射出成形におけるバリの原因と対策
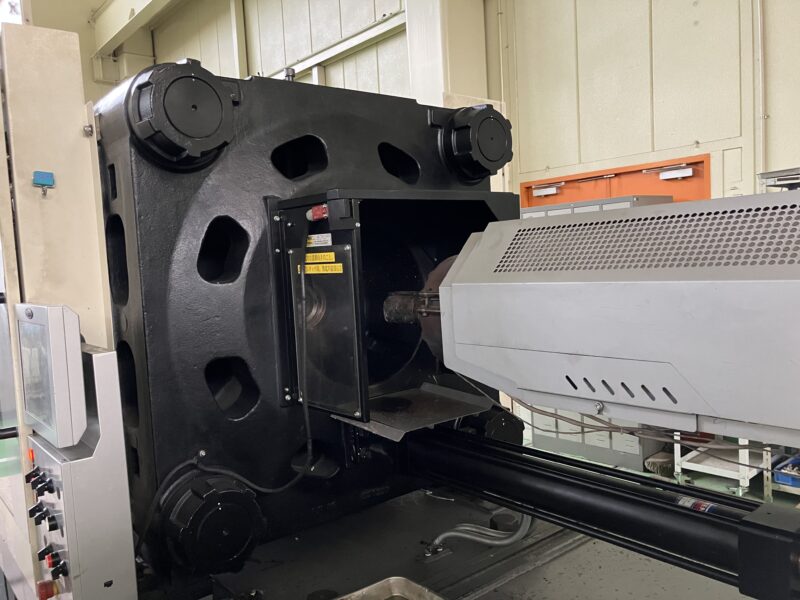
バリは、射出成形において成形品の表面に生じる、樹脂が本来の形状以上に流れた結果として発生する不良を指します。これは、樹脂の流動性が高すぎるため、成形品の形状を超えて流れ込むことで発生します。具体的には、金型の合わせ面(パーティングライン)や突き出しピンなどの隙間から溶融樹脂が溢れ出て固化した、成形品の形状からはみ出した部分を指します。
バリは主にキャビコアの合わせ面や金型部品の境界、スライド入れ子の摺動部、ゲート周辺、ランナーやダルマピンの周囲で発生します。発生要因としては、過充填や金型の消耗、金型の取り扱い不良、複雑な金型構造、成形条件の不適切さなどがあります。特に過剰な充填圧力や保圧が原因となることが多く、金型の摩耗や損傷も影響を与えます。
バリの発生は成形後のバリ取り作業を必要とし、生産リードタイムの延長とコスト増加を招きます。手作業によるバリ取りは時間と労力を要し、作業中に成形品を傷つける可能性もあります。バリは製品の外観と機能性に影響を与え、特に精密部品では寸法精度の低下や性能劣化を引き起こす可能性があります。そのため、バリ防止対策は製品品質の向上とコスト削減において極めて重要です。
バリの発生原因
バリの発生原因は、大きく分けて成形条件、金型設計、材料特性の3つの要因に分類されます。それぞれの要因について詳しく解説します。
成形条件に起因する要因
樹脂温度の高さ
樹脂温度が高すぎると、流動性が高まり、バリが発生します。特に、バレル温度が高すぎるとこの現象が顕著です。
圧力の高さ
圧力が高すぎると、樹脂が過度に流動し、バリが発生します。適切な圧力を設定することでバリを防ぎます。
射出速度の速さ
射出速度が速すぎると、樹脂が過度に流動し、バリが発生します。
不適切な型締め力設定
射出圧に対し型締め力が不足していると金型に隙間が生じ、バリが発生します。
金型設計に起因する要因
キャビコアの合わせ面(パーティングライン)
射出成形の繰り返しにより、パーティングライン付近の金型表面が徐々に摩耗し、微細な凹凸や隙間が生じます。また、金型の開閉を繰り返すことで、合わせ面の平面度が低下することもあり、これらの要因により、本来密閉されるべきパーティングラインに隙間が生じ、そこから樹脂が漏れ出してバリとなります。
金型部品の境界
複雑な形状の成形品を作るには、それに対応する複雑な構造の金型が必要となり、一般的に、金型は母型(おもがた)と呼ばれる金型本体に、複数のパーツがはめ込まれた入れ子構造となっています。入れ子と入れ子の合わせ目がバリの発生ポイントになりやすいです。
