インサート成形で実現する設計革新(前編): 製品価値を高める5大メリット

部品設計において、コスト削減、性能向上、納期短縮、そして高い信頼性の確保は、常に追求される重要なテーマです。特に、電気電子機器、精密機械、流体制御機器など、高度な機能と品質が求められる分野では、これらの要求をいかに高いレベルで満たすかが製品競争力を左右します。こうした課題に対する有効な解決策の一つとして、近年ますます注目を集めているのが「インサート成形」と呼ばれる射出成形技術です。
インサート成形とは、金型内にあらかじめ金属部品やセラミックス部品などの異材質部品(インサート品)をセットし、その周囲に溶融した樹脂を射出して充填・固化させることで、樹脂とインサート品を強固に一体化させる技術です。この技術を活用することで、従来の設計や製造プロセスでは実現が難しかった数多くのメリットを享受できます。
そこで、今回は2回のコラムにわたって、特に電気電子機器、機械、流体制御機器メーカーの部品設計に携わる皆様を対象に、インサート成形の基礎知識から、その最大の魅力であるメリット(特にコスト削減、高機能化、品質向上)について、具体的な理由や事例を交えながら徹底的に解説します。また、インサート成形を成功させるための材料選定や設計上の重要ポイントについても触れていきます。このコラムを通じて、インサート成形技術への理解を深めていただき、皆様が抱える設計上の課題解決や、より付加価値の高い製品開発の一助となれば幸いです。
インサート成形による5大メリット
インサート成形は、単に異材質を組み合わせる技術というだけでなく、設計や製造プロセス全体に大きな変革をもたらすポテンシャルを秘めています。ここでは、設計者が特に注目すべき、インサート成形がもたらす具体的なメリットを5つの観点から詳しく見ていきましょう。
メリット-1 劇的なコスト削減
インサート成形がもたらす最も大きなメリットの一つが、コスト削減効果です。これは主に「部品統合」と「工程削減」によって実現されます。
Before/After比較
従来、例えば金属製のネジや端子を樹脂製の筐体に組み付ける場合、「金属部品の製造」「樹脂部品の製造」「組立工程(ネジ締め、圧入、接着など)」といった複数のステップが必要でした。これに対しインサート成形では、金属部品をインサート品として樹脂部品と一体で成形するため、部品そのものが「完成形」に近い状態で出来上がります。
組立工数の削減
これにより、最もコストインパクトが大きい組立工程を丸ごと削減できます。手作業による組立はもちろん、自動組立ラインの構築・維持にかかる設備投資や人件費、スペースといったコストも不要になります。これは、特に大量生産品において、製品単価に直接的な削減効果をもたらします。
部品点数削減効果
複数の部品を一つにまとめることで、管理すべき部品点数が減ります。これは、部品の購買・調達コスト、在庫管理コスト、受け入れ検査コスト、品質管理コストなど、部品管理に関わる間接的なコストの削減にも繋がります。サプライチェーンがシンプルになり、管理業務の効率化も期待できます。
材料費削減の可能性
一見、インサート成形用の金型は複雑で高価になる傾向がありますが、組立工程の削減や、場合によってはインサート品の形状最適化による材料使用量の削減などにより、トータルでのコスト削減が実現できるケースが多くあります。特にライフサイクル全体で見た場合、その効果はより顕著になります。
具体例
コネクタハウジング:従来は端子をプレス加工し、樹脂ハウジングに後から圧入していましたが、フープ成形(連続インサート成形)を用いれば、端子とハウジングを一体成形でき、大幅なコストダウンと生産性向上が可能です。
モーター部品の絶縁構造:金属シャフトと樹脂製のコイルボビンを一体成形することで、接着工程や圧入工程をなくし、信頼性とコスト競争力を両立できます。
