PEEKとは?最強のスーパーエンプラの特性、射出成形技術を徹底解説
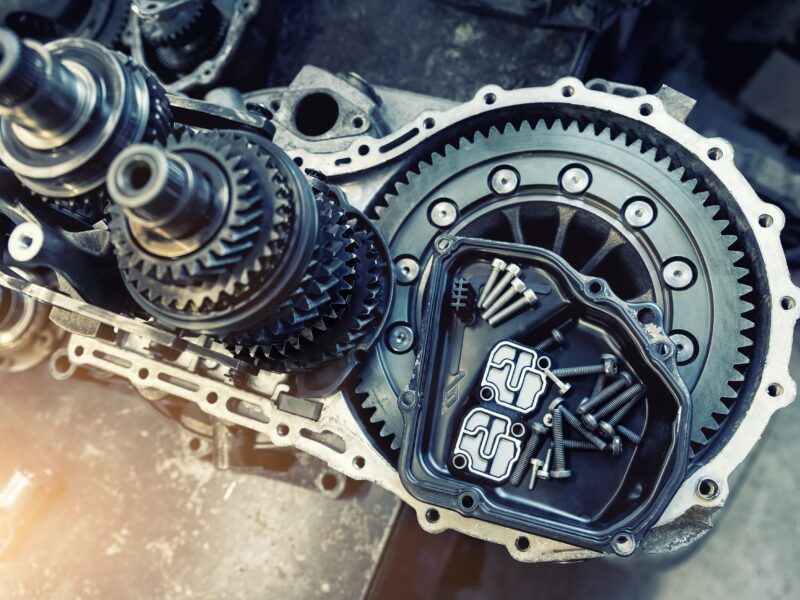
射出成形の専門メーカーとして長年の経験を持つ当社が、高性能ポリマーの最高峰とされるPEEKの可能性と、その加工技術について解説します。PEEK(ポリエーテルエーテルケトン)は、従来金属が使用されてきた過酷な環境でも優れた性能を発揮する先進素材です。近年、軽量化や機能性向上のニーズの高まりにより、自動車や航空宇宙、医療機器など様々な産業分野で注目を集めています。
射出成形メーカーから見たPEEKの魅力
当社では様々な高機能プラスチックを扱ってきましたが、PEEKは他の素材と一線を画す特性を持っています。特に、金属代替として使用される場面での優位性は顕著です。
バランスの取れた高性能特性
PEEKの最大の特徴は、単一の特性だけが突出しているのではなく、多方面にわたって高い性能を持ち合わせている点です。射出成形品としての加工性を維持しながら、金属並みの耐久性と機能性を両立させた素材と言えます。
耐熱性能と寸法安定性
PEEKの実用連続使用温度は約260℃に達し、一般的なエンジニアリングプラスチックを大きく上回ります。私たちが製造する部品においても、高温環境下での寸法安定性は非常に重要です。特に精密部品では、熱による膨張や収縮が機能に直結するため、PEEKの優れた耐熱性と寸法安定性は大きなアドバンテージとなります。
化学薬品に対する優れた耐性
当社のお客様の中には、腐食性の高い化学物質を扱う環境で使用される部品を必要とされる方も多くいらっしゃいます。PEEKは多くの酸・アルカリ・有機溶剤に対して極めて高い耐性を示すため、こうした過酷な環境でも長期間信頼性を維持できる部品製造が可能です。
機械的強度と耐疲労性
射出成形品に求められる機械的強度と耐久性において、PEEKは特筆すべき性能を発揮します。私たちの製造経験では、繰り返し応力がかかる部品や高負荷環境で使用される部品において、PEEKは優れた耐疲労性を示します。特に繊維強化グレードを使用した場合、金属に迫る強度特性を実現できます。
PEEKの化学的背景と特性
分子構造と基本情報
PEEK(ポリエーテルエーテルケトン)は、ポリアリールエーテルケトン(PAEK)という高機能ポリマー群に属する材料です。このPAEK系ポリマーは、分子鎖に芳香族環(アリール基)、エーテル結合、そしてケトン基を交互に配置した構造を有しており、これが多くの優れた物理・化学特性の源となっています。
(画像の出所:ビクトレックスジャパン「PEEKって何? – スーパーエンプラ概論(パート2)」)
