その設計、コスト上がってませんか?射出成形における「抜き勾配」と「アンダーカット」処理の重要性
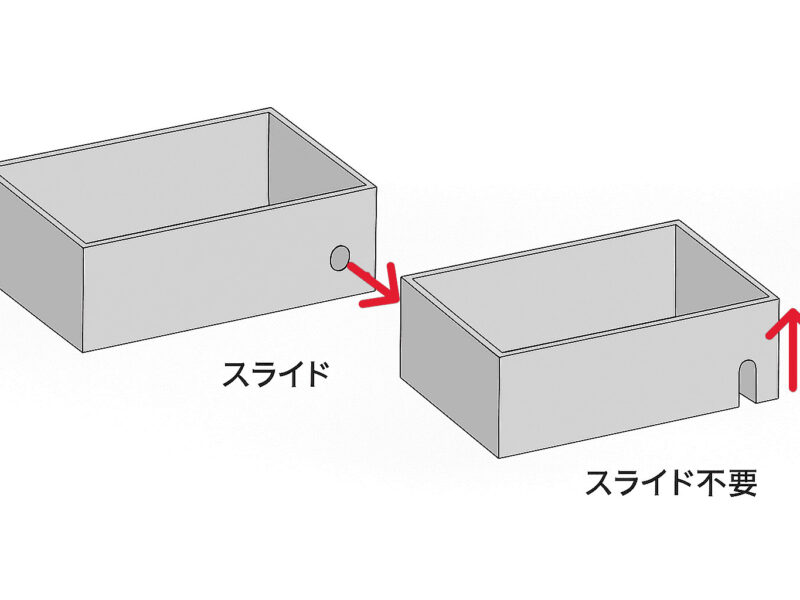
プラスチック製品の開発において、「製品の機能は満たしているのに、金型費の見積もりが想定を大幅に超えてしまった」という経験はありませんか?その原因は、製品設計のわずかな形状、特に「抜き勾配」の有無と「アンダーカット」の処理方法にあるかもしれません。
射出成形は、金型に樹脂を流し込み、冷やし固めて製品を取り出す、というシンプルな工程です。しかし、この「取り出す」というプロセスをいかにスムーズに行えるかが、金型の構造、ひいてはコストと品質を大きく左右します。
本コラムでは、射出成形における金型コストの鍵を握る「抜き勾配」と「アンダーカット」に焦点を当てます。これらの基本を理解し、設計段階で適切に処理することが、いかにコスト削減に繋がるのか。そして、設計の工夫でアンダーカットを回避する具体的なアイデアまで、詳しく解説していきます。
なぜ「抜き勾配」と「アンダーカット」が金型費に直結するのか
製品設計の段階で、この2つの要素を考慮しているかどうかで、金型費用には数十万、時には百万円単位の差が生まれることもあります。まずは、それぞれの役割とコストへの影響を理解しましょう。
抜き勾配の必要性
<抜き勾配とは何か?>
抜き勾配とは、成形品を金型からスムーズに取り出すために、金型の抜き方向に対して設けるわずかな傾斜のことです。一見すると垂直に見える製品の側面も、実際には1°や2°といった微かな角度が付けられています。この「わずかな傾斜」が、成形プロセスにおいて極めて重要な役割を果たします。
<抜き勾配がない場合の成形トラブル>
もし、設計者が抜き勾配を全くつけず、「完全な垂直な壁」を持つ製品を設計したらどうなるでしょうか。溶融した樹脂は金型内で冷却・固化する際に必ず体積が収縮し、金型(特にコアと呼ばれる凸側)に強く密着します。抜き勾配がないと、製品の側面全体が金型と接触したまま突き出されることになり、非常に大きな摩擦力(離型抵抗)が発生します。その結果、以下のような深刻な成形トラブルを引き起こします。
製品表面のカジリ・擦り傷:大きな抵抗に逆らって無理やり突き出すため、製品の側面が金型に擦れて深い傷がついてしまいます。これは外観不良として致命的です。
エジェクターピン跡の白化・変形:製品を突き出すエジェクターピンが当たる部分に過大な力が集中し、その部分が白く変色したり(白化)、凹んだり、ひどい場合はピンが製品を突き破ってしまったりします。
製品全体の変形・破損:製品全体に無理な力がかかるため、意図しない反りやねじれといった変形、あるいは薄いリブや壁の破損に繋がります。
<抜き勾配が適切に設計されていることのメリット>
逆に、適切な抜き勾配が設計に織り込まれていると、単に不良を防ぐだけでなく、多くのメリットが生まれます。
成形サイクルの短縮と生産性向上:製品がスムーズに金型から離れるため、突き出しにかかる時間が短縮されます。この数秒の差が、大量生産においては大きな生産性向上に繋がり、製品単価の低減に貢献します。
金型寿命の延長:金型への物理的な負荷が大幅に軽減されるため、摩耗や損傷が起こりにくくなります。これは金型のメンテナンス頻度を下げ、長期的に見て金型の寿命を延ばすことにつながります。
安定した品質の確保:擦り傷や変形のない、均一で安定した品質の製品を継続的に生産できるようになります。
このように、抜き勾配は射出成形における「基本中の基本」であり、コストと品質を担保するための不可欠な設計要件なのです。