センサーケース:金属製のネジインサートを樹脂ケースと一体成形することで、後加工のタップ立てやネジ締め工程を不要にし、組立コストを削減します。
メリット-2 製品の高機能化と付加価値向上
インサート成形は、単に部品を一体化するだけでなく、それぞれの材料が持つ長所を組み合わせることで、製品の高機能化と付加価値向上を実現します。
金属インサートによる機能付与
強度・剛性向上:樹脂だけでは強度が不足する箇所に、金属製のフレーム、プレート、ボスなどをインサートすることで、部品全体の強度や剛性を大幅に高めることができます。荷重がかかる構造部品や、嵌合部の補強などに有効です。
耐熱性・耐摩耗性向上:高温環境下で使用される部品や、摺動部など摩耗が懸念される箇所に、耐熱性や耐摩耗性に優れた金属(ステンレス、特殊合金など)やセラミックスをインサートすることで、製品の耐久寿命を飛躍的に向上させることができます。軸受部やバルブシートなどが代表例です。
設計自由度の拡大:インサート成形を用いることで、従来は別部品で構成せざるを得なかった複雑な機能を持つ部品を一体で成形することが可能になります。これにより、設計の制約が減り、より自由な発想での製品開発が可能になります。例えば、流路とセンサー取り付け部を一体化したハウジングなど、従来にない新しい構造を生み出すことができます。
ターゲット業界事例
電気電子機器:機器筐体の薄肉化と強度確保を両立するための金属フレームインサート、放熱性が求められる部品へのヒートシンクのインサート固定などが挙げられます。
機械:軽量化が求められるロボットアームなどの構造部品に、強度が必要な部分のみ金属をインサートしたハイブリッド構造のギアやプーリー、精密位置決めが要求される機構部品の軸受部などが考えられます。
流体制御機器:高圧に耐えるための金属リングをインサートした樹脂製ハウジング、耐薬品性・耐摩耗性が求められるバルブシートやポンプ部品に特殊金属やセラミックスをインサートする例があります。
メリット-3 品質と信頼性の劇的向上
部品を後から組み立てるのではなく、成形段階で一体化させるインサート成形は、製品の品質と信頼性の向上に大きく貢献します。
強固な接合
樹脂がインサート品の周囲を包み込むように固化するため、非常に強固な接合状態が得られます。接着剤のように経時劣化による剥離の心配がなく、ネジのように振動による緩みのリスクもありません。物理的なアンカー効果(インサート品の凹凸形状など)を利用すれば、さらに接合強度を高めることができます。
寸法精度の安定
複数の部品を組み立てる場合、各部品の公差の積み重ねや組立時のバラツキにより、最終的な製品の寸法精度を安定させることが難しい場合があります。インサート成形では、金型内でインサート品の位置を高精度に決めて一体成形するため、部品間の相対的な位置精度が非常に高く、安定した寸法精度を維持できます。
気密性・防水性の向上
Oリングなどのシール部品を別途組み付ける代わりに、シール機能を持つエラストマー(熱可塑性エラストマー:TPE)などをインサート成形(または二色成形)することで、高い気密性や防水性を備えた部品を効率的に製造できます。接合界面からの漏れのリスクを低減できます。
振動・衝撃への耐久性向上
一体構造であるため、部品間のガタつきがなく、振動や衝撃に対して優れた耐久性を示します。これは、自動車部品や産業機器など、過酷な環境下で使用される製品にとって重要なメリットとなります。
長期信頼性の確保
上記のメリットにより、製品の初期品質が高いだけでなく、長期間にわたってその性能を維持しやすくなります。結果として、製品の寿命が延び、メンテナンスコストの削減や、市場での信頼性向上に繋がります。
メリット-4 小型化・軽量化
インサート成形は、製品の小型化・軽量化にも貢献し、製品競争力を高める上で有効な手段となります。