PEEKの分子構造を詳しく見ると、エーテル(E)-エーテル(E)-ケトン(K)という基本単位が繰り返し並ぶ“E-E-K”構造をとっています。この構造が平均して200〜300個ほど連なって一つのポリマーチェーンを形成しています。この直鎖状の分子構造の中で、剛性の高い芳香族環とケトン基が高い機械的強度や耐熱性を実現し、柔軟性を持つエーテル基が適度な靭性を付与しています。また、PEEKは芳香族化合物を含みますが、他の多くの芳香族物質(トルエンやナフタレンなど)と異なり、通常の使用環境下では無臭である点も特徴です。PEEKの開発は1970年代の高性能材料研究の流れの中で始まり、1980年代には商業生産が確立されました。現在では複数のメーカーから各種グレードが提供されており、当社ではお客様の用途に応じた最適な原材料を選定しています。
結晶構造とその影響
当社の射出成形における知見から特に注目すべきは、PEEKが持つ半結晶性の構造です。結晶化の程度は成形時の冷却条件や保温プロセスによって大きく変化し、それに応じて寸法安定性、耐摩耗性、さらには耐薬品性といった特性にも違いが生まれます。これは、規則的に並ぶE-E-K構造が結晶化を可能にし、それによってPEEK特有のバランスの取れた物性が実現されているからです。当社では金型温度や冷却速度の最適化に独自のノウハウを持ち、安定した結晶構造の確保によって、高精度かつ高信頼性のPEEK成形品を提供しています。
耐燃性と安全性
一般的な樹脂と異なり、PEEKは自己消火性を持ち、燃焼時の発煙量も極めて少ないという特徴があります。当社が航空機内装部品や医療機器向けに提供する部品において、この特性は非常に重要です。安全基準の厳しい分野においても、PEEKは優れた選択肢となります。
PEEK成形における技術課題と当社のソリューション
高温処理の技術的課題
PEEKの射出成形において最大の課題は、その高い加工温度です。当社の経験では、一般的に370℃から400℃の範囲で樹脂を溶融させる必要があります。この高温での加工は特殊な設備と技術を要求します。当社では、PEEK専用の高温対応射出成形機を導入し、最適な温度プロファイルを構築することで安定した成形を実現しています。また、熱分解による樹脂の劣化を防ぐため、滞留時間の管理も厳密に行っています。
金型設計の重要性
PEEKの成形では、金型設計が製品品質を大きく左右します。当社の金型設計では以下の点に特に注意を払っています。
・高温に対応する金型材料と表面処理
・均一な冷却を実現するための冷却回路設計
・結晶化度を制御するための金型温度管理システム
・離型性を確保するためのゲート位置と突出し機構
