複雑形状はスライドコアが鍵:金型構造の工夫とトラブル予防の考え方
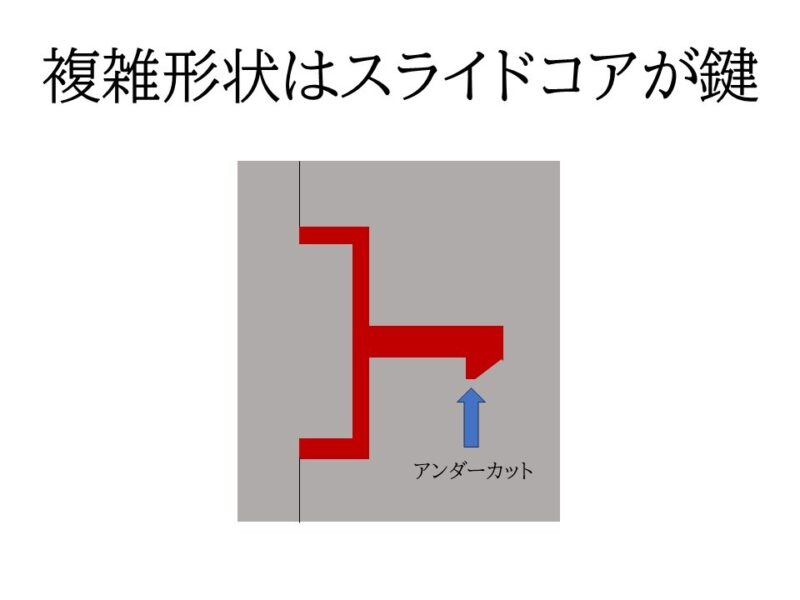
射出成形において、複雑な形状やアンダーカットを持つ製品を実現するために、スライドコアは不可欠な存在です。しかし、その強力な機能性ゆえに、安易な採用や設計上の配慮不足は、金型トラブルの頻発、成形品質の不安定化、そして最終的には製造コストの増大という深刻な問題を引き起こします。本コラムでは、スライドコアを効果的に活用しつつ、金型構造全体の合理化と長期的なトラブル予防を両立させるための、実務に即した設計の考え方を解説します。
スライドコアの役割と金型構造全体への影響
スライドコアの役割はアンダーカットの成形に留まりません。その存在は金型全体の機能や構造、コストに至るまで多角的な影響を及ぼすため、採用には俯瞰的な視点が求められます。
スライドコアの最も基本的な役割は、金型の開閉方向だけでは成形できないアンダーカット形状(製品側面の穴や凹凸など)を作り出すことです。しかし、その機能は単に形状を創出するだけに留まりません。アンダーカット対応以外にも、設計者の意図次第で副次的な効果を発揮します。例えば、スライドコアと主型との合わせ面は、意図的なクリアランス設定により、成形時に発生するガスを排出する「ガスベント」として機能させることが可能です。これにより、ガス焼けやショートショットといった成形不良の抑制に貢献します。また、充填完了後にコアをわずかに前進させる「部分加圧」で局所的なヒケを抑制したり、スライド側にゲートを設けて製品外観やゲート処理の自由度を高めたりすることもできます。このように、スライドコアは品質向上に貢献する戦略的な要素となり得るのです。
一方で、スライドコアの存在は、金型構造全体に大きな制約とリスクをもたらします。スライドが移動するための十分な移動距離(ストローク)を確保するため、金型全体の厚みが増し、より大きな型開き能力を持つ成形機が必要になることがあります。また、重量のあるスライドが偏って配置されると、型締時の力のバランスが崩れ、パーティング面の片当たり、ガイドピンの異常摩耗、バリ発生や金型破損を招きます。
さらに深刻なのが、冷却系との相互干渉です。金型内部には、製品を均一に冷却するための回路が張り巡らされていますが、スライド機構のスペースがこの冷却回路の自由な配置を阻害します。結果として冷却ムラが生じると、製品の反りや寸法不良、成形サイクルの延長を招き、生産性を低下させます。当然ながら、スライドコアの数やサイズは、金型コストと耐久性にも直結します。精密加工が必要な摺動部品が増えれば、材料費、加工費、組立調整工数が必然的に増加し、可動部が増えることは摩耗や破損のリスク増大を意味するのです。
スライドコア起因のトラブル実例と設計対策
スライドコアは、金型におけるトラブル発生の主要因の一つです。ここでは、現場で頻発するトラブルと、それを未然に防ぐための設計上の対策を具体的に解説します。