部品統合による省スペース設計
複数の部品を一つにまとめることで、部品間のクリアランスや締結スペースが不要になり、製品全体のサイズダウンが可能になります。特に、電子機器など高密度実装が求められる分野で効果を発揮します。
金属部品の部分的な樹脂化による軽量化
従来はオール金属で作られていた部品でも、強度が必要な部分のみ金属インサートを残し、他の部分を軽量な樹脂に置き換えることで、機能性を損なわずに大幅な軽量化を実現できます。自動車や航空宇宙分野、ロボットなど、軽量化が燃費や運動性能に直結する分野で重要視されています。
薄肉設計の可能性拡大
金属インサートによって構造的な強度を補強できるため、樹脂部分の肉厚を限界まで薄くすることが可能になります。これも小型化・軽量化に貢献します。
メリット-5 生産性の向上とリードタイム短縮
インサート成形は、特に自動化との親和性が高く、生産性の向上とリードタイムの短縮に貢献します。
自動化に適したプロセス
インサート品の自動供給・挿入ロボットと射出成形機を組み合わせることで、インサート成形プロセス全体の自動化が可能です。これにより、人手に頼る部分が減り、安定したサイクルタイムでの連続生産が可能となり、生産性が大幅に向上します。
後工程(組立)削減によるトータルリードタイムの大幅短縮
前述の通り、組立工程が不要になるため、部品製造から最終製品完成までのトータルリードタイムを大幅に短縮できます。これにより、市場への製品投入スピードを速め、ビジネスチャンスを逃しません。
インサート成形の仕組み:メリットを支える基本原理とプロセス
これら数々のメリットを生み出すインサート成形は、どのような仕組みで成り立っているのでしょうか。その基本的な原理とプロセスを見ていきましょう。
基本プロセス
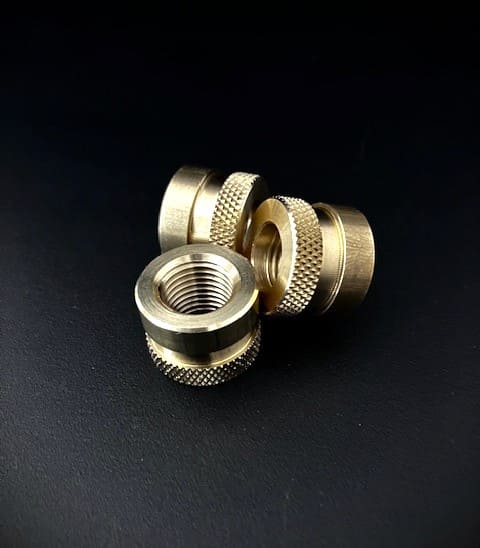
1.インサート品の準備・前処理:インサート品(金属端子、ネジ、シャフト、プレートなど)を用意します。必要に応じて、油分除去のための洗浄や、樹脂との密着性を高めるための表面処理(プライマー塗布、粗化処理など)、あるいは成形時の温度差を緩和するための予熱を行います。
2.金型へのインサート品セット: 開いた金型の所定の位置に、インサート品を正確にセットします。手作業で行う場合と、自動化されたロボットアームなどで行う場合があります。
3.型締め:金型を閉じ、インサート品を確実に保持・固定します。この際、インサート品がずれたり、変形したりしないように、適切な型締め力と保持機構が必要です。
4.樹脂の射出・保圧・冷却:加熱され溶融した樹脂を、金型内に高圧で射出・充填します。樹脂はインサート品の周囲に流れ込み、一体化します。その後、圧力を保持しながら冷却し、樹脂を固化させます。
5.型開き:樹脂が十分に固化したら、金型を開きます。
6.製品の取り出し:成形品(インサート品と樹脂が一体化したもの)を金型から取り出します。突き出しピンやロボットアームなどが用いられます。
インサート品の保持技術
成形プロセス中、特に樹脂が高圧で射出される際にインサート品が動かないように、金型内で確実に保持することが非常に重要です。保持方法には、金型に設けたピンで押さえる方法、インサート品の形状を利用して嵌め込む方法、マグネットで吸着する方法(インサート品が磁性体の場合)、真空で吸着する方法など、インサート品の材質、形状、サイズ、精度に応じて様々な工夫が凝らされます。
樹脂の流動と固化
射出された溶融樹脂が、インサート品の隅々まで行き渡り、かつインサート品を変形させたりダメージを与えたりしないように、樹脂の流動性、射出速度、圧力、温度などを精密に制御する必要があります。樹脂が冷却・固化する過程で、インサート品との間に強固な結合(物理的なアンカー効果や、場合によっては化学的な結合)が形成されます。