特に、ウェルドラインやボイドの発生を抑制するために、当社独自の金型設計ガイドラインを策定し、高品質なPEEK製品の製造を実現しています。
成形収縮と寸法精度の確保
PEEKの成形収縮率は材料グレードによって異なりますが、一般的には約1〜2%の範囲にあります。当社では長年の経験から蓄積したデータベースを活用し、製品ごとに最適な収縮率補正を行い、高い寸法精度を実現しています。特に精密部品においては、後加工を極力減らすために射出成形段階での寸法精度の確保が重要です。当社では成形条件の最適化に加え、必要に応じて金型製作段階でのCAE解析も活用しています。
コスト効率と生産性の向上
PEEKは高価な材料であるため、製造コストの最適化は重要な課題です。当社では以下の取り組みによりコスト効率を高めています。
・ランナー系の最適設計によるロス削減
・再生材の有効活用(要求特性に応じて)
・サイクルタイムの最適化
特に、少量多品種生産においても効率的な製造が可能な生産方式を導入し、お客様のニーズに合わせた柔軟な生産体制を構築しています。
産業界におけるPEEKの金属代替事例
自動車部品での応用
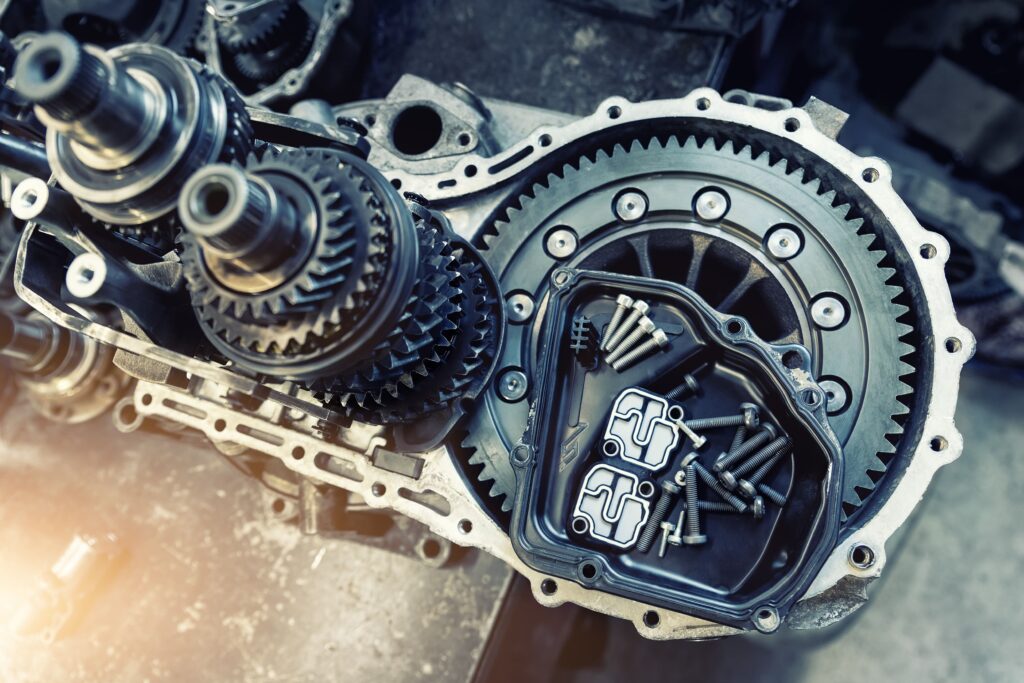
自動車産業では、軽量化と燃費向上を目指して、様々な部品でPEEKの採用が進んでいます。特に注目されているのが、高温環境下で使用されるエンジン周りの部品です。業界では、トランスミッション部品やベアリングケージなど、従来金属で製造されていた多くの部品がPEEK製に置き換えられています。例えば、ドイツの大手自動車メーカーではトランスミッション用ギアにPEEKを採用し、騒音レベルを約3dB低減させることに成功したという報告があります。また、潤滑システム内のバルブやシールリングにPEEKを使用することで、耐久性の向上と摩擦損失の低減を実現した事例も報告されています。
航空宇宙分野での実績
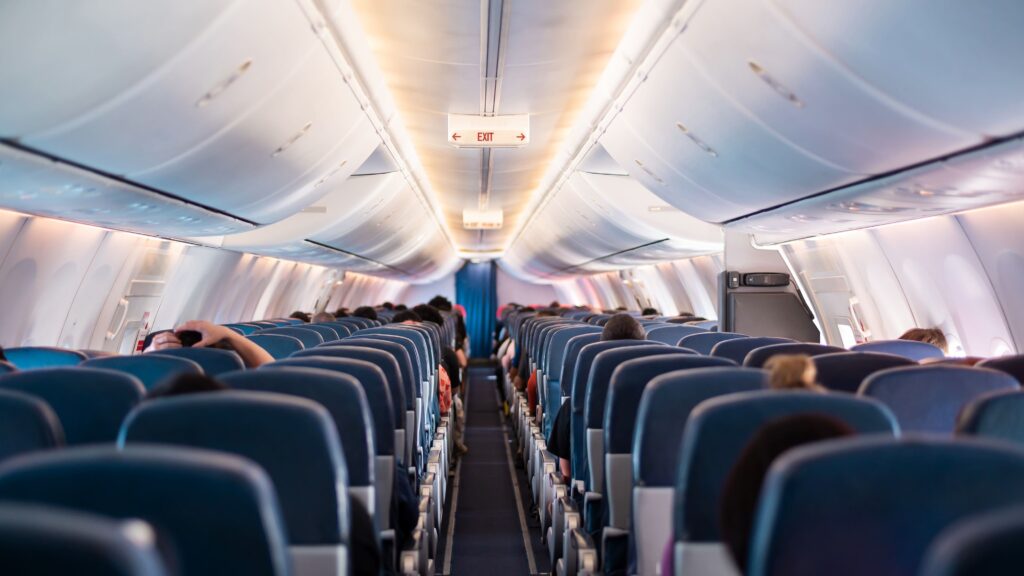
航空機産業では、燃費効率向上のための軽量化が永遠のテーマです。航空機の様々な部品で金属からPEEK製品への転換が進んでいます。特に内装部品、ブラケット、クリップなどの構造部品において、アルミニウム合金からPEEK複合材料への転換が進んでいます。業界報告によれば、ある航空機メーカーでは、キャビン内の結合部品をPEEK製に変更することで、部品重量を約40%削減し、燃費効率の向上に貢献しています。加えて、PEEKの優れた難燃性能と低煙発生特性が、航空安全基準への適合において重要な役割を果たしています。
医療機器における金属代替