スライドコアの代表的なトラブルが、摺動部の「焼き付き」や「かじり」といった動作不良です。潤滑不足が直接の原因ですが、その背景には成形熱によるコアの膨張や、樹脂から発生するガス・微細なバリの侵入による潤滑剤の劣化があります。これらの動作不良を防ぐには、まず設計段階で、使用樹脂や成形温度を考慮した適切なクリアランスを設定することが基本です。その上で、摺動部へのガス侵入を最小限に抑えるため、ガスベントの位置を最適化するなどの配慮が求められます。
次に深刻なのが、バリ発生とパーティング不良です。スライドコアと主型との合わせ面は、事実上のパーティングラインです。成形時の高い射出圧力でスライドコアが僅かに後退したり傾いたりすると、合わせ面に隙間が生じ、バリとなります。この問題を解決するには、スライドコアを強固に固定する設計思想が不可欠です。スライドコアの背面を主型で受ける「当たり面」を設けたり、特に高圧がかかる場合は、型締力を利用してくさび状に締め付ける「テーパーロック」構造が極めて有効です。もちろん、大前提として、ミクロン単位で管理された合わせ面の加工精度が、安定した品質の鍵となります。
スライド機構の摩耗や破損は、交換コストと生産停止(ダウンタイム)に直結します。そのため、各部品の役割に応じた材質や表面処理の選定が金型の耐久性を大きく左右します。例えば、頻繁に摺動するガイド部には耐摩耗性に優れた工具鋼(SKD61など)に窒化処理やDLCコーティングを、衝撃が加わるアンギュラピンには靭性も備えた材質を選ぶなど、製品の総生産数量や予算とのバランスを考慮した費用対効果の観点からの判断が必要です。
また、トラブルは事後対応ではなく予防が理想であり、設計段階からメンテナンス性を織り込む必要があります。例えば、スライド機構をユニット化し、金型を成形機に搭載したままでも交換できる構造にしておけば、トラブル時のダウンタイムを最小限に抑えられます。潤滑剤の給油口を外部からアクセスしやすい位置に設けたり、摩耗が避けられない摺動面に「ウェアプレート」と呼ばれる交換可能な板を取り付けたりする工夫も有効です。こうした配慮が、長期的な安定稼働と生産性向上に貢献します。
スライドコアの摺動部は、摩耗や焼き付きといったトラブルが発生しやすい箇所であり、設計段階での対策が不可欠です。
複雑形状対応におけるスライドコア設計の合理化アプローチ
複雑形状への対応とはいえ、安易なスライドの採用は避けるべきです。優れた金型設計とは、必要最小限の機構で目的を達成することにあります。
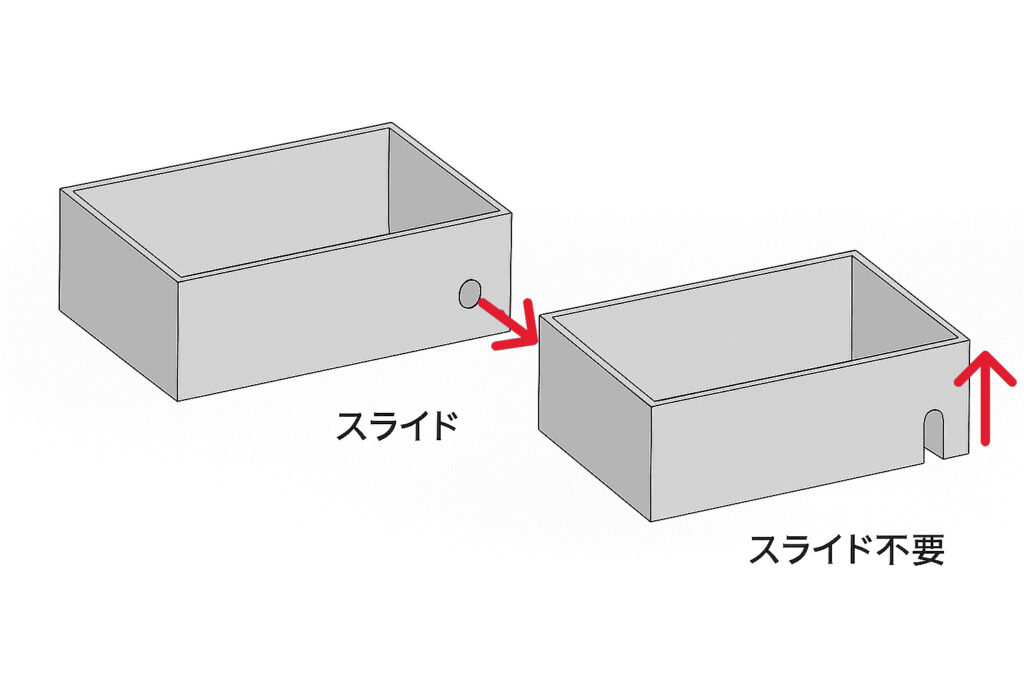