代表的な成形方法
手動インサート成形:作業者が手でインサート品をセットする方法。試作品や少量生産、複雑な形状のインサート品などに用いられます。
自動インサート成形:ロボットなどを利用してインサート品の供給・セットを自動化した方法。大量生産に適しており、品質の安定化と生産性向上に貢献します。
フープ成形(リールtoリール成形):長い帯状(フープ)に加工された金属端子などをリールから連続的に金型へ供給し、次々とインサート成形を行う方法。コネクタ端子などの電子部品の大量生産に非常に効率的です。
材料選定の勘所:インサート成形の成功を左右する要素
インサート成形のメリットを最大限に引き出し、安定した品質を得るためには、樹脂材料とインサート品の適切な選定が不可欠です。
樹脂選定のポイント
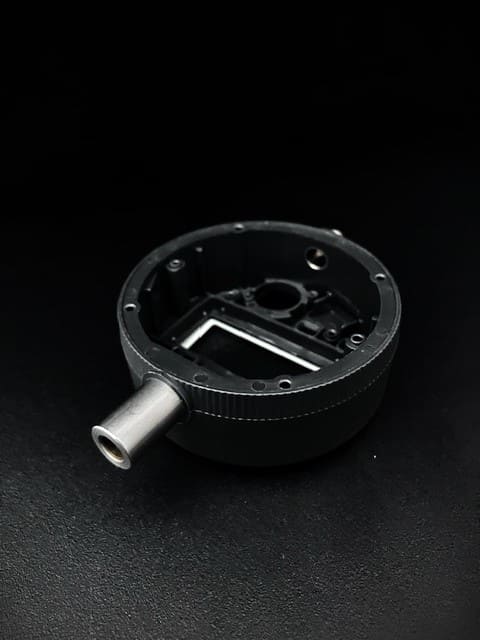
インサート品との密着性:最も重要な要素の一つです。インサート品の材質(金属、セラミックなど)と化学的・物理的に良好な密着性を示す樹脂を選ぶ必要があります。一般的に、極性を持つ樹脂(例:PA, PBT)は金属との親和性が高い傾向にありますが、非極性樹脂(例:PP, PE)でもアンカー効果や表面処理により対応可能です。
1.要求される物性:製品に求められる機械的強度(引張強度、曲げ強度、衝撃強度など)、耐熱性、電気特性(絶縁性など)、耐薬品性、寸法安定性などを満たす樹脂を選定します。ターゲットとなる使用環境や要求スペックを明確にすることが重要です。
2.成形性:溶融時の流動性が低いとインサート品の細部まで樹脂が回らない(ショートショット)可能性があります。逆に流動性が高すぎるとバリが発生しやすくなります。また、成形収縮率がインサート品との間で大きく異なると、反りや剥離、クラックの原因となるため注意が必要です。
3.コスト:材料コストも重要な選定要素です。要求性能を満たす範囲で、最もコストパフォーマンスの高い材料を選定します。
各種樹脂材料の特性については、当サイトの材料解説ページもご参照ください。
インサート品選定のポイント
材質と特性:製品に求められる機能(強度、耐熱性、耐摩耗性など)を発揮できる材質を選定します。金属(銅、真鍮、ステンレス、アルミなど)、セラミックス、ガラスなどが一般的です。
表面状態と前処理:インサート品の表面に油分や汚れ、酸化膜が付着していると、樹脂との密着性を著しく低下させます。そのため、成形前に適切な洗浄や脱脂処理が必要です。また、密着性をさらに向上させるために、表面を粗化する(サンドブラストなど)、プライマーを塗布するといった前処理を行うこともあります。
形状精度と供給安定性:インサート品は金型内に正確にセットされる必要があるため、高い寸法精度と形状精度が求められます。寸法バラツキが大きいと、位置ずれや保持不良、バリの原因となります。また、量産においては、安定した品質のインサート品を継続的に供給できる体制も重要です。
次回コラム後編のご案内
今回のコラム前編では、インサート成形がもたらすコスト削減、高機能化、品質向上といった絶大なメリット、その基本的な仕組み、そして成功を左右する材料選定の勘所について解説しました。これらのメリットを最大限に引き出すためには、さらに踏み込んだ知識が必要です。次回のコラム後編では、インサート成形を成功させるための設計段階での重要検討事項に焦点を当てます。インサート品の確実な固定方法、樹脂流動のコントロール、密着強度を高める工夫、応力集中や熱応力への対策、そしてトラブルを未然に防ぐための具体的なノウハウを詳しく解説します。さらに、様々な産業分野におけるインサート成形の応用事例もご紹介する予定です。より実践的な知識を得て、インサート成形を貴社の製品開発に活かすために、ぜひ次回のコラム後編もご覧ください。