キーエンス製3DプリンターAgilistaを活用したプラスチック製品開発
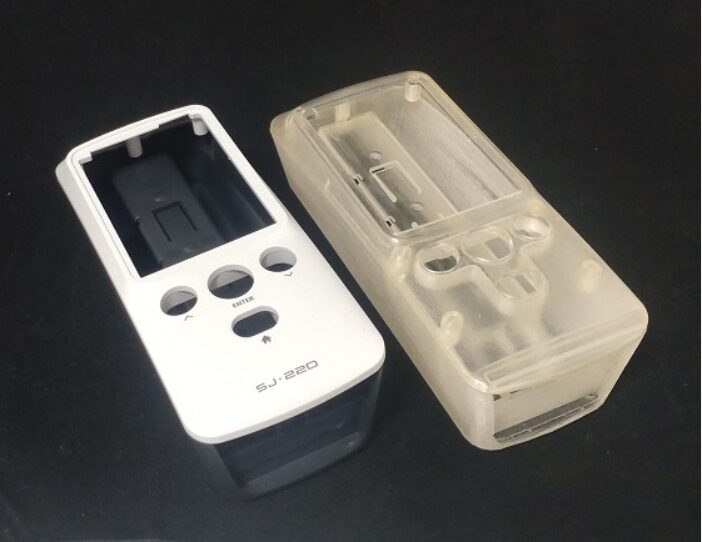
3Dプリンター技術は、製造業界に革命をもたらしています。従来の製造方法では実現が困難だった複雑な形状や、少量多品種生産を可能にし、製品開発のプロセスを大きく変革しています。
特に、試作品の製作や最終製品の製造において、3Dプリンターの活用は時間とコストの削減、そして品質向上に大きく貢献しています。当社では、この革新的な技術の最前線に立ち、お客様の製品開発を支援するため、キーエンス製3DプリンターAgilistaを導入しています。
Agilistaは、高精度かつ高速な造形能力を持ち、特にインクジェット方式を採用することで、細部まで精密な造形を実現します。本コラムでは、Agilistaの特徴と、それを活用した製品開発支援について詳しく解説します。
Agilistaの技術仕様と特長
Agilistaは、インクジェット方式を採用した3Dプリンターです。この方式の最大の特徴は、液状の樹脂を微細なノズルから吐出し、紫外線で硬化させながら積層していく点にあります。
高精細造形能力
Agilistaの最大の強みは、その高精細な造形能力です。最小15μmという極めて薄い層を積層することができ、これにより滑らかな表面仕上げと精密な形状再現が可能となります。この精度は、従来の3Dプリンターと比較しても群を抜いており、微細な部品や複雑な形状を持つ製品の試作に特に適しています。
水溶性サポート材の利点
Agilistaでは、造形物を支えるサポート材として水溶性の材料を使用しています。これにより、造形後のサポート除去が非常に容易になります。従来の3Dプリンターでは、サポート材の除去に時間と労力がかかり、時には造形物を傷つけてしまうリスクもありました。水溶性サポート材を使用することで、これらの問題が解決され、より複雑な内部構造を持つ部品の造形も可能になりました。
材料の特性
Agilistaで使用する材料は、半透明で靭性に優れています。半透明の樹脂を使用することで、内部構造の可視化や光学部品の試作が可能になります。また、靭性のある材料を使用することで、機械的強度が要求される部品の試作にも対応できます。これらの特性により、幅広い用途での活用が期待できます。
製品開発プロセスにおけるAgilistaの活用
Agilistaは、製品開発の様々な段階で活用することができ、開発プロセス全体の効率化に貢献します。
設計段階での迅速な試作
設計段階では、3DCADデータを直接Agilistaに送信し、短時間で実物の試作品を作製することができます。これにより、設計者はアイデアを素早く形にし、その妥当性を確認することができます。従来の試作方法と比較して、大幅な時間短縮とコスト削減が可能となります。
機能検証と改良サイクルの短縮
Agilistaで作製した試作品を用いて、実際の使用環境での機能検証を行うことができます。検証結果に基づいて設計を修正し、再度試作品を作製するというサイクルを、従来よりも短期間で繰り返すことが可能です。これにより、製品の完成度を高めながら、開発期間の短縮を実現できます。
組立性や操作性の事前確認
複数の部品から構成される製品の場合、各部品の組立性や操作性を事前に確認することが重要です。Agilistaを使用することで、実際の寸法や形状を持つ部品を作製し、組立や操作の問題点を早期に発見し、解決することができます。これにより、量産段階での手戻りを最小限に抑えることが可能となります。
