは吸湿性があるため、事前の適切な乾燥(約80℃で3~4時間)を徹底し、成形時のガス発生や外観不良を防止します。さらに、厚肉成形や薄肉成形にも対応できるよう、流動解析を活用して最適な充填バランスを確保し、安定した成形加工を実現します。その他、射出速度や保圧の最適化にも注力し、ウェルドラインの低減やボイドの発生を抑える工夫を行っています。特に、薄肉成形では高速充填による短時間成形を実現し、反対に厚肉成形では段階的な保圧制御により、内部の気泡やヒケを防止します。
当社では、これらのノウハウを活かし、精密なTPE成形を必要とするお客様に対し、高品質な製品と一貫したサポートを提供いたします。
本記事の内容は、執筆時点での情報に基づいております。記載内容は各メーカーの公式情報と異なる可能性がございます。当社は本記事の内容の正確性、完全性について保証するものではなく、本記事の利用によって生じたいかなる損害についても責任を負いかねます。読者の皆様におかれましては、具体的な材料選定に際しては当社までお問合せをお願い致します。
エラストマー(TPE・TPU・TPO・TPSなど)の成形実績
-
流体制御機器 方向転換用ボール
本製品は、流体制御パイプの先端に取り付け、吐出方向を調整するボールです。
水漏れ防止とスムーズな可動性を確保するため、ネジ部にはガラス繊維入りPPを使用し、自動成形で精密に製造しています。その後、ネジ部を金型にインサートし、TPOを射出成形することで、高い密着性と柔軟性を備えた一体型構造を実現しました。
詳細はこちら
-
測定器(硬度計)のコネクタ差し込み部カバー
本製品は、硬度計のコネクタ差し込み部を保護するカバーです。
従来のABS製カバーと別部品のパッキンを統合するため、カバー本体に溝を設計し、TPUによる二次成形を採用しています。これにより部品点数を削減し、組立工程を簡略化しました。さらに、製造後の印刷工程も社内で一貫対応しています。
詳細はこちら
-
画像測定器 ハンドル部品
本製品は、画像測定器の軸を操作するハンドル部品です。
滑りにくさと快適な触感を重視し、本体をABSで成形後、外形全体にTPUを二次成形しています。これにより、耐久性と強度を保ちつつ、手に馴染む柔らかな触感を実現しました。
詳細はこちら