全ての議論の出発点となるのが、「アンダーカットの必要性を再検証する」という思考習慣です。金型設計者は、提示された図面をただ実現するだけでなく、製品設計の意図を汲み取り「このアンダーカット形状は、製品機能上、本当に不可欠か?」と問いかけることが重要です。製品設計者と協働し、スナップフィットの形状をアンダーカットにならないタイプに変更したり、側面の穴をテーパー状の貫通穴に変更したりすることで、金型構造を劇的に簡素化できる可能性は常に存在します。この「形状の工夫によるスライド削減」は、コスト、品質、納期全てにおいて最も効果的な合理化アプローチです。
それでもなおスライドが必要な場合でも、パーティングライン(PL)の工夫でスライドを減らせる可能性があります。PLを製品形状に沿って段差状や曲面状に設定する「インクラインPL」や「曲面PL」を用いることで、本来アンダーカットとなる形状を主型で直接成形できる場合があります。この「割り方の妙」は、高度なCAD活用能力、金型構造への深い知見、柔軟な発想力が求められ、金型の信頼性とコスト競争力を飛躍的に向上させます。
スライドコアが必要と判断された場合、次に「スライド数と駆動方式の最適選択」を検討します。駆動方式には、金型開閉に連動する「アンギュラピン方式」と、油圧などを用いる「シリンダー方式」があります。アンギュラピン方式はコストを抑えやすいですがストローク長に限界があり、シリンダー方式は駆動力やストロークの自由度が高いですが構造が複雑で高コストです。必要なストローク、駆動力、金型サイズ、成形サイクルなどを総合的に勘案して最適な方式を選定します。
最後に、スライドの配置と、金型全体の強度や冷却設計との「整合性確保」です。スライドコアの設置は、いわば金型という鋼の塊に大きな穴を空ける行為に等しく、その部分の剛性を著しく低下させます。特に大型のスライドを配置する場合は、FEM解析による強度検証やリブ構造による補強が不可欠です。また、スライド機構は冷却回路の配置を妨げるため、スライドコア自体の冷却と、周辺の主型の温度が均一になるような冷却回路全体の最適化が求められます。この整合性を欠いた設計は、サイクル遅延や品質不良に直結します。
まとめ
スライドコアは、単なるアンダーカット対応のための局所的な装置ではなく、金型全体の設計、製品品質、量産性にまで深く関わる戦略的な要素です。その設計の巧拙は、以下のような重要な要素すべてに直結します。
- 製品の外観品質と寸法安定性
- 成形サイクルと生産効率
- 金型自体の強度と耐久性
- 成形不良(バリ、焼き付き、反り、ヒケ)の発生リスク
- メンテナンス性とトータルコスト
これらの観点を総合的に見据え、「必要最小限のスライド設計」と「金型全体の構造バランス確保」を徹底することが、製品競争力を高め、トラブルを未然に防ぐ最短ルートです。
府中プラでは、これまでに3,000型を超える金型製作実績を通じて、スライドコアを含む複雑形状対応金型の設計・製作ノウハウを蓄積してきました。製品設計段階からの構造見直しや、スライド数・駆動方式・配置の最適化、さらに量産性・メンテナンス性までを視野に入れたご提案が可能です。