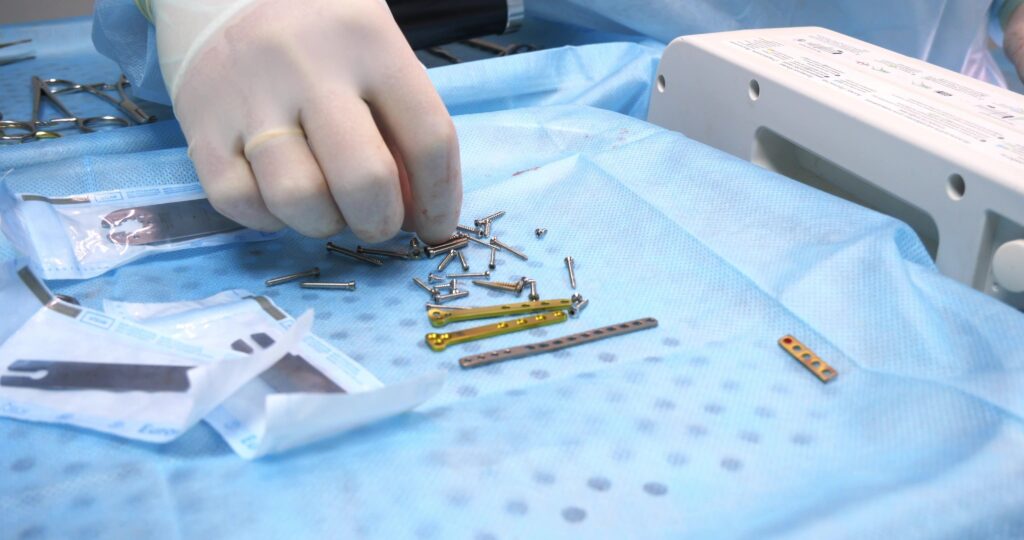
医療機器分野では、X線透過性と生体適合性を兼ね備えたPEEKが注目されています。整形外科用インプラントや手術器具において、ステンレス鋼やチタン合金からPEEKへの材料転換が進んでいます。例えば、脊椎固定用インプラントにおいては、PEEKの弾性率が骨に近いことから、金属インプラントよりも応力遮蔽(stress shielding)のリスクが低いという利点があります。また、MRIやCTスキャンなどの画像診断においても、PEEKはアーチファクト(画像の乱れ)を生じにくいという特長から採用が増えています。
半導体製造装置での採用例
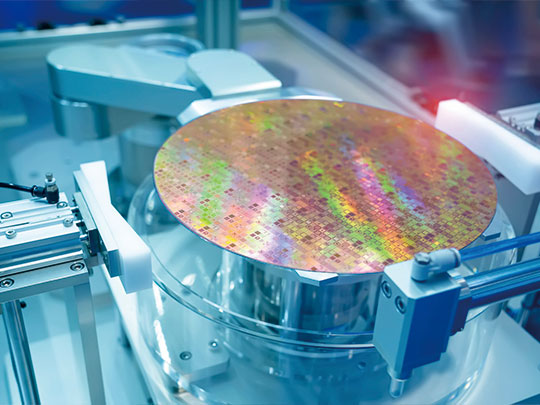
半導体製造環境では、耐熱性・耐薬品性・クリーン性が厳しく要求されます。業界では、ウエハー搬送用部品やチャンバー内使用部品の多くでPEEKが採用されています。あるウエハーハンドリングシステムでは、従来のステンレス製部品をPEEK製に置き換えることで、パーティクル(微粒子)発生を大幅に低減し、製造歩留まりの向上を実現したという報告があります。また、腐食性ガスを使用するエッチングプロセスにおいても、PEEK製の部品が高い耐食性を示し、メンテナンス頻度の低減に貢献しています。
当社のPEEK成形における強み
PEEKは極めて高い性能を持つ反面、成形加工においては高度な知識と設備、精密な条件管理が必要です。当社は長年にわたる高機能樹脂の成形実績を通じて、PEEKに最適化された技術と体制を確立してきました。以下に、当社が提供するPEEK成形における代表的な強みをご紹介します。
製品・金型デザインに関するノウハウ
PEEKは高剛性・高収縮・高温成形という特性を持ち、設計段階での適切な肉厚バランス、リブの配置、抜き勾配の確保などが成形安定性や寸法精度を大きく左右します。当社では、金型設計と製品デザインの両面からPEEKに特化したノウハウを蓄積しており、成形トラブルの原因となりやすいヒケ、反り、ウェルドラインを最小限に抑える構造設計を提案します。また、金型素材の選定や熱膨張を考慮した型割設計、精密な温調回路の構築にも対応しています。
最適な成形条件の設定
PEEKの成形温度は樹脂温度で370~400℃、金型温度は160~200℃が必要とされ、一般的な成形とは一線を画す高温条件での制御が求められます。当社では高温対応の専用成形機を導入し、温度プロファイルの緻密な設定により、安定した樹脂流動と高品質な充填を両立。加えて、滞留時間の最小化や加熱中の劣化防止を目的としたスクリュー選定・パージ管理も徹底し、初回トライから高い再現性を実現しています。