(入れ子とは、金型に後付けする製品の形状になる型のことです。)
スライド入れ子の摺動部
スライド入れ子の摺動部でバリが発生する主な原因は、クリアランス(隙間)の消耗とガタつきです。射出成形を繰り返すことで、スライド入れ子と可動側入れ子の摺動面が摩耗し、当初設定されていたクリアランスが広がっていきます。この摩耗は累積ショット数が増えるほど顕著になり、特に長期間の使用では隙間が拡大し、樹脂がその隙間に入り込みバリとなります。
サポートピラーの不適切な配置・設計
中心部から離れた配置では型板中心のたわみを効果的に防止できず、PLバリのリスクが増加します。また不十分な長さでスペーサーブロックより著しく短いと、型板のたわみを抑制できず、射出圧力による型開きでバリが発生します。
材料特性に起因する要因
材料の流動性
流動性が高すぎる材料はバリを引き起こしやすくなります。例えば、PPSやLCPは高流動性を持つため、バリが発生しやすい材料です。
材料の粘度
粘度が低すぎると流動が安定せず、バリが生じます。適切な粘度を持つ材料を選ぶことが重要です。
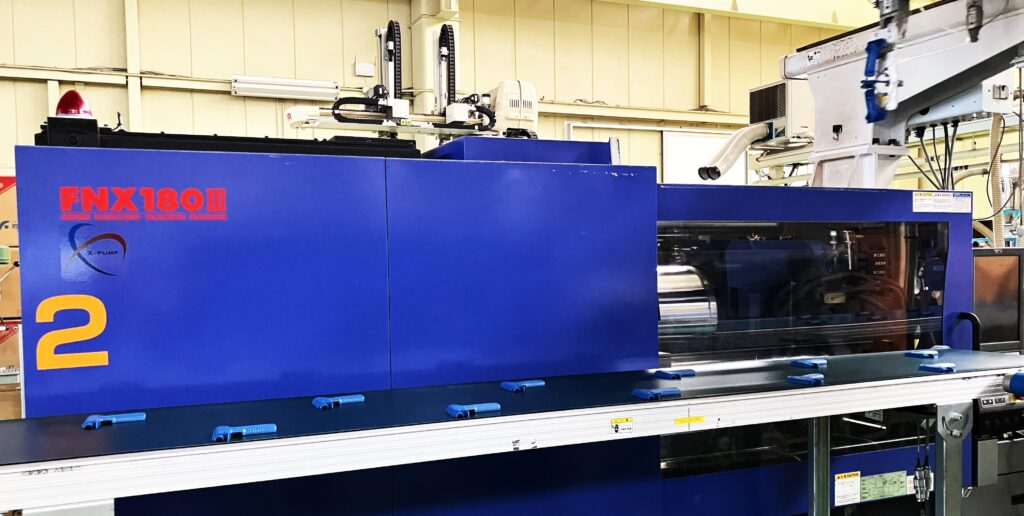
バリの発生を防止する対策
バリを防止するためには、成形条件の最適化、金型設計の改善、材料特性の工夫が重要です。
成形条件の最適化
樹脂温度の調整
樹脂温度を適切に設定し、流動性を抑えます。特に、バレル温度を材料の推奨範囲内で設定することが重要です。
圧力の調整
圧力を適正に設定し、過度の流動を防ぎます。一般的に、圧力を低下させることでバリを防ぎます。また、保圧力を多段階で設定し、ゲートにかかる圧力を適切に制御することも効果的です。
射出速度の調整
射出速度を適切に設定し、過度の流動を防ぎます。
適切な型締め力設定
射出圧に対し適切に型締め力を高くします。MAX値でも発生する場合は他の要因になります。
F: 必要型締力 (tf) p: キャビティ内圧力 (kgf/cm²) A: 投影面積の合計 (cm²)
F = p × A / 1000
一般的にキャビティ内圧力(p)は約300~500 kgf/cm²の範囲です。
金型設計の改善
キャビコア(パーティングライン)のメンテナンス・修正
金型のパーティングラインを定期的に清掃し、ガスヤニや汚れを除去します。必要に応じて研磨や修正を行い、隙間を最小限に抑えます。また、パーティングラインの設計を最適化し、樹脂漏れを防ぐ構造にします。必要に応じて、ガスベントを設置し、樹脂圧力を分散させるなど金型の摩耗が進行する前に適切なタイミングでメンテナンスや修正を行います。