金型製作前の最終確認
射出成形用の金型製作は、多大な時間とコストがかかります。Agilistaを使用して最終的な形状を確認することで、金型製作前の段階で問題点を洗い出し、修正することができます。これにより、金型の手直しや再製作のリスクを大幅に低減することができ、結果として開発コストの削減と納期短縮につながります。
当社の3Dプリンターによる製作事例のご紹介
計測器ハウジング
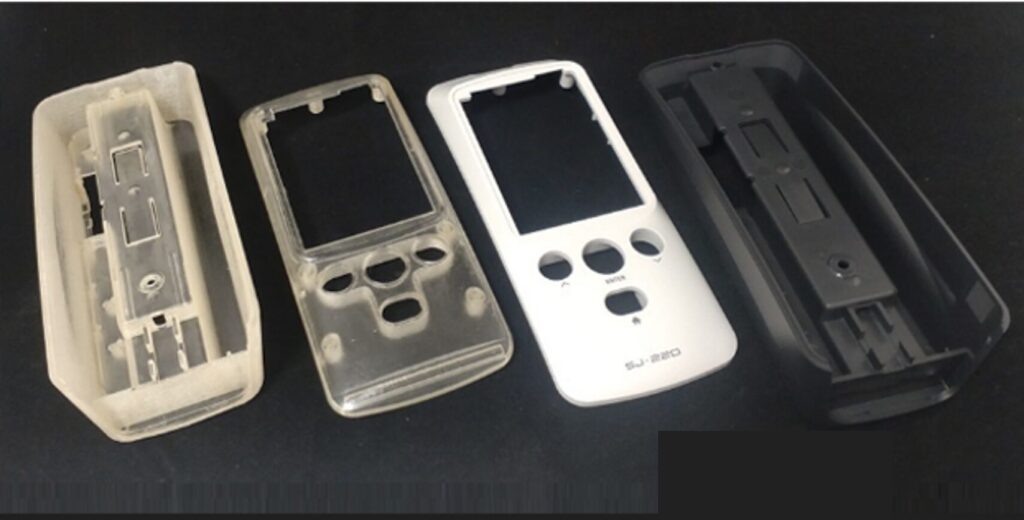
用途:ハウジング Upperカバー、Lowerカバー
サイズ:
Upperカバー 165mm×65mm×20mm
Lowerカバー 165mm×65mm×45mm
3Dプリンターでのサンプル作成の目的:
①内臓部品を組み込んでの動作確認(内部が確認できる半透明サンプル作成)
②設計・仕様の検証・確認
最終量産品は写真右側の2つになります。
Upperカバー材質:ASA
Lowerカバー材質:ABS
ポンプ接続部品
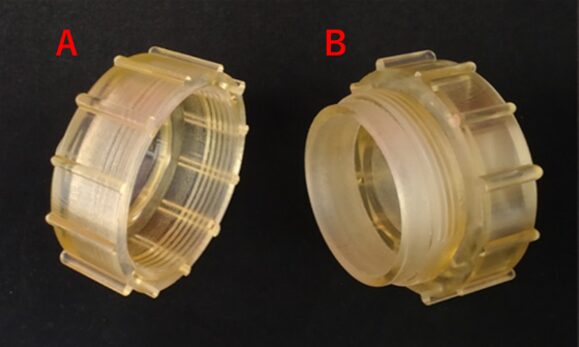
用途:流体制御機器用ポンプ接続部品(2部品)
サイズ:
部品A Φ90mm×H40mm
部品B Φ90mm×H60mm
3Dプリンターでのサンプル作成の目的:
①ネジの嵌合性確認
②A,B嵌合時の外周リブ位置確認(ネジスタート位置の確認)
③設計・仕様の検証・確認
従来の製造方法との比較
Agilistaを活用した製品開発は、従来の製造方法と比較して多くの利点があります。ここでは、射出成形と切削加工との比較を行います。
射出成形との比較
1.コスト面
射出成形は大量生産に適していますが、金型製作に多大なコストがかかります。一方、Agilistaは金型不要で少量生産が可能なため、初期投資を抑えることができます。特に、試作段階や少量多品種生産においては、Agilistaの方が圧倒的にコスト効率が高くなります。
2.リードタイム
射出成形では金型製作に数週間から数ヶ月かかることがありますが、Agilistaでは3DCADデータから直接造形できるため、数日で製品を得ることができます。この迅速性は、特に開発初期段階での試作や、市場ニーズの変化に対する迅速な対応に大きな利点となります。
3.形状の自由度
射出成形では、金型の構造上、製品形状に制約があります。例えば、アンダーカットや複雑な内部構造の実現が困難です。Agilistaではこれらの制約がなく、より自由度の高い設計が可能となります。
4.少量生産
射出成形は大量生産に適していますが、少量生産の場合はコスト面で不利になります。Agilistaは、生産数に関わらず一定のコストで製造できるため、少量生産や多品種少量生産に適しています。
切削加工との比較
1.複雑形状との比較
切削加工では、工具の干渉や機械の動作範囲の制限により、複雑な形状や内部構造の加工が困難な場合があります。Agilistaでは、これらの制限なく複雑な形状を一体成形で実現できます。
2.材料ロス
切削加工は材料を削り取って形状を作り出すため、材料のロスが大きくなります。Agilistaは積層造形のため、必要な部分にのみ材料を使用し、材料の無駄を最小限に抑えることができます。但し、部品の形状によっては、部品単価が切削加工の方が低コストにできる場合もあります。まずは当社にご相談下さい。
3.工程の簡略化
切削加工では、複雑な形状を実現するために複数の工程や治具が必要になることがあります。Agilistaでは、3DCADデータから直接造形するため、工程が大幅に簡略化されます。
4.軽量化設計
切削加工では、材料の強度を確保するために必要以上に厚みを持たせる必要がある場合があります。Agilistaでは、内部に複雑な構造を持たせることで、強度を保ちながら軽量化を図ることができます。
Agilista活用のメリットとデメリット
メリット
1.開発期間の短縮
Agilistaを使用することで、設計から試作、評価までのサイクルを大幅に短縮することができます。従来の方法では数週間かかっていた試作品の製作が、数時間から数日で完了することで、製品開発のスピードが飛躍的に向上します。
2.コスト削減効果
金型製作や専用の治具作製が不要になるため、特に少量生産や試作段階でのコスト削減効果が顕著です。また、設計変更に伴う追加コストも最小限に抑えることができます。
3.品質向上への貢献
高精度な造形能力により、設計意図を忠実に再現した試作品を作製できます。これにより、設計段階での問題点の早期発見や、より精密な機能検証が可能となり、最終製品の品質向上に貢献します。
4.設計の自由度向上
従来の製造方法では実現が困難だった複雑な形状や内部構造を持つ部品の製作が可能になります。これにより、製品の機能性や付加価値を高める革新的な設計が実現できます。
5.環境負荷の低減
必要な部分にのみ材料を使用する積層造形方式により、材料の無駄を最小限に抑えることができます。また、金型製作が不要なため、金型製作に伴う環境負荷も削減できます。
デメリット
1.材料の制限
Agilistaで使用できる材料はアクリル系の光硬化性樹脂であり、全ての製品に適用できるわけではありません。特に、高強度や特殊な物性が要求される部品の場合、適用が難しい場合があります。
2.大量生産性
Agilistaは少量生産に適していますが、大量生産の場合は射出成形などの従来の製造方法の方がコスト効率が高くなります。生産数量に応じて、適切な製造方法を選択する必要があります。
3.表面品質
積層造形の特性上、表面に層の跡が残る場合があります。高い表面品質が要求される部品では、後処理が必要になることがあります。
4.サイズの制限
Agilistaの造形サイズには制限があるため、大型の部品を一体で製作することはできません。大きな部品は分割して造形し、後で組み立てる必要があります。
5.大量生産の場合のコスト
材料コストが従来の樹脂材料と比較して高価であるため、大量生産時にはコスト面で不利になる場合があります。
6.長期耐久性の不確実性
3Dプリント製品の長期耐久性については、まだ十分なデータが蓄積されていない面があります。特に、応力がかかる部品や長期使用が想定される部品では、慎重な評価が必要です。
今後の展望と可能性
Agilistaを含む3Dプリンター技術は、急速に進化を続けています。今後、さらなる技術革新や新たな応用分野の開拓が期待されます。
新素材開発との連携
3Dプリンター用の新素材開発が活発に行われており、より高機能な材料や特殊な物性を持つ材料の登場が期待されています。例えば、高強度、高耐熱性、生体適合性などの特性を持つ材料が開発されれば、Agilistaの適用範囲が大きく広がる可能性があります。
IoTやAIとの統合による更なる効率化
3DプリンターとIoT技術を組み合わせることで、遠隔地からの造形指示や、造形状況のリアルタイムモニタリングが可能になります。また、AIを活用することで、最適な造形パラメータの自動設定や、設計段階での最適化提案など、さらなる効率化が期待できます。
最終製品への適用可能性
現在、Agilistaは主に試作品製作に使用されていますが、材料や造形技術の進歩により、最終製品への適用可能性も広がっています。特に、カスタマイズ製品や少量多品種生産の分野では、3Dプリンターの活用が進むと予想されます。
サステナビリティへの貢献
3Dプリンター技術は、必要な量だけ材料を使用し、地域での生産を可能にすることから、サステナビリティの観点からも注目されています。輸送コストの削減や、在庫管理の最適化など、環境負荷の低減に貢献する可能性があります。
医療分野での応用
医療分野では、患者個々の体型に合わせたカスタムメイドの医療機器や、人工臓器の製作など、3Dプリンター技術の応用が進んでいます。Agilistaの高精度造形能力は、これらの分野での活用が期待されます。
まとめ
キーエンス製3DプリンターAgilistaは、その高精度な造形能力と使いやすさにより、製品開発プロセスに革新をもたらす強力なツールです。当社がAgilistaを導入したことで、お客様の製品開発支援において、以下のような価値を提供することが可能になりました。
開発期間の大幅な短縮
設計から試作、評価までのサイクルを従来の数週間から数日へと短縮し、製品の市場投入までの時間を大幅に削減できます。
コスト効率の向上
金型製作や専用治具の作製が不要になり、特に少量生産や試作段階でのコスト削減効果が顕著です。また、設計変更に伴う追加コストも最小限に抑えることができます。
設計の自由度の向上
従来の製造方法では実現困難だった複雑な形状や内部構造を持つ部品の製作が可能となり、製品の機能性や付加価値を高める革新的な設計を実現できます。
品質向上への貢献
高精度な造形能力により、設計意図を忠実に再現した試作品を作製でき、設計段階での問題点の早期発見や、より精密な機能検証が可能となります。
環境負荷の低減
必要な部分にのみ材料を使用する積層造形方式により、材料の無駄を最小限に抑え、環境に配慮した製品開発を支援します。
当社は、Agilistaの特性を最大限に活用し、お客様の製品開発における課題解決を支援いたします。設計段階からの綿密な打ち合わせ、最適な造形方法の提案、試作品の評価サポートなど、製品開発の各段階で専門的なサポートを提供いたします。
また、Agilistaの活用に加え、当社の射出成形技術や切削加工技術と組み合わせることで、試作から量産まで一貫したサポートが可能です。お客様のニーズに応じて、最適な製造方法を選択し、高品質な製品を効率的に開発・生産するためのトータルソリューションを提供いたします。3Dプリンター技術は日々進化しており、当社も常に最新の技術動向をキャッチアップし、お客様に最適なソリューションを提案できるよう努めています。
新素材の開発やIoT、AI技術との統合など、今後の技術革新にも積極的に対応し、さらなる製品開発支援の高度化を目指してまいります。製品開発におけるスピード、コスト、品質の向上をお求めの方は、ぜひ当社のAgilista活用サービスをご検討ください。お客様の革新的なアイデアを、最先端の3Dプリンター技術で形にする、そんな製品開発の新しいカタチを、当社は全力でサポートいたします。