少量生産から量産まで柔軟な対応
PEEK部品は医療機器や電子・輸送機器など、少量多品種の需要が多い分野でも広く用いられています。当社では、試作段階の数十個から、数千~数万個規模の量産まで、ニーズに応じて柔軟に対応可能な生産体制を整えています。ロットサイズに関わらず高効率な供給が可能となっています。
品質保証体制
PEEK成形品は高負荷環境や高信頼性を求められる用途が多いため、厳格な品質管理が不可欠です。当社では必要に応じて画像検査装置による寸法・外観評価を実施します。さらに、原材料ロット・成形条件・検査記録まで一元的にトレース可能な管理システムを構築しており、万一のトラブル時にも迅速な原因分析と再発防止策を講じることが可能です。
PEEKと射出成形技術の将来展望
材料技術の進化と新たな可能性
PEEKは常に進化を続けており、最近では、ナノ複合材料技術の応用や、バイオベース由来のPEEK類似材料の開発も進んでいます。材料メーカーは新しいグレードの開発を続けており、より幅広い用途への適用が期待されています。
3Dプリンティングとの融合
高温対応の3Dプリンティング技術の発展により、PEEKを使用した積層造形も実用化されつつあります。射出成形技術と3Dプリンティング技術を組み合わせたハイブリッド製造の研究も進んでおり、より複雑な形状や機能を持つPEEK製品の開発が可能になりつつあります。
サステナビリティへの貢献
PEEKは長寿命で信頼性が高く、製品のライフサイクル全体で見ると環境負荷の低減に貢献します。成形工程で発生するランナーやスプルーの再利用や、使用済み製品のリサイクルプログラムも業界全体で推進されています。
新たな応用分野の開拓
再生可能エネルギー、水素関連技術、次世代モビリティなど、新たな成長分野においても、PEEKの特性を活かした部品開発が期待されています。特にクリーンエネルギー分野では、耐熱性・耐薬品性を活かした部品の需要が高まっています。
まとめ
PEEKは、その優れた特性から多くの産業分野で金属や他の樹脂の代替材料として注目を集めています。しかし、その特性を最大限に引き出すためには、適切な製品設計と高度な射出成形技術が不可欠です。当社は、射出成形のスペシャリストとして、材料特性の理解と加工技術の両面から、お客様のPEEKを原料とする射出成形部品の開発をサポートします。材料選定から量産までのトータルソリューションを提供し、製品の高機能化と製造効率向上に貢献します。高性能部品の開発や、金属からのPEEKへの置き換えをご検討の際は、ぜひ当社にご相談ください。お客様の課題に最適なソリューションを提案いたします。