金型部品の境界
入れ子の加工精度を向上させ、合わせ面の隙間を最小限に抑えることが重要です。また、耐摩耗性の高い材質を選択し、必要に応じて表面処理を施すことで、長期使用による摩耗を防ぎます。上記同様、入れ子部分の清掃と点検を行い、摩耗や損傷を早期に発見し対処することで、バリの発生を未然に防ぐことに繋がります。
スライド入れ子の摺動部
摩耗性の高い材質を選択し、必要に応じて表面処理(窒化処理やコーティング)を施すことで、摩耗の進行を遅らせます。クリアランスの設定ではバリが出やすい樹脂を使用する場合に、クリアランスを0.005程度に設定することが推奨されます。また、スライド入れ子にSKD61(HRC52)、可動側入れ子にHPM31(HRC58)を使用するなど、適切な材質と硬度の組み合わせを選択します。
サポートピラーの適切な配置・設計
型板の中心部分を取り囲むように配置し、コアの真下に配置することも効果的ですがエジェクターピンの配置との関係を考慮します。長さはスペーサーブロックよりも0.1~0.2mm長い程度に設定することでバリを防ぎます。
材料選定の工夫
以下は、バリが出やすい材料です。
PPS(ポリフェニレンサルファイド)
高流動性を持つため、バリが発生しやすいです。適切な成形条件と金型設計でバリを防ぎます。
LCP(液晶ポリマー)
高流動性を持つため、バリが生じやすくなります。特に、ランナー径やゲートサイズを調整することで流動を制御します。
PA(ポリアミド)
流動性が比較的高いため、バリが発生しやすいです。適切な成形条件と材料選定でバリを防ぎます。
粘度の適正化
粘度が適切なグレードを選ぶことで流動を安定させます。
材料の種類の変更
部品の要求特性によってはバリが出にくい材料に変更することが可能な場合も多々あります。当社は様々な用途でバリ対策をしてきた経験から、最適な材料のご提案をさせて頂きます。
樹脂の前処理
樹脂を適切に乾燥し、成形過程での水分蒸発を防ぎます。特に、吸湿性の高い材料は樹脂メーカーが推奨する乾燥時間を確実に守って乾燥します。
バリ対策表
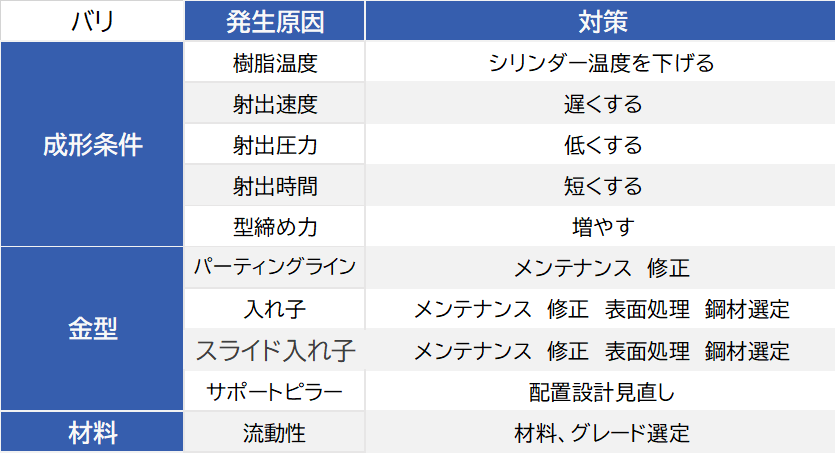
まとめ
射出成形におけるバリは、成形品の品質に大きな影響を与える不良の一つです。バリの発生原因を正確に把握し、成形条件、金型設計、材料特性の各要素に対する対策を講じることで、バリの発生を効果的に防止できます。当社では、長年の経験と高度な成形技術を活かし、高品質な成形品を提供します。
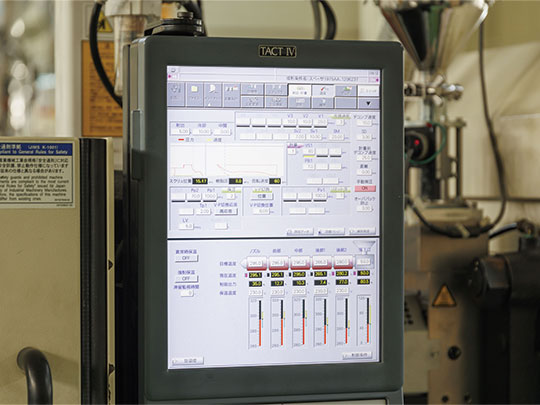