アンダーカット処理のコスト影響
<アンダーカットとは何か?>
アンダーカットとは、金型を単純に開閉するだけでは取り出せない「引っかかり」部分を持つ形状のことです。例えば、製品の側面にある横穴や凹み、内側を向いたフック形状などがこれに該当します。金型が開く方向(抜き方向)に対して、影になる部分と考えてもよいでしょう。
このアンダーカット形状を成形するためには、金型に特殊な機構を追加する必要があります。その代表的なものが「スライドコア」です。これは、金型が開く前に、油圧や機械的な仕組みで横方向や斜め方向に動き、「引っかかり」部分を製品から退避させるための可動部品です。
<アンダーカットが金型設計に与える影響>
製品図面にアンダーカットが1つ存在するだけで、金型設計は飛躍的に複雑化します。スライドコア本体だけでなく、それを動かすための油圧シリンダーや傾斜したピン、可動部を正確に位置決めし支えるためのガイドレールなど、多くの追加部品が必要になります。そして、これらの複雑な部品を一つひとつ精密に加工し、高温高圧の環境下でスムーズに、かつ正確に動くように調整するには、膨大な時間と高い技術力が求められます。
<金型費用が高くなる理由>
アンダーカット処理は、なぜこれほど金型費用を押し上げるのでしょうか。理由は複合的です。
部品点数増加による直接的なコストアップ:スライド機構を構成する部品そのものの材料費と、複雑な形状を削り出すための加工費が純粋に上乗せされます。一般的に、スライド機構が1箇所増えるごとに、金型費用は10%~30%増加するのが一般的であり、これが最も直接的なコストアップの要因です。
メンテナンスコストと故障リスクの増大:金型は消耗品であり、特にスライドのような可動部は摩耗しやすく、定期的なメンテナンスや部品交換が不可欠です。構造が複雑なほどメンテナンスの手間とコストは増大し、万が一故障した際の修理費用や生産停止による機会損失も大きくなります。
成形不良リスクの増加:スライドコアの合わせ面(パーティングライン)から樹脂が漏れ出て「バリ」が発生したり、スライドの動きが悪くなって製品を傷つけたりと、新たな成形不良の原因を生み出します。これにより製品の歩留まりが低下し、結果的にトータルコストを圧迫することになります。
つまり、アンダーカットは金型のイニシャルコストだけでなく、将来にわたるランニングコストや品質リスクまでをも増大させる、非常に「高価な」形状なのです。
設計の工夫で金型費は下げられる
アンダーカットは、本当にその製品に不可欠でしょうか?実は、設計の工夫次第で、機能を損なうことなくアンダーカットを回避できるケースは数多く存在します。コストを意識した設計者は、アンダーカット形状を見つけると「これをなくせないか?」と考える習慣を持っています。
アンダーカット回避の設計変更アイデア
ここでは、代表的なアンダーカット回避のアイデアをいくつかご紹介します。これらは、ほんのわずかな発想の転換で、大きなコスト削減効果を生む可能性があります。
アイデア①:穴や凹みを「逃げ」形状に変更する
ケーススタディとして、筐体の側面にケーブルを通すための「丸穴」を考えてみましょう。この丸穴は典型的なアンダーカットです。しかし、もしその機能が「ケーブルを通すこと」だけであり、完全に閉じた穴である必要がない場合、穴の形状を金型のパーティングライン(金型の分割面)まで貫通するU字型の溝(スリット)に変更できないでしょうか。この変更により、横方向に動くスライドコアは不要になり、単純な金型の開閉だけで成形可能になります。
アイデア②:製品を分割し、後工程で組み立てる
複雑な内外構造を持つ製品で、どうしてもアンダーカットが生じてしまう場合があります。このような場合、製品を2つ以上のシンプルな部品に分割して設計し、それぞれをアンダーカットのない金型で成形した後、超音波溶着やネジ留めなどで組み立てるというアプローチが有効です。一見、金型が2つ必要になるためコストアップに思えるかもしれませんが、複雑なスライド機構を持つ1つの高価な金型よりも、シンプルな2つの金型の方がトータルコストを抑えることができることもあります。
アイデア③:材料の弾性を利用した「無理抜き」を活用する
電池蓋などを固定するための爪(フック)形状も、一般的なアンダーカットです。しかし、PPやPOMのような弾性の高い材料を使用する場合、爪の形状や根元の肉厚を適切に設計することで、材料の「しなり」を利用して金型から強制的に引き抜く「無理抜き」が可能な場合があります。これはスナップフィットの考え方を応用したもので、スライド機構をなくせる非常に効果的なテクニックですが、高度なノウハウが求められます。
アイデア④:パーティングラインの位置を見直す
ある形状がアンダーカットになるかどうかは、金型のパーティングラインをどこに設定するかで決まります。製品の外観や機能に影響のない範囲でパーティングラインの位置を変更することで、アンダーカットそのものを解消できる場合があります。これは金型構造の深い理解が必要ですが、最もスマートな解決策の一つです。
これらの設計変更は、製品の要求仕様を満たしつつ、製造コストを劇的に下げる可能性を秘めています。
府中プラが提案する「コストを抑える設計」
ここまで見てきたように、抜き勾配やアンダーカットの処理は、製品のコストと品質に絶大な影響を与えます。そして最も重要なのは、これらの検討は設計が固まってからでは手遅れになるということです。
製品設計者が「この形状は、金型でどうやって作るのだろうか?」という製造現場の視点を持つことが、コスト競争力のある製品を生み出すための第一歩です。しかし、製品設計者が金型の詳細な構造や、材料ごとの特性、成形条件まで、すべてを把握するのは極めて困難です。そこで、府中プラの出番です。府中プラは、単にお客様の図面通りに金型を作り、成形するだけではありません。射出成形と金型のプロとして下記のようなご支援をさせていただきます。
量産性のレビュー:お客様の設計図面を拝見し、抜き勾配は適切か、不要なアンダーカットは存在しないか、より効率的な製造方法はないか、といった観点から詳細なレビューを行います。
コスト削減の提案: 先述したようなアンダーカット回避のアイデアをはじめ、材料選定や肉厚の最適化など、品質を維持・向上させながらトータルコストを削減するための具体的な設計変更案をご提案します。
CAE解析による事前検証: 必要に応じて流動解析などを行い、設計変更による樹脂の流れや反りの影響を事前にシミュレーションすることで、手戻りのない確実な製品開発をサポートします。
設計が完了し、複数の金型メーカーに見積もりを取ってからコストの問題に直面するのでは、貴重な時間と開発費を無駄にしてしまいます。その前に、ぜひ一度府中プラにご相談ください。
まとめ
射出成形におけるコスト削減の鍵は、設計の初期段階にあります。抜き勾配を徹底し、高コストの原因となるアンダーカットを設計の工夫で回避すること。この2点を意識するだけで、金型費は大きく変わります。製造性を考慮した設計こそが、競争力のある製品開発の第一歩です。当社は、これまで3,000型を優に超える金型の受注を通じてノウハウを蓄積してきました。どんな些細なことでも構いません。部品設計でご不明な点等ございましたら、何なりと当社までご